Rozmieszczenie maszyn produkcyjnych – najlepsze strategie
Powierzchnia to kapitał – mówiłem o tym w jednym z odcinków podcastu Produkcja bez chaosu. Twoja hala może generować zyski, ale może też generować straty. Wszystko zależy od jednej rzeczy, jaką jest… rozmieszczenie maszyn na hali produkcyjnej. Odpowiednie strategie rozmieszczenia maszyn produkcyjnych pozwala wykorzystać powierzchnię tak, aby nie tracić na niej, a właśnie zarabiać. Gniazda produkcyjne, identyfikacja wąskich gardeł pozwalają na optymalizację organizacji produkcji. No dobra, jakie strategie rozmieszczenia maszyn produkcyjnych wybrać?
Spis treści:
- Znaczenie optymalnego rozmieszczenia maszyn produkcyjnych na hali
- Metody i narzędzia do analizy i planowania layoutu fabryki
- Instalacja i montaż linii produkcyjnych w kontekście optymalizacji rozmieszczenia
- Zarządzanie i kontrola procesu produkcji w kontekście layoutu fabryki
- Rozmieszczenie maszyn produkcyjnych – wdrożenie strategii
- Podsumowanie
- Odbierz za darmo: BAZA WSKAŹNIKÓW PRODUKCYJNYCH
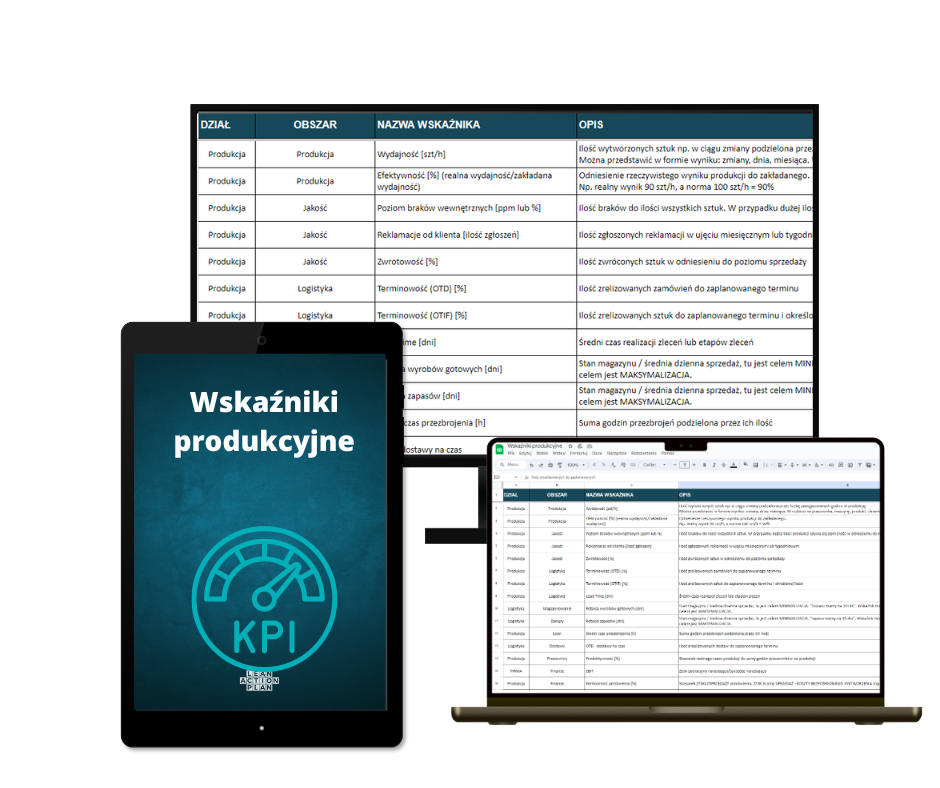
Znaczenie optymalnego rozmieszczenia maszyn produkcyjnych na hali
Zanim wybierzemy strategię, warto zrozumieć po co i dlaczego odpowiednie rozmieszczenie maszyn produkcyjnych na hali jest takie ważne. Dobre rozmieszczenie maszyn na hali produkcyjnej wpływa na efektywność operacyjną, przepływ materiałów oraz bezpieczeństwo pracowników. Jak to możliwe? Dobrze zaprojektowany layout fabryki może zwiększyć wydajność, bo minimalizuje czas i odległość potrzebne do przemieszczenia surowców, półproduktów i gotowych produktów między etapami produkcji. Dodatkowo, odpowiednie rozmieszczenie maszyn produkcyjnych pozwala na lepsze wykorzystanie dostępnej przestrzeni, co jest szczególnie ważne w przypadku ograniczonych zasobów. Efektywne rozmieszczenie maszyn produkcyjnych i stanowisk pracy zmniejsza ryzyko kolizji i wypadków, poprawia ergonomię stanowisk pracy oraz przyczynia się do ogólnego wzrostu produktywności (zmniejsza czas produkcji produktu) i jakości produktów końcowych. Jak to możliwe? Odpowiedni layout hali produkcyjnej ułatwia efektywne zarządzanie produkcją oraz jej kontrolę.
Jak rozmieszczenie maszyn produkcyjnych wpływa na efektywność produkcji?
Rozmieszczenie maszyn produkcyjnych bezpośrednio wpływa na efektywność produkcji poprzez optymalizację przepływu materiałów, redukcję czasów przestoju i minimalizację strat. Gdy maszyny są ustawione w sposób umożliwiający płynny przepływ procesów produkcyjnych, zmniejsza się czas potrzebny na przemieszczanie surowców i produktów między poszczególnymi etapami produkcji. To z kolei prowadzi do skrócenia cyklu produkcyjnego i zwiększenia wydajności. Dodatkowo, odpowiednie rozmieszczenie maszyn minimalizuje potrzebę przechowywania dużych ilości surowców i półproduktów w różnych miejscach fabryki, co redukuje koszty magazynowania i transportu wewnętrznego. Zmniejszenie odległości między stanowiskami pracy pozwala także na szybsze reagowanie na ewentualne problemy i awarie, co minimalizuje czas przestoju i poprawia ogólną efektywność produkcji.
Jak rozmieszczenie maszyn produkcyjnych wpływa na bezpieczeństwo pracy?
Bezpieczeństwo pracy w fabrykach produkcyjnych jest absolutnym priorytetem, a odpowiednie rozmieszczenie maszyn odgrywa rolę w minimalizowaniu ryzyka wypadków i urazów. Optymalne rozmieszczenie maszyn nie tylko zwiększa efektywność operacyjną, ale także poprawia warunki pracy. Właściwe ustawienie maszyn uwzględnia również łatwy dostęp do wyłączników awaryjnych i punktów ewakuacyjnych, co jest bardzo ważne w sytuacjach zagrożenia. Pracodawcy muszą przestrzegać przepisów BHP oraz standardów ergonomicznych, aby zapewnić pracownikom bezpieczne i komfortowe środowisko pracy, co przyczynia się do zmniejszenia liczby wypadków oraz poprawy ogólnej wydajności produkcji.
Rozmieszczenie maszyn w przestrzeni produkcyjnej ma bezpośredni wpływ na bezpieczeństwo pracy, ponieważ determinuje sposób, w jaki pracownicy poruszają się po hali, wykonują swoje zadania i wchodzą w interakcje z urządzeniami. Odpowiednie rozmieszczenie maszyn powinno minimalizować ryzyko kolizji między pracownikami a sprzętem, zapewniając szerokie, wolne od przeszkód ścieżki komunikacyjne oraz wyraźnie oznaczone strefy pracy. Ważne jest, aby maszyny były ustawione w sposób umożliwiający pracownikom łatwy dostęp do paneli sterowania i narzędzi, bez konieczności wykonywania niebezpiecznych ruchów lub nadmiernego wysiłku fizycznego. Dodatkowo, przestrzeganie zasad ergonomii w rozmieszczeniu maszyn pomaga zapobiegać urazom związanym z powtarzającymi się ruchami oraz niewłaściwą postawą ciała. Równie istotne jest zapewnienie odpowiedniego oświetlenia oraz wentylacji, co przyczynia się do lepszego widzenia i komfortu pracy, redukując ryzyko wypadków i poprawiając ogólne bezpieczeństwo w fabryce.
Zasady lean manufacturing a plan ustawienia maszyn
Lean manufacturing kładzie duży nacisk na eliminację marnotrawstwa i maksymalizację wartości dodanej w procesach produkcyjnych. Zasady lean manufacturing mają istotny wpływ na planowanie rozmieszczenia maszyn, ponieważ dążą do stworzenia jak najbardziej efektywnego i elastycznego układu fabryki. Podstawowe zasady lean, takie jak ciągły przepływ, just-in-time oraz pull system, wymagają takiego ustawienia maszyn, które minimalizuje przestoje, zmniejsza zapasy i umożliwia szybkie dostosowanie się do zmieniających się wymagań produkcyjnych. Layout w firmie zgodny z zasadami lean powinien umożliwiać łatwy dostęp do wszystkich zasobów i stanowisk pracy, skracając czas przemieszczania materiałów oraz ułatwiając monitorowanie i kontrolowanie procesów. Ponadto, lean manufacturing promuje ustawienie maszyn w sposób, który wspiera autonomię i zaangażowanie pracowników w procesy ciągłego doskonalenia, co przyczynia się do poprawy jakości i efektywności produkcji.
Rola analizy layoutu fabryki w optymalizacji rozmieszczenia maszyn
Analiza layoutu fabryki odgrywa rolę w optymalizacji rozmieszczenia maszyn, ponieważ pozwala na identyfikację obszarów, które wymagają poprawy oraz na zaprojektowanie bardziej efektywnego układu produkcyjnego. Proces ten zazwyczaj rozpoczyna się od zbierania i analizy danych dotyczących przepływu materiałów, czasów cyklu, odległości między stanowiskami pracy oraz częstości występowania problemów i awarii. Na podstawie tych informacji można opracować różne scenariusze rozmieszczenia maszyn i ocenić ich wpływ na efektywność produkcji.
Wykorzystanie narzędzi takich jak symulacje komputerowe, diagramy spaghetti oraz mapowanie strumienia wartości (Value Stream Mapping) pozwala na wizualizację obecnego layoutu oraz na przetestowanie potencjalnych zmian przed ich wdrożeniem. Analiza layoutu fabryki umożliwia także uwzględnienie przyszłych potrzeb produkcyjnych, takich jak wzrost produkcji, wprowadzenie nowych produktów czy zmiany w technologii, co pozwala na stworzenie elastycznego i skalowalnego układu fabryki. Efektywna optymalizacja layoutu fabryki przyczynia się do zwiększenia wydajności, redukcji kosztów operacyjnych oraz poprawy bezpieczeństwa i komfortu pracy, co w długoterminowej perspektywie przekłada się na wyższe zyski i większą konkurencyjność firmy.
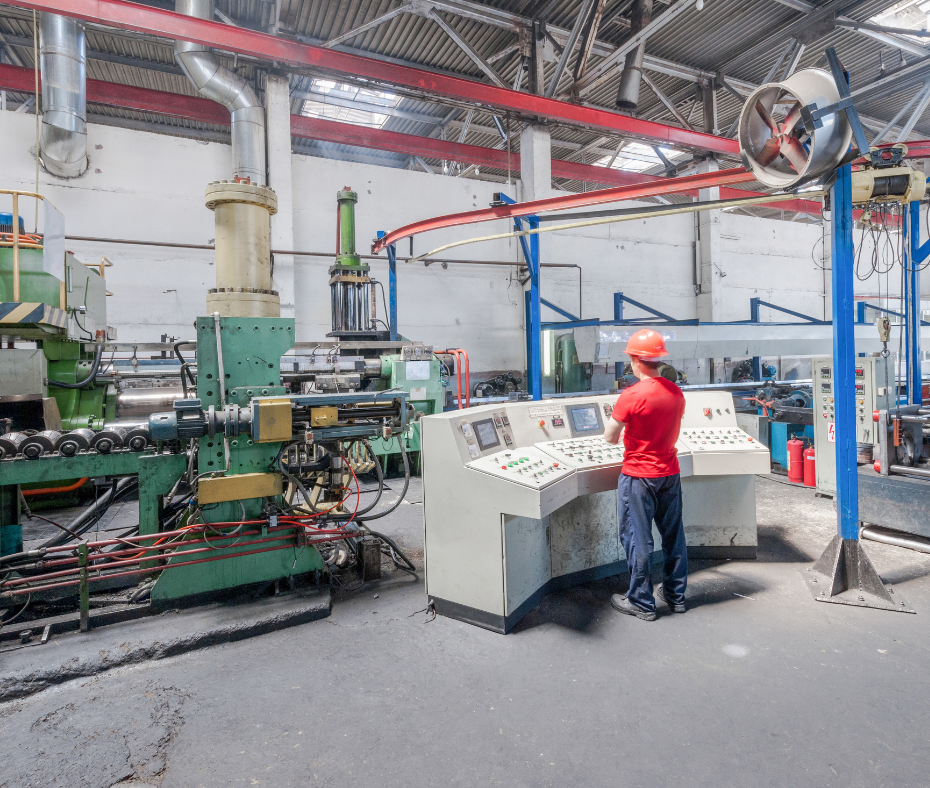
Metody i narzędzia do analizy i planowania layoutu fabryki
Analiza i planowanie layoutu w firmie są elementami zarządzania produkcją, które mają na celu optymalizację przepływu materiałów, minimalizację kosztów operacyjnych oraz poprawę efektywności pracy. W procesie tym stosuje się różnorodne metody i narzędzia, które pomagają zrozumieć obecny układ fabryki, identyfikować potencjalne problemy oraz opracowywać bardziej efektywne rozwiązania. Główne narzędzia obejmują diagramy spaghetti, mapowanie strumienia wartości (Value Stream Mapping), symulacje komputerowe oraz analizy ABC. Te narzędzia umożliwiają wizualizację przepływu pracy, identyfikację wąskich gardeł oraz ocenę różnych scenariuszy rozmieszczenia maszyn. Dzięki temu możliwe jest opracowanie layoutu fabryki, który maksymalizuje wydajność produkcji, redukuje straty i poprawia jakość produktów.
Diagram spaghetti jako narzędzie do analizy przepływu pracy
Diagram spaghetti to proste, ale niezwykle skuteczne narzędzie służące do analizy przepływu pracy w fabryce. Polega ono na śledzeniu ruchu materiałów, półproduktów i pracowników w przestrzeni produkcyjnej oraz zaznaczaniu ich ścieżek na planie fabryki. W rezultacie powstaje wizualna reprezentacja przepływu pracy, która przypomina poplątane nitki spaghetti, stąd nazwa tego narzędzia. Diagram spaghetti pozwala na łatwą identyfikację nieefektywności, takich jak nadmierne przemieszczanie się, powtarzalne trasy i zbędne kroki w procesie produkcyjnym. Analiza tych ścieżek umożliwia zidentyfikowanie obszarów, w których można wprowadzić usprawnienia, takie jak zmiana rozmieszczenia maszyn, skrócenie dystansów czy eliminacja zbędnych ruchów. Wprowadzenie zmian na podstawie diagramu spaghetti prowadzi do bardziej płynnego przepływu pracy, redukcji czasu cyklu i zwiększenia wydajności produkcji.
Zastosowanie analizy layoutu w planowaniu produkcji
Analiza layoutu hali produkcyjnej jest nieodzownym elementem planowania produkcji, ponieważ umożliwia ocenę efektywności obecnego układu i identyfikację obszarów wymagających optymalizacji. Proces ten obejmuje zbieranie i analizę danych dotyczących przepływu materiałów, czasów przetwarzania, odległości między stanowiskami pracy oraz stopnia wykorzystania przestrzeni. Na podstawie tych informacji można opracować różne scenariusze rozmieszczenia maszyn produkcyjnych i ocenić ich wpływ na wydajność produkcji. Wykorzystanie narzędzi takich jak symulacje komputerowe pozwala na przetestowanie różnych układów przed ich wdrożeniem, co minimalizuje ryzyko nieudanych zmian. Analiza layoutu pomaga również w uwzględnieniu przyszłych potrzeb produkcyjnych, takich jak zwiększenie mocy produkcyjnych, wprowadzenie nowych produktów czy zmiany w technologii. Dzięki temu możliwe jest stworzenie elastycznego i skalowalnego układu fabryki, który zapewnia optymalną efektywność produkcji w długoterminowej perspektywie.
Jak zidentyfikować i zminimalizować wąskie gardła w procesie produkcyjnym?
Identyfikacja i minimalizacja wąskich gardeł w procesie produkcyjnym są istotne dla poprawy efektywności i płynności produkcji. Wąskie gardła to punkty w procesie, które ograniczają przepustowość całego systemu i powodują opóźnienia oraz zwiększenie kosztów operacyjnych. Aby zidentyfikować wąskie gardła, można wykorzystać różne metody, takie jak analiza przepływu pracy, diagramy spaghetti, mapowanie strumienia wartości (VSM) oraz narzędzia do monitorowania danych produkcyjnych w czasie rzeczywistym.
Analiza przepływu pracy pozwala na zrozumienie, gdzie występują opóźnienia i przeciążenia, natomiast VSM pomaga w identyfikacji procesów, które generują najwięcej strat i opóźnień. Monitorowanie danych produkcyjnych w czasie rzeczywistym, za pomocą systemów MES (Manufacturing Execution System), umożliwia bieżące śledzenie wydajności maszyn i pracowników, co pozwala na szybkie reagowanie na problemy.
Aby zminimalizować wąskie gardła, można wdrożyć różne strategie, takie jak zwiększenie wydajności maszyn, wprowadzenie dodatkowych zasobów na newralgicznych etapach produkcji, optymalizacja harmonogramu produkcji oraz eliminacja zbędnych kroków w procesie. Ważne jest również regularne monitorowanie i analiza danych, aby na bieżąco identyfikować i reagować na pojawiające się wąskie gardła. Wdrażanie ciągłego doskonalenia procesów oraz angażowanie pracowników w identyfikację i rozwiązywanie problemów produkcyjnych pozwala na utrzymanie wysokiej efektywności i płynności produkcji w długoterminowej perspektywie.
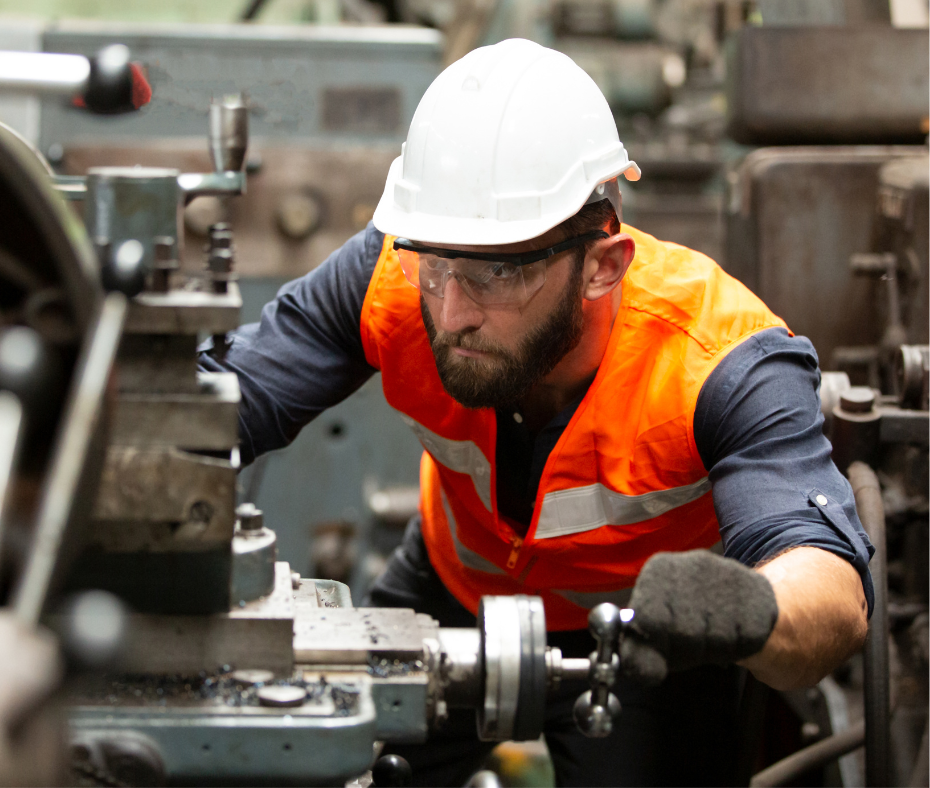
Instalacja i montaż linii produkcyjnych w kontekście optymalizacji rozmieszczenia
Instalacja i montaż linii produkcyjnych to ważne etapy w projektowaniu efektywnej przestrzeni produkcyjnej. Optymalne rozmieszczenie maszyn i stanowisk pracy w linii produkcyjnej ma ogromny wpływ na wydajność operacyjną, jakość produktów oraz bezpieczeństwo pracowników. Proces ten zaczyna się od dokładnej analizy przepływu materiałów, wymagań produkcyjnych oraz przestrzennych ograniczeń fabryki. Projektanci muszą uwzględnić różne czynniki, takie jak ergonomia, łatwość konserwacji, dostępność do komponentów oraz możliwość przyszłych modyfikacji układu. Właściwe rozmieszczenie linii produkcyjnych pozwala na minimalizację marnotrawstwa, redukcję czasów przestoju i optymalizację przepływu pracy, co w rezultacie zwiększa efektywność produkcji i zmniejsza koszty operacyjne.
Wymagania techniczne a rozmieszczenie linii produkcyjnej
Rozmieszczenie linii produkcyjnej musi spełniać określone wymagania techniczne, aby zapewnić jej sprawne i bezpieczne działanie. Wymagania te obejmują specyfikacje dotyczące instalacji elektrycznych, systemów hydraulicznych i pneumatycznych, wentylacji, a także normy bezpieczeństwa i ergonomii. Przede wszystkim, maszyny i urządzenia muszą być rozmieszczone w sposób umożliwiający łatwy dostęp do wszystkich elementów wymagających konserwacji i naprawy, co minimalizuje czas przestoju spowodowany awariami. Ponadto, rozmieszczenie powinno uwzględniać przepisy dotyczące bezpiecznych odległości między maszynami, aby zapobiec kolizjom i zapewnić przestrzeń do swobodnego przemieszczania się pracowników. Wymagania techniczne dotyczą również zapewnienia odpowiednich warunków środowiskowych, takich jak temperatura, wilgotność i oświetlenie, które mogą wpływać na wydajność i trwałość maszyn oraz komfort pracy operatorów. Wszystkie te czynniki muszą być uwzględnione podczas projektowania i instalacji linii produkcyjnej, aby zapewnić jej optymalne funkcjonowanie.
Redukcja odległości i optymalizacja przepływu w procesie montażu linii
Redukcja odległości i optymalizacja przepływu materiałów są elementami w procesie montażu linii produkcyjnych. Skrócenie odległości między poszczególnymi maszynami i stanowiskami pracy minimalizuje czas potrzebny na przemieszczanie materiałów, co z kolei zwiększa wydajność produkcji. W praktyce oznacza to analizę i mapowanie aktualnych przepływów materiałowych oraz identyfikację i eliminację zbędnych kroków i odległości w procesie produkcyjnym. Można to osiągnąć poprzez zastosowanie narzędzi takich jak diagramy spaghetti, które wizualizują ścieżki przemieszczania materiałów i pracowników.
Optymalizacja przepływu obejmuje również zorganizowanie maszyn i stanowisk w taki sposób, aby umożliwiały one płynny i logiczny przepływ pracy, od surowców po gotowe produkty. Przykładem może być zastosowanie układu linii produkcyjnej w kształcie litery U lub L, co minimalizuje konieczność przemieszczania się materiałów na duże odległości i ułatwia zarządzanie procesem produkcyjnym. Dodatkowo, integracja automatyzacji i nowoczesnych technologii, takich jak przenośniki taśmowe, roboty i systemy magazynowania, może znacząco poprawić przepływ materiałów i zwiększyć efektywność linii produkcyjnej. Dzięki tym optymalizacjom możliwe jest nie tylko zwiększenie wydajności produkcji, ale także poprawa jakości produktów i redukcja kosztów operacyjnych.
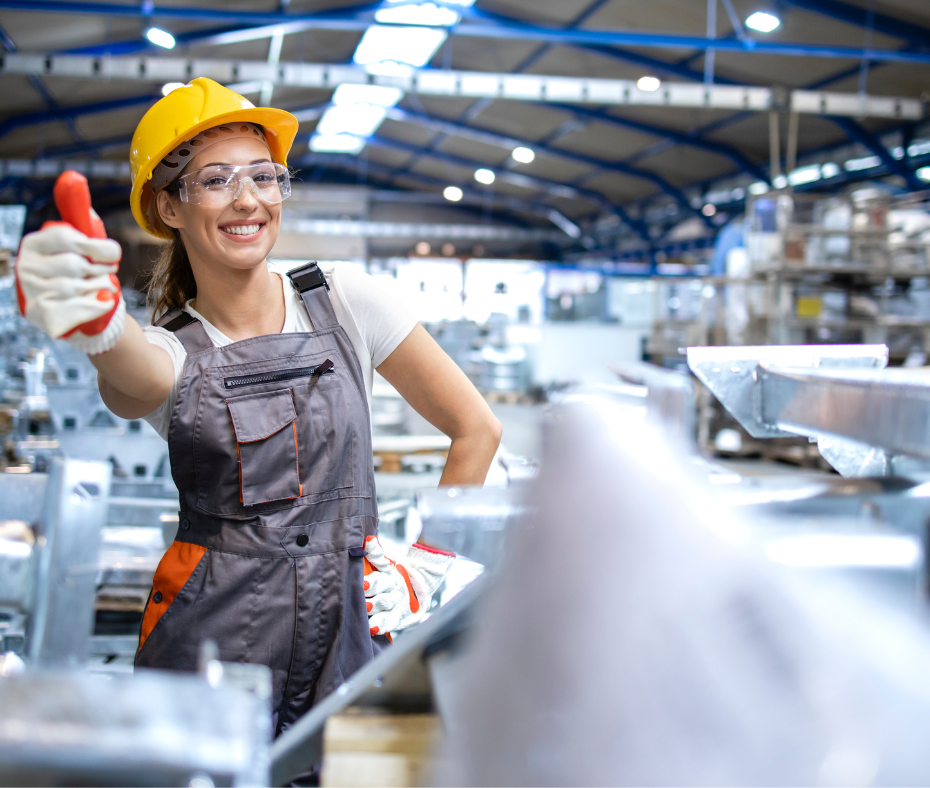
Szkolenie Online
Ergonomia stanowisk pracy
Podstawy prawne odnośnie ergonomii stanowisk pracy
Prawidłowa analiza stanowisk pracy
Poznanie istoty, celu i funkcji ergonomii
Ocena i szacowanie ryzyka wystąpienia dolegliwości
Zarządzanie i kontrola procesu produkcji w kontekście layoutu fabryki
Zarządzanie i kontrola procesu produkcji są ściśle związane z layoutem fabryki, który bezpośrednio wpływa na efektywność operacyjną, jakość produktów i bezpieczeństwo pracowników. Optymalny layout fabryki umożliwia płynny przepływ materiałów, minimalizuje przestoje i redukuje koszty operacyjne. Efektywne zarządzanie procesem produkcji wymaga ciągłego monitorowania i analizy danych produkcyjnych, co pozwala na szybkie reagowanie na wszelkie odchylenia od normy. W kontekście layoutu fabryki, istotne jest, aby maszyny i stanowiska pracy były rozmieszczone w sposób umożliwiający łatwy dostęp do wszystkich zasobów, skracając tym samym czas przemieszczania się surowców i półproduktów. Regularne przeglądy i audyty layoutu mogą pomóc w identyfikacji obszarów wymagających optymalizacji, co w konsekwencji prowadzi do lepszej koordynacji działań, zwiększenia wydajności produkcji i poprawy jakości końcowych produktów.
Ciągły przepływ i płynność procesów produkcyjnych jako cel optymalizacji layoutu
Ciągły przepływ i płynność procesów produkcyjnych są fundamentalnymi celami optymalizacji layoutu fabryki. Płynność produkcji oznacza minimalizację przerw i przestojów, co prowadzi do bardziej efektywnego wykorzystania zasobów i zwiększenia wydajności. Aby osiągnąć ciągły przepływ, layout fabryki musi być zaprojektowany w sposób umożliwiający logiczny i nieprzerwany przepływ materiałów od surowców do gotowych produktów. Obejmuje to eliminację zbędnych kroków i odległości, co redukuje czas przemieszczenia się oraz zmniejsza ryzyko błędów i strat. Narzędzia takie jak Value Stream Mapping (VSM) pomagają w identyfikacji i eliminacji marnotrawstwa w procesach produkcyjnych, co wspiera osiągnięcie płynności produkcji. Optymalizacja layoutu z naciskiem na ciągły przepływ przyczynia się do poprawy jakości produktów, zwiększenia satysfakcji klientów oraz redukcji kosztów operacyjnych.
Budowa hali produkcyjnej a plan ustawienia maszyn
Budowa hali produkcyjnej powinna być dokładnie zaplanowana, aby zapewnić optymalne ustawienie maszyn, które wspiera zarówno efektywność produkcji, jak i bezpieczeństwo pracy. Projektowanie hali produkcyjnej rozpoczyna się od analizy wymagań produkcyjnych oraz specyfikacji technicznych maszyn, co pozwala na zaplanowanie odpowiednich stref roboczych, magazynowych oraz komunikacyjnych. Istotnym elementem jest zapewnienie, że układ hali umożliwia płynny przepływ materiałów i produktów między poszczególnymi etapami produkcji, minimalizując zbędne przemieszczenia i opóźnienia.
W trakcie budowy hali należy uwzględnić również aspekty związane z instalacjami elektrycznymi, systemami wentylacyjnymi i chłodzącymi, które muszą być dostosowane do specyficznych wymagań poszczególnych maszyn. Ważne jest także zaplanowanie przestrzeni dla serwisowania i konserwacji urządzeń, co pozwala na szybkie i bezpieczne przeprowadzanie prac naprawczych bez zakłócania procesu produkcyjnego. Wreszcie, należy uwzględnić zasady bezpieczeństwa pożarowego, takie jak odpowiednia lokalizacja gaśnic, systemów alarmowych i dróg ewakuacyjnych, które muszą być łatwo dostępne dla wszystkich pracowników. Skuteczne planowanie i budowa hali produkcyjnej z uwzględnieniem tych wszystkich aspektów pozwalają na stworzenie bezpiecznego, efektywnego i ergonomicznego środowiska pracy.
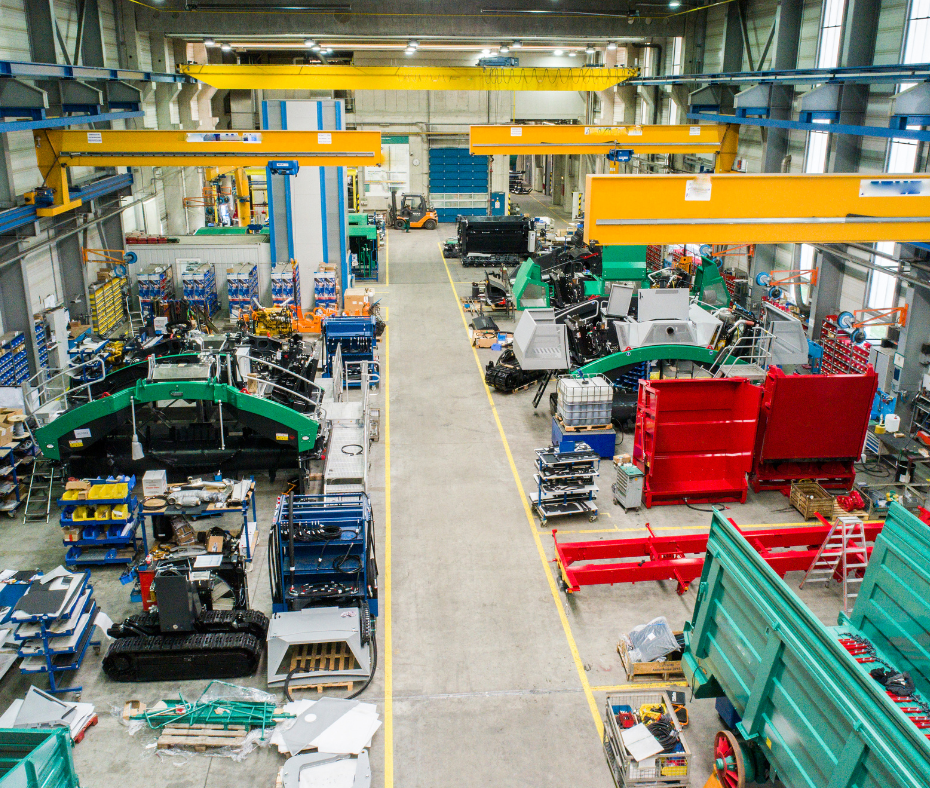
Rozmieszczenie maszyn produkcyjnych – wdrożenie strategii
Jak już ustaliliśmy – strategie rozmieszczenia maszyn produkcyjnych odgrywają rolę w optymalizacji procesów produkcyjnych, zwiększaniu wydajności i zapewnieniu bezpieczeństwa w zakładach produkcyjnych. Różne firmy stosują różnorodne podejścia w zależności od swoich specyficznych potrzeb i celów produkcyjnych. Przykładem może być układ linii produkcyjnych w kształcie litery U, który pozwala na minimalizację odległości między maszynami, co z kolei skraca czas przemieszczania się materiałów i półproduktów. Inne firmy mogą stosować układ w linii prostej, szczególnie w przypadku produkcji masowej, gdzie istotne jest utrzymanie stałego przepływu materiałów.
Strategie te są często wspierane przez technologie takie jak systemy wizyjne, które monitorują jakość produktów na każdym etapie produkcji, oraz systemy ERP lub aplikacje, np. ZaPro , które umożliwiają zarządzanie zasobami i optymalizację harmonogramów produkcyjnych. Dzięki analizie danych i ciągłemu doskonaleniu procesów, firmy mogą wdrażać strategie rozmieszczenia maszyn, które maksymalizują efektywność operacyjną, minimalizują koszty i poprawiają jakość produktów.
Wdrożenie nowej produkcji a plan rozmieszczenia maszyn
Wdrożenie nowej produkcji w istniejącej fabryce wymaga starannego planowania rozmieszczenia maszyn, aby zminimalizować zakłócenia w bieżących procesach i zapewnić płynne przejście do nowego systemu. Ważnym elementem tego procesu jest analiza wymagań nowej produkcji, w tym specyfikacji technicznych maszyn, wymaganych przepływów materiałowych oraz potencjalnych wąskich gardeł. Na tej podstawie można opracować plan rozmieszczenia, który uwzględnia zarówno przestrzeń potrzebną dla nowych maszyn, jak i integrację z istniejącymi systemami produkcyjnymi.
Przed wdrożeniem nowej produkcji, warto przeprowadzić symulacje komputerowe, które pozwalają na przetestowanie różnych scenariuszy rozmieszczenia i ich wpływu na efektywność produkcji. Właściwe planowanie rozmieszczenia maszyn podczas wdrażania nowej produkcji może znacząco przyczynić się do sukcesu projektu, minimalizując ryzyko przestojów i maksymalizując wydajność od samego początku.
Działania firmy produkcyjnej na rzecz optymalizacji rozmieszczenia maszyn
Firmy produkcyjne podejmują szereg działań mających na celu optymalizację rozmieszczenia maszyn, aby zwiększyć wydajność produkcji, zredukować koszty operacyjne oraz poprawić jakość produktów. Jednym z pierwszych kroków jest przeprowadzenie dokładnej analizy obecnego layoutu fabryki, identyfikacja wąskich gardeł oraz zbędnych kroków w procesach produkcyjnych. W tym celu często wykorzystuje się narzędzia takie jak diagramy spaghetti, mapowanie strumienia wartości (VSM) oraz symulacje komputerowe, które pozwalają na wizualizację i analizę przepływów materiałowych oraz operacyjnych.
Na podstawie zebranych danych, firmy mogą opracować plany reorganizacji przestrzeni produkcyjnej, które obejmują przestawienie maszyn, zmianę układu stanowisk pracy oraz optymalizację tras przepływu materiałów. Wdrożenie takich zmian często wiąże się z koniecznością inwestycji w nowe technologie, takie jak systemy automatyzacji, przenośniki taśmowe czy roboty przemysłowe, które zwiększają efektywność i elastyczność produkcji. Dodatkowo, firmy mogą wprowadzać regularne audyty i przeglądy layoutu fabryki, aby na bieżąco monitorować efektywność wprowadzonych zmian i dostosowywać strategie rozmieszczenia maszyn do zmieniających się potrzeb produkcyjnych.
Optymalizacja rozmieszczenia maszyn wymaga również zaangażowania pracowników na wszystkich poziomach organizacji. Szkolenia i warsztaty z zakresu lean manufacturing oraz continuous improvement mogą pomóc w budowaniu kultury ciągłego doskonalenia, gdzie pracownicy są aktywnie zaangażowani w identyfikację problemów i proponowanie usprawnień. Jednym z takich elementów mogą być warsztaty Layout. To praktyczne szkolenie, którego celem jest ułożenie optymalnego dla Twojej firmy planu rozmieszczenia maszyn. Dzięki takim działaniom firmy mogą osiągnąć trwałą poprawę efektywności operacyjnej, zwiększenie zadowolenia klientów oraz wzmocnienie swojej pozycji konkurencyjnej na rynku.
Podsumowanie
Podsumowując, odpowiednie rozmieszczenie maszyn produkcyjnych na hali, wspierane przez zaawansowane narzędzia analityczne i technologie, jest niezbędne do osiągnięcia optymalnej efektywności operacyjnej. Optymalizacja procesów produkcji jest możliwa dzięki ustaleniu, jaki layout w firmie sprawdzi się najlepiej. Odpowiedni montaż linii produkcyjnych, gniazda produkcyjne ułatwiają efektywne zarządzanie produkcją i kontrolę produkcji.
W usprawnianiu produkcji potrzebne są konieczne narzędzia – jednym z przydatnych jest aplikacja ZaPro. To rozwiązanie stworzone na potrzeby i specyfikę branży produkcyjnej, pozwala więc na kontrolę przekroju procesów produkcyjnych.
Sprawdź odcinek naszego podcastu ,,Produkcja bez chaosu“, w którym odpowiadamy na pytanie: “Jak zaprojektować ułożenie maszyn na hali produkcyjnej”
Rozmawiamy o tym:
- Czemu ustawienie maszyn na hali produkcyjnej jest takie ważne?
- Jak zaprojektować idealny layout, aby zwiększyć efektywność produkcji?
- Krok po kroku: Jak projektować ułożenie maszyn w praktyce?
Pobierz bazę 100 wskaźników produkcyjnych
za darmo!
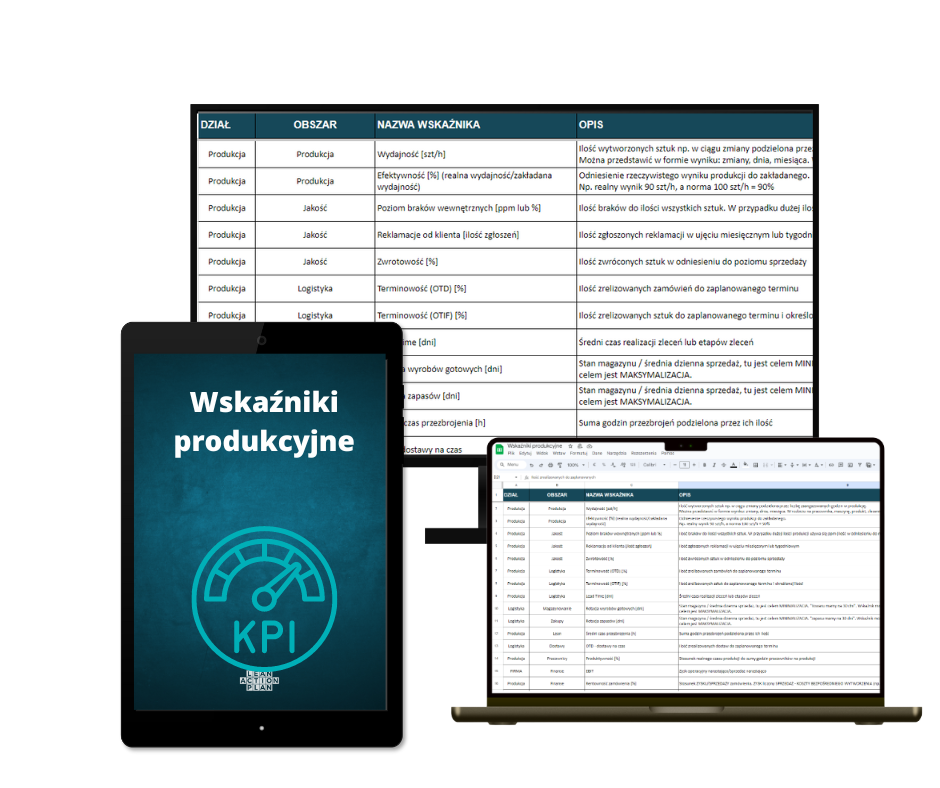