Minimalizowanie marnotrawstwa w firmie produkcyjnej
Less waste czy zero waste to nie tylko trendy, które możesz wdrożyć w swoim życiu. Mogą mieć one również swoje odpowiedniki w branży produkcyjnej – mowa tu o minimalizacji marnotrawstwa materiałów. Dlaczego warto nad tym pomyśleć właśnie w kontekście procesów produkcji? Przede wszystkim, eliminacja marnotrawstwa to po prostu oszczędność. Im mnie materiałów i surowców marnujemy, tym mniejsze koszty, jakie firma ponosi. W tym artykule przedstawiamy strategie i metody zarządzania marnotrawstwem – tak, aby optymalizacja procesów produkcyjnych szła w parze z cięciem kosztów produkcji. A gdzie zaczniemy? Oczywiście od poznania, co na temat marnotrawstwa mówi podejście Lean Management! Sprawdź, jak możesz wdrożyć minimalizowanie marnotrawstwa w swojej firmie!
Lean Management w optymalizacji procesów i eliminacji marnotrawstwa
Zacznijmy od przypomnienia podstaw: Czym jest Lean Management? Jakie są cele Lean Management i co wspólnego ma z marnotrawstwem? Otóż, to podejście do zarządzania, które koncentruje się na eliminacji marnotrawstwa i maksymalizacji wartości dostarczanej klientowi. Jego głównym celem jest optymalizacja procesów produkcyjnych i biznesowych w taki sposób, aby każda aktywność, każda zasada i każde narzędzie przyczyniały się do tworzenia wartości dodanej, eliminując jednocześnie wszelkie zbędne elementy, które nie przynoszą korzyści klientowi. Lean Management, wywodzący się z japońskiego przemysłu motoryzacyjnego, szczególnie z praktyk systemu produkcyjnego Toyoty, stał się fundamentem dla nowoczesnych metod zarządzania w wielu branżach na całym świecie. W praktyce Lean Management to nieustanny system optymalizacji procesów, który skupia się na angażowaniu pracowników na wszystkich poziomach organizacji oraz wdrażaniu systematycznych zmian, które prowadzą do usprawnienia operacji, obniżenia kosztów – eliminacji marnotrawstwa. Przy tym warto zaznaczyć, że w Lean Thinking marnotrawstwo może przybierać różne formy, takie jak nadprodukcja, zbędny transport, nadmierne zapasy, błędy w procesach, przestoje czy niepotrzebne ruchy.
Identyfikacja i Eliminacja Marnotrawstwa (Muda)
Identyfikacja i eliminacja marnotrawstwa, znanego jako “muda” w zarządzaniu Lean, jest jednym z centralnych elementów tej filozofii zarządzania. Marnotrawstwo to – jak zostało wspomniane – wszelkie działania, procesy lub zasoby, które nie dodają wartości dla klienta, a jedynie zwiększają koszty i czas realizacji procesów. W Lean Management kluczowe jest zrozumienie, że każdy element procesu produkcyjnego lub operacyjnego powinien być tak zaprojektowany, aby dostarczać maksymalną wartość przy minimalnym wykorzystaniu zasobów. Proces identyfikacji marnotrawstwa zaczyna się od analizy poszczególnych etapów produkcji, aby wykryć te, które są nieefektywne lub niepotrzebne. Eliminacja muda polega na wdrożeniu zmian, które usuwają lub redukują te elementy, co pozwala na poprawę wydajności, skrócenie czasu realizacji i obniżenie kosztów. Często wymaga to zastosowania narzędzi Lean, takich jak mapowanie strumienia wartości (Value Stream Mapping), które pomagają wizualizować przepływ materiałów i informacji, identyfikując miejsca, gdzie dochodzi do marnotrawstwa.
Typy Marnotrawstwa w Lean Management
W Lean Management zidentyfikowano siedem podstawowych typów marnotrawstwa, które należy eliminować, aby osiągnąć maksymalną efektywność operacyjną. Pierwszym z nich jest nadprodukcja, która występuje wtedy, gdy produkowane są większe ilości, niż jest to potrzebne, co prowadzi do magazynowania zbyt dużej ilości zapasów (produktów). Kolejnym typem jest zbędny transport, czyli niepotrzebne przemieszczanie produktów lub materiałów w trakcie produkcji, co generuje dodatkowe koszty i ryzyko uszkodzeń. Trzecim rodzajem marnotrawstwa jest nadmiar zapasów, który wiąże się z utrzymywaniem zbyt dużej ilości surowców, półproduktów lub gotowych wyrobów, co zwiększa koszty magazynowania i ryzyko przeterminowania. Kolejne typy to zbędny ruch, który odnosi się do niepotrzebnych ruchów pracowników lub maszyn, oraz oczekiwanie, czyli przestoje w produkcji spowodowane brakiem materiałów, informacji lub awariami sprzętu. Szóstym typem marnotrawstwa jest nadmierna obróbka, gdzie procesy produkcyjne są bardziej skomplikowane lub czasochłonne niż to konieczne. Ostatnim typem jest wytwarzanie defektów, które prowadzą do konieczności poprawek lub wyrzucania wadliwych produktów. Zrozumienie i eliminacja tych siedmiu typów marnotrawstwa jest najważniejszym celem Lean Manufacturing.
Nadprodukcja i jej konsekwencje
Nadprodukcja, czyli produkowanie więcej niż jest to potrzebne lub zanim jest to potrzebne, jest jednym z najpoważniejszych typów marnotrawstwa według Lean Thinking. Nadprodukcja prowadzi do wielu negatywnych konsekwencji, które mogą znacząco wpłynąć na efektywność operacyjną i rentowność firmy. Przede wszystkim, nadprodukcja zwiększa koszty związane z magazynowaniem nadmiaru zapasów, które mogą ulegać przeterminowaniu, uszkodzeniu lub dezaktualizacji, szczególnie w branżach, gdzie technologia i trendy szybko się zmieniają. Dodatkowo, produkcja ponad zapotrzebowanie może wymagać dodatkowej przestrzeni magazynowej oraz zwiększać obciążenie finansowe firmy, związaną z zamrożonym kapitałem. Nadprodukcja często prowadzi również do marnotrawstwa w innych obszarach, takich jak nadmierne zużycie surowców, energii i zasobów ludzkich, które mogłyby zostać lepiej wykorzystane. W kontekście Lean Management, eliminacja nadprodukcji jest istotna, ponieważ umożliwia firmom bardziej precyzyjne dostosowanie produkcji do realnego popytu, co z kolei prowadzi do lepszej kontroli nad kosztami.
Zbędny ruch i oczekiwanie
Zbędny ruch oraz oczekiwanie to kolejne typy marnotrawstwa, które praktyka Lean Management stara się eliminować, aby zwiększyć efektywność operacyjną i produktywność. Zbędny ruch to wszelkie niepotrzebne działania fizyczne wykonywane przez pracowników lub maszyny, które nie przyczyniają się bezpośrednio do dodawania wartości do produktu. Przykłady zbędnego ruchu mogą obejmować pracowników przemieszczających się po hali produkcyjnej w celu uzyskania narzędzi lub materiałów, które mogłyby być lepiej zorganizowane, lub maszyny, które wymagają nadmiernych regulacji lub ustawień. Eliminacja zbędnego ruchu poprzez lepsze planowanie layoutu hali, automatyzację lub ergonomiczne ustawienie stanowisk pracy może prowadzić do znacznego skrócenia czasu realizacji oraz zmniejszenia zmęczenia pracowników. Twój layout potrzebuje optymalizacji? Sprawdź warsztaty Layout, które w formie praktycznego szkolenia pomogą stworzyć layout dla Twojej firmy.
Oczekiwanie to czas, w którym zasoby są niewykorzystywane, np. kiedy pracownicy czekają na dostarczenie materiałów, instrukcje, narzędzia lub na zakończenie procesu na poprzednim stanowisku. Oczekiwanie często wynika z nieodpowiedniego harmonogramowania, braku synchronizacji między etapami produkcji, problemów z dostawami lub awarii sprzętu. W Lean Management, eliminacja czasu oczekiwania jest kluczowa, ponieważ przestoje mogą prowadzić do opóźnień w produkcji, marnowania zasobów i obniżenia produktywności. Wdrożenie narzędzi Lean, takich jak just-in-time (JIT) oraz standaryzacja procesów, pomaga minimalizować czas oczekiwania i zapewnia płynność operacyjną, co z kolei poprawia zdolność firmy do terminowego realizowania zamówień i zwiększa jej konkurencyjność na rynku.
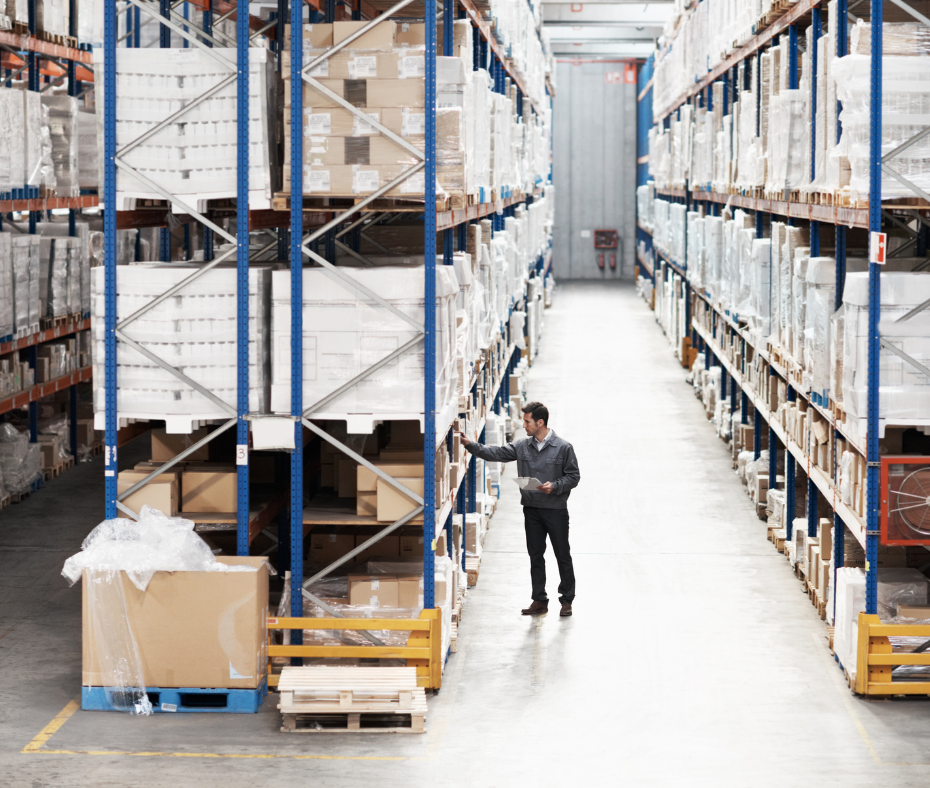
Techniki i narzędzia Lean Management w minimalizacji marnotrawstwa
W kontekście minimalizacji marnotrawstwa materiałów, Lean Management wykorzystuje zestaw technik i narzędzi, które pomagają w optymalizacji procesów produkcyjnych, redukcji nadmiaru surowców oraz maksymalizacji efektywności operacyjnej. Narzędzia takie jak Kaizen, Just-In-Time, metoda 5S oraz Poka-yoke odgrywają kluczową rolę w minimalizacji strat materiałowych, zmniejszając nie tylko ilość odpadów, ale także koszty związane z nadprodukcją, nadmiernym magazynowaniem oraz błędami produkcyjnymi. Poprzez wdrożenie tych narzędzi, organizacje mogą znacząco poprawić swoje procesy, zwiększając jednocześnie jakość procesów, wydajność oraz zrównoważony rozwój.
Kaizen: Ciągłe usprawnianie procesów produkcyjnych
Kaizen, czyli ciągłe doskonalenie (również ciągłe doskonalenie procesów produkcyjnych), jest jedną z podstawowych technik Lean Management, która koncentruje się na systematycznym i ciągłym ulepszaniu procesów produkcyjnych i operacyjnych. W kontekście minimalizacji marnotrawstwa materiałów, Kaizen polega na regularnym identyfikowaniu obszarów, gdzie dochodzi do strat surowców, takich jak nadmierne zużycie materiałów, odpady produkcyjne czy nieefektywne wykorzystanie surowców. Pracownicy na wszystkich poziomach organizacji są zachęcani do zgłaszania propozycji ulepszeń, co prowadzi do drobnych, ale systematycznych zmian, które w dłuższym okresie znacząco redukują marnotrawstwo. Przykłady zastosowania Kaizen mogą obejmować optymalizację procesów cięcia materiałów, lepsze planowanie produkcji, które eliminuje potrzebę nadprodukcji, oraz doskonalenie metod recyklingu i ponownego wykorzystania surowców. Dzięki Kaizen firmy mogą postawić na ciągłe doskonalenie procesów produkcyjnych, minimalizując straty materiałowe i zwiększając swoją efektywność operacyjną.
Just-In-Time: Optymalizacja Zapasów
Just-In-Time (JIT) to technika Lean Management, która polega na dostarczaniu surowców i komponentów dokładnie wtedy, gdy są one potrzebne w procesie produkcyjnym, co pozwala na minimalizację zapasów i eliminację marnotrawstwa materiałów. W ramach JIT, produkcja jest ściśle zsynchronizowana z rzeczywistym popytem, co zapobiega gromadzeniu nadmiernych ilości surowców, które mogłyby ulec przeterminowaniu lub uszkodzeniu. W kontekście minimalizacji marnotrawstwa, JIT zmniejsza ryzyko nadprodukcji, która często prowadzi do gromadzenia się zbędnych zapasów, generujących dodatkowe koszty magazynowania oraz straty surowców. Dzięki wdrożeniu JIT, firmy mogą bardziej efektywnie zarządzać swoimi zasobami, ograniczając straty materiałowe i zwiększając rentowność. Przykładem może być firma produkująca komponenty elektroniczne, która dzięki JIT zmniejsza ilość magazynowanych surowców do niezbędnego minimum, co pozwala na redukcję odpadów wynikających z przestarzałych lub uszkodzonych materiałów. Firma to wprowadziła proces optymalizacji zapasów dzięki metodzie JIT.
Metoda 5S: Organizacja Miejsca Pracy
Metoda 5S jest narzędziem Lean Management, które koncentruje się na organizacji i standaryzacji miejsca pracy, co jest kluczowe dla minimalizacji marnotrawstwa materiałów. 5S obejmuje pięć kroków: Seiri (Sortowanie), Seiton (Systematyzacja), Seiso (Sprzątanie), Seiketsu (Standaryzacja), i Shitsuke (Samodyscyplina), z których każdy ma na celu poprawę organizacji pracy, redukcję marnotrawstwa oraz zapewnienie, że wszystkie zasoby są efektywnie wykorzystywane. Jednak 5S to nie tylko zarządzanie procesami produkcyjnymi i miejscem pracy. W kontekście minimalizacji strat materiałowych, metoda 5S pomaga w eliminacji zbędnych materiałów, które zajmują miejsce i mogą ulegać zniszczeniu lub przeterminowaniu. Dzięki systematyzacji, pracownicy mają łatwiejszy dostęp do potrzebnych surowców, co redukuje ryzyko marnowania materiałów przez błędne wykorzystanie lub niewłaściwe przechowywanie. Regularne sprzątanie i utrzymanie porządku (Seiso) zapewnia, że materiały są przechowywane w odpowiednich warunkach, co minimalizuje ryzyko ich uszkodzenia. Wprowadzenie metody 5S w organizacji prowadzi do bardziej efektywnego wykorzystania przestrzeni, lepszej organizacji pracy i redukcji strat materiałowych. Wprowadziłeś 5S do swojej firmy, ale nie wiesz czy jesteś w stanie długotrwale utrzymać te zasady? Sprawdź aplikację Audyty 5S, która w tym pomoże!
Poka-yoke: Zapobieganie Błędom
Poka-yoke to technika Lean Management, która ma na celu zapobieganie błędom w procesie produkcyjnym poprzez wprowadzenie prostych, ale skutecznych mechanizmów, które eliminują możliwość popełnienia błędu lub natychmiast go wykrywają. W kontekście minimalizacji marnotrawstwa materiałów, Poka-yoke odgrywa kluczową rolę w zapobieganiu błędom, które mogą prowadzić do marnowania surowców. Przykłady Poka-yoke mogą obejmować automatyczne wyłączniki, które zatrzymują maszynę, jeśli wykryta zostanie anomalia, czujniki wykrywające brak komponentu lub bariery fizyczne, które uniemożliwiają niewłaściwe złożenie części. Dzięki zastosowaniu Poka-yoke, firmy mogą znacząco zmniejszyć ilość odpadów wynikających z błędów produkcyjnych, co z kolei prowadzi do oszczędności materiałów i poprawy jakości produktów. Poka-yoke nie tylko redukuje straty surowców, ale także przyczynia się do zwiększenia efektywności operacyjnej, ponieważ minimalizuje konieczność poprawek i skraca czas cyklu produkcyjnego. Wprowadzenie tej techniki w firmie buduje również kulturę jakości, w której prewencja błędów jest integralną częścią codziennych operacji.
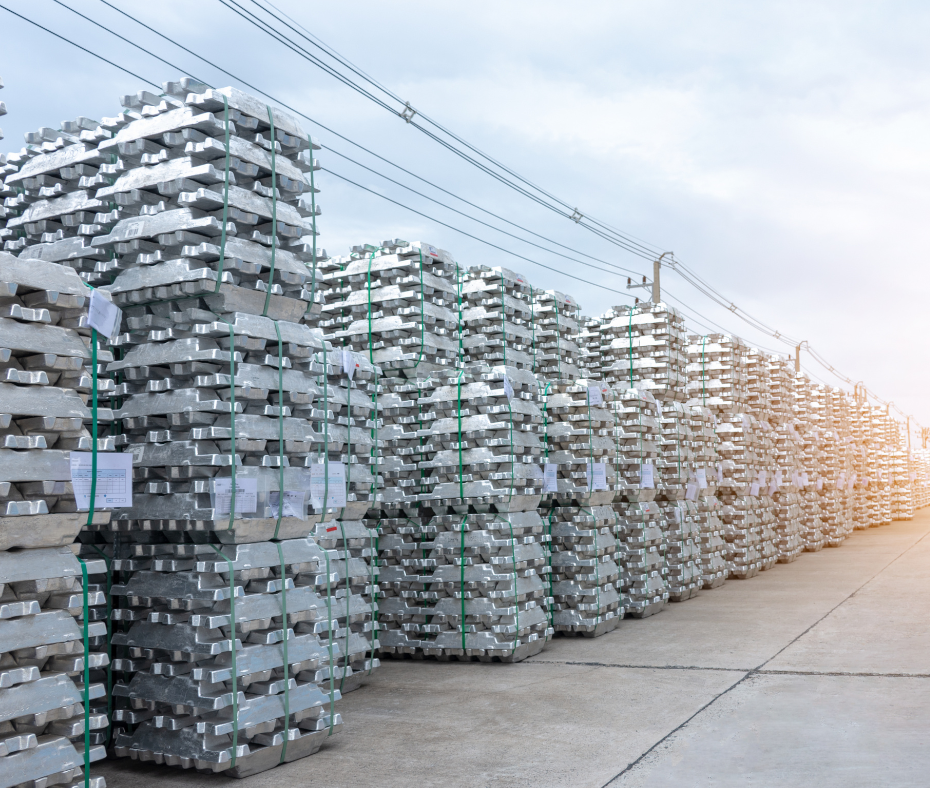
Lean Six Sigma: Integracja z Lean Management
Lean Six Sigma to zintegrowana metodologia, która łączy w sobie zasady Lean Management i Six Sigma, tworząc potężne narzędzie do optymalizacji procesów i eliminacji marnotrawstwa w organizacji. Lean koncentruje się na identyfikacji i eliminacji marnotrawstwa (muda) oraz na poprawie efektywności procesów poprzez ciągłe doskonalenie. Six Sigma natomiast skupia się na redukcji zmienności w procesach i zapewnieniu najwyższej jakości poprzez zastosowanie metod statystycznych. Integracja tych dwóch podejść pozwala firmom na osiągnięcie wyjątkowej wydajności operacyjnej, poprzez nie tylko usuwanie zbędnych elementów procesów, ale także eliminowanie defektów i błędów, które mogą prowadzić do strat. W praktyce, Lean Six Sigma wykorzystuje narzędzia i techniki obu metodologii, takie jak mapowanie strumienia wartości (Value Stream Mapping), analiza przyczyn źródłowych (Root Cause Analysis), oraz cykl DMAIC (Define, Measure, Analyze, Improve, Control), aby systematycznie doskonalić procesy produkcyjne i usługowe. Dzięki integracji Lean i Six Sigma, organizacje mogą skuteczniej zarządzać swoimi zasobami, zwiększać zadowolenie klientów i osiągać trwałe przewagi konkurencyjne.
Zasady i korzyści Lean Six Sigma
Lean Six Sigma opiera się na kilku zasadach, które stanowią fundament tego zintegrowanego podejścia do zarządzania jakością i efektywnością operacyjną. Pierwszą zasadą jest koncentracja na kliencie, która wymaga, aby wszystkie działania w organizacji były ukierunkowane na dostarczanie maksymalnej wartości dla klienta końcowego. Kolejną zasadą jest eliminacja marnotrawstwa, która polega na identyfikacji i usuwaniu wszystkich procesów i działań, które nie dodają wartości z perspektywy klienta, takich jak nadprodukcja, zbędny transport czy oczekiwanie. Lean Six Sigma również kładzie duży nacisk na zarządzanie oparte na danych, co oznacza, że decyzje dotyczące doskonalenia procesów są podejmowane na podstawie rzetelnych analiz statystycznych, a nie intuicji. Kolejną zasadą jest ciągłe doskonalenie, które promuje systematyczne wprowadzanie drobnych ulepszeń, które w dłuższym okresie prowadzą do znaczącej poprawy efektywności.
Korzyści z wdrożenia Lean Six Sigma są znaczne i obejmują zarówno poprawę jakości, jak i zwiększenie efektywności operacyjnej. Przede wszystkim, Lean Six Sigma pozwala firmom na znaczną redukcję marnotrawstwa, co prowadzi do obniżenia kosztów produkcji i poprawy rentowności. Dodatkowo, dzięki redukcji zmienności w procesach, firmy mogą osiągnąć wyższą jakość produktów i usług, co z kolei przekłada się na większe zadowolenie klientów i lojalność. Lean Six Sigma również przyczynia się do skrócenia czasu cyklu produkcyjnego, co pozwala firmom na szybsze reagowanie na zmiany rynkowe i lepsze wykorzystanie zasobów. Co więcej, wdrożenie Lean Six Sigma sprzyja budowaniu kultury ciągłego doskonalenia, w której pracownicy na wszystkich poziomach organizacji są zaangażowani w procesy optymalizacji, co prowadzi do trwałego wzrostu efektywności i innowacyjności organizacji.
Szkolenie Online
Intro to Lean
Stosowanie zarządzania wizualnego
Problemy jako szansa do optymalizacji
Identyfikacja marnotrawstwa
Wdrażanie działań w ramach Kaizen
Value Stream Mapping: analiza przepływu materiałów
Value Stream Mapping (VSM), czyli mapowanie strumienia wartości, to kolejne istotne narzędzie Lean Management, które służy do analizy i optymalizacji przepływu materiałów oraz informacji w procesie produkcyjnym. VSM umożliwia wizualizację wszystkich kroków niezbędnych do dostarczenia produktu lub usługi, od momentu pozyskania surowców aż po dostarczenie gotowego wyrobu klientowi. Celem VSM jest identyfikacja czynności, które dodają wartość, oraz eliminacja marnotrawstwa (muda), które nie przynoszą wartości dodanej z perspektywy klienta. Analizując przepływ materiałów za pomocą VSM, firmy mogą zidentyfikować wąskie gardła, zbędne zapasy, nadprodukcję oraz inne nieefektywności, które spowalniają proces i generują dodatkowe koszty. Dzięki VSM firmy mogą wprowadzić lepsze zarządzanie zapasami i optymalizację procesów produkcyjnych. Na przykład, w procesie produkcyjnym mogą występować niepotrzebne przestoje między operacjami, wynikające z braku synchronizacji działań lub nadmiernych odległości między stanowiskami pracy. Dzięki VSM organizacje mogą stworzyć bardziej płynny i efektywny przepływ materiałów, co usprawnia zarządzanie przepływem pracy, prowadzi do obniżenia kosztów i poprawy jakości produktów.
Wykorzystanie potencjału pracowników w usprawnianiu procesów produkcyjnych
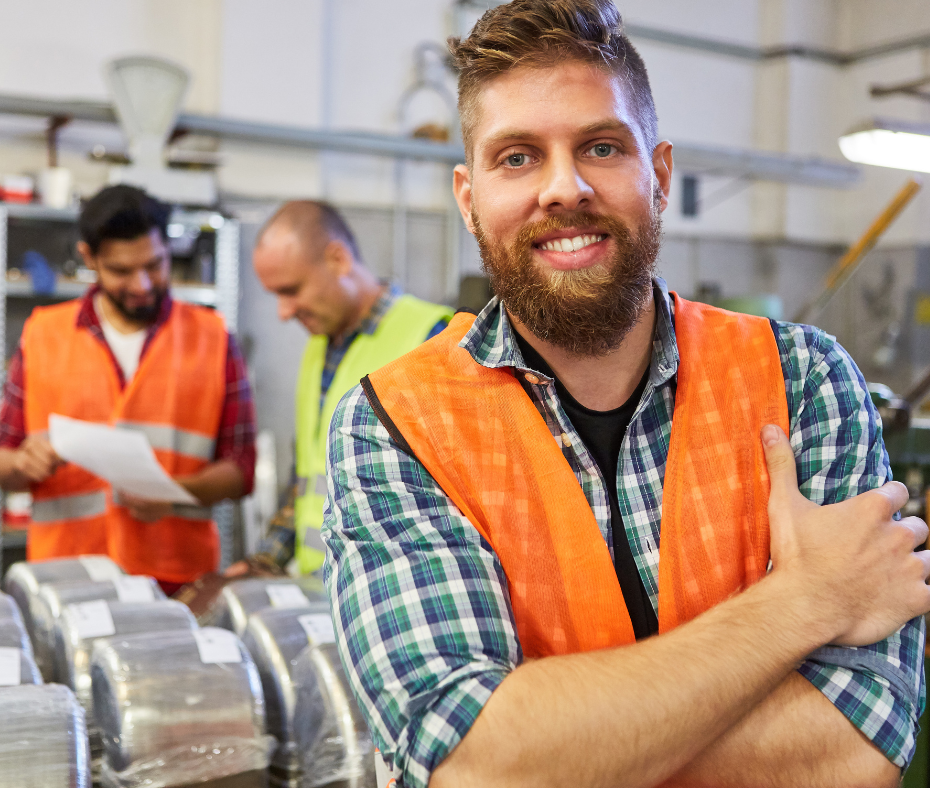
Wykorzystanie potencjału pracowników jest jednym z fundamentów koncepcji Lean Management, który podkreśla, że sukces organizacji w dużej mierze zależy od zaangażowania i kompetencji jej zespołu. Lean Thinking promuje podejście, w którym każdy pracownik, niezależnie od stanowiska, jest postrzegany jako cenne źródło wiedzy i innowacji. W praktyce oznacza to, że firmy powinny aktywnie rozwijać umiejętności swoich pracowników, tworzyć środowisko sprzyjające współpracy oraz zachęcać do dzielenia się pomysłami na poprawę procesów. Wykorzystanie potencjału pracowników obejmuje także upoważnianie pracowników do podejmowania decyzji i działania na rzecz ciągłego doskonalenia. Na przykład, operatorzy maszyn mogą być zachęcani do identyfikowania marnotrawstwa w swoich codziennych działaniach oraz do wdrażania małych, ale efektywnych zmian, które poprawiają wydajność pracy i minimalizują straty materiałowe. Efektywne wykorzystanie potencjału pracowników prowadzi do większej innowacyjności, wyższej jakości pracy oraz lepszego dostosowania organizacji do zmieniających się warunków rynkowych.
Angażowanie pracowników w usprawnienie procesów
Angażowanie pracowników w ciągłe usprawnianie procesów produkcyjnych to ważny element filozofii Lean Thinking, który umożliwia organizacjom nieustanne ulepszanie swoich procesów i eliminację marnotrawstwa. Pracownicy, będący najbliżej rzeczywistych operacji, często najlepiej rozumieją, gdzie występują nieefektywności i jak można je usunąć. Dlatego Lean Management zachęca do tworzenia kultury, w której każdy pracownik czuje się odpowiedzialny za jakość i efektywność swojej pracy oraz jest aktywnie zaangażowany w procesy doskonalenia. Jednym z narzędzi, które wspiera to zaangażowanie, jest Kaizen, gdzie regularne spotkania zespołów pozwalają na identyfikowanie problemów i proponowanie rozwiązań na poziomie operacyjnym. Przykładem może być zespół pracowników produkcyjnych, który regularnie spotyka się, aby omawiać sposoby redukcji odpadów materiałowych, optymalizacji pracy maszyn lub poprawy bezpieczeństwa na stanowisku pracy. Dzięki takiemu zaangażowaniu pracowników, firmy mogą nie tylko usprawniać swoje operacje, ale także zwiększać motywację i satysfakcję pracowników, co przekłada się na lepsze wyniki biznesowe i większą konkurencyjność na rynku.
Podsumowanie
Podstawowe narzędzia Lean, takie jak Value Stream Mapping, Kaizen, Just-In-Time, metoda 5S oraz Poka-yoke, stanowią fundament nowoczesnego podejścia do zarządzania procesami produkcyjnymi i operacyjnymi. Integracja tych technik umożliwia organizacjom skuteczne eliminowanie marnotrawstwa, poprawę efektywności oraz zwiększenie jakości produktów. W szczególności, Value Stream Mapping pozwala na dokładną analizę przepływu materiałów i identyfikację obszarów wymagających optymalizacji, podczas gdy Kaizen i Poka-yoke angażują pracowników w ciągłe doskonalenie i zapobieganie błędom.
Wnioski są jednoznaczne: aby organizacja mogła skutecznie konkurować na dynamicznym rynku, musi nieustannie dążyć do optymalizacji swoich procesów poprzez eliminację marnotrawstwa, wykorzystanie nowoczesnych narzędzi Lean oraz angażowanie pracowników na wszystkich poziomach. Tylko wtedy możliwe jest osiągnięcie trwałych wyników, które zapewnią długoterminowy sukces i przewagę konkurencyjną.
Pobierz bazę 100 wskaźników produkcyjnych
za darmo!
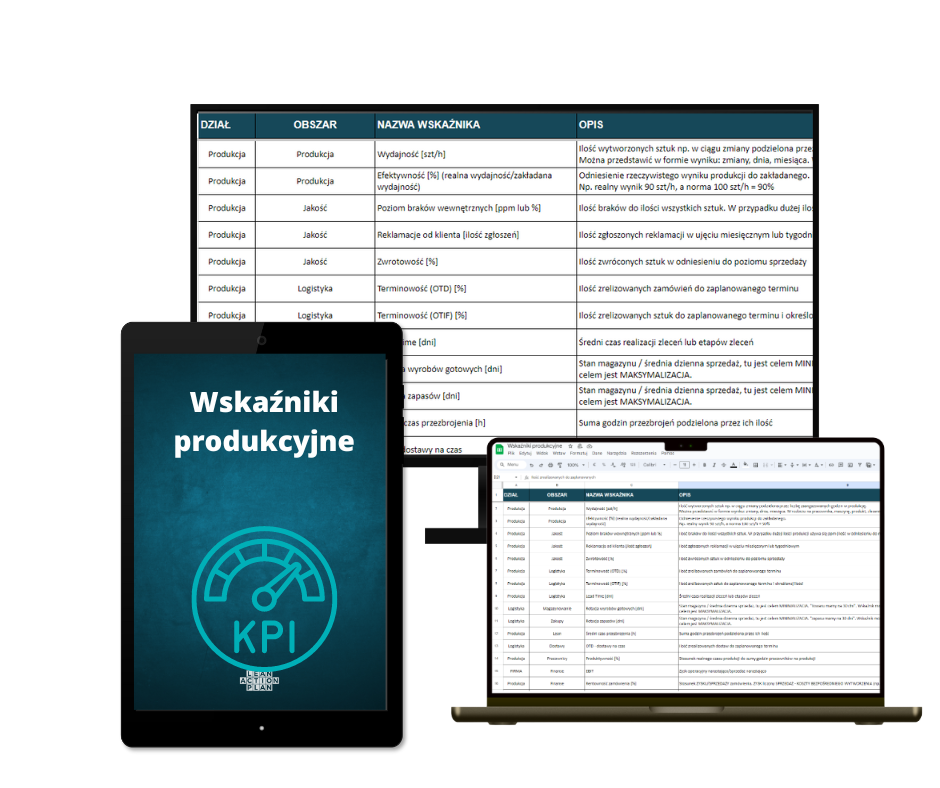