Jak zarządzać zapasami, aby uniknąć niedoborów surowców?
Produkcja idzie jak z płatka, popyt wciąż rośnie, wydajność na wysokim poziomie, ale… Dowiadujesz się nagle, że skończył się jeden z materiałów, potrzebnych do dalszego działania. Jakie są konsekwencje braku zapasów w magazynie? Panika, jak szybko zamówić ten surowiec, przestój w produkcji i opóźnienia, straty finansowe – koszty braku zapasów są wysokie. A to niestety tylko wynik niedostatecznych zapasów surowców. Co więcej, taka sytuacja jest do uniknięcia dzięki optymalizacji zapasów i dostosowaniu poziomu zapasów do tempa produkcji. O co w tym chodzi i jak zarządzać zapasami? Dziś rozkładamy na czynniki pierwsze techniki zarządzania zapasami, które pozwolą zapomnieć o brakach na magazynie!
Spis treści:
- Kluczowe strategie zarządzania zapasami surowców w firmie produkcyjnej
- Narzędzia wspierające zarządzanie zapasami materiałów
- Zapasy bezpieczeństwa – jak i kiedy je stosować?
- Jak zarządzać zapasami: prognozowanie popytu i dostaw
- Praktyczne rozwiązania na wyzwania związane z zarządzaniem zapasami
- Podsumowanie
- Odbierz za darmo: BAZA WSKAŹNIKÓW PRODUKCYJNYCH
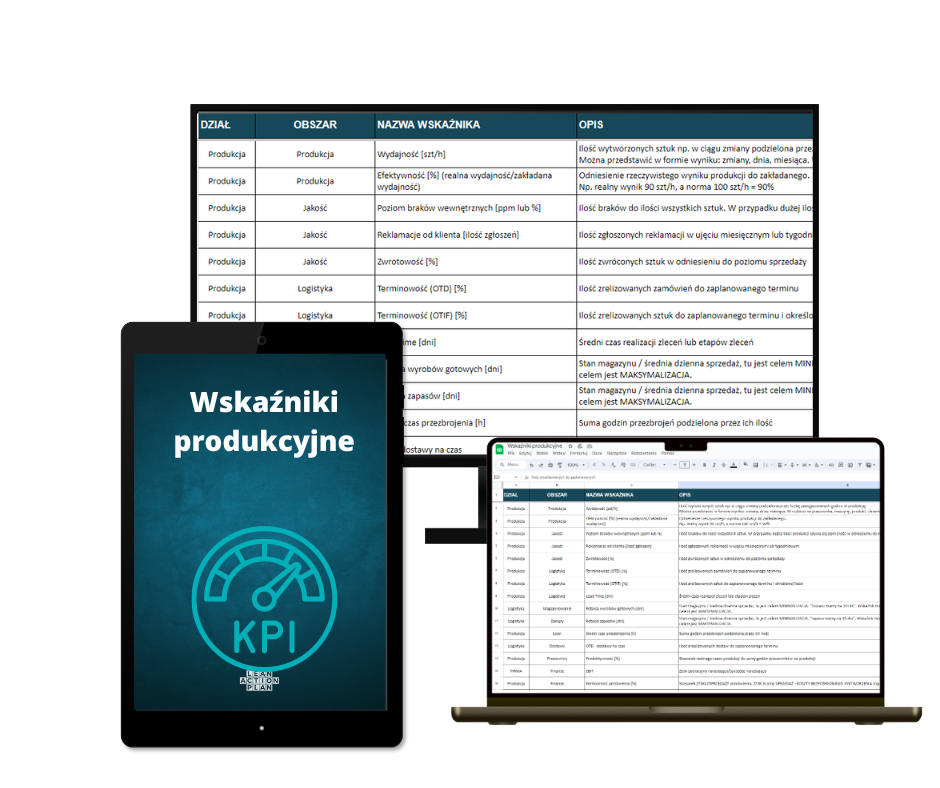
Kluczowe strategie zarządzania zapasami surowców w firmie produkcyjnej
Jakie strategie zarządzania zapasami w przesiębiorstwie są najlepsze? Zacznijmy od tego, że zarządzanie zapasami surowców jest jednym z najważniejszych elementów, wpływających na efektywność produkcji, koszty operacyjne i zdolność do elastycznego reagowania na zmieniający się popyt rynkowy. Właściwe strategie i techniki zarządzania zapasami pozwalają firmom na utrzymanie równowagi pomiędzy dostępnością surowców a minimalizacją kosztów związanych z ich przechowywaniem i zamrażaniem kapitału. Kluczowe strategie, takie jak Just-In-Time (JIT), analiza ABC oraz model ekonomicznej wielkości zamówienia (EOQ), oferują różne podejścia do optymalizacji zarządzania zapasami. Każda z tych metod ma swoje unikalne zalety i jest stosowana w zależności od specyfiki firmy, rodzaju produkcji oraz charakterystyki surowców. Skuteczne zarządzanie zapasami nie tylko zapobiega niedoborom, ale także pozwala na bardziej efektywne wykorzystanie zasobów.
Just-In-Time (JIT) – minimalizacja zapasów a unikanie niedoborów
Metoda Just-In-Time (JIT) to strategia zarządzania zapasami, która koncentruje się na minimalizacji zapasów magazynowych poprzez synchronizację dostaw surowców z faktycznym zapotrzebowaniem produkcyjnym. W systemie JIT surowce są dostarczane dokładnie wtedy, gdy są potrzebne do produkcji, co pozwala na znaczne zmniejszenie kosztów magazynowania oraz minimalizację ryzyka przeterminowania lub uszkodzenia surowców. Dużą zaletą JIT jest redukcja marnotrawstwa i zwiększenie efektywności operacyjnej, co jest szczególnie istotne w branżach, gdzie surowce mają krótki okres przydatności lub są kosztowne w przechowywaniu. Jednakże, skuteczne wdrożenie JIT wymaga ścisłej współpracy z dostawcami oraz precyzyjnego planowania, aby uniknąć niedoborów. Nawet krótkie opóźnienia w dostawach mogą mieć poważne konsekwencje, dlatego firmy stosujące JIT muszą dysponować niezawodnymi systemami logistycznymi i elastycznymi łańcuchami dostaw, które umożliwiają szybkie reagowanie na zmieniające się warunki. Metoda JIT, choć wymagająca w czasie wdrożenia, pozwala firmom na osiągnięcie oszczędności i poprawę konkurencyjności, poprzez optymalizację zarządzania zapasami surowców.
Analiza ABC – priorytetyzacja surowców kluczowych
Analiza ABC to technika zarządzania zapasami, która polega na klasyfikacji surowców na trzy kategorie (A, B i C) w oparciu o ich znaczenie dla firmy. Surowce klasy A to te, które stanowią największą wartość ekonomiczną dla firmy, mimo że ich ilość może być stosunkowo niewielka. Surowce klasy B mają umiarkowaną wartość, a surowce klasy C są liczne, ale generują najmniejszy przychód lub zysk. Analiza ABC umożliwia firmom skoncentrowanie zasobów i uwagi na zarządzaniu surowcami, które mają największy wpływ na ich działalność. Dzięki temu firma może optymalizować zapasy, redukując nadmierne magazynowanie zapasów klasy C, a jednocześnie zapewniając, że surowce klasy A są zawsze dostępne w odpowiednich ilościach. Metoda ta pozwala na lepsze planowanie zakupów, minimalizację ryzyka związanego z niedoborami krytycznych surowców oraz bardziej efektywne zarządzanie budżetem przeznaczonym na zapasy. W praktyce, analiza ABC może być zintegrowana z innymi narzędziami zarządzania zapasami, takimi jak systemy ERP, co dodatkowo zwiększa jej efektywność i ułatwia podejmowanie strategicznych decyzji dotyczących zarządzania surowcami.
Model ekonomicznej wielkości zamówienia (EOQ) – optymalizacja kosztów zamówień
Model ekonomicznej wielkości zamówienia (EOQ) jest narzędziem, które pomaga firmom określić optymalną wielkość zamówienia, minimalizującą całkowite koszty związane z zamawianiem i przechowywaniem surowców. EOQ uwzględnia dwa główne typy kosztów: koszty zamówienia, które rosną wraz ze zwiększaniem częstotliwości zamawiania mniejszych partii, oraz koszty przechowywania, które rosną w miarę zwiększania się wielkości zamówionych zapasów. Celem EOQ jest znalezienie punktu równowagi między tymi kosztami, co pozwala na optymalizację zarządzania zapasami i utrzymanie minimalnego poziomu zamrożonego kapitału. Model EOQ jest szczególnie użyteczny w sytuacjach, gdzie popyt na surowce jest stabilny i przewidywalny, a koszty związane z zamówieniami i magazynowaniem zapasów są dobrze znane. Przykładowo, w firmach produkcyjnych, które mają regularne cykle produkcyjne i stabilne zapotrzebowanie na surowce, EOQ umożliwia precyzyjne planowanie dostaw, co z kolei pozwala na utrzymanie ciągłości produkcji bez nadmiernych kosztów związanych z przechowywaniem. Zastosowanie modelu EOQ pozwala firmom na bardziej efektywne zarządzanie zapasami surowców, co przekłada się na zwiększenie rentowności i lepsze wykorzystanie zasobów finansowych.
Narzędzia wspierające zarządzanie zapasami materiałów
Skuteczne zarządzanie zapasami materiałów wymaga zaawansowanych narzędzi, które wspierają procesy planowania, monitorowania i optymalizacji. Dzięki takim narzędziom firmy mogą integrować różne aspekty zarządzania zapasami, takie jak prognozowanie popytu, kontrola stanów magazynowych, planowanie zamówień oraz analiza wydajności, co prowadzi do bardziej precyzyjnego i efektywnego zarządzania materiałami. Wśród najważniejszych narzędzi wspierających optymalizację procesu zarządzanie zapasami wyróżniają się systemy ERP (Enterprise Resource Planning) i WMS (Warehouse Management System), a także nowoczesne technologie automatyzacji i monitorowania zapasów w czasie rzeczywistym.
Systemy ERP i WMS – jak technologia wspiera zarządzanie zapasami?
Systemy ERP i WMS odgrywają rolę w zarządzaniu zapasami materiałów, integrując różnorodne procesy operacyjne i logistyczne w jednym spójnym systemie. ERP to kompleksowe oprogramowanie, które umożliwia firmom zarządzanie wszystkimi aspektami działalności, w tym finansami, łańcuchem dostaw, produkcją, sprzedażą oraz zarządzaniem zapasami. Dzięki systemom klasy ERP firmy mogą monitorować poziomy zapasów w czasie rzeczywistym, planować zamówienia na podstawie prognozowanego popytu, a także optymalizować procesy produkcyjne, minimalizując koszty związane z przechowywaniem surowców. Jeśli jednak ERP to rozwiązanie, które jest zbyt obszerne lub kosztowne dla Twojej firmy, alternatywą jest aplikacja ZaPro, czyli system do zarządzania produkcją. Możemy go ,,uszyć na miarę”, czyli dodać funkcjonalności dopasowane do Twojej firmy, przykładowo moduł WMS.
WMS to natomiast specjalistyczne oprogramowanie, które koncentruje się na zarządzaniu operacjami magazynowymi, takimi jak przyjmowanie towarów, ich składowanie, kompletacja zamówień oraz wysyłka. WMS umożliwia automatyzację wielu procesów magazynowych, co przekłada się na większą efektywność, dokładność i szybkość realizacji zamówień. Integracja systemów ERP i WMS pozwala firmom na pełną kontrolę poziomu zapasów, od momentu ich zakupu, przez magazynowanie zapasów, aż po wykorzystanie w produkcji.
Automatyzacja i monitorowanie zapasów w czasie rzeczywistym
Automatyzacja i monitorowanie zapasów w czasie rzeczywistym to ważne elementy nowoczesnego, skutecznego zarządzania zapasami, które pozwalają firmom na szybkie i precyzyjne reagowanie na zmieniające się warunki rynkowe oraz na minimalizację ryzyka związanego z niedoborami lub nadmiernymi zapasami. Wprowadzenie technologii takich jak IoT (Internet of Things), RFID (Radio-Frequency Identification) oraz zaawansowane systemy sensorowe umożliwia bieżące śledzenie poziomów zapasów, lokalizacji materiałów w magazynie oraz statusu zamówień. Dzięki automatyzacji procesów firmy mogą zminimalizować ryzyko błędów ludzkich, zwiększyć dokładność danych oraz skrócić czas potrzebny na realizację zamówień. Monitorowanie stanu zapasów w czasie rzeczywistym pozwala również na optymalizację procesów zamawiania, poprzez automatyczne generowanie zamówień uzupełniających, gdy poziom zapasów osiąga określony próg. Ponadto, dane zbierane w czasie rzeczywistym mogą być analizowane w celu identyfikacji trendów, prognozowania przyszłych potrzeb oraz optymalizacji strategii zarządzania zapasami. Automatyzacja i monitorowanie zapasów w czasie rzeczywistym przekształcają tradycyjne zarządzanie zapasami w dynamiczny, precyzyjnie kontrolowany proces, który znacząco zwiększa efektywność operacyjną oraz konkurencyjność firm produkcyjnych na rynku.
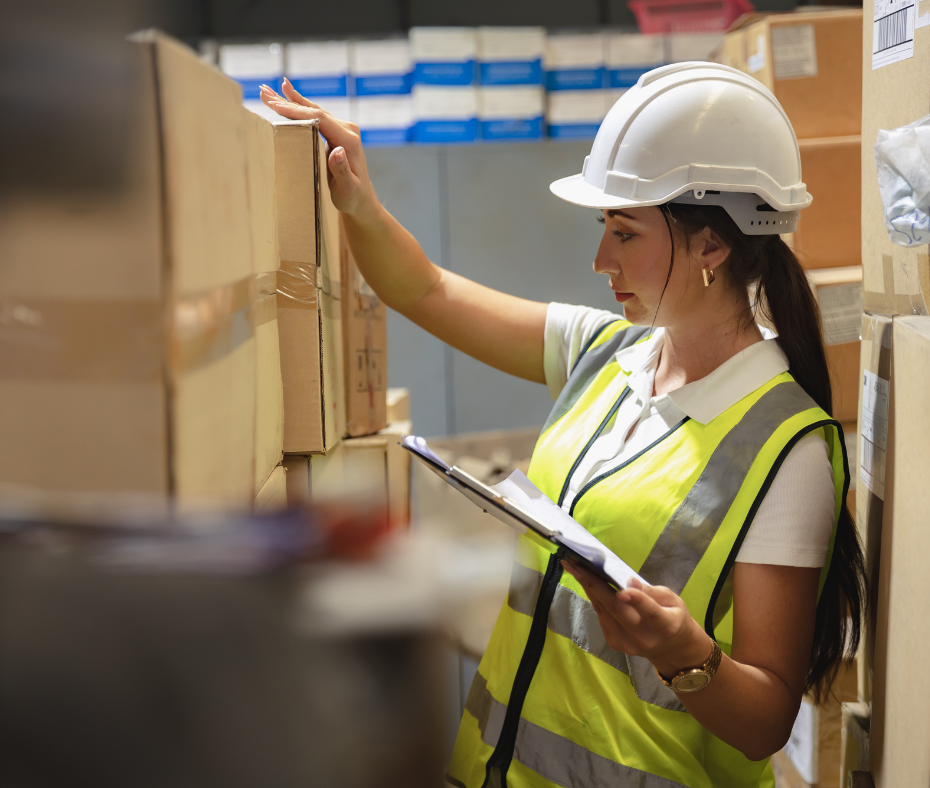
Zapasy bezpieczeństwa – jak i kiedy je stosować?
Zapasy bezpieczeństwa (inaczej zwany: zapas rezerwowy) to istotny element strategii zarządzania zapasami, mający na celu ochronę firm przed nieprzewidywalnymi zdarzeniami, które mogą zakłócić ciągłość produkcji. Stosowanie zapasów bezpieczeństwa polega na utrzymywaniu dodatkowych, rezerwowych ilości surowców lub produktów, które mogą być wykorzystane w przypadku nagłych zmian popytu, opóźnień w dostawach lub innych nieoczekiwanych wydarzeń, takich jak awarie sprzętu czy problemy logistyczne. Choć zapasy bezpieczeństwa wiążą się z dodatkowymi kosztami związanymi z przechowywaniem i zarządzaniem zapasami, to ich odpowiednie zastosowanie pozwala firmom na minimalizację ryzyka związanego z przerwami w produkcji, utratą klientów oraz potencjalnymi stratami finansowymi. Wybór, kiedy i jak stosować zapasy bezpieczeństwa, zależy od wielu czynników, w tym stabilności łańcucha dostaw, zmienności popytu oraz charakterystyki produkcji. Przedsiębiorstwa muszą zatem zrównoważyć koszty utrzymania dodatkowych zapasów z korzyściami wynikającymi z zapewnienia nieprzerwanej działalności operacyjnej.
Rola zapasów bezpieczeństwa w zapewnieniu ciągłości produkcji
Zapas rezerwowy odgrywa rolę w zapewnieniu ciągłości produkcji, szczególnie w branżach, gdzie przestoje mogą prowadzić do znaczących strat finansowych oraz osłabienia pozycji rynkowej. Dzięki zapasom bezpieczeństwa firmy mogą utrzymać stabilność operacyjną, nawet w obliczu nieoczekiwanych wydarzeń, takich jak opóźnienia w dostawach, wahania popytu, czy awarie maszyn. W praktyce, zapasy te działają jako bufor, który zapewnia firmom dodatkowy czas na rozwiązanie problemów bez przerywania produkcji. Przykładowo, w przemyśle motoryzacyjnym, gdzie produkcja jest ściśle zsynchronizowana z dostawami komponentów, zapasy bezpieczeństwa mogą zapobiec kosztownym przestojom w przypadku opóźnień dostaw od kluczowych dostawców. W branżach o wysokiej zmienności popytu, takich jak sektor FMCG (Fast-Moving Consumer Goods), zapasy bezpieczeństwa pomagają firmom w elastycznym reagowaniu na nagłe wzrosty popytu, zapewniając dostępność produktów na półkach sklepowych. W ten sposób, zapasy bezpieczeństwa przyczyniają się do utrzymania ciągłości operacyjnej, co z kolei przekłada się na wyższą satysfakcję klientów oraz lepsze wyniki finansowe.
Jak określić odpowiedni poziom zapasów bezpieczeństwa?
Określenie odpowiedniego poziomu zapasów bezpieczeństwa jest wyzwaniem dla firm, które chcą zminimalizować ryzyko przerw w produkcji, jednocześnie kontrolując koszty obsługi zapasów – szczególnie tych nadmiernych. Proces ten wymaga dokładnej analizy wielu czynników, takich jak zmienność popytu, czas realizacji dostaw, niezawodność dostawców oraz koszty obsługi zapasów. Jednym z podstawowych podejść do określania poziomu zapasów bezpieczeństwa jest analiza statystyczna, która uwzględnia historyczne dane dotyczące popytu oraz czasu realizacji zamówień, aby oszacować prawdopodobieństwo wystąpienia niedoborów. W praktyce, firmy często stosują model zapasów bezpieczeństwa oparty na odchyleniu standardowym od średniego popytu, co pozwala na ustalenie poziomu zapasów, który z dużym prawdopodobieństwem pokryje nieprzewidziane zapotrzebowanie. Dodatkowo, systemy ERP mogą automatycznie dostosowywać poziom zapasów bezpieczeństwa w zależności od bieżących warunków rynkowych, takich jak zmiany popytu czy opóźnienia dostaw. Warto również uwzględnić strategiczne znaczenie poszczególnych surowców – surowce kluczowe dla produkcji mogą wymagać wyższego poziomu zapasów bezpieczeństwa niż surowce mniej istotne. Ostatecznie, odpowiednie zarządzanie zapasami bezpieczeństwa wymaga ciągłego monitorowania i dostosowywania strategii, aby utrzymywać optymalne poziomy zapasów, mimo zmieniających się warunków rynkowych.
Jak zarządzać zapasami: prognozowanie popytu i dostaw
Prognozowanie popytu i dostaw jest fundamentem skutecznego zarządzania zapasami w firmie produkcyjnej. Precyzyjne przewidywanie przyszłych potrzeb oraz terminowe zapewnienie dostaw surowców to czynniki, które decydują o ciągłości produkcji i efektywności operacyjnej. Prognozowanie pozwala firmom na lepsze planowanie zamówień, minimalizację kosztów obsługi zapasów oraz szybsze reagowanie na zmieniające się warunki rynkowe. Odpowiednie metody prognozowania, wspierane przez zaawansowane technologie i bliską współpracę z dostawcami, umożliwiają firmom nie tylko przewidywanie popytu, ale także zabezpieczenie się przed ryzykiem opóźnień w dostawach, co jest ważne w dynamicznych branżach, gdzie czas reakcji jest często decydującym czynnikiem konkurencyjnym.
Metody prognozowania popytu – analiza historyczna vs. predykcja na przyszłość
W prognozowaniu popytu firmy produkcyjne mogą korzystać z dwóch głównych podejść: analizy historycznej oraz predykcji na przyszłość. Analiza historyczna polega na wykorzystaniu danych z przeszłości, takich jak sprzedaż, zamówienia czy zmiany w popycie, do przewidywania przyszłych potrzeb. Jest to metoda oparta na założeniu, że przeszłe trendy będą się utrzymywać, co jest często skuteczne w stabilnych rynkach o niewielkich wahaniach. Zaletą tej metody jest jej stosunkowo prosta implementacja i niskie koszty, jednak jej skuteczność może być ograniczona w dynamicznych branżach, gdzie popyt może ulegać gwałtownym zmianom z powodu nowych trendów, zmian w preferencjach konsumentów czy innowacji technologicznych.
Z kolei predykcja na przyszłość wykorzystuje zaawansowane algorytmy, modele statystyczne, a często również sztuczną inteligencję, aby prognozować popyt na podstawie szerokiego zakresu danych, w tym wskaźników makroekonomicznych, trendów rynkowych, działań konkurencji oraz zachowań konsumenckich. Metoda ta jest bardziej złożona i wymaga zaawansowanych narzędzi analitycznych, ale oferuje większą precyzję i elastyczność w dynamicznie zmieniających się warunkach. Przykładowo, w branży technologicznej, gdzie cykle życia produktów są krótkie, a zmiany popytu mogą być nagłe i drastyczne, predykcja na przyszłość może dostarczyć bardziej trafnych i aktualnych prognoz, co umożliwia firmom lepsze planowanie produkcji i zamówień. Wybór między analizą historyczną a predykcją na przyszłość zależy od specyfiki rynku, branży oraz dostępnych zasobów analitycznych.
Współpraca z dostawcami surowców – jak zapewnić terminowość dostaw?
Współpraca z dostawcami surowców odgrywa rolę w zapewnieniu terminowości dostaw, co jest niezbędne do utrzymania ciągłości produkcji i minimalizacji ryzyka przerw w działalności. Aby zapewnić terminowość dostaw, firmy muszą nawiązywać i utrzymywać bliskie, partnerskie relacje z dostawcami, oparte na zaufaniu, transparentności i wzajemnym zrozumieniu potrzeb biznesowych. Ważnym elementem takiej współpracy jest regularna i otwarta komunikacja, która pozwala na bieżąco monitorować status zamówień, przewidywać potencjalne opóźnienia i szybko reagować na zmieniające się warunki. Wprowadzenie narzędzi takich jak EDI (Electronic Data Interchange) czy platformy współpracy online umożliwia automatyzację i usprawnienie wymiany informacji między firmą a dostawcami, co znacząco zwiększa efektywność komunikacji i skraca czas reakcji na ewentualne problemy.
.Kolejnym ważnym aspektem jest elastyczność w zarządzaniu zamówieniami i dostawami. Firmy powinny dążyć do dywersyfikacji bazy dostawców, co pozwala na zminimalizowanie ryzyka związanego z ewentualnymi problemami u jednego dostawcy. Ustalenie precyzyjnych umów z dostawcami, które zawierają klauzule dotyczące terminowości dostaw, kar za opóźnienia oraz procedur awaryjnych, może również pomóc w zabezpieczeniu interesów firmy. Długoterminowe partnerstwa z dostawcami, oparte na wzajemnych korzyściach, sprzyjają lepszej współpracy i zaangażowaniu dostawców w dostarczanie wysokiej jakości surowców na czas. Przykładowo, w przemyśle motoryzacyjnym, gdzie produkcja jest silnie uzależniona od terminowości dostaw komponentów, bliska współpraca z dostawcami oraz wspólne planowanie produkcji i logistyki jest kluczowe dla utrzymania płynności operacyjnej i spełnienia oczekiwań klientów.
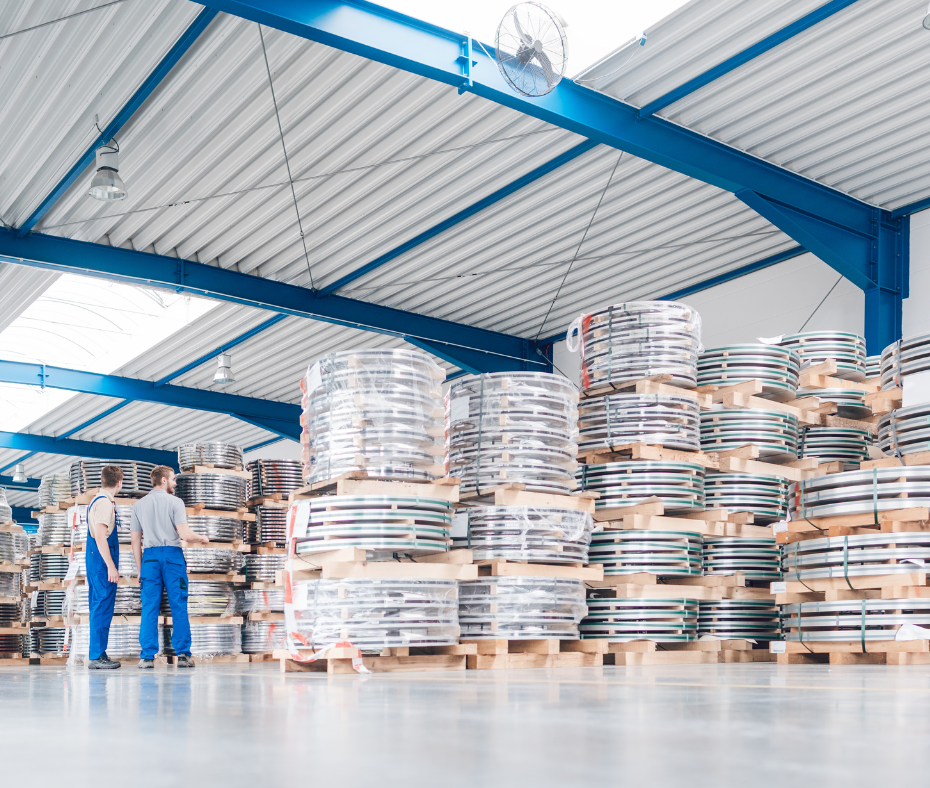
Praktyczne rozwiązania na wyzwania związane z zarządzaniem zapasami
Zarządzanie zapasami to jeden z najbardziej kluczowych i jednocześnie złożonych elementów logistyki w firmie produkcyjnej. W obliczu dynamicznie zmieniających się warunków rynkowych, fluktuacji popytu i nieprzewidywalności dostaw, firmy muszą stosować praktyczne i innowacyjne rozwiązania, aby sprostać wyzwaniom związanym z zarządzaniem zapasami. Skuteczne zarządzanie zapasami wymaga nie tylko precyzyjnego planowania i prognozowania, ale także wdrażania zaawansowanych narzędzi oraz elastycznych strategii, które pozwolą na szybkie reagowanie na zmieniające się warunki. Wśród tych rozwiązań znajdują się między innymi implementacja Vendor Managed Inventory (VMI), skracanie cyklu zamówień oraz opracowywanie strategii awaryjnych na wypadek nieprzewidzianych braków.
Implementacja Vendor Managed Inventory (VMI)
Vendor Managed Inventory (VMI) to zaawansowane rozwiązanie logistyczne, które przenosi odpowiedzialność za zarządzanie zapasami z odbiorcy na dostawcę. W ramach VMI dostawca monitoruje poziomy zapasów u swojego klienta i na ich podstawie samodzielnie decyduje o terminach i wielkości dostaw, co pozwala na bardziej efektywne zarządzanie zapasami i minimalizację ryzyka niedoborów. Implementacja VMI przynosi szereg korzyści, w tym redukcję kosztów magazynowania, lepszą synchronizację dostaw z rzeczywistym zapotrzebowaniem oraz zwiększenie elastyczności operacyjnej. Przykładowo, w branży motoryzacyjnej VMI pozwala na dostarczanie komponentów dokładnie wtedy, gdy są potrzebne na linii produkcyjnej, co minimalizuje zapasy magazynowe i optymalizuje przepływ materiałów. Wdrożenie VMI wymaga jednak silnej współpracy i zaufania między firmą a dostawcą, a także zaawansowanych systemów IT, które umożliwiają bieżące monitorowanie i analizę danych. Dzięki VMI firmy mogą osiągnąć większą stabilność operacyjną, lepiej zarządzać swoimi zasobami i zwiększać satysfakcję klientów poprzez zapewnienie ciągłości dostaw.
Redukcja cyklu zamówień – jak skrócić czas realizacji zamówień?
Skracanie cyklu zamówień jest jednym z elementów zwiększania efektywności operacyjnej i konkurencyjności na rynku. Krótszy czas realizacji zamówień pozwala firmom na szybsze reagowanie na zmieniające się potrzeby klientów, zmniejszenie poziomu zapasów i redukcję kosztów operacyjnych. Aby skutecznie skrócić cykl zamówień, firmy mogą zastosować kilka praktycznych strategii, w tym automatyzację procesów zamówieniowych, optymalizację łańcucha dostaw oraz współpracę z dostawcami na zasadach just-in-time. Automatyzacja zamówień poprzez wykorzystanie zaawansowanych systemów ERP pozwala na natychmiastowe generowanie zamówień na podstawie aktualnych stanów magazynowych i prognoz popytu, co eliminuje opóźnienia wynikające z ręcznego przetwarzania danych. Dodatkowo, optymalizacja łańcucha dostaw, poprzez eliminację zbędnych etapów i usprawnienie komunikacji między partnerami biznesowymi, przyczynia się do szybszej realizacji zamówień. Współpraca na zasadach just-in-time z dostawcami pozwala na dostarczanie surowców i komponentów dokładnie wtedy, gdy są potrzebne, co minimalizuje czas oczekiwania na dostawy i zwiększa elastyczność produkcji. Dzięki tym strategiom firmy mogą skrócić cykl zamówień, co przekłada się na właściwe zarządzanie zapasami i wyższą satysfakcję klientów.
Strategie awaryjne – co robić w przypadku nieprzewidzianych braków?
Wspomniałem na początku, że koszty braku zapasów są bardzo wysokie. Nieprzewidziane braki zapasów mogą prowadzić do poważnych problemów operacyjnych, takich jak przerwy w produkcji, opóźnienia w realizacji zamówień czy nawet utrata klientów. Aby zminimalizować ryzyko związane z niedoborami, firmy muszą opracować i wdrożyć skuteczne strategie awaryjne. Jednym z podstawowych elementów takiej strategii jest utrzymywanie zapasów bezpieczeństwa, które mogą być wykorzystane w sytuacjach kryzysowych. Jednakże, w przypadku nagłych i nieprzewidywalnych braków, firmy powinny również mieć przygotowane inne rozwiązania, takie jak szybkie uzupełnianie zapasów, poszukiwanie alternatywnych dostawców, elastyczne zarządzanie harmonogramem produkcji oraz natychmiastowa komunikacja z klientami.
Szybkie znalezienie alternatywnych dostawców lub wykorzystanie zamienników może pomóc w szybkim uzupełnieniu braków i uniknięciu przerw w produkcji. Elastyczne i efektywne metody zarządzania produkcją, poprzez reorganizację procesów i priorytetyzację zleceń, pozwala na efektywne wykorzystanie dostępnych zasobów. Istotna jest również otwarta i szybka komunikacja z klientami, informowanie ich o możliwych opóźnieniach oraz proponowanie alternatywnych rozwiązań, co może pomóc w utrzymaniu zaufania i lojalności klientów. Skuteczne strategie awaryjne nie tylko minimalizują negatywne skutki niedoborów, ale również zwiększają odporność firmy na nieprzewidziane zdarzenia i poprawiają jej zdolność do szybkiego reagowania na zmieniające się warunki rynkowe.
Podsumowanie
Właściwe zarządzanie zapasami surowców w firmie produkcyjnej to niepozorny element, który bezpośrednio wpływa na efektywność operacyjną, zdolność do reagowania na zmieniający się popyt oraz redukcję kosztów związanych z przechowywaniem zapasów w nadmiarze. Bliska współpraca z dostawcami, oparta na zaufaniu i transparentnej komunikacji, jest niezbędna do zapewnienia terminowości dostaw, co z kolei pozwala na dostosowania poziomu zapasów, a co za tym idzie utrzymanie ciągłości produkcji i minimalizację ryzyka przerw. Wdrożenie takich strategii i narzędzi pomaga firmom nie tylko unikać nieprzewidzianych braków, ale także budować bardziej elastyczny i odporny na zmiany łańcuch dostaw. Odpowiedni system zarządzania poziomem zapasów pozwala na zmniejszenie kosztów utrzymania zapasów i zmniejszenie ryzyka nadmiaru zapasów, jednocześnie redukując ryzyko ich braku. Operacyjne zarządzanie zapasami i monitorowanie stanu zapasów pozwalają na elastyczne zarządzanie ryzykiem i popytem. Wszystko to przekłada się na niższe koszty zarządzania zapasami, podnosi wartość zapasów, które są efektywnie wykorzystywane i zwiększa konkurencyjność firmy.
Pobierz bazę 100 wskaźników produkcyjnych
za darmo!
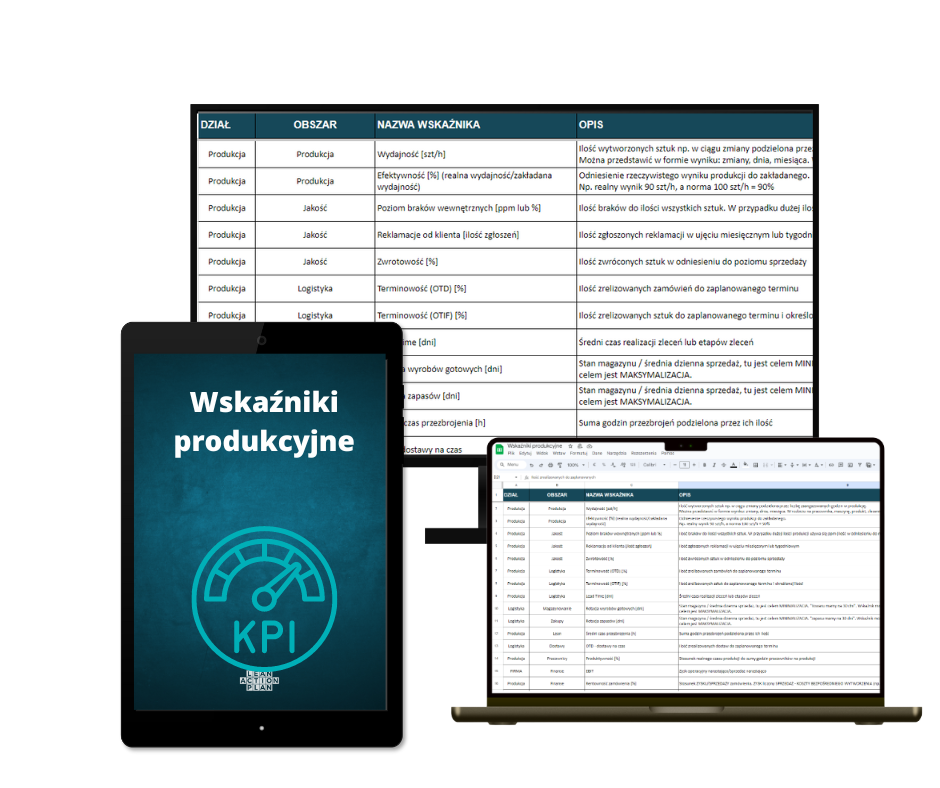