Marnotrawstwa
8 rodzajów marnotrawstwa
Poznanie rodzajów marnotrawstwa to pierwszy krok do ich eliminacji. Teoria o stratach to podstawy koncepcji Lean Management. Redukcja marnotrawstw sprzyja efektywnej organizacji procesów.
Co to jest marnotrawstwo?
W podejściu Lean wyróżnia się dwa rodzaje czynności: dodające wartość i niedodające wartości. Czynności, które nie dodają wartości to straty nazywane marnotrawstwem, z japońskiego MUDA.
Typy marnotrawstw
Wyróżniamy dwa typy marnotrawstw:
Typ I: Straty konieczne
Do strat koniecznych zaliczymy wszystkie czynności, które muszą być wykonane ze względu na proces, ale nie dodają do produktu żadnej wartości.
Przykłady: uruchomienie maszyny, przezbrojenie, transport wewnętrzny, transport do kooperacji, przygotowanie stanowiska, druk dokumentów, podpisy.
To są czynności, które często są akceptowane, a powinny być minimalizowane.
Typ II: Straty zbędne
Straty zbędne to zbiór czynności, które w ogóle nie powinny występować, jednak ich udział w procesach często jest bardzo duży.
Przykłady: przekładanie materiałów, nadmierny transport, poprawki, szukanie, czekanie na materiał.
Te czynności powinny być eliminowane w pierwszej kolejności. Aby umożliwić ich usunięcie, należy potrafić je dostrzec oraz znaleźć ich przyczynę źródłową. W tym celu konieczne jest mapowanie strumienia wartości (więcej tutaj: https://leanactionplan.pl/mapowanie/)
Proces w kontekście wartości składa się z różnych elementów
Każdy proces można opisać tymi składowymi:
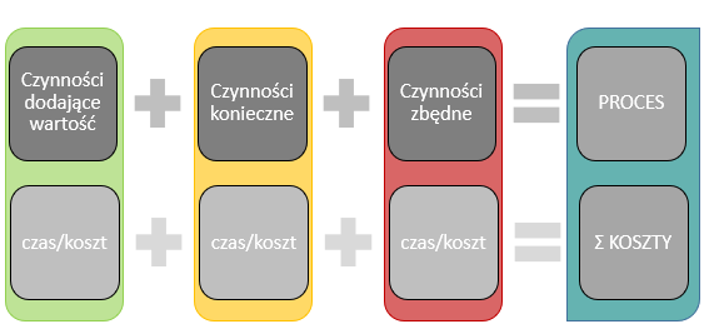
Podstawowe typy strat
W celu zoptymalizowania procesu należy go przeanalizować i zidentyfikować rodzaje marnotrawstw, które się w nim pojawiają. Taichii Ohno, twórca Systemu Produkcyjnego Toyoty, wyróżnił siedem typów strat:
Nadprodukcja (ang. waste of overproduction)
To jedna z najgorszych strat, gdyż pociąga za sobą kolejne. Wyprodukowanie więcej, niż zamówił klient (praca z niższym czasem taktu, niż takt klienta) wiąże się z dodatkowym zużyciem surowców, wykorzystaniem siły roboczej, transportu, magazynowania oraz zbędnych ruchów. Nadprodukcja często wizualizowana jest za pomocą góry lodowej – zazwyczaj na hali widać nadprodukcję, bo maszyny pracują pełną parą, widać również zapasy, które zalegają na hali i w magazynach, i widać trochę transportu – wszyscy gdzieś się przemieszczają. Ale w jakim celu? Poniżej dostrzec można ukryte problemy, których zazwyczaj nie widać na pierwszy rzut oka. Są to uszkodzenia zapasów, zamrożone zasoby, przestoje, defekty, zakłócenia, opóźnienia dostaw i inne.
Nadprodukcja wydaje się jedynym rozwiązaniem dla firm, które widzą potrzebę produkcji w partiach, aby minimalizować przenoszenie, mają zbyt duże obciążenia jednego ze stanowisk, w firmie brakuje informacji o rzeczywistych potrzebach dalszych procesów, wydajności maszyn są różne, a czas przezbrojenia bardzo długi.
Zapasy (ang. waste of inventory)
Jakie są główne powody zapasów? Brak informacji o zapotrzebowaniu narzuconym przez klienta, mała częstotliwość wysyłek oraz duże partie produkcyjne. Utrzymywanie zapasów w żaden sposób nie wpływa na dodawanie wartości, a dodatkowo generuje koszty magazynowania, ryzyko zniszczenia lub pogorszenia jakości oraz unieruchamia zasoby finansowe, ale również przyczynia się do braku elastyczności na zmiany popytu.
Transport (ang. waste of transport)
Transport może być traktowany jako strata konieczna – mimo że nie wpływa na wartość samego produktu, konieczne jest to, aby go dostarczyć do klienta. Transport, jako stratę zbędną, będziemy traktować przy przemieszczaniu na zbyt odległe od siebie stanowiska produkcyjne, zbędny załadunek i rozładunek. Każdy ruch produktu rodzi ryzyko uszkodzenia, a jeśli nie jest związany z dodawaniem wartości, jest stratą.
Chcesz lepiej planować logistykę i transport w swojej firmie?
Koniecznie sprawdź nasze szkolenie zamknięte Logistyka Lean!
Program warsztatów opiera się na przykładach z wewnątrz firmy i realizowany jest – w przeważającej części – na hali produkcyjnej, w biurze czy obszarze magazynowym. Jeśli nie można pozwolić sobie na takie rozwiązanie, przygotowujemy dedykowane symulacje pozwalające zapoznać się z tematyką w praktyce.
Kliknij i sprawdź szkolenie z Logistyki Lean!
Oczekiwanie (ang. waste of waiting)
Stratą będzie każda chwila, w której następuje przestój w produkcji, niezależnie czy przyczyną jest brak surowców, komponentów, niewłaściwa organizacja pracy, kontrola po wznowieniu produkcji, oczekiwanie na decyzje zarządzających czy brak pracownika na stanowisku. Na co oczekują pracownicy? Zazwyczaj na materiał – bo wózkowy jeszcze nie przyjechał, na dokumenty – są jeszcze w biurze, na decyzję – kiedy szef jest zajęty, na Utrzymanie Ruchu – gdy maszyna się zepsuła, na przezbrojenie – kiedy długo się przestawiamy, na półprodukty – bo poprzednie stanowisko nie wydala.
Aby zminimalizować ryzyko wystąpienia opóźnień, sprawdź aplikację TPM- Prewencja.
To rozwiązanie, które zostało stworzone do zminimalizowania opóźnień w zamówieniach, prowadzenia działań prewencyjnych i efektywnego utrzymania ruchu.
Zbędny ruch (ang. waste of motion)
Zbędną stratą będzie każdy ruch niezwiększający wartości produktu. Wśród popularnych zbędnych ruchów wyróżnić można trudny odstęp do części czy narzędzi, schylanie się, podnoszenie, sięganie.
Nadmierne przetwarzanie (ang. waste of overprocessing)
Ponawianie czynności jest marnotrawstwem bez względu na to, czy dotyczy zapobiegania spadkom jakości, czy ma związek z rodzajem stosowanego materiału. Ten punkt wiąże się również z nadmierną rozbudową procesu, czyli niezbilansowaniem go na etapie projektowania, zbyt dużymi rozmiarami maszyn lub źle zwymiarowanym stanowiskiem pracy, zbyt ciężkimi pudłami, ale także nieczytelnymi instrukcjami pracy.
Braki/defekty (ang. waste of defects)
To działania niezgodne z systemem TQM lub Poka-Yoke, kontynuowanie produkcji z defektami, brak reakcji na niezachowanie standardu, skomplikowane instrukcje stanowiskowe. To wszystko rodzi konieczność poprawiania usterek w produkcie, który nie został wykonany poprawnie za pierwszym razem i nie spełnia wymagań jakościowych.
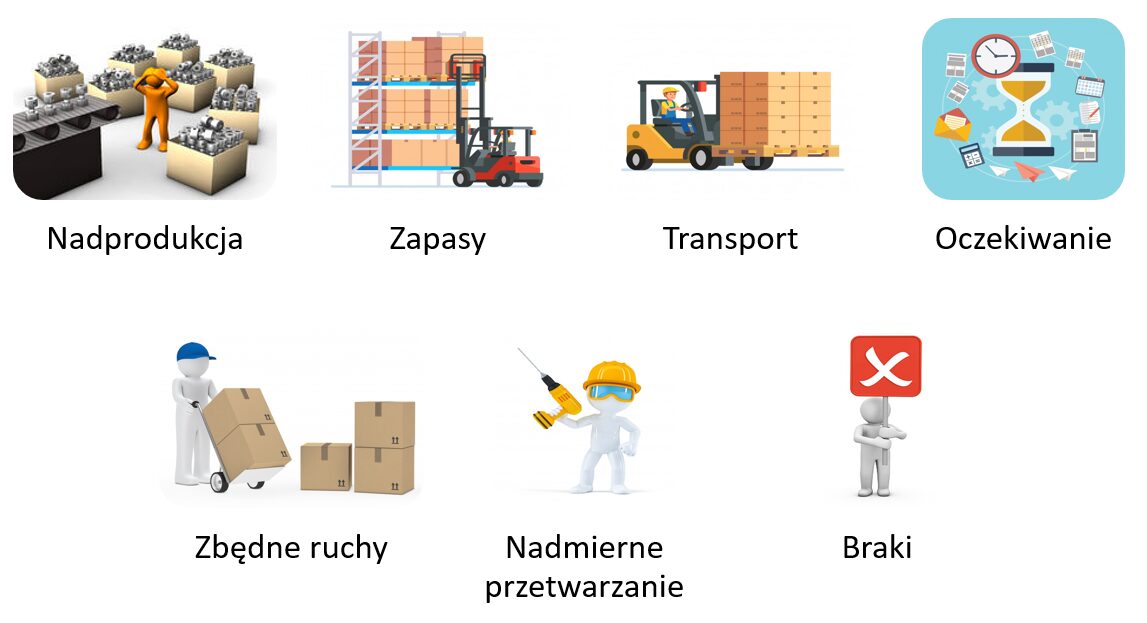
Szkolenie Online
Intro to Lean
Na czym polega Lean i jak go wdrażać?
Podstawowe narzędzia Lean
Identyfikacja marnotrawstwa
Korzyści stosowania Lean
Ósma muda
Wraz z rozwojem organizacji i znaczenia wiedzy oraz doświadczenia pracowników dodana została kolejna strata – Niewykorzystany potencjał ludzki.
Jest to strata polegająca na nieangażowaniu pracowników w rozwój procesów rozwiązywania problemów. To znacznie może zwolnić rozwój organizacji. Przez wysokie tempo pracy marnujemy kreatywność pracowników i ograniczamy ich rozwój.
Jak wyeliminować marnotrawstwo?
Na początku wystarczy przeprowadzenie mapowania strumienia wartości i określenie największych strat. Wynikiem mapowania jest przygotowanie planu działania wraz z priorytetami. Początkowe działania przynoszą bardzo często zaskakujące efekty. Dzięki temu możliwe jest zaangażowanie najwyższego kierownictwa i pracowników, którzy widzą efekty działań Lean.
Kolejne działania to już wejście na drogę Kaizen. Więcej na ten temat tutaj: https://kursylean.pl/product/kaizen-ciagle-doskonalenie/