System kontroli jakości, czyli jak zmniejszyć ilość błędów?
Liczy się jakość, nie ilość – też to słyszałeś wielokrotnie? W branży produkcyjnej to nie do końca prawda – tu liczy się i jakość, i ilość. No właśnie – jak połączyć sprawną, terminową produkcję z wysoką jakością produktów? Na czym powinna opierać się kontrola jakości produktu, aby zminimalizować ryzyko nieprawidłowości? Jak powinno wyglądać wdrożenie kontroli jakości w firmie, a jeśli już w niej jest, to jak je usprawnić? Jak minimalizować błędy w kontroli jakości? Sprawdźmy wspólnie!
Podstawy kontroli jakości: Definicja i znaczenie
Zacznijmy od podstaw: definiowania kontroli jakości. Kontrola jakości` (QC) to proces, który ma na celu zapewnienie, że produkty lub usługi spełniają określone standardy jakościowe. Obejmuje to systematyczne działania podejmowane na różnych etapach produkcji lub świadczenia usług, aby zapobiec wadom i zapewnić zgodność z wymaganiami klientów oraz przepisami. Definicja kontroli jakości nie ogranicza się jedynie do inspekcji końcowego produktu; obejmuje również działania zapobiegawcze na różnych etapach procesu produkcyjnego. Znaczenie kontroli jakości polega na zapewnieniu, że produkt końcowy jest zgodny z wymaganiami technicznymi i oczekiwaniami klientów, co minimalizuje ryzyko reklamacji, zwrotów i strat finansowych. Ponadto, wysoka jakość produktów wzmacnia reputację firmy, zwiększa zadowolenie klientów i może prowadzić do zwiększenia udziału w rynku. Brand, który został wypracowany dzięki wysokim standardom kontroli i jakości mówi sam za siebie – i to jest atrakcyjne dla klientów.
Co to jest kontrola jakości i dlaczego jest ważna?
Kontrola jakości jest ważnym elementem zarządzania produkcją i usługami, mającym na celu zapewnienie zgodności produktów z określonymi standardami jakościowymi. Proces ten obejmuje monitorowanie, testowanie i inspekcję produktów na różnych etapach produkcji, aby wykryć i skorygować wady przed finalizacją produktu. Znaczenie efektywnego systemu kontroli jakości polega na zapobieganiu problemom, zanim dotrą one do klientów, co redukuje koszty związane z naprawą, wymianą i obsługą reklamacji. Kontrola jakości pomaga również w identyfikacji obszarów do poprawy w procesach produkcyjnych, co prowadzi do ciągłego doskonalenia. W konsekwencji, efektywny system kontroli jakości przyczynia się do zwiększenia konkurencyjności firmy, wzrostu zadowolenia klientów i długoterminowego sukcesu na rynku.
Zasady kontroli jakości: Jakie są podstawowe wymagania efektywnego systemu kontroli jakości?
Podstawowe zasady kontroli jakości obejmują kilka elementów, które są niezbędne do skutecznego zarządzania jakością. Po pierwsze, zaangażowanie kierownictwa jest fundamentalne – bez wsparcia na najwyższym szczeblu trudno jest wdrożyć i utrzymać skuteczny system kontroli jakości. Po drugie, kontrola jakości powinna być zintegrowana z całym procesem produkcji lub świadczenia usług, co oznacza, że każdy etap od projektowania po dostarczenie produktu końcowego powinien być monitorowany pod kątem jakości. Po trzecie, istotne jest stosowanie odpowiednich standardów i specyfikacji, które określają wymagania jakościowe. Kolejną zasadą jest regularne szkolenie pracowników, aby mieli oni niezbędne umiejętności i wiedzę do realizacji zadań związanych z kontrolą jakości. Wreszcie, niezbędne jest stosowanie metod statystycznych i analitycznych do monitorowania jakości oraz identyfikowania trendów i anomalii, co pozwala na szybkie reagowanie na potencjalne problemy.
Rodzaje kontroli jakości: Różne metody i ich zastosowanie
Istnieje wiele różnych metod kontroli jakości, z których każda ma swoje specyficzne zastosowania i korzyści. Do najpopularniejszych należą:
- Kontrola wejściowa (Incoming Quality Control, IQC): Polega na sprawdzaniu surowców i komponentów dostarczanych przez dostawców, zanim zostaną użyte w procesie produkcyjnym. Celem jest zapewnienie, że materiały te spełniają określone standardy jakościowe i są wolne od wad.
- Kontrola procesu (Process Quality Control, PQC): Obejmuje monitorowanie i kontrolę procesów produkcyjnych w czasie rzeczywistym, aby upewnić się, że są one zgodne z ustalonymi procedurami i standardami. Metody takie jak Six Sigma czy Statistical Process Control (SPC) są często stosowane do analizy i poprawy procesów produkcyjnych.
- Kontrola końcowa (Final Quality Control, FQC): To inspekcja i testowanie gotowych produktów przed ich wysyłką do klientów. FQC ma na celu upewnienie się, że produkty końcowe spełniają wszystkie wymagania jakościowe i są wolne od wad.
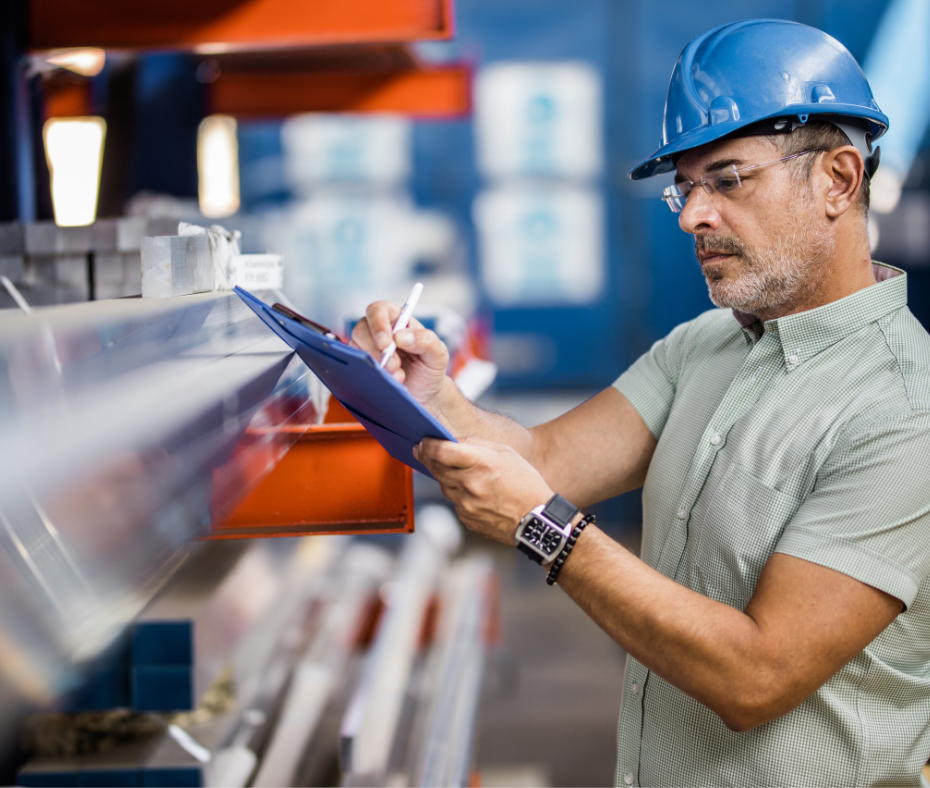
4. Kontrola statystyczna (Statistical Quality Control, SQC): Używa narzędzi statystycznych do monitorowania i kontrolowania procesów produkcyjnych. SQC obejmuje metody takie jak analiza pareto, diagramy przyczynowo-skutkowe i histogramy, które pomagają w identyfikacji i eliminacji przyczyn problemów jakościowych.
5. Audyt jakości (Quality Audit): Regularne przeglądy i oceny systemu zarządzania jakością, które mają na celu sprawdzenie zgodności z określonymi standardami i normami (np. ISO 9001). Audyty jakości pomagają w identyfikacji obszarów wymagających poprawy i zapewniają, że procesy są efektywne i zgodne z wymaganiami.
Każda z tych metod ma swoje zastosowania i może być dostosowana do specyficznych potrzeb organizacji, co pozwala na skuteczne zarządzanie jakością i zapewnienie najwyższych standardów produktów i usług.
Skuteczny system kontroli jakości
Skuteczny system kontroli jakości jest fundamentem każdego przedsiębiorstwa dążącego do zapewnienia wysokiej jakości swoich produktów lub usług. Taki system obejmuje zestaw procedur, standardów i narzędzi, które są stosowane w celu monitorowania, oceny i poprawy jakości na wszystkich etapach produkcji lub świadczenia usług. Istotnymi elementami skutecznego systemu kontroli jakości są zaangażowanie kierownictwa, szkolenia pracowników, systematyczne monitorowanie procesów oraz regularne audyty jakości. Wdrażanie i utrzymywanie wysokich standardów jakości przyczynia się do minimalizacji błędów, zwiększenia zadowolenia klientów oraz poprawy reputacji firmy na rynku. Ponadto, skuteczny system kontroli jakości pozwala na lepsze zarządzanie zasobami, redukcję kosztów związanych z wadami i reklamacjami oraz zwiększenie konkurencyjności przedsiębiorstwa.
Jak skuteczny system kontroli jakości wpływa na jakość produktu końcowego?
Skuteczny system kontroli jakości ma bezpośredni wpływ na jakość produktu końcowego. Dzięki systematycznemu monitorowaniu i analizie procesów produkcyjnych, możliwe jest wykrywanie i eliminowanie wad na wczesnych etapach produkcji, co minimalizuje ryzyko wystąpienia defektów w finalnym produkcie. Inspekcje surowców, półproduktów i gotowych produktów pozwalają na identyfikację niezgodności z wymaganiami jakościowymi, co umożliwia szybkie reagowanie i wprowadzenie korekt. Regularne testy i audyty jakościowe pomagają w utrzymaniu wysokich standardów, a także w ciągłym doskonaleniu procesów produkcyjnych. Skuteczny system kontroli jakości zapewnia, że produkty końcowe są zgodne ze specyfikacjami technicznymi i oczekiwaniami klientów, co przekłada się na wyższą satysfakcję klientów, redukcję liczby reklamacji i zwrotów oraz zwiększenie lojalności klientów.
Automatyzacja kontroli jakości: Nowoczesne podejście do zarządzania jakością
Automatyzacja kontroli jakości to nowoczesne podejście do zarządzania jakością, które wykorzystuje zaawansowane technologie, takie jak sztuczna inteligencja (AI), robotyka i systemy wizyjne, w celu zwiększenia precyzji, efektywności i niezawodności procesów kontrolnych. Automatyzowane systemy kontroli jakości mogą przeprowadzać inspekcje z dużą szybkością i dokładnością, identyfikując wady i niezgodności, które mogą być niewidoczne dla ludzkiego oka. Technologie takie jak AI mogą analizować dane w czasie rzeczywistym, przewidując potencjalne problemy i sugerując działania naprawcze. Automatyzacja kontroli jakości nie tylko poprawia dokładność i spójność ocen jakościowych, ale także zwiększa wydajność, redukując czas i koszty związane z ręcznymi inspekcjami. Przedsiębiorstwa, które inwestują w automatyzację kontroli jakości, mogą zyskać przewagę konkurencyjną, oferując produkty o wyższej jakości przy jednoczesnym obniżeniu kosztów produkcji.
Wizyjny system kontroli jakości: Technologia wspierająca procesy produkcyjne
Wizyjny system kontroli jakości (ang. Vision Inspection System) to technologia, która wykorzystuje kamery i oprogramowanie do analizy obrazów w celu automatycznego wykrywania wad i niezgodności w procesach produkcyjnych. Systemy te mogą być stosowane do kontroli różnorodnych aspektów jakości, takich jak wymiary, kształt, kolor, tekstura i inne cechy fizyczne produktów. Dzięki zaawansowanym algorytmom i technologiom przetwarzania obrazu, wizyjne systemy kontroli jakości są w stanie przeprowadzać szybkie i dokładne inspekcje, identyfikując nawet najmniejsze defekty, które mogą wpływać na jakość produktu końcowego.
Zastosowanie wizyjnych systemów kontroli jakości przynosi wiele korzyści, w tym zwiększenie dokładności i spójności ocen jakościowych, redukcję liczby wadliwych produktów opuszczających linię produkcyjną oraz poprawę efektywności procesów produkcyjnych. Dodatkowo, wizyjne systemy kontroli jakości mogą być łatwo zintegrowane z innymi systemami automatyki przemysłowej, co umożliwia pełną automatyzację i optymalizację procesów produkcyjnych. Pracodawcy, którzy wdrażają wizyjne systemy kontroli jakości, mogą nie tylko zwiększyć jakość swoich produktów, ale także zyskać przewagę konkurencyjną, dzięki oferowaniu bardziej niezawodnych i doskonałych wyrobów.
Oprogramowanie do zarządzania jakością: Narzędzie do usprawniania procesów
Oprogramowanie do zarządzania jakością (Quality Management Software, QMS) jest niezbędnym narzędziem dla firm dążących do utrzymania i poprawy standardów jakości. QMS automatyzuje i usprawnia procesy związane z zarządzaniem jakością, umożliwiając kompleksowe monitorowanie, analizowanie i raportowanie wszystkich aspektów jakości. Dzięki QMS firmy mogą zintegrować wszystkie działania związane z kontrolą jakości w jednym systemie, co pozwala na lepszą koordynację i zarządzanie procesami. Oprogramowanie to pomaga w dokumentowaniu procedur, zarządzaniu niezgodnościami, audytach, szkoleniach pracowników oraz w analizie danych, co pozwala na ciągłe doskonalenie procesów. Dzięki temu organizacje mogą szybko reagować na problemy jakościowe, minimalizując ryzyko wad i zwiększając efektywność operacyjną. Możesz połączyć też technologie kontroli z systemami zarządzania produkcją – przykładowo spersonalizowaną aplikacją ZaPro, która pozwala na zarządzanie procesem produkcji od A do Z.
Jak oprogramowanie do zarządzania jakością pomaga w monitorowaniu systemów kontroli?
Oprogramowanie do zarządzania jakością (QMS) pełni rolę w monitorowaniu systemów kontroli jakości poprzez automatyzację i centralizację zbierania danych oraz raportowania. QMS umożliwia bieżące śledzenie wskaźników jakościowych, takich jak wskaźniki wadliwości, czas realizacji, zgodność z normami oraz wyniki audytów. Automatyczne alerty i powiadomienia pozwalają na szybką reakcję na wszelkie odchylenia od normy, co minimalizuje ryzyko produkcji wadliwych produktów. Ponadto, QMS integruje dane z różnych etapów procesu produkcyjnego, co umożliwia pełen wgląd w cały cykl życia produktu. Systemy QMS często wyposażone są w zaawansowane funkcje analityczne i raportowe, które pomagają w identyfikacji trendów, analizie przyczyn źródłowych problemów oraz w ocenie efektywności wdrażanych działań naprawczych. Dzięki temu, firmy mogą nie tylko monitorować, ale również przewidywać i zapobiegać problemom jakościowym, co znacząco poprawia ogólną wydajność i jakość produktów.
Integracja kontroli jakości: Jak optymalizować procesy za pomocą nowoczesnych technologii?
Jak działają nowoczesne systemy kontroli jakości? Opierają się na nowoczesnych technologiach! Integracja kontroli jakości za pomocą nowoczesnych technologii, takich jak oprogramowanie QMS, systemy wizyjne i Internet Rzeczy (IoT), pozwala na optymalizację procesów produkcyjnych poprzez automatyzację, lepsze zarządzanie danymi i zwiększenie dokładności inspekcji. Nowoczesne technologie umożliwiają bezszwową integrację kontroli jakości z innymi systemami zarządzania, co pozwala na płynny przepływ informacji i koordynację działań.
Przykładowo, IoT pozwala na zbieranie danych w czasie rzeczywistym z różnych urządzeń i sensorów, co umożliwia natychmiastowe wykrywanie problemów jakościowych i podejmowanie działań naprawczych bez opóźnień. Systemy wizyjne mogą automatycznie kontrolować produkty na linii produkcyjnej, identyfikując wady, które mogą być niewidoczne dla ludzkiego oka, i automatycznie odrzucając wadliwe produkty. Integracja tych technologii z oprogramowaniem QMS pozwala na centralne zarządzanie wszystkimi danymi jakościowymi, co umożliwia bardziej efektywną analizę i raportowanie.
Nowoczesne technologie umożliwiają również wdrożenie predykcyjnej analizy jakości, która pozwala na przewidywanie potencjalnych problemów jakościowych na podstawie analizy historycznych danych i bieżących trendów. Dzięki temu firmy mogą proaktywnie zarządzać jakością, minimalizując ryzyko wystąpienia wad i poprawiając ogólną efektywność operacyjną. Integracja kontroli jakości z nowoczesnymi technologiami nie tylko poprawia dokładność i efektywność procesów produkcyjnych, ale też zwiększa elastyczność i zdolność do szybkiego reagowania na zmieniające się warunki rynkowe.
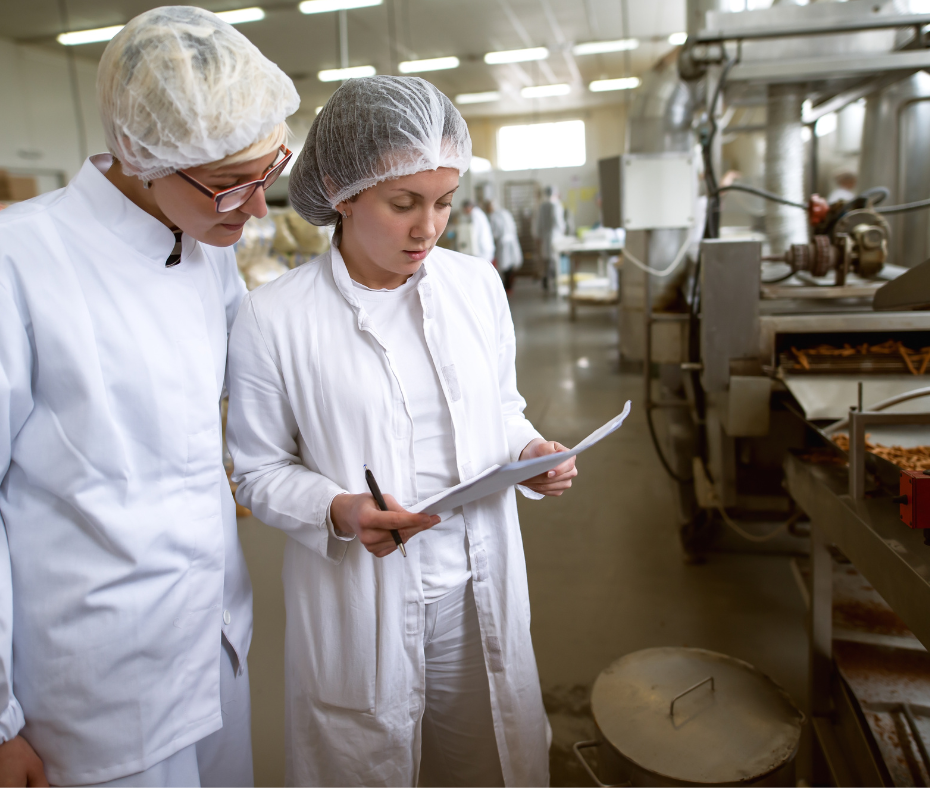
Kontrola jakości w procesie produkcyjnym: Etapy i procedury
Organizacja kontroli jakości w procesie produkcyjnym to złożony systematyczny proces, który obejmuje kilka etapów i procedur, mających na celu zapewnienie, że produkt końcowy spełnia określone standardy jakości. Proces ten zaczyna się od kontroli jakości wejściowej, przechodzi przez kontrolę procesów produkcyjnych i kończy się na kontroli końcowej. Każdy etap kontroli jakościowej ma swoje specyficzne procedury, które pomagają w identyfikacji i eliminacji wad, minimalizując ryzyko produkcji wadliwych produktów. Odpowiednia kontrola jakości jest integralną częścią zarządzania produkcją, która nie tylko pomaga w utrzymaniu wysokich standardów jakości, ale także w optymalizacji procesów produkcyjnych, redukcji kosztów i zwiększeniu satysfakcji klientów.
Kontrola jakości wejściowa: Pierwszy krok do zapewnienia wysokiej jakości
Kontrola jakości wejściowa (IQC) jest pierwszym etapem w procesie zapewniania jakości, obejmującym inspekcję surowców i komponentów dostarczanych przez dostawców. Celem IQC jest upewnienie się, że wszystkie materiały używane w produkcji spełniają określone specyfikacje i są wolne od wad. Procedury IQC obejmują inspekcje wizualne, testy fizyczne i chemiczne oraz sprawdzanie dokumentacji dostawców. W przypadku wykrycia niezgodności, surowce mogą zostać odrzucone lub zwrócone do dostawcy, co zapobiega wprowadzeniu wadliwych materiałów do procesu produkcyjnego. Odpowiednia kontrola jakości wejściowa minimalizuje ryzyko problemów jakościowych w późniejszych etapach produkcji i stanowi fundament dla utrzymania wysokich standardów jakości w całym procesie produkcyjnym.
Kontrola procesów produkcyjnych: Jak utrzymać wysoki standard produkcji?
Kontrola procesów produkcyjnych (PQC) to etap, który zapewnia, że każdy krok w procesie produkcyjnym jest realizowany zgodnie z ustalonymi standardami jakości. PQC obejmuje monitorowanie i kontrolę parametrów procesów produkcyjnych w czasie rzeczywistym, aby zapewnić zgodność z wymaganiami technicznymi i specyfikacjami. Procedury PQC mogą obejmować regularne inspekcje i testy, monitorowanie wskaźników procesowych oraz stosowanie narzędzi statystycznej kontroli procesu (SPC), takich jak diagramy kontrolne i analiza przyczynowo-skutkowa. Wykorzystanie nowoczesnych technologii, takich jak czujniki i systemy wizyjne, pozwala na automatyczne monitorowanie i wykrywanie odchyleń od normy, co umożliwia szybkie reagowanie i korygowanie problemów. Efektywna kontrola procesów produkcyjnych pomaga w utrzymaniu wysokiej jakości produktów, redukuje marnotrawstwo i zwiększa efektywność operacyjną.
Końcowa kontrola jakości: Ostatni etap zapewniający jakość produktu końcowego
Końcowa kontrola jakości (FQC) jest ostatnim etapem w procesie zapewniania jakości, polegającym na inspekcji i testowaniu gotowych produktów przed ich wysyłką do klientów. Celem kontroli jakości gotowych produktów jest upewnienie się, że produkty końcowe spełniają wszystkie wymagania jakościowe i są wolne od wad. Procedury FQC mogą obejmować inspekcje wizualne, testy funkcjonalne, testy wytrzymałościowe oraz sprawdzanie zgodności z normami i specyfikacjami. W przypadku wykrycia wad, produkty mogą zostać odrzucone lub skierowane do naprawy. Końcowa kontrola jakości jest fundamentalna dla zapewnienia, że tylko produkty spełniające najwyższe standardy trafiają do klientów, co minimalizuje ryzyko reklamacji i zwrotów, a także zwiększa satysfakcję klientów. Efektywna końcowa kontrola jakości jest więc niezbędna dla utrzymania wysokiej reputacji firmy na rynku i budowania długoterminowych relacji z klientami.
Zarządzanie działem jakości: Organizacja i planowanie
Zarządzanie działem jakości w firmach produkcyjnych wymaga starannej organizacji i planowania, aby zapewnić skuteczne wdrożenie polityk jakościowych i utrzymanie wysokich standardów produkcji. Dział jakości jest odpowiedzialny za opracowanie strategii jakościowej, która obejmuje ustanowienie procedur, standardów oraz metod kontroli i monitorowania procesów produkcyjnych. Organizacja działu jakości powinna obejmować wyznaczenie klarownych ról i obowiązków dla członków zespołu, co pozwala na efektywne zarządzanie zadaniami i komunikację wewnętrzną. Planowanie w dziale jakości obejmuje również regularne audyty, szkolenia pracowników oraz ciągłe doskonalenie procesów na podstawie analiz i raportów jakościowych. Skuteczne zarządzanie działem jakości wymaga również współpracy z innymi działami firmy, aby zapewnić integralność i zgodność wszystkich działań produkcyjnych z wymogami jakościowymi.
Rola działu jakości w firmach produkcyjnych: Jakie są jego zadania i obowiązki?
Dział jakości odgrywa rolę w firmach produkcyjnych, pełniąc szereg istotnych zadań i obowiązków, które mają na celu zapewnienie, że wszystkie produkty spełniają określone standardy jakościowe. Do głównych zadań działu jakości należy opracowanie i wdrażanie systemów zarządzania jakością, które obejmują procedury kontrolne, dokumentację oraz szkolenia pracowników. Dział jakości jest również odpowiedzialny za przeprowadzanie regularnych inspekcji i testów na różnych etapach produkcji, od kontroli surowców po końcową inspekcję gotowych produktów. Kolejnym ważnym obowiązkiem jest monitorowanie i analizowanie danych jakościowych, identyfikowanie trendów i potencjalnych problemów oraz wdrażanie działań korygujących i zapobiegawczych. Dział jakości współpracuje także z dostawcami w celu zapewnienia, że dostarczane materiały spełniają wymagania jakościowe. Dodatkowo, zarządza reklamacjami klientów, prowadzi audyty wewnętrzne i zewnętrzne oraz zapewnia zgodność z międzynarodowymi standardami i regulacjami jakościowymi, takimi jak ISO 9001.
Szkolenie Online
Budowanie zaangażowania i odpowiedzialności pracowników
motywowanie i angażowanie pracowników
wpływanie na percepcję innych osób
wprowadzanie zmiany w myśleniu i zachowaniu swoich pracowników
wykorzystanie użytecznych schematów myślenia
Plan i wdrożenie działu jakości: Jak efektywnie zarządzać zespołem?
Efektywne zarządzanie zespołem w dziale jakości wymaga precyzyjnego planowania i wdrożenia odpowiednich strategii, które pozwolą na osiągnięcie założonych celów jakościowych. Pierwszym krokiem jest zdefiniowanie misji i celów działu jakości oraz stworzenie jasnych procedur i standardów operacyjnych. Ważne jest również wyznaczenie kompetentnych liderów, którzy będą odpowiedzialni za koordynację działań zespołu i monitorowanie postępów. Planowanie obejmuje także szkolenie pracowników w zakresie najlepszych praktyk jakościowych oraz regularne sesje doskonalące, które pomagają utrzymać wysoki poziom wiedzy i umiejętności.
Ważnym elementem zarządzania zespołem jakości jest komunikacja. Regularne spotkania zespołowe, podczas których omawiane są wyniki jakościowe, problemy oraz sugestie dotyczące poprawy, sprzyjają lepszej koordynacji działań i zaangażowaniu pracowników. Warto również wdrożyć systemy motywacyjne, które zachęcają pracowników do aktywnego uczestnictwa w procesach doskonalenia jakości. Dobra komunikacja to również rozwiązywanie problemów – co jest trudniejszym elementem. Sprawdź szkolenie: Problem solving, które pozwoli Ci rozwiązywać problemy w zespole bez tworzenia nieprzyjaznej atmosfery.
Kolejnym istotnym aspektem jest monitorowanie i analiza danych jakościowych. Wdrożenie nowoczesnych narzędzi do zarządzania jakością, takich jak systemy QMS (Quality Management System), umożliwia efektywne zbieranie, analizowanie i raportowanie danych, co pozwala na szybką identyfikację problemów i wdrażanie działań naprawczych. Stała kontrola i audytowanie procesów produkcyjnych pomagają w utrzymaniu zgodności z ustalonymi standardami jakości oraz w wykrywaniu i eliminowaniu odchyleń.
W efektywnym zarządzaniu zespołem jakości bardzo ważne jest także promowanie kultury jakości w całej organizacji. Oznacza to angażowanie wszystkich pracowników, niezależnie od ich roli, w procesy poprawy jakości i zachęcanie ich do zgłaszania uwag oraz pomysłów na usprawnienia. Takie podejście buduje poczucie odpowiedzialności za jakość na każdym poziomie organizacji i sprzyja tworzeniu środowiska, w którym jakość jest priorytetem.
Korzyści z wdrożenia systemów kontroli jakości
Wdrożenie systemów kontroli jakości przynosi liczne korzyści dla organizacji, które przekładają się na poprawę efektywności operacyjnej, zadowolenia klientów i ogólnej konkurencyjności firmy. Systemy te pozwalają na systematyczne monitorowanie i analizowanie procesów produkcyjnych, co umożliwia wczesne wykrywanie i eliminowanie wad oraz minimalizowanie ryzyka produkcji wadliwych produktów. Dzięki automatyzacji i integracji różnych aspektów kontroli jakości, organizacje mogą lepiej zarządzać zasobami, co prowadzi do redukcji kosztów związanych z naprawą, reklamacji i zwrotami produktów. Ponadto, wdrożenie systemów kontroli jakości pomaga w spełnianiu wymogów regulacyjnych i standardów branżowych, co jest istotne dla utrzymania licencji i certyfikatów. Systemy te również wspierają procesy doskonalenia jakości poprzez gromadzenie danych i analizowanie wyników, co umożliwia ciągłe wprowadzanie ulepszeń i optymalizacji procesów.
Jak kontrola jakości przyczynia się do zwiększenia jakości produktów?
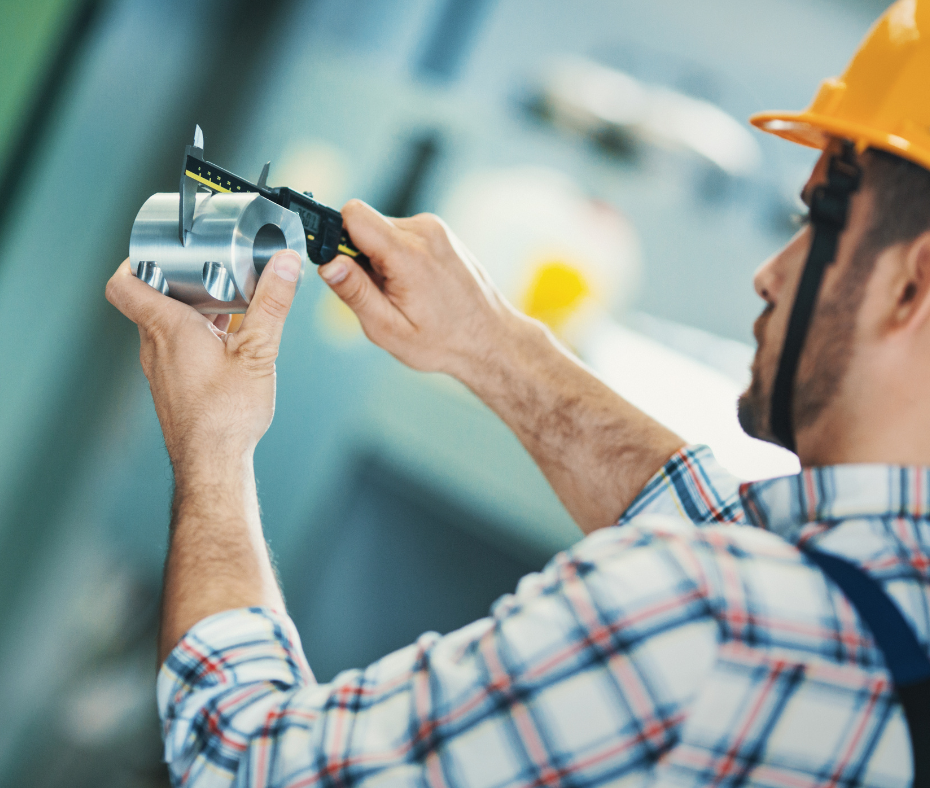
Kontrola jakości odgrywa rolę w zwiększaniu jakości produktów poprzez systematyczne monitorowanie, inspekcje i testy na różnych etapach produkcji. Proces ten zaczyna się od kontroli wejściowej surowców, które muszą spełniać określone standardy jakościowe, aby zostały dopuszczone do produkcji. Na etapie produkcji, kontrola jakości obejmuje monitorowanie parametrów procesów produkcyjnych, co pozwala na szybkie wykrywanie i korygowanie odchyleń od normy. Dzięki temu można zapobiegać powstawaniu wadliwych produktów już na wczesnym etapie produkcji.
Końcowa kontrola jakości zapewnia, że gotowe produkty spełniają wszystkie wymagania jakościowe, zanim trafią do klientów. Regularne testy i audyty jakościowe pomagają w utrzymaniu wysokich standardów oraz w identyfikacji obszarów wymagających poprawy. Skuteczna kontrola jakości nie tylko minimalizuje ryzyko wystąpienia wadliwych produktów, ale także zwiększa zaufanie klientów do marki, co przekłada się na większą lojalność i pozytywne rekomendacje.
Utrzymanie wysokiej jakości: Długoterminowe korzyści z efektywnej kontroli jakości
Utrzymanie wysokiej jakości produktów poprzez efektywną kontrolę jakości przynosi długoterminowe korzyści dla organizacji. Przede wszystkim, konsekwentne dostarczanie wysokiej jakości produktów zwiększa zadowolenie klientów, co prowadzi do wzrostu lojalności i pozytywnych opinii o marce. Zadowoleni klienci są bardziej skłonni do ponownych zakupów oraz rekomendacji firmy innym, co sprzyja zwiększeniu udziału w rynku i generowaniu wyższych przychodów.
Efektywna kontrola jakości również przyczynia się do redukcji kosztów związanych z naprawą, reklamacjami i zwrotami produktów. Systematyczne monitorowanie i wczesne wykrywanie problemów pozwala na szybkie podejmowanie działań naprawczych, co minimalizuje straty finansowe i operacyjne. Ponadto, wdrożenie systemów kontroli jakości pomaga w optymalizacji procesów produkcyjnych, co prowadzi do zwiększenia wydajności i efektywności operacyjnej.
Długoterminowe korzyści z efektywnej kontroli jakości obejmują również wzmocnienie pozycji konkurencyjnej firmy. Przedsiębiorstwa, które konsekwentnie dostarczają wysokiej jakości produkty, budują silną reputację na rynku, co przyciąga nowych klientów i partnerów biznesowych. Efektywna kontrola jakości sprzyja również innowacjom i ciągłemu doskonaleniu procesów, co pozwala firmie na szybką adaptację do zmieniających się wymagań rynkowych i technologicznych. W rezultacie, organizacje mogą utrzymać przewagę konkurencyjną i osiągać długoterminowy sukces.
Podsumowanie
Wdrożenie kontroli jakości, usprawnianie kontroli jakości, monitorowanie działu jakości… Wszystkie te działania wprowadzamy po to, aby uzyskiwać produkty spełniające standardy nawet najbardziej wymagających klientów. Właśnie dlatego tak ważny jest poziom kontroli – zapewnienie jakości finalnego produktu od niego zależy. Korzyści z kontroli jakości to przede wszystkim przeciwdziałanie błędom i zapewnienie efektywności produkcji. Zrobotyzowana kontrola jakości ułatwia to zadanie – odpowiednie systemy i oprogramowanie pozwalają na optymalizację kontroli jakości, zarówno pod względem efektywności oraz jakości jej samej. Nowoczesna kontrola jakości ułatwia zarządzanie procesem i nie wpływa negatywnie na efektywność produkcji – co najwyżej sprawia, że proces wytwarzania produktów stanie się jeszcze bardziej efektywnym procesem.
Pobierz bazę 100 wskaźników produkcyjnych
za darmo!
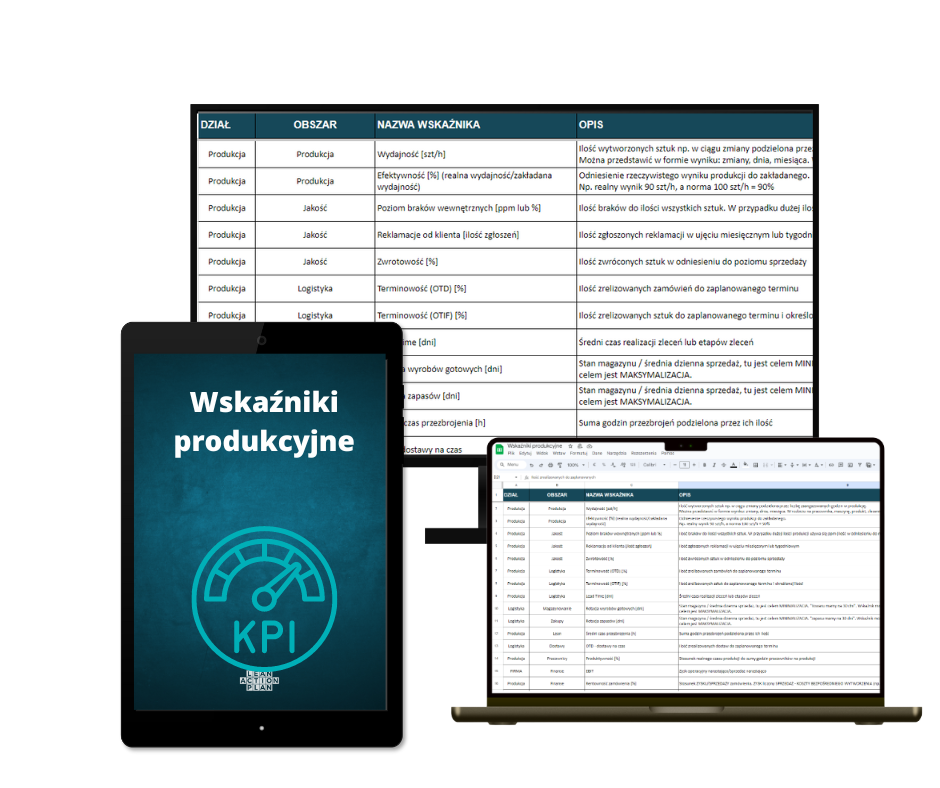