Wykorzystanie danych z systemu ERP do obliczania zapotrzebowania na surowce, planowania produkcji oraz kosztów wytwarzania wyrobów gotowych.
Branża | Druk wielkoformatowy |
---|---|
Zatrudnienie | +50 |
Produkcja | druk |
Główne procesy | druk, cięcie, kalandrowanie, zgrzewanie, oczkowanie, pakowanie |
Założenia | określenie kosztów wytworzenia produktu, ustalanie cen handlowych |
Zwiększenie rotacji magazynowej
Redukcja czasu potrzebnego na planowanie produkcji
Zdecydowanie polecam współpracę z firmą Lean Action Plan, ponieważ stanowią merytoryczne i narzędziowe wsparcie do zarządzania firmy.

KAPS
Wyzwania klienta
Implementacja rozwiązania
- Analiza Procesów
Firma borykała się z problemami związanymi z obliczaniem zapotrzebowania na materiały, planowaniem produkcji oraz kontrolą kosztów produkcyjnych wyrobów gotowych. System ERP firmy nie był wykorzystywany w pełni, co prowadziło do problemów z zarządzaniem zasobami, spadkiem marży oraz czasochłonnym układaniem planu produkcyjnego. W celu poprawy efektywności operacyjnej, firma postanowiła zoptymalizować swoje procesy za pomocą lepszego wykorzystania danych z systemu ERP.
- Moduł MRP (Material Requirements Planning):
Automatyzacja procesu planowania zapotrzebowania na materiały na podstawie prognoz sprzedaży/zamówień, aktualnych stanów magazynowych oraz BOM (Bill of Materials) umożliwiła lepsze zarządzanie zapasami. Automatyczne generowanie ilości wymaganych do zamówienia uwzględnia stany minimalne oraz czas dostawy surowców. Narzędzie wskazuje ilość oraz termin zamówienia surowców.
- Moduł Capacity
Gromadzenie danych w systemie ERP i Excelu takich jak:
- Marszruty(przebieg procesu produkcyjnego wyrobu gotowego)
- Czasy wykonania
- Zamówienia produkcyjne
- Prognozy sprzedażowe
- Dostępność pracowników oraz maszyn
Pozwoliły na automatyczne obliczanie Capacity wszystkich stanowisk w firmie. Wyniki pozwoliły firmie na lepsze zarządzanie dostępnymi zasobami. Moduł pozwolił zidentyfikować i wyeliminować wąskie gardła w procesie produkcyjnym. Dodatkowo firma jest w stanie szybciej dostosować się do wzrostu lub spadku popytu oraz precyzyjnego podjęcia decyzji o zwiększeniu dostępności na konkretnych stanowiskach poprzez dodatkowe zatrudnienie lub inwestycje.
4. Moduł Planowania produkcji
Dane służące do wykonania Capacity uzupełnione o terminy zamówień pozwoliły również wygenerować zakładany plan produkcyjny na wszystkie obecne stanowiska/procesy w firmie. Plan produkcyjny został zwizualizowany w formie wykresu Gantta.
Dzięki temu, że plan jest czytelny został wyświetlany na stanowiskach produkcyjnych. Jasny plan produkcyjny pozwala pracownikom lepiej organizować swoje zadania, co minimalizuje przestoje i maksymalizuje wykorzystanie zasobów. Pracownicy na różnych stanowiskach wiedzą, jakie mają zadania i jakie są priorytety, co poprawia płynność i synchronizację działań.
5. Moduł obliczania kosztów produkcji
Ostatnim z wykonanych modułów był moduł do obliczania kosztów produkcji. Z pozoru, na pierwszy rzut oka podobne do siebie wyroby gotowe mogą charakteryzować się różną marżowością. Dzięki informacji o wykorzystanych surowcach oraz czasie potrzebnym na wyprodukowanie poszczególnych półwyrobów firma otrzymała narzędzie, które automatycznie oblicza i porównuje ze sobą wybrane produkty.
Precyzyjne określenie kosztów produkcyjnych wyznaczyło produkty, na których firma nie zarabiała lub ich marżowość była na zbyt niskim poziomie. Dodatkowo koszty produkcji na poszczególnych procesach związane z czasem wykonania wyznaczyły procesy, które zostały wzięte pod uwagę podczas planowanych inwestycji lub konieczności zmiany organizacji pracy.
6. Szkolenie Pracowników
Przeprowadzono szkolenia dla pracowników, aby zapewnić efektywne wykorzystanie nowych funkcjonalności systemu ERP. Szkolenia obejmowały:
- Korzystanie z poszczególnych modułów (MRP, capacity, Planowania produkcji, obliczania kosztów produkcji)
- Analiza danych i generowanie raportów.
- Podejmowanie decyzji na podstawie danych z systemu ERP.
Wyniki
- Lepsze Zarządzanie Zapasami: Automatyzacja generowania zamówień na materiały i optymalizacja zarządzania zapasami zwiększyły rotację magazynową o 34% oraz zmniejszyły zamrożony kapitał magazynowy o 19%
- Capacity: Umożliwiło planowanie inwestycji w nowe maszyny, technologie lub dodatkowe okresowe zatrudnienie, gdy obecne zdolności produkcyjne były niewystarczające. Pomogło również uniknąć przeciążenia zasobów, co mogło prowadzić do spadku jakości, wzrostu kosztów i opóźnień.
- Zwiększona Efektywność Produkcji: Dzięki automatyzacji procesu planowania zapotrzebowania, firma zredukowała czas potrzebny na planowanie produkcji o 83%. Zmniejszenie nadprodukcji i niedoborów zapasów poprawiło płynność produkcji.
- Dokładne Obliczenia Kosztów Produkcyjnych: Integracja z systemem ERP umożliwiła dokładne śledzenie kosztów co pozwoliło na szybsze reagowanie na wszelkie odchylenia.
Wnioski
Wykorzystanie danych z systemu ERP do obliczania zapotrzebowania, kosztów produkcyjnych, planowania produkcji oraz capacity znacząco poprawiło efektywność operacyjną firmy. Automatyzacja procesów i lepsza analiza danych pozwoliły na osiągnięcie znacznych oszczędności i poprawę zarządzania zasobami. Regularne monitorowanie i ciągłe ulepszanie procesów zapewniło utrzymanie wysokiej jakości produkcji i zdolność szybkiego reagowania na zmiany rynkowe.
Dzięki wdrożonym rozwiązaniom, firma jest teraz lepiej przygotowana na przyszłe wyzwania i może skuteczniej konkurować na rynku.
KONTAKT BEZPOŚREDNI
Obsługa klienta
Anna Etgens
Specjalistka ds. zadowolenia klienta
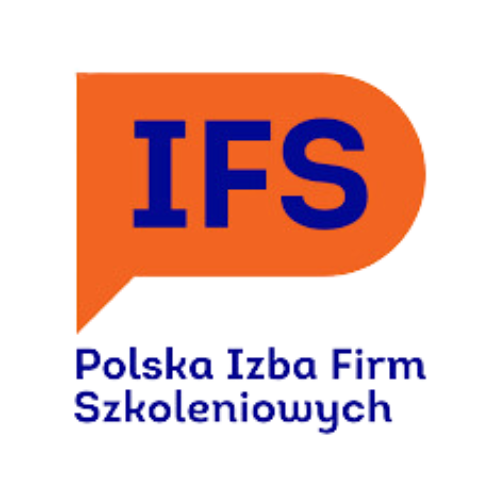
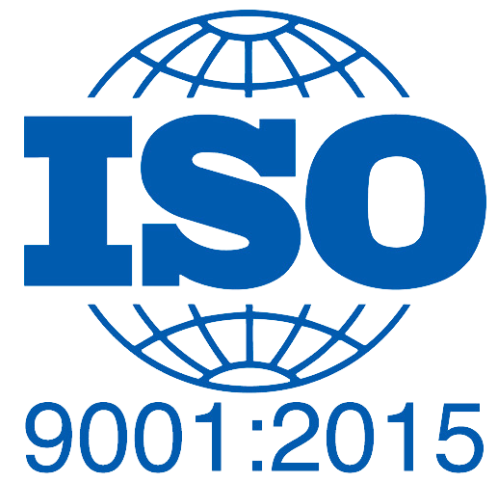