8 sposobów, aby szkolenia Lean przyniosły rezultaty na produkcji
Czy zdarzyło Ci się uczestniczyć w szkoleniu Lean Management, którego przebieg, aż budził dreszczyk pozytywnej energii, ferworu, satysfakcji, wizji górnolotnych zmian… a potem w rzeczywistości pozorny efekt zniknął w aurze codzienności? To niestety znana bolączka.
Nie sądzisz, że takie stwierdzenia słyszy się dosyć często? „Operatorzy byli zwykle oporni na zmianę, jednak tak aktywnie udzielali się w trakcie warsztatów, że zobaczyłem w tym potencjał rozwoju, szkoda, że ten zapał zgasł po weekendzie”, „Po warsztatach z zarządzania wizualnego postawiliśmy pracownikom whiteboard’y, sami entuzjastycznie rozrysowali szablon, który pomógłby im w monitorowaniu codziennych obowiązków, dlaczego później przestali nawet spoglądać w tamtą stronę?”. Jeżeli jesteś właścicielem, kierownikiem lub menadżerem w firmie produkcyjnej, pewnie sam niejednokrotnie zadałeś sobie podobne pytanie, rozważając również rentowność inwestycji, a w zasadzie jej brak. Przecież idea Lean Manufacturing dąży do eliminacji marnotrawstwa, redukcji kosztów, skracania czasu realizacji, poprawy efektywności oraz jakości, a tutaj widać kompletny brak spójności już na etapie nauki i wprowadzenia!
Jeśli chcesz dalej iść w kierunku nieefektywnego szkolenia pracowników, przedstawię Ci najpierw:
8 sposobów, przez które szkolenia Lean nie przynoszą rezultatów w Twojej firmie:
- Powiedz pracownikom, że szkolenie realizowane jest z powodu wdrażania ISO, za wszelką cenę nie używaj sam wiesz jakiego słowa, ponieważ jest angielskojęzyczne i przecież i tak nic im to nie powie.
- Pamiętaj, aby spotkanie było wysycone specjalistycznym językiem, bez zagłębiania się w tłumaczenie (operator może sprawdzić w telefonie), najlepiej żeby nie było też zbyt dużo przykładów, ponieważ procesy „w naszej firmie wyglądają zupełnie inaczej, niż gdzie indziej”.
- Zaanonsuj, że spotkanie wiąże się z nowymi obowiązkami, a co za tym idzie będzie jeszcze więcej pracy.
- Zespół powinien wiedzieć dlaczego odbędzie się szkolenie, najlepszym uzasadnieniem jest „potrzeba zmian”. Właśnie to słowo, bez przedstawienia szczegółów obudzi w nich odpowiednie nastawienie i (nie)chęć do działania.
- Prowadź lub wybieraj szkolenia Lean tak, aby ich program zawierał możliwie dużo teorii. Zrezygnuj z formy warsztatowej.
- Ignoruj feedback i trzymaj się sztywno jednego scenariusza lub poproś o to trenera.
- Zorganizuj przedsięwzięcie z budżetu premiowego, to najlepsza nagroda dla pracownika.
- Po zakończeniu spotkania, zapomnij o nim.
Czy słuchać w tym nutę ironii? Absolutnie! To brutalna rzeczywistość i jeżeli podświadomie czujesz, że którykolwiek z tych punktów mógł mieć miejsce lub na pewno wydarzył się w Twoim zespole, poważnie się zastanów: Jak w takim razie przekuć fiasko w satysfakcjonujący rezultat, z którego wykiełkuje skuteczne wdrożenie metod, bądź narzędzi Lean?
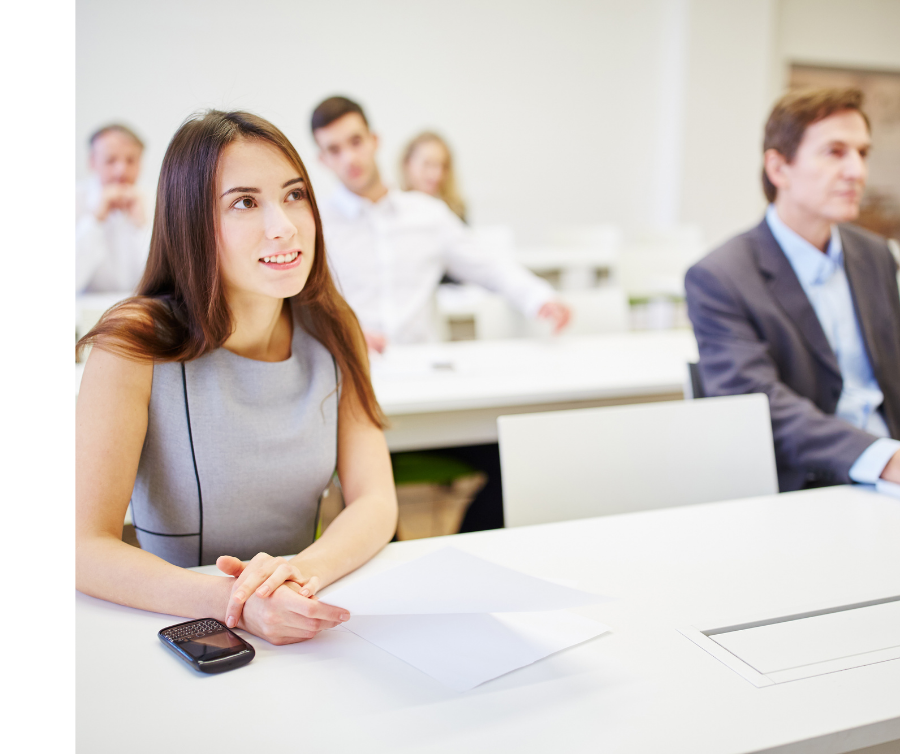
Oczekiwania szkoleniowe
- Chcesz, aby pracownicy zaczęli dostrzegać marnotrawstwo?
- Chcesz, aby Twój zespół pracował mądrzej, a nie więcej?
- Chcesz, aby pracownicy wykazywali się zaangażowaniem i odpowiedzialnością w wykonywanych procesach?
- A może chcesz, aby Twoi ludzie byli bardziej proaktywni i sami rozwiązywali pojawiające się problemy?
To nie tylko Twoje oczekiwania, ale również potrzeby operatorów, którzy często nie potrafią sami postawić pierwszego kroku lub nie są świadomi, że mogą domagać się zmian. Stąd tak ważne jest Twoja inicjatywa.
Korzyści z dobrze przeprowadzonego szkolenia będą płynąć zarówno dla Ciebie, jak i dla zespołu. Zdobyte doświadczenie oraz umiejętności mogą realnie przełożyć się na sposób wykonywania operacji, organizację przestrzeni, a także zwiększenie płynności przepływu produkcyjnego. Jednak wszystko to zależne jest od odpowiedniego podejścia do sprawy.
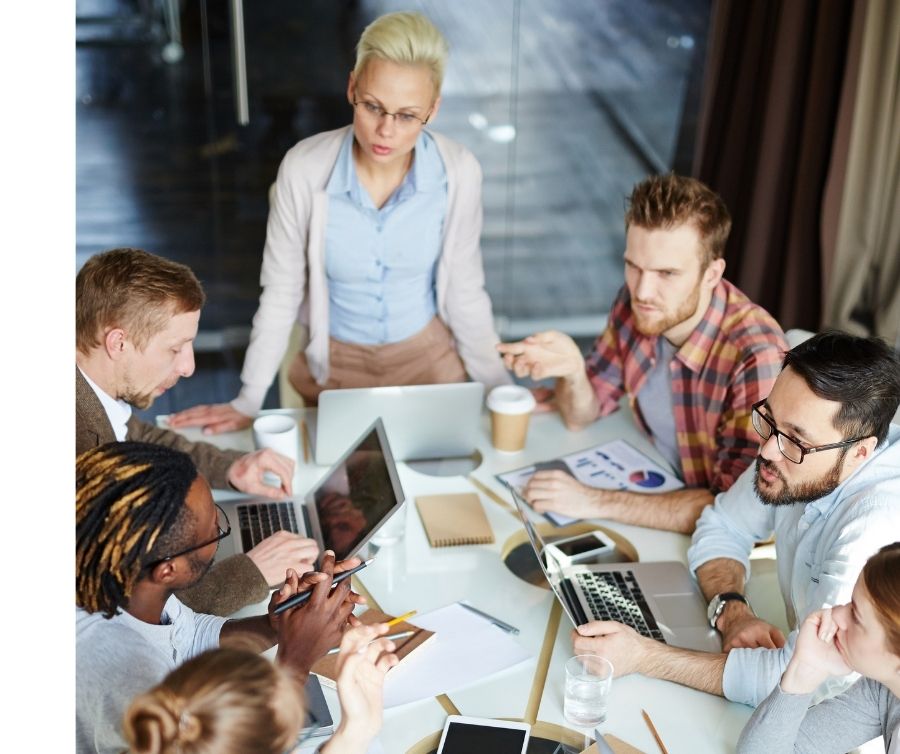
Szkolenie Online
Intro to Lean
Stosowanie zarządzania wizualnego
Problemy jako szansa do optymalizacji
Identyfikacja marnotrawstwa
Wdrażanie działań w ramach Kaizen
Zasady procesu nabywania wiedzy i umiejętności
Poniższe założenia odnoszą się tak naprawdę każdej płaszczyzny związanej z pozyskiwaniem doświadczenia. Jeżeli jednak zdajesz sobie sprawę z tego jak żmudnym i czasochłonnym wyzwaniem jest wprowadzanie nowych rozwiązań organizacji procesów, utrzymanie pracowników, podążanie za trendem technologii i potrzebą optymalizacji, z pewnością też zrozumiesz, że kultywowanie zasad może mieć nadrzędne znaczenie dla rozwoju przedsiębiorstwa.
1. Przedstaw jasno pracownikom czego się będą uczyć, a także wytłumacz dlaczego
Choć to operatorzy hali produkcyjnej mają przełożyć zdobytą wartość w faktyczne działanie, jako kierownik jesteś tak samo odpowiedzialny za potencjalny sukces. Wprowadź zespół precyzyjnie w tematykę warsztatów, dzięki temu będą mieli szansę ustosunkować się do ich zakresu, a także przygotować się mentalnie. Wytłumacz jaka jest przyczyna ich realizacji i odpowiedz na każde pytanie „dlaczego?”. To bardzo istotne, aby pracownik znał cel swojej nauki, a także był świadomy korzyści jakie może przynieść nowa wiedza. Co więcej, jeżeli Twoja wypowiedź wskaże mu sens i poczucie jego istotności w budowaniu wartości dla organizacji, będzie chętniej uczestniczył w spotkaniu, a następnie w faktycznej zmianie. Rozwiązania, które może nieść program szkolenia, takie jak możliwość wprowadzenia usprawnień, modyfikacji czasochłonnych i nieergonomicznych czynności, czy trudnych procedur, mogą stać się dla niego motywacją.
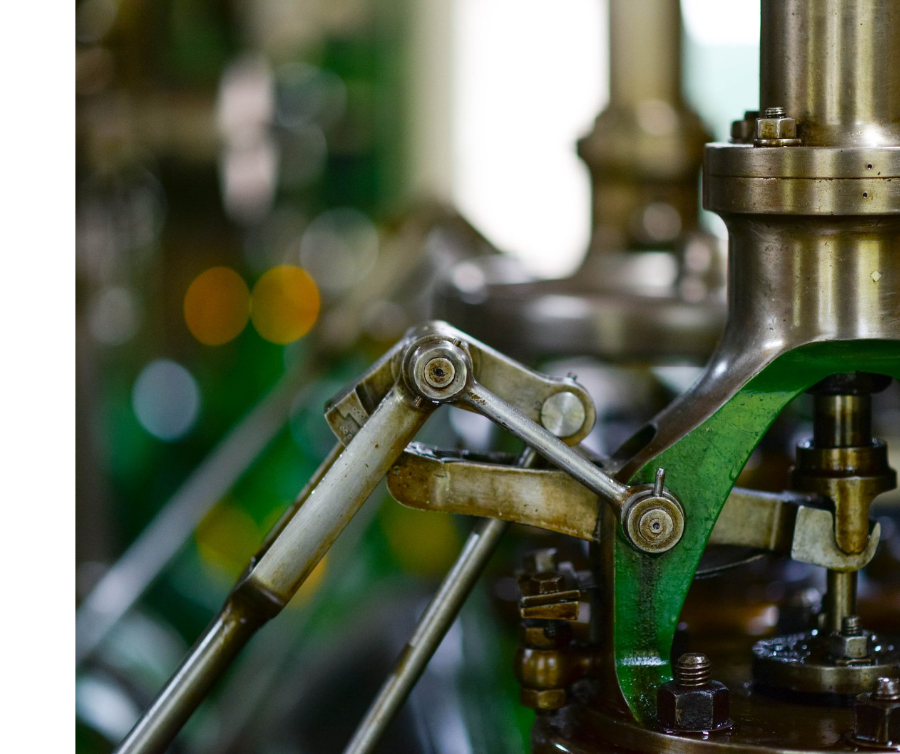
Rozpracujmy to na krótkim przykładzie: Uczestniczysz w organizacji szkolenia dla brygady techników i ustawiaczy maszyn. Kilka dni wcześniej zapowiedz inicjatywę, a na faktycznym spotkaniu przekaż: „Dzisiaj weźmiecie udział w warsztatach związanych z podniesieniem efektywności parku maszynowego. Nowa wiedza pozwoli wyeliminować Wam zbędne czynności, które ograniczają obecnie Waszą dyspozycyjność. Usprawnienie sposobu pracy oraz organizacja miejsca przy maszynie może wpłynąć na wyeliminowanie często zgłaszanych błędów w trakcie przezbrojenia, a także zredukować liczbę niezgodności. Oznacza to, że macie dużą szansę na zmniejszenie ilości awarii, które bywają frustrujące dla Was oraz operatorów, a także zakłócają płynną realizację zleceń. Wasza obecna wiedza, poszerzona o nowe doświadczenie może przynieść nowe sugestie rozwiązań i automatyzacji.”
2. Program szkolenia to podstawa
Program warsztatów Lean Management to duży krok w dobrym kierunku. Realizacja spotkania bez harmonogramu oraz jasnego podziału na etapy może spowodować omyłkowe przeoczenie pewnych zagadnień, niedokończenie zakładanego programu, czy wymknięcie się spoza ram czasowych. Przygotowany scenariusz pozwala na spójne przekazanie wiedzy, jej logiczne uporządkowanie, ustala ponadto balans między teorią, a praktyką.
3. Zadbaj o atmosferę współpracy
Choć może się wydawać, że nastrój i humor pracownika w danym momencie jest ostatnim z elementów, które przekładają się na dalsze rezultaty szkolenia, jest wręcz odwrotnie. Stres w związku z nowymi obowiązkami, strach przed zmianą, znudzenie zbyt długimi wykładami, zmęczenie, to bariery rozwojowe. Odpowiednie warunki warsztatów Lean, zapewnienie komfortu i pozytywnej atmosfery przyczynią się do większej motywacji, chęci zapamiętania przekazywanych zagadnień, a następnie ich przetestowania. Na pozytywną interakcję uczestników wpłyną również praca w grupie, ćwiczenia praktyczne, dyskusje i burze mózgów.
- Zadbaj o to, aby sala szkoleniowa oprócz miejsc siedzących miała również dodatkową przestrzeń do wykonywania zadań w ruchu.
- Obraz odtwarzanej prezentacji będzie bardziej przystępny dla operatorów, jeżeli na sali będzie projektor lub telewizor.
- Dobrze, aby w miejscu szkolenia znajdowała się również tablica, na której będzie można zapisać kluczowe zagadnienia, rozrysować przykłady, czy spisać pomysły z burzy mózgów.
- To miły gest w stronę pracowników, jeżeli na czas szkolenia zapewnisz im wodę do picia oraz symboliczne przekąski.
- Zrobisz kawał roboty, jeżeli delegując zespół na szkolenie, również będziesz w nim uczestniczył lub pojawisz się na jego początku, bądź końcu. Twoja obecność będzie świadczyć o Twoim zaangażowaniu.
- Jeżeli masz taką możliwość, postaraj się, aby chociaż część warsztatów odbywała się bezpośrednio w miejscu (gniazdo, linia, maszynownia, laboratorium), w którym pracownicy wykonują swoje codzienne obowiązki.
W tym wszystkim pamiętaj również jak ważną rolę w utrzymaniu dobrej atmosfery pełni trener. Jeżeli chcesz dokładnie przeanalizować jak wybierać szkolenia Lean, przejdź tutaj – Na co zwrócić uwagę przy wyborze szkoleń Lean?
4. Praktyka ma większą moc niż książkowe definicje
Największy wpływ i przełożenie na usystematyzowanie wiedzy mają interaktywne formy zajęć, a także analiza case’ów popartych ciekawymi przykładami. Nadmierna ilość złożonych definicji umknie pracownikom z głów jeszcze w trakcie szkolenia, czego z pewnością nie będzie można przekuć w działania przy procesach produkcyjnych.
Rozłóżmy ten sposób na przykładzie: Tym razem motywem przewodnim szkolenia jest nauka komunikacji i współpracy podczas rozwiązywania problemów produkcyjnych. Chcąc wprowadzić pracowników w ten temat oczywiście warto wprowadzić kilka zagadnień teoretycznych. Jednak główna część szkolenia powinna opierać się o wspólne ćwiczenie. Uczestnicy spotkania po otrzymaniu instruktażu sposobu postępowania, powinni dostać okazję osobistego przetestowania case’u – przenosząc go na warunki swojej organizacji. Ćwicząc opracowywanie sposobu zgłaszania problemów, systemu ich oceniania, czy mierzenia efektywności wdrożonych rozwiązań usystematyzują tym samym wiedzę, którą będą mogli przełożyć na dalszą praktykę na stanowisku pracy.
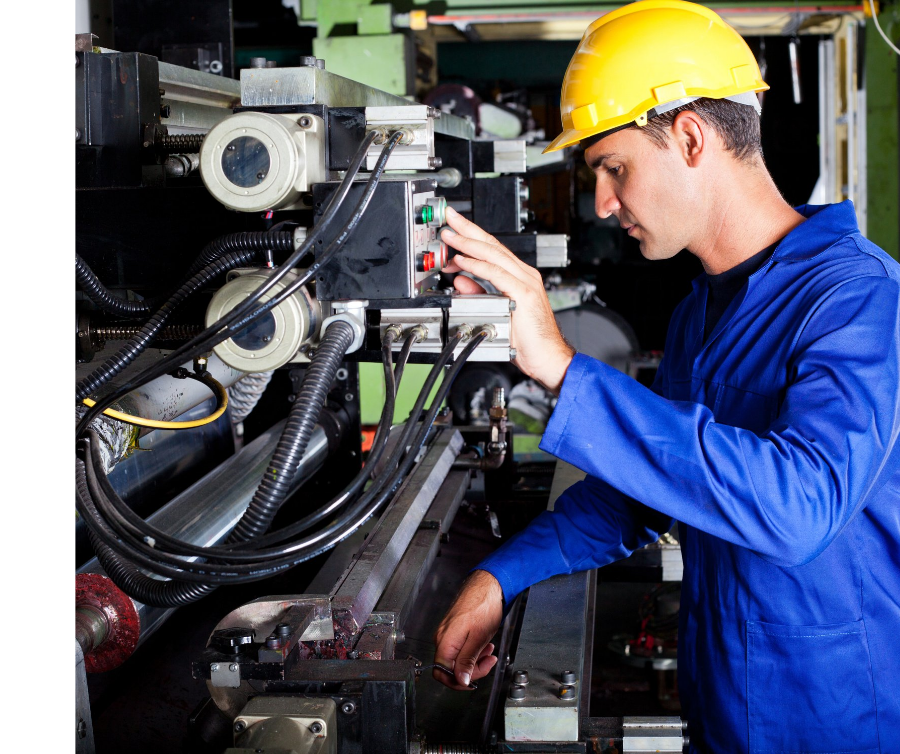
5. Trójkąt kompetencji – Wiedza, Umiejętności, Postawy
O tym czy szkolenie przełoży się na faktyczne rezultaty decyduje również podejście do jego realizacji. Jaki jest jego cel? Czy jest to potrzeba zdobycia nowej kwalifikacji, czy może faktycznych kompetencji? Sama w sobie kwalifikacja jest elementem wyjściowym procesu uczenia się i stanowi w głównej mierze formalne potwierdzenie, że takie działanie zostało wykonane zgodnie z założonymi wymaganiami. Kompetencję natomiast tworzą trzy elementy: wiedza, umiejętności oraz postawy. Oznacza to, że osoba posiadająca kompetencje w danej dziedzinie potrafi sprawnie oraz skutecznie wykonać określone zadania z oczekiwanym poziomem jakości. Łączy tym samym zdobyte informacje oraz dane, odpowiednio zarządzając nimi, komunikując się i wyznaczając cele, przejawiając przy tym swoje zaangażowanie i potrzebę współpracy. Jaki jest z tego wniosek? Kierowniku, nie organizuj szkoleń dla swojego zespołu dla samego certyfikatu, dobieraj trenerów, którzy są w stanie poszerzyć kompetencje Twojego zespołu.
6. Pracuj na procesie
Jednym z lepszych sposobów na przeprowadzenie skutecznego szkolenia, jest potraktowanie go jako bodźca do rozwiązania problemów oraz wypracowania usprawnień. Pracownicy, którzy nauczyli się nowych narzędzi Lean na swoim stanowisku, będą przypominać sobie ich zasady między innymi właśnie dlatego, że mieli okazję przetestować ich działanie w swoim środowisku. A ten kontekst i wykorzystanie sytuacji może realnie wpłynąć na jakość procesu.
7. Zadania nie tylko dla uczniów, ale również dla pracowników
Sposób może z początku wydawać się chybiony ze względu na ryzyko zniechęcenia operatora. Paradoksalnie odpowiednie zapowiedzenie kolejnego ćwiczenia wpłynie na utrwalanie wiedzy i budowanie nawyku. Wygospodaruj więc czas w grafiku operatora i zleć mu, aby np.: przez 1 godzinę swojej pracy skupił się na obserwacji czynności wykonywanych przez kolegę i zanotowaniu problemów oraz pomysłów. Nie będzie to dla Ciebie stratą, wręcz przeciwnie. Dzięki temu ta dwójka pracowników spojrzy na obowiązki oraz proces z zupełnie innej perspektywy, a co za tym idzie będą samodzielnie pracować nad utrzymaniem sprawdzonych sposobów pracy, bądź wprowadzeniem usprawnień.
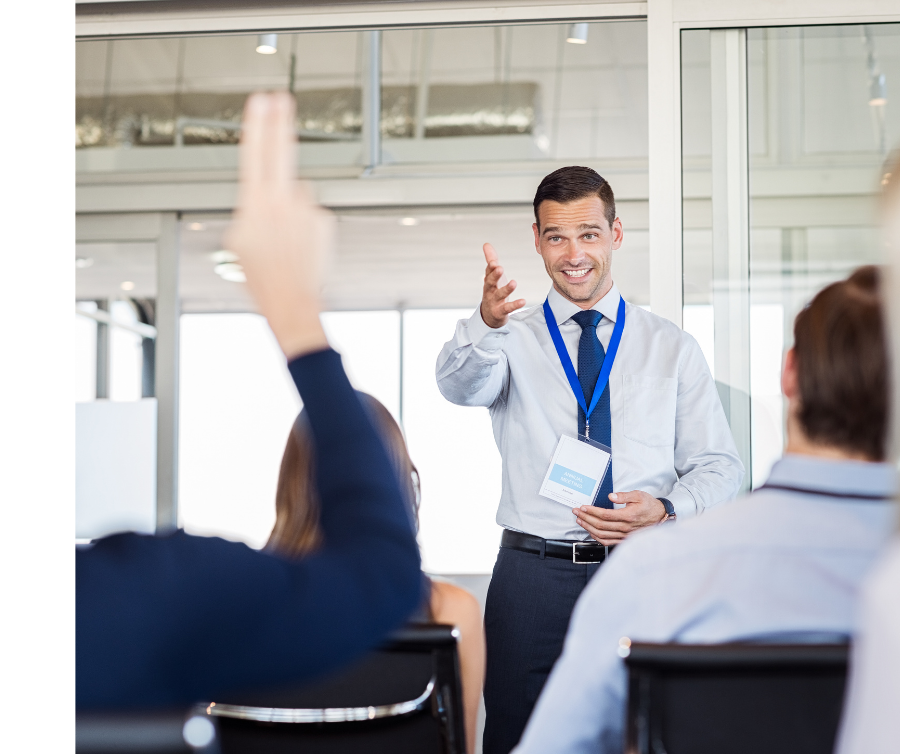
Zadanie ćwiczenia do domu też nie jest złym krokiem. Ta procedura powinna spowodować powrót operatora do refleksji z warsztatów, bynajmniej nie absorbując go nadmiernie i nie zabierając wolnego czasu. Możesz poprosić go o przygotowanie listy 5 marnotrawstw, które widzi w swojej codziennej pracy lub nakłonić do spisania 3 pomysłów, które jego zdaniem zmniejszą ilość błędów w trakcie operacji. Ta prosta czynność przyniesie podstawę do wspólnej analizy i wzbudzi w pracowniku poczucie zaangażowania. Skoro spisał swoje myśli, którymi mógł się następnie podzielić, warto, abyś podtrzymał jego zapał, udzielając swojej opinii lub pomagając wdrożyć najlepsze rozwiązania.
8. Buduj nawyki i zwiększaj efektywność
W tym punkcie ponownie powrócę do odpowiedzialności za potencjalny sukces. Patrząc ze strony kadry kierowniczej zaangażowanie, postawa ciekawości oraz chęć współpracy z pracownikami hali produkcyjnej wpływają na szansę skuteczności wdrożenia metod, bądź narzędzi Lean Management. Nawet najprostsze czynności stają się nawykami dopiero po ich wielokrotnym powtórzeniu. Stąd też do właśnie Lider odgrywa tak dużą rolę w utrzymaniu determinacji i samodyscypliny pracowników w utrzymaniu nowych założeń.
Jakie mogą być tego korzyści? Między innymi:
- wzrost efektywności procesów,
- zwiększenie motywacji do pracy,
- poczucie istotności w budowaniu kultury, w czym pomoże aplikacja ProblemBox
- poprawa poziomu jakości,
- chęć ciągłego doskonalenia, a także rozwoju osobistego.
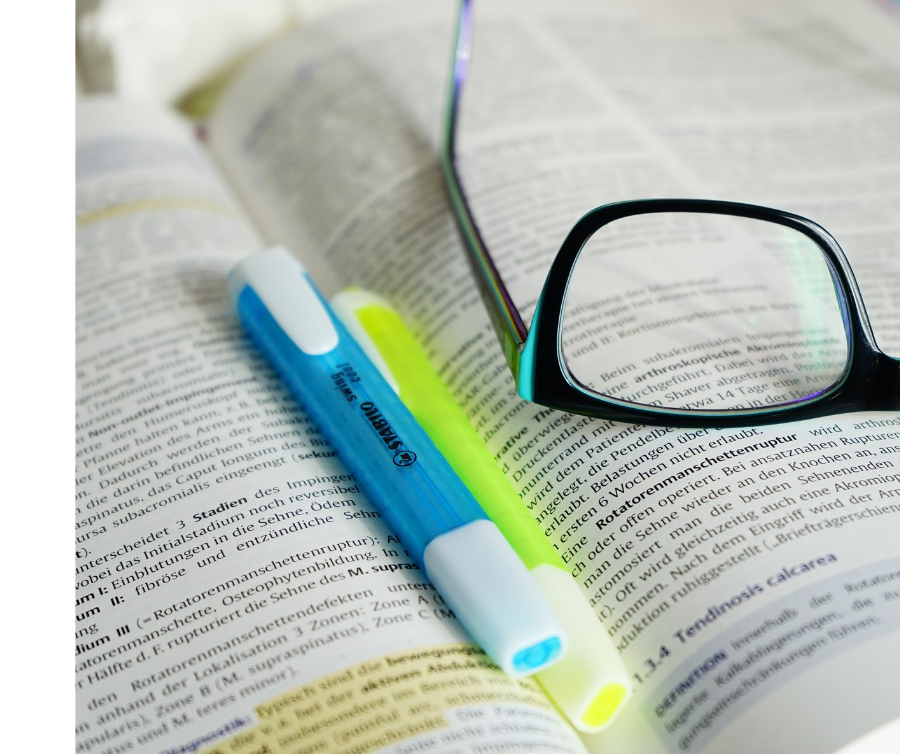
Odbierz poradnik — jak korzystać z zalet e-learningu?
Aby to zrobić, wypełnij formularz poniżej.
Co po szkoleniu?
Zasady te mogą mieć nieskończoną ilość parafraz, jednak najważniejsza jest przecież realizacja celu. Nie jest to symboliczna siódemka, czy marketingowe top ten, to osiem kluczowych punktów, które mogą przełożyć się na skuteczność szkoleń, a także ich dalsze rezultaty. Na tym jednak jeszcze nie koniec. Zespół Lean Action Plan realizując warsztaty, pracuje na realnych procesach. W trakcie zajęć wypracowywane są sposoby postępowania i wdrożenia rozwiązań, które następnie stają się faktycznym planem do działania w praktyce. Do tej układanki potrzebne jest jeszcze jedno ogniwo: Koordynator. Wyznacz go i wskaż mu, aby zadbał o utrzymanie zdobytej wiedzy oraz zastosowanie jej w codziennej pracy.
Jeżeli chcesz dowiedzieć się jak to wygląda w Lean Action Plan skontaktuj się z nami, wspólnie wypracujemy rozwiązanie! Razem z nami możesz podnosić kompetencje Twojego zespołu.
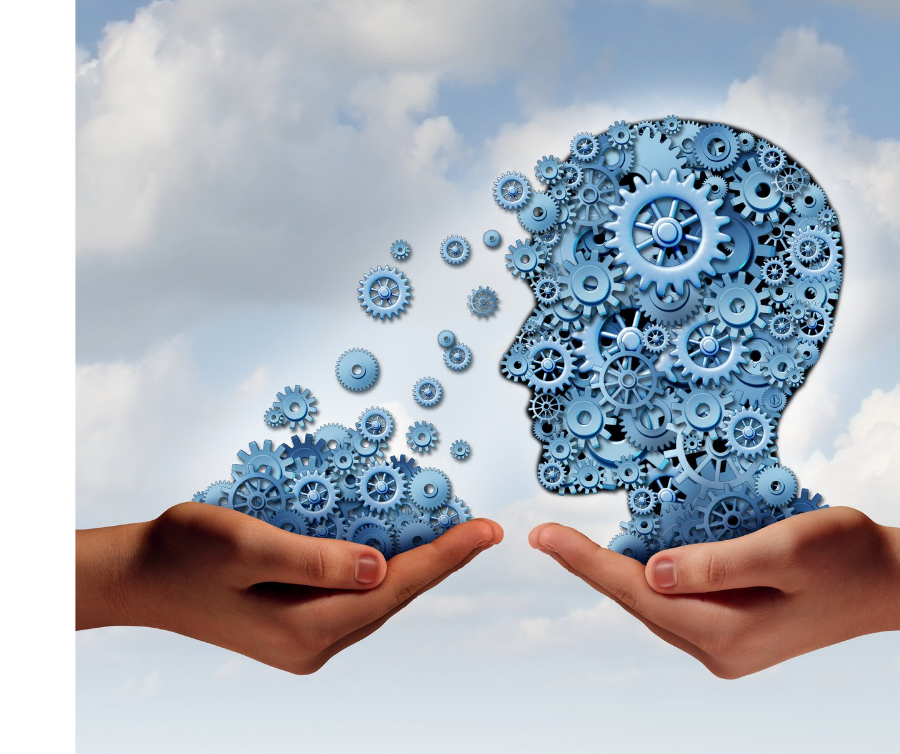
Szukasz szkolenia zamkniętego?
Zostaw numer, oddzwonimy i doradzimy, które szkolenie sprawdzi się w Twojej firmie.
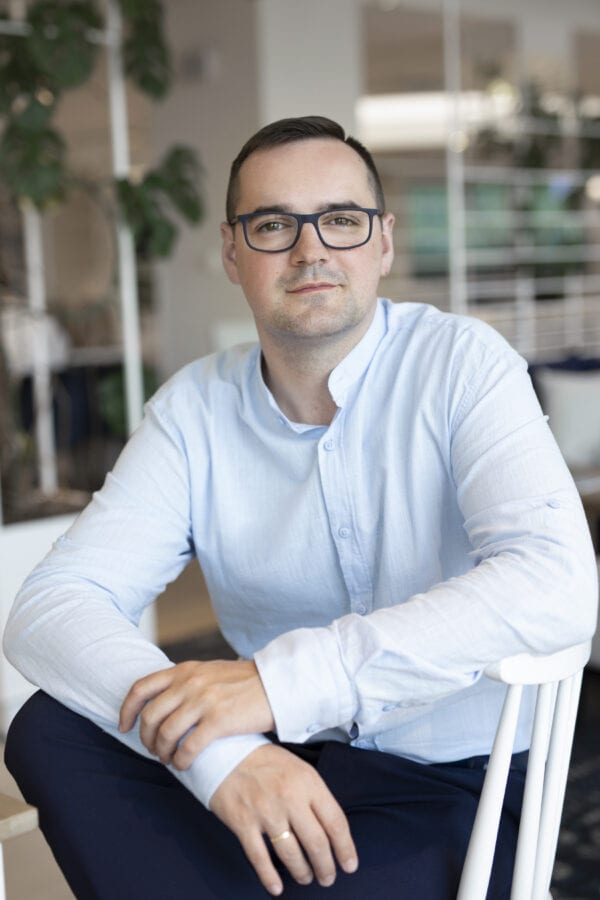