Problem Solving w produkcji – jak identyfikować przyczyny błędów i zapobiegać ich powstawaniu?
W dynamicznym i wymagającym środowisku produkcyjnym, każda firma napotyka wyzwania związane z błędami, opóźnieniami, nieefektywnością maszyn czy problemami jakościowymi. Aby utrzymać konkurencyjność i wysoką efektywność, niezbędne jest wdrożenie systematycznych metod rozwiązywania problemów. Problem Solving w produkcji to zbiór technik i narzędzi, które pomagają zidentyfikować przyczyny problemów, usunąć je i zapobiec ich ponownemu wystąpieniu. Celem jest minimalizowanie strat, poprawa jakości oraz optymalizacja procesów produkcyjnych.
Spis treści:
- Czym jest Problem Solving w kontekście produkcji?
- Metodologie Problem Solving w produkcji.
- Kluczowe etapy w procesie rozwiązywania problemów w produkcji.
- Przywództwo i praca zespołowa w procesie rozwiązywania problemów.
- Jakie narzędzia jakościowe stosować do rozwiązywania problemów?
- Jakie korzyści płyną z wdrożenia procesów Problem Solving w produkcji?
- Podsumowanie – Kluczowe zasady skutecznego rozwiązywania problemów w produkcji.
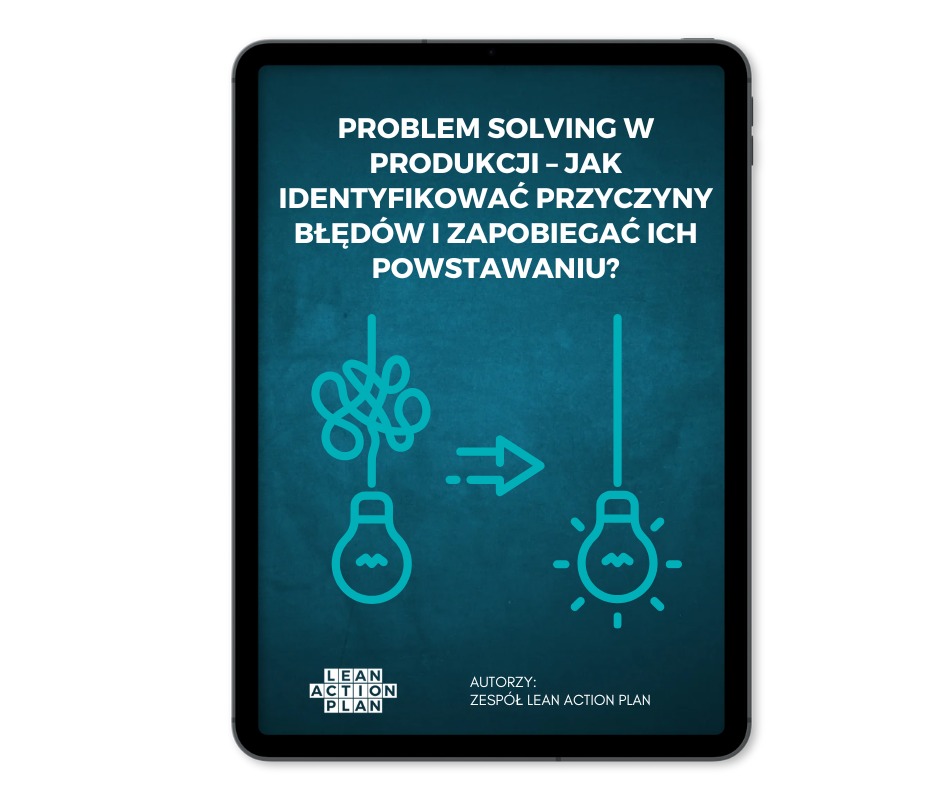
Czym jest Problem Solving w kontekście produkcji?
Problem Solving w produkcji odnosi się do zestawu metod i narzędzi, które pozwalają na identyfikowanie przyczyn problemów, analizowanie ich źródeł oraz wprowadzanie skutecznych rozwiązań. W produkcji, gdzie problemy mogą obejmować:
– błędy jakościowe,
– opóźnienia w procesach,
– nieefektywność maszyn,
– problemy z zasobami ludzkimi – kluczowe jest podejście oparte na metodologii, które pozwala na szybsze identyfikowanie i eliminowanie przeszkód. Problem Solving w produkcji pozwala na tworzenie bardziej efektywnych procesów, zmniejszenie liczby błędów oraz zapewnienie lepszej jakości produktów, co wpływa na poprawę rentowności i satysfakcji klienta.
Metodologie Problem Solving w produkcji
W zarządzaniu produkcją, istnieje kilka popularnych metodologii, które pozwalają na skuteczne rozwiązywanie problemów i eliminowanie źródeł błędów. Poniżej przedstawiamy najczęściej stosowane metody Problem Solving w produkcji.
QRQC – Quick Response Quality Control
QRQC to metoda, która ma na celu szybkie reagowanie na problemy jakościowe w produkcji. Jest to podejście, które skupia się na natychmiastowym identyfikowaniu i eliminowaniu problemów, zanim staną się one poważnym zagrożeniem dla procesu produkcyjnego. Główna zasada QRQC to błyskawiczne wykrycie wad w produkcji, zminimalizowanie ich skutków i zapobieganie ich powtórzeniu. Metoda ta jest szczególnie przydatna w środowiskach, gdzie czas reakcji ma kluczowe znaczenie, a szybkie eliminowanie problemów pozwala utrzymać ciągłość produkcji. QRQC jest oparty na kilku podstawowych zasadach:
– szybka identyfikacja problemu,
– zatrzymanie produkcji w przypadku poważnych defektów,
– szybkie usuwanie przyczyn,
– dokumentowanie działań naprawczych.
Dzięki szybkiemu reagowaniu na problemy, QRQC pomaga zredukować straty związane z jakością i poprawia ogólną efektywność produkcji.
PDCA – Plan-Do-Check-Act w produkcji
PDCA to cykliczny model doskonalenia procesów, który jest wykorzystywany do ciągłego ulepszania jakości w produkcji. Jest to metoda, która wspiera przedsiębiorstwa w systematycznym podejściu do rozwiązywania problemów i optymalizacji procesów. Cykl PDCA składa się z czterech kluczowych etapów:
- Plan (Planowanie) – polega na określeniu celów, opracowaniu strategii oraz wytycznych do osiągnięcia zamierzonych rezultatów. Planowanie opiera się na dokładnej analizie problemów i ich przyczyn.
- Do (Wykonanie) – realizacja planu, wdrożenie działań naprawczych lub usprawniających w wybranym procesie produkcyjnym.
- Check (Sprawdzanie) – monitorowanie wyników po wdrożeniu planu, sprawdzanie, czy podjęte działania przyniosły oczekiwane rezultaty.
- Act (Działanie) – podejmowanie działań korygujących na podstawie wyników analizy. Jeśli wyniki są pozytywne, podejmowane są dalsze działania standaryzujące, jeśli nie, proces jest powtarzany od początku.
Zastosowanie PDCA w produkcji pozwala na ciągłe doskonalenie procesów poprzez identyfikowanie nieefektywności, ich eliminowanie oraz wdrażanie nowych rozwiązań.
8D – Raport 8D jako narzędzie rozwiązywania problemów
8D (Eight Disciplines Problem Solving) to metodologia, która koncentruje się na identyfikowaniu przyczyn źródłowych problemów oraz wdrażaniu skutecznych rozwiązań. Jest to szczególnie popularna w firmach produkcyjnych metoda, która pomaga rozwiązywać poważne problemy jakościowe oraz eliminować ich powtarzalność. Raport 8D składa się z ośmiu kroków, które prowadzą do systematycznego rozwiązywania problemów:
- D1: Zespół rozwiązywania problemów – powołanie zespołu odpowiedzialnego za rozwiązanie problemu, składającego się z pracowników z różnych działów.
- D2: Opis problemu – precyzyjne określenie problemu, jego zakresu oraz skutków.
- D3: Tymczasowe działania korygujące – szybkie wprowadzenie rozwiązań mających na celu zatrzymanie problemu i minimalizację strat.
- D4: Analiza przyczyn źródłowych – głębokie badanie przyczyn problemu, aby zapobiec jego powtórzeniu.
- D5: Działania naprawcze – wdrożenie działań, które eliminują przyczyny problemu.
- D6: Weryfikacja działań – sprawdzenie, czy wprowadzone rozwiązania skutecznie eliminują problem.
- D7: Zapewnienie trwałości rozwiązań – działania mające na celu zapewnienie, że rozwiązanie będzie trwałe.
- D8: Zakończenie i podsumowanie – zakończenie procesu, dokumentowanie działań oraz udokumentowanie lekcji wyniesionych z procesu.
A3 – Metoda A3 w rozwiązywaniu problemów produkcyjnych
Metoda A3 to podejście oparte na raportowaniu problemów w formacie A3, czyli jednego arkusza papieru. Jest to narzędzie, które wspiera rozwiązywanie problemów poprzez analizę przyczyn, wypracowanie rozwiązań oraz ścisłe monitorowanie postępu działań. Proces rozwiązywania problemów za pomocą metody A3 składa się z kilku kluczowych kroków:
- Tło problemu – opis sytuacji, która wymaga rozwiązania, w tym kontekst problemu i jego wpływ na procesy produkcyjne.
- Analiza przyczyn – badanie głównych przyczyn problemu, z zastosowaniem technik takich jak analiza 5 Why lub diagram Ishikawy.
- Określenie celów i działań – ustalenie konkretnych celów do osiągnięcia i zaplanowanie działań naprawczych.
- Wdrażanie rozwiązań – przeprowadzenie zaplanowanych działań mających na celu eliminację przyczyn problemu.
- Podsumowanie i wyniki – ocena efektów działań oraz wnioski, które pomagają w przyszłości unikać podobnych problemów.
Kluczowe etapy w procesie rozwiązywania problemów w produkcji
Rozwiązywanie problemów w produkcji to proces składający się z kilku kluczowych etapów, które pozwalają na skuteczne zidentyfikowanie, analizowanie i eliminowanie problemów. Każdy etap, począwszy od identyfikacji problemu, aż po działania korygujące, zapobiegawcze i standaryzację, ma na celu nie tylko naprawienie zaistniałych trudności, ale także zapobieganie ich przyszłemu wystąpieniu.
Identyfikowanie problemów i strat procesowych
Pierwszym krokiem w procesie Problem Solving jest identyfikacja problemów i strat procesowych. Do tego celu można wykorzystać różne narzędzia, takie jak analiza przyczyn źródłowych, diagramy przyczynowo-skutkowe czy analiza FMEA. Identyfikacja problemów polega na precyzyjnym określeniu, gdzie i dlaczego dochodzi do błędów, a także jakie straty procesowe występują w produkcji. W wyniku tej analizy firma jest w stanie wykryć wąskie gardła, które obniżają wydajność produkcji i prowadzą do strat finansowych.
Znajdowanie przyczyn źródłowych problemów
Po zidentyfikowaniu problemów, następnym krokiem jest znalezienie przyczyn źródłowych tych problemów. Do analizy przyczyn problemów w produkcji wykorzystywane są takie techniki jak diagram Ishikawy (diagramy rybiej ości), analiza 5 whys czy FMEA. Wyszukiwanie przyczyn pozwala na głębsze zrozumienie źródła problemu, co umożliwia podjęcie skutecznych działań korygujących i zapobiegawczych.
Działania korygujące, zapobiegawcze i standaryzacja
Po znalezieniu przyczyn problemów należy przejść do podejmowania działań korygujących, które pozwolą na usunięcie błędów. Działania zapobiegawcze są niezbędne, aby zapobiec ich ponownemu wystąpieniu. Kolejnym krokiem jest standaryzacja procesów, czyli wdrożenie nowych procedur, które będą zapewniały wysoką jakość produkcji i minimalizowały ryzyko błędów.
Przywództwo i praca zespołowa w procesie rozwiązywania problemów
Skuteczne rozwiązywanie problemów w produkcji nie jest możliwe bez zaangażowania odpowiednich liderów oraz współpracy zespołowej. Rola kadry menedżerskiej jest kluczowa, aby zainicjować proces rozwiązywania problemów oraz właściwie ukierunkować zespół. Praca zespołowa umożliwia pełniejsze wykorzystanie wiedzy i doświadczeń wszystkich pracowników, co z kolei przekłada się na szybsze i skuteczniejsze rozwiązanie problemu. Zespół, który aktywnie angażuje się w rozwiązywanie trudności, ma większą szansę na skuteczne eliminowanie błędów i usprawnienie procesów produkcyjnych.
Rola menedżerów i zespołów w procesie rozwiązywania problemów
Skuteczne rozwiązywanie problemów produkcyjnych nie jest możliwe bez zaangażowania menedżerów i zespołów produkcyjnych. Menedżerowie pełnią kluczową rolę w zarządzaniu procesem Problem Solving, ponieważ to oni wyznaczają cele, monitorują postępy i podejmują decyzje na podstawie zebranych danych. Z kolei zespoły produkcyjne są odpowiedzialne za identyfikowanie problemów i wdrażanie działań korygujących.
Praca zespołowa jako klucz do sukcesu w rozwiązywaniu problemów
Zespołowa praca w rozwiązywaniu problemów pozwala na lepsze wykorzystanie wiedzy i doświadczenia pracowników, co prowadzi do szybszego wykrywania problemów i skuteczniejszego ich rozwiązywania. Praca zespołowa jest kluczowa w procesie Problem Solving, ponieważ różne perspektywy pozwalają na dokładniejsze zrozumienie problemów i skuteczne wdrożenie rozwiązań.
Jakie narzędzia jakościowe stosować do rozwiązywania problemów?
W procesie Problem Solving w produkcji kluczowe są odpowiednie narzędzia jakościowe, które pozwalają na dokładną analizę przyczyn problemów i skuteczną ich eliminację. Są to m.in. narzędzia takie jak:
– analiza FMEA (Failure Mode and Effects Analysis) – to narzędzie analityczne, które służy do identyfikacji i oceny potencjalnych problemów (usterek) w procesach produkcyjnych, a także ich wpływu na dalszy przebieg produkcji. Jego celem jest przewidywanie możliwych awarii, określenie ich przyczyn oraz zaprojektowanie działań zapobiegawczych, zanim problem wystąpi.
– diagramy Ishikawy (diagramy rybiej ości) – jest narzędziem stosowanym w analizie przyczyn problemów. Pomaga w systematycznym przedstawieniu różnych czynników, które mogą mieć wpływ na wystąpienie danego problemu. Diagram ten składa się z „kręgosłupa” i „ości”, na których zapisuje się różne kategorie przyczyn problemów, takie jak: maszyny, materiały, metody pracy, ludzie, środowisko i inne czynniki. Każda z ości odpowiada za jedną z kategorii, co ułatwia identyfikację głównych przyczyn błędów i umożliwia skupienie się na najbardziej istotnych aspektach procesu.
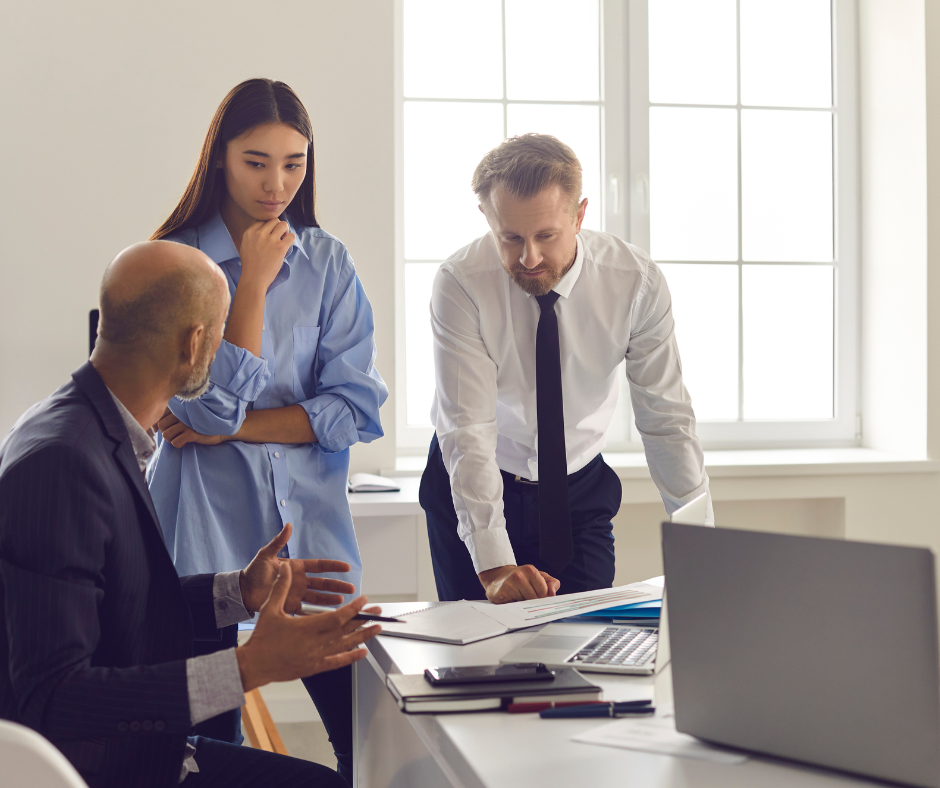
– metoda 5 whys – prosta, ale bardzo skuteczna technika służąca do identyfikowania przyczyn problemów poprzez zadawanie pytania “dlaczego?”. Zgodnie z tą metodą, aby znaleźć przyczynę główną problemu, należy pięciokrotnie zapytać “dlaczego?”. Każde kolejne “dlaczego” prowadzi do odkrywania bardziej szczegółowych przyczyn, co pomaga dojść do źródła problemu.
Jakie korzyści płyną z wdrożenia procesów Problem Solving w produkcji?
Wdrożenie procesów Problem Solving w produkcji niesie za sobą szereg korzyści, które mają bezpośredni wpływ na poprawę efektywności, jakości i rentowności firmy. Skuteczne zarządzanie problemami prowadzi do redukcji kosztów operacyjnych, poprawy jakości produktów oraz zwiększenia wydajności maszyn i pracowników. Dodatkowo, procesy te pomagają w minimalizacji ryzyka wystąpienia powtarzających się błędów, co przekłada się na długoterminową poprawę wyników produkcji oraz większą satysfakcję klientów.
Zwiększenie efektywności i jakości produkcji
Zwiększenie efektywności produkcji jest jednym z głównych celów wdrażania metod Problem Solving w firmach produkcyjnych. Poprzez identyfikowanie i eliminowanie przyczyn błędów, opóźnień i marnotrawstwa, organizacje mogą zoptymalizować swoje procesy produkcyjne, co prowadzi do wzrostu wydajności. Istotnym elementem tego procesu jest poprawa jakości produktów, ponieważ każde niedopatrzenie na etapie produkcji może prowadzić do błędów, które mają poważne konsekwencje dla końcowego wyniku. Zwiększając jakość, firmy zmniejszają liczbę reklamacji i zwrotów, co z kolei przekłada się na lepsze relacje z klientami i wyższą rentowność. Wdrożenie skutecznego procesu rozwiązywania problemów umożliwia szybsze identyfikowanie źródeł błędów i wprowadzanie odpowiednich poprawek w czasie rzeczywistym, co pozwala na utrzymanie wysokiej jakości produktów i sprawną produkcję. Dodatkowo, ciągłe doskonalenie procesów produkcyjnych jest niezbędne do dążenia do perfekcji, co w rezultacie zapewnia firmom przewagę na rynku.
Redukcja kosztów i eliminacja strat
Redukcja kosztów oraz eliminacja strat to nieodłączne elementy skutecznego zarządzania produkcją, a proces Problem Solving odgrywa tu kluczową rolę. W identyfikowaniu i eliminowaniu źródeł marnotrawstwa, takich jak:
– nadmiar surowców,
– przestoje maszyn,
– niewłaściwe wykorzystanie zasobów ludzkich – organizacje mogą znacząco obniżyć koszty operacyjne.
Wdrożenie metod takich jak QRQC, PDCA, czy 8D pozwala na szybkie wykrywanie błędów, zanim staną się one kosztownymi problemami. Eliminacja marnotrawstwa w produkcji wiąże się również z lepszym wykorzystaniem maszyn, zmniejszeniem zapasów i usprawnieniem procesów. Optymalizacja kosztów to także zmniejszenie zapotrzebowania na zasoby energetyczne i materiałowe, co nie tylko obniża koszty, ale również przyczynia się do zrównoważonego rozwoju i poprawy efektywności ekologicznej firmy. Co więcej, regularne monitorowanie i analiza wydajności pozwalają na szybsze wykrycie nieoptymalnych procesów, co umożliwia ich szybkie poprawienie i przyczynia się do dalszej eliminacji strat, a tym samym do dalszego zwiększania rentowności przedsiębiorstwa.
Podsumowanie – Kluczowe zasady skutecznego rozwiązywania problemów w produkcji
Kluczowymi zasadami skutecznego rozwiązywania problemów w produkcji są systematyczne podejście, zaangażowanie zespołu oraz ciągłe doskonalenie procesów. Dzięki odpowiedniemu stosowaniu metodologii Problem Solving, firmom udaje się nie tylko poprawić jakość produkcji, ale również zminimalizować straty, zwiększyć rentowność i uzyskać przewagę konkurencyjną. Aby skutecznie wdrożyć proces Problem Solving, firma powinna przede wszystkim zainwestować w odpowiednie szkolenia dla pracowników, wdrożyć odpowiednie narzędzia analityczne, a także zadbać o kulturę ciągłego doskonalenia. Kluczowe jest zaangażowanie menedżerów, którzy będą motywować zespół do podejmowania działań naprawczych i systematycznej analizy procesów.
Masz pytania lub chcesz dowiedzieć się więcej? Skontaktuj się z nami i skorzystaj z bezpłatnej konsultacji, podczas której pomożemy zidentyfikować problemy i zaproponujemy konkretne rozwiązania dla Twojej firmy.