Koszty jakości w produkcji – jak zarządzać i redukować straty?
Koszty jakości w produkcji to jeden z kluczowych elementów, które mają wpływ na rentowność przedsiębiorstwa. Efektywne zarządzanie tymi kosztami nie tylko pozwala na poprawę jakości produktów, ale także na zwiększenie wydajności i redukcję niepotrzebnych wydatków. Przedsiębiorstwa, które skutecznie zarządzają kosztami jakości, są w stanie osiągnąć wyższy poziom efektywności produkcji, a także zwiększyć swoją konkurencyjność na rynku. Jakie są koszty jakości, jak obliczać ich wysokość, i co można zrobić, aby je zredukować?
Spis treści:
- Co to są koszty jakości na produkcji?
- Rodzaje kosztów jakości na produkcji.
- Jak obliczyć koszty jakości na produkcji?
- Jak zredukować koszty jakości na produkcji?
- Rola kultury jakości w zarządzaniu kosztami.
- Jak skutecznie zarządzać kosztami jakości na produkcji?
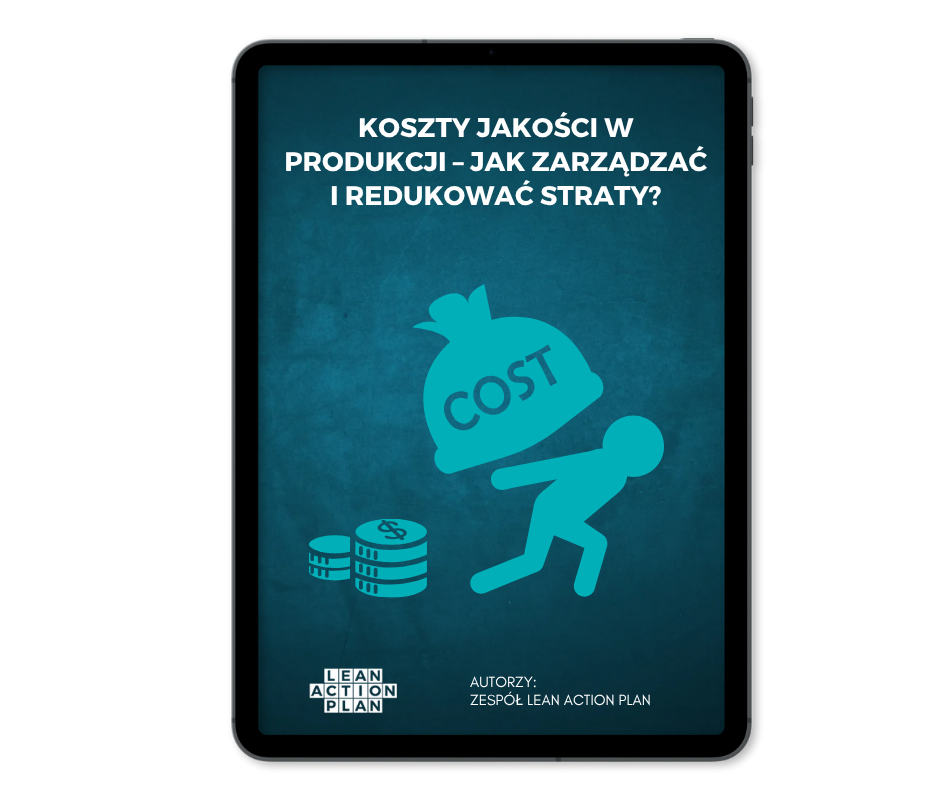
Co to są koszty jakości na produkcji?
Koszty jakości w produkcji obejmują wszelkie wydatki związane z zapewnieniem odpowiednich standardów jakościowych. Są to koszty, które firma ponosi, aby utrzymać jakość produktów, jak również te związane z naprawą błędów i stratami wynikającymi z niezadowalającej jakości. Koszty jakości dzielą się na różne kategorie, które obejmują zarówno koszty zapobiegania problemom, jak i koszty ich usuwania. Zrozumienie tych kosztów jest kluczowe dla przedsiębiorstw, które dążą do optymalizacji procesów produkcyjnych i zwiększenia rentowności.
Dlaczego zarządzanie kosztami jakości jest istotne w produkcji?
Wysokie koszty jakości mogą znacząco wpływać na rentowność firmy produkcyjnej. Zbyt wysokie nakłady na kontrolę jakości, usuwanie błędów czy reklamacje mogą prowadzić do znacznych strat finansowych. Dlatego tak ważne jest skuteczne zarządzanie tymi kosztami. Optymalizacja kosztów jakości nie tylko redukuje straty, ale również poprawia ogólną efektywność produkcji. Firmy, które skutecznie zarządzają jakością, osiągają wyższą konkurencyjność i zadowolenie klientów, co w dłuższej perspektywie przyczynia się do ich sukcesu na rynku.
Rodzaje kosztów jakości na produkcji
Koszty jakości w produkcji dzielą się na różne kategorie, z których każda ma swoją specyfikę i wpływ na rentowność firmy. Zrozumienie tych rodzajów jest kluczowe dla skutecznego zarządzania procesami produkcyjnymi i optymalizacji wydatków. Głównym rodzajem kosztów jakości, są takie koszty jak: koszty prewencyjne, oceny, awaryjne i wewnętrzne. Jaka jest ich rola w kontekście zarządzania jakością?
Koszty prewencyjne – zapobieganie błędom i awariom
Koszty prewencyjne to koszty ponoszone na działania zapobiegające wystąpieniu problemów związanych z jakością. Obejmuje to szkolenia dla pracowników, inwestowanie w nowoczesne technologie, oraz wdrażanie procedur jakościowych, które pozwalają unikać błędów w procesie produkcyjnym. Przykłady działań prewencyjnych to:
- regularne szkolenie pracowników w zakresie standardów jakości,
- utrzymywanie i modernizacja maszyn produkcyjnych,
- wprowadzenie procedur kontrolnych na każdym etapie produkcji.
Inwestowanie w te działania pozwala na obniżenie kosztów związanych z naprawą błędów i reklamacjami, a także zwiększa efektywność produkcji.
Koszty oceny – kontrola jakości i audyty
Koszty oceny dotyczą działań związanych z kontrolą jakości, audytami oraz testowaniem produktów przed ich wprowadzeniem na rynek. Obejmuje to zarówno kontrolę jakości wewnętrzną, jak i zewnętrzną. Przykłady kosztów oceny to:
- koszty audytów jakościowych,
- płatności za testy jakościowe,
- koszty analizy wyników produkcji.
Chociaż kontrola jakości jest niezbędna do zapewnienia zgodności produktów z wymaganiami, nadmierna ilość testów i procedur kontrolnych może prowadzić do wysokich kosztów. Ważne jest, aby utrzymywać równowagę pomiędzy kontrolą jakości a efektywnością procesów.
Koszty awaryjne – naprawa błędów i reklamacje
Koszty awaryjne to koszty związane z błędami w produkcji, które wymagają naprawy. Mogą to być zarówno naprawy wewnętrzne, jak i zewnętrzne (np. reklamacje klientów). Przykłady kosztów awaryjnych to:
- naprawy wadliwych produktów,
- koszty związane z wymianą produktów,
- wydatki na reklamacje i zwroty.
Koszty te są szczególnie wysokie, gdy błędy w produkcji są wykrywane po dostarczeniu produktów do klientów. Dlatego tak ważne jest inwestowanie w zapobieganie błędom i poprawę kontroli jakości, aby uniknąć kosztów związanych z naprawą błędów.
Koszty wewnętrzne – straty związane z niespełnianiem norm jakościowych
Koszty wewnętrzne to straty, które wynikają z niewłaściwego wykonania produktów, które nie spełniają ustalonych norm jakościowych. Może to obejmować odpady, usunięte części produkcyjne, a także nadmierne zużycie surowców. Przykłady kosztów wewnętrznych to:
- odpady produkcyjne,
- zniszczone surowce,
- utracona produkcja z powodu błędów w procesie.
Te straty często mogą być wynikiem nieodpowiednich standardów jakościowych w firmie. Właściwa kontrola jakości i optymalizacja procesów produkcyjnych pozwala na ich zminimalizowanie.
WSZECHSTRONNY INŻYNIER JAKOŚCI
Praktyczne zastosowanie narzędzi jakości
Znajomość etapów procesu APQP i PPAP
Prowadzenie oceny sprawności systemów pomiarowych
Dostrzeganie i eliminacja źródeł marnotrawstwa
Jak obliczyć koszty jakości na produkcji?
Obliczanie kosztów jakości wymaga uwzględnienia wielu czynników, które wpływają na proces produkcji.
Metody obliczania kosztów jakości w firmie produkcyjnej
Obliczanie kosztów jakości na produkcji wymaga uwzględnienia różnych kategorii kosztów: prewencyjnych, oceny, awaryjnych i wewnętrznych. Można to zrobić, stosując metody takie jak:
- Analiza kosztów działalności prewencyjnej – określenie, ile firma wydaje na zapobieganie błędom.
- Koszty kontroli jakości – obliczenie wydatków na testy i audyty jakościowe.
- Koszty naprawy błędów i reklamacji – uwzględnienie wydatków na naprawy i zwroty produktów.
- Straty wewnętrzne – obliczenie wartości odpadów i straconych surowców.
Przy obliczaniu kosztów jakości ważne jest, aby systematycznie monitorować wszystkie wydatki związane z jakością i wdrożyć odpowiednią politykę optymalizacji tych kosztów.
Przykłady obliczania kosztów jakości na produkcji
Przykład 1: Jeśli firma wyprodukuje 10 000 jednostek, a 2% z nich zostaną uznane za wadliwe i wymienione, koszty jakości można obliczyć, uwzględniając wartość wadliwych produktów, koszty wymiany oraz naprawy.
Przykład 2: W przypadku zastosowania procedur prewencyjnych, firma może zmniejszyć liczbę wadliwych produktów, a koszty związane z naprawami i reklamacjami mogą spaść o 20%. Wówczas oszczędności można obliczyć na podstawie tych zmniejszonych kosztów.
Jak zredukować koszty jakości na produkcji?
Redukcja kosztów jakości to jedno z kluczowych wyzwań dla firm produkcyjnych, które dążą do poprawy efektywności. Konkretne strategie i metody pomagają zredukować koszty związane z jakością, takie jak optymalizacja procesów kontrolnych, automatyzacja oraz szkolenie pracowników. Jak wdrożenie odpowiednich działań może pozytywnie wpłynąć na rentowność i jakość produktów?
Optymalizacja procesów kontrolnych i audytów
Optymalizacja procesów kontrolnych to kluczowy sposób na obniżenie kosztów jakości. Poprzez usprawnienie procedur testowania, audytów oraz kontroli jakości, firmy mogą zmniejszyć liczbę błędów i wadliwych produktów. Wdrożenie zautomatyzowanych systemów kontroli, takich jak systemy wizyjne czy czujniki jakościowe, pozwala na szybkie wykrywanie błędów już na wczesnym etapie produkcji.
Automatyzacja procesów jakościowych
Automatyzacja procesów jakościowych może znacznie obniżyć koszty jakości. Dzięki nowoczesnym narzędziom i systemom, takim jak sztuczna inteligencja i robotyka, procesy kontrolne stają się bardziej precyzyjne i szybsze, co pozwala zaoszczędzić czas i zasoby. Wprowadzenie automatycznych systemów do monitorowania jakości produktów w czasie rzeczywistym zapewnia wyższą dokładność oraz minimalizuje ryzyko błędów.
Rola kultury jakości w zarządzaniu kosztami
Kultura jakości w firmie produkcyjnej odgrywa kluczową rolę w skutecznym zarządzaniu kosztami jakości. Wdrażanie kultury jakości sprzyja ciągłemu doskonaleniu procesów, eliminacji marnotrawstwa i poprawie jakości produktów. Zrozumienie tej kultury i jej wpływu na codzienne operacje jest niezbędne do osiągnięcia trwałych korzyści związanych z redukcją kosztów.
Wdrażanie kultury jakości w firmie produkcyjnej
Wdrażanie kultury jakości w organizacji jest kluczowe dla długoterminowego sukcesu i redukcji kosztów. Kultura jakości polega na włączeniu zasad jakości do codziennej pracy pracowników i menedżerów. Firmy, które wdrażają kulturę jakości, skupiają się na ciągłym doskonaleniu procesów, eliminacji marnotrawstwa i poprawie wyników produkcyjnych. Pracownicy są bardziej świadomi swojej roli w zapewnianiu jakości, a to przekłada się na zmniejszenie błędów i kosztów.
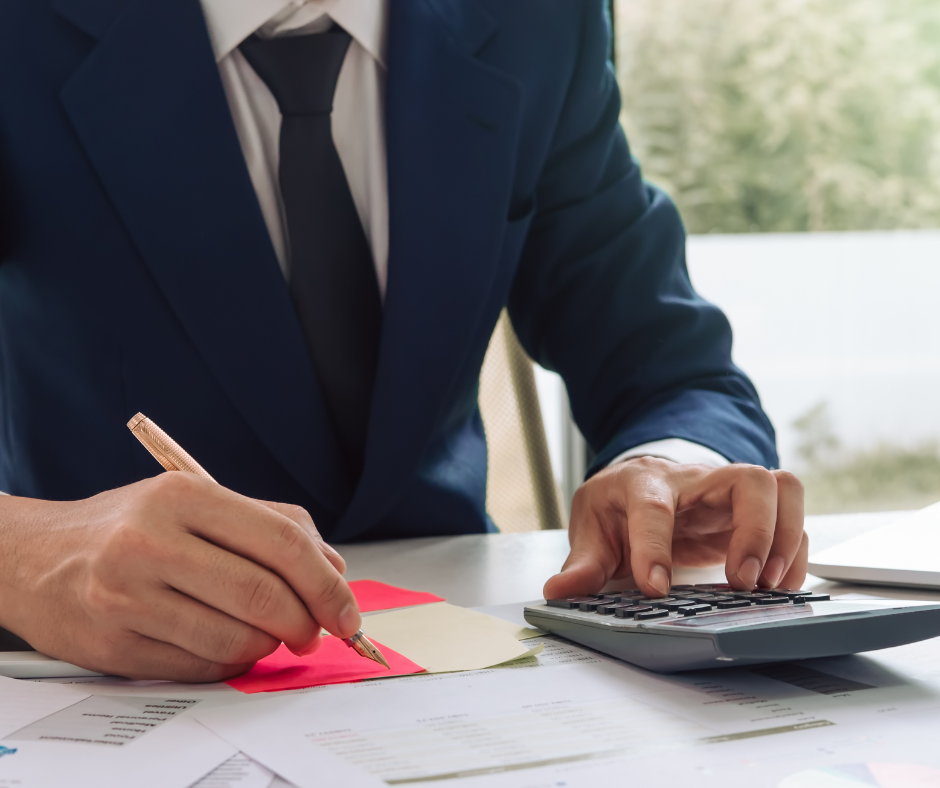
Szkolenie pracowników w zakresie jakości
Regularne szkolenia z zakresu jakości są niezbędne, aby pracownicy byli dobrze przygotowani do utrzymywania wysokich standardów jakości. Szkolenia powinny obejmować zarówno techniczne aspekty kontroli jakości, jak i umiejętności analizy danych jakościowych. Zwiększenie świadomości na temat jakości wśród pracowników pozwala na wczesne wykrywanie problemów, co ogranicza koszty związane z błędami i poprawkami.
Jak skutecznie zarządzać kosztami jakości na produkcji?
Zarządzanie kosztami jakości to proces wymagający konsekwencji i zastosowania sprawdzonych metod. W tym rozdziale przedstawimy kluczowe zasady, które pozwalają na efektywne zarządzanie tymi kosztami w firmie produkcyjnej. Jakie narzędzia i strategie warto wdrożyć, by nie tylko zredukować koszty, ale także poprawić jakość produktów, zwiększyć efektywność produkcji i zbudować długoterminową przewagę konkurencyjną?
Kluczowe zasady zarządzania kosztami jakości w produkcji
Zarządzanie kosztami jakości wymaga zastosowania spójnej strategii obejmującej zarówno zapobieganie błędom, jak i ich eliminację w późniejszych etapach produkcji. Kluczowe zasady to:
- optymalizacja procesów kontrolnych i audytów,
- wprowadzenie nowoczesnych narzędzi i systemów automatyzacji,
- edukacja pracowników w zakresie jakości.
Jakie korzyści niesie optymalizacja kosztów jakości?
Optymalizacja kosztów jakości przynosi korzyści w postaci wyższej efektywności produkcji, mniejszych strat finansowych oraz poprawy jakości produktów. Przedsiębiorstwa, które skutecznie zarządzają kosztami jakości, zyskują przewagę konkurencyjną na rynku oraz zwiększają zadowolenie swoich klientów.
Masz pytania lub chcesz dowiedzieć się więcej? Skontaktuj się z nami i skorzystaj z bezpłatnej konsultacji, podczas której pomożemy zidentyfikować problemy i zaproponujemy konkretne rozwiązania dla Twojej firmy.