Standaryzacja procesów pracy w firmie produkcyjnej
Standaryzacja procesów pracy to fundament skutecznego zarządzania w firmach produkcyjnych. Dzięki niej można osiągnąć powtarzalność działań, poprawić wydajność zespołów i zapewnić stałą jakość produktów. To nie tylko zestaw wytycznych, ale przede wszystkim sposób na uproszczenie codziennych operacji i eliminację błędów. W artykule przyjrzymy się, dlaczego standaryzacja w produkcji jest tak ważna, jakie narzędzia wspierają wdrożenie standaryzacji pracy oraz jak wpływa na sukces firmy.
Spis treści:
- Wprowadzenie do standaryzacji procesów pracy
- Kluczowe elementy standaryzacji procesów pracy
- Metody i narzędzia wspierające standaryzację
- Proces wdrażania standaryzacji w firmie produkcyjnej
- Zastosowanie standaryzacji w różnych obszarach firmy
- Korzyści i wyzwania związane ze standaryzacją
- Podsumowanie
- Odbierz za darmo poradnik: 4 sposoby na poprawienie komunikacji w firmie
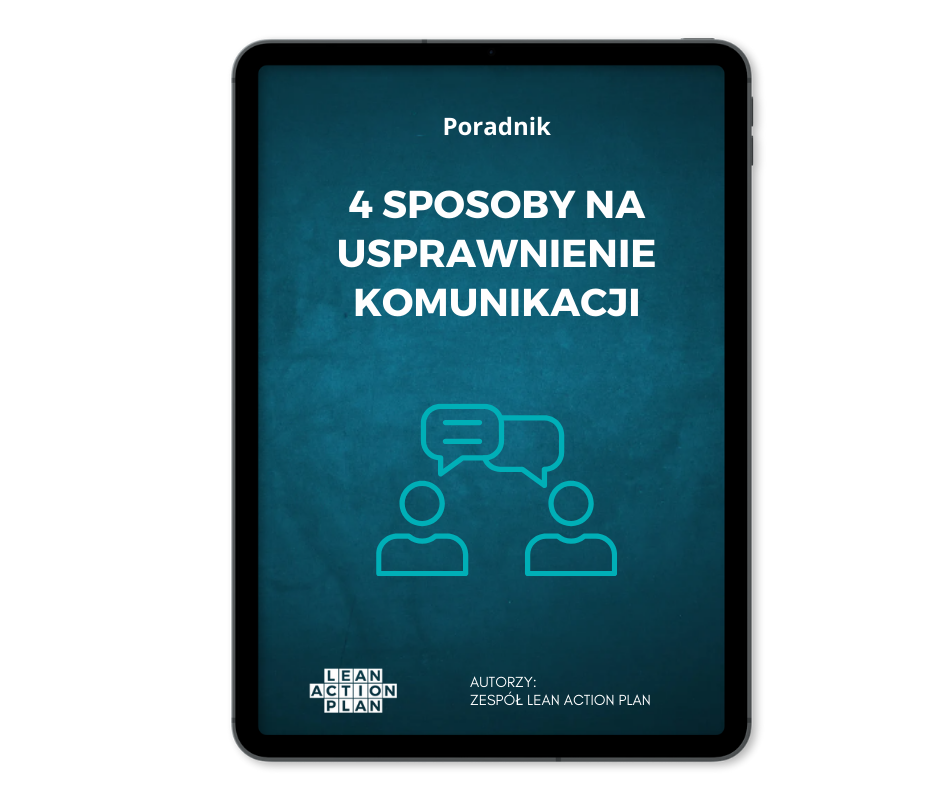
Wprowadzenie do standaryzacji procesów pracy
Standaryzacja procesów pracy to sposób na uporządkowanie działań w firmie, aby były one wykonywane w sposób jednolity i efektywny. Dzięki temu wszystkie zadania, niezależnie od tego, kto je realizuje, przebiegają w ten sam, sprawdzony sposób. W firmach produkcyjnych efektywna standaryzacja pracy jest szczególnie ważna, ponieważ wpływa na jakość produktów, wydajność pracy oraz bezpieczeństwo pracowników. Wdrażanie standaryzacji pracy pozwala unikać chaosu, błędów oraz marnotrawstwa czasu i zasobów.
Czym jest standaryzacja procesów pracy?
Standaryzacja procesów pracy to tworzenie szczegółowych instrukcji i wytycznych, które określają najlepszy sposób wykonywania konkretnych zadań. Dzięki temu pracownicy dokładnie wiedzą, jak powinien wyglądać każdy etap pracy. Standardy obejmują zarówno procedury produkcyjne, jak i działania wspierające, takie jak kontrola jakości czy obsługa maszyn. Głównym celem standaryzacji jest eliminacja różnic w sposobie pracy, co prowadzi do uzyskania powtarzalnych i przewidywalnych rezultatów.
Dlaczego standaryzacja jest kluczowa w firmach produkcyjnych?
Standaryzacja jest niezbędna w firmach produkcyjnych, ponieważ zapewnia stabilność i powtarzalność procesów. Dzięki temu jakość produktów pozostaje na stałym poziomie, niezależnie od zmiany pracowników lub warunków pracy. Standaryzacja pozwala także zidentyfikować i wyeliminować marnotrawstwo, co przekłada się na oszczędności czasu i zasobów. Poprawia także bezpieczeństwo pracy, ponieważ jasno określa procedury, które minimalizują ryzyko błędów i wypadków. Dodatkowo, standaryzacja ułatwia szkolenie nowych pracowników, którzy mogą szybko dostosować się do obowiązujących reguł.
Kluczowe elementy standaryzacji procesów pracy
Standaryzacja procesów pracy opiera się na kilku kluczowych elementach, które muszą być jasno określone i wdrożone. Pierwszym z nich jest praca standaryzowana, czyli określenie dokładnych kroków i sekwencji działań dla każdego stanowiska. Drugim ważnym elementem jest arkusz pracy standaryzowanej, który dokumentuje wszystkie etapy procesu, czasy wykonania poszczególnych zadań oraz narzędzia potrzebne do ich realizacji. Kolejnym kluczowym aspektem jest czas taktu, który wyznacza tempo produkcji w oparciu o zapotrzebowanie klienta. Wszystkie te elementy tworzą spójną strukturę, która pozwala na monitorowanie, analizowanie i doskonalenie procesów produkcyjnych, co prowadzi do zwiększenia efektywności pracy i pozwala na zwiększenie jakości produktów.
Praca standaryzowana – definicja i korzyści
Praca standaryzowana to określona i powtarzalna sekwencja działań, która pozwala osiągnąć optymalną wydajność na danym stanowisku pracy. W praktyce oznacza to, że każdy pracownik wykonuje zadania w ten sam sposób, korzystając z tych samych narzędzi i w ustalonym czasie. Jedną z głównych korzyści pracy standardowej jest minimalizacja błędów – standaryzacja eliminuje różnice w sposobach pracy i pozwala utrzymać wysoką jakość produktów. Kolejną zaletą jest zwiększenie wydajności, ponieważ procesy stają się bardziej uporządkowane i przewidywalne. Dodatkowo, praca standardowa ułatwia szkolenie nowych pracowników, którzy szybko przyswajają procedury i adaptują się do stanowiska pracy.
Arkusz pracy standaryzowanej jako narzędzie dokumentacji
Arkusz pracy standaryzowanej to narzędzie, które szczegółowo dokumentuje wszystkie kroki procesu produkcyjnego. Zawiera on informacje o czynnościach wykonywanych na stanowisku, czasie potrzebnym na realizację każdego zadania oraz wykorzystywanych narzędziach i materiałach. Dzięki temu arkusz stanowi punkt odniesienia dla pracowników oraz kadry zarządzającej. Jego głównym celem jest uproszczenie pracy i umożliwienie stałego monitorowania procesów. Arkusz pracy standaryzowanej pozwala także na identyfikację nieefektywności, takich jak zbędne kroki czy marnotrawstwo czasu. Regularna aktualizacja arkusza zapewnia, że procesy są dostosowane do zmieniających się warunków i wymagań produkcji, co zapewnia wzrost wydajności i zwiększenie jakości produktów.
Metody i narzędzia wspierające dyscyplinę na produkcji
Dyscyplina w produkcji to nie tylko przestrzeganie zasad, ale także stałe monitorowanie i poprawa standardów pracy. Aby efektywnie wspierać dyscyplinę, firmy produkcyjne korzystają z różnych metod i narzędzi. Kluczowe znaczenie mają systematyczne podejścia, takie jak metoda 8D, które pozwalają na szybkie reagowanie na problemy i eliminowanie ich przyczyn. Monitoring wydajności wspiera kontrolę procesów w czasie rzeczywistym, pomagając w identyfikacji niezgodności i wdrożeniu działań naprawczych. Rozmowy dyscyplinujące, prowadzone w odpowiedni sposób, są narzędziem motywacyjnym i edukacyjnym, pomagającym utrzymać zaangażowanie i porządek w zespole. Stosowanie tych metod razem przyczynia się do stworzenia środowiska pracy opartego na odpowiedzialności, przejrzystości i efektywności.
Metoda 8D: Rozwiązywanie problemów i utrzymanie standardów
Metoda 8D (Eight Disciplines) to narzędzie wykorzystywane do rozwiązywania problemów i utrzymania standardów na produkcji. Skupia się na dokładnej analizie źródeł problemów oraz wprowadzeniu skutecznych działań zapobiegawczych. Proces 8D składa się z ośmiu etapów, od zidentyfikowania problemu i utworzenia zespołu, po wdrożenie korekt i analizę skuteczności działań. Dzięki tej metodzie organizacja może nie tylko poprawić dyscyplinę pracy, ale również zwiększyć zaangażowanie zespołu w utrzymanie wysokiej jakości. W firmach produkcyjnych metoda ta pomaga szybko reagować na odstępstwa od standardów i zapobiegać ich powtarzaniu, co wpływa na efektywność i bezpieczeństwo.
Monitoring wydajności: Jak identyfikować i eliminować problemy?
Monitoring wydajności to jedno z kluczowych narzędzi wspierających wzmacnianie dyscypliny pracy na produkcji. Polega na systematycznym śledzeniu wskaźników takich jak czas cyklu, liczba wyprodukowanych sztuk czy poziom odpadów. Dzięki nowoczesnym systemom, takim jak MES (Manufacturing Execution System), możliwe jest monitorowanie w czasie rzeczywistym, co pozwala szybko zidentyfikować obszary wymagające poprawy. Działania te pomagają utrzymać porządek i zapewnić zgodność z ustalonymi standardami. Regularne analizy danych umożliwiają pracodawcom identyfikację problemów, takich jak spadki wydajności wynikające z zaniedbań lub nieprzestrzegania procedur, i wdrożenie działań korygujących.
Rozmowa dyscyplinująca: Narzędzie do poprawy zachowań pracowników
Rozmowa dyscyplinująca jest jednym z podstawowych narzędzi wykorzystywanych do utrzymania dyscypliny w miejscu pracy. Jej celem nie jest karanie, lecz zmotywowanie pracownika do poprawy. Rozmowa powinna być prowadzona w sposób konstruktywny, z poszanowaniem godności pracownika, ale też z jasnym określeniem oczekiwań i konsekwencji w przypadku dalszych naruszeń. Ważne jest, aby podczas rozmowy wyjaśnić, jakie działania są niewłaściwe, i zaproponować konkretne rozwiązania, które pomogą uniknąć podobnych sytuacji w przyszłości. W firmach produkcyjnych, gdzie współpraca zespołowa i terminowość są kluczowe, takie podejście może poprawić morale i zachęcić pracowników do większego zaangażowania w swoje obowiązki – to ważne plusy tej metody zarządzania dyscypliną.
Czas taktu – jak wpływa na standaryzację procesów?
Czas taktu to kluczowy wskaźnik w standaryzacji procesów, który określa tempo produkcji potrzebne do zaspokojenia zapotrzebowania klienta. W praktyce oznacza to, że każda operacja produkcyjna musi zostać wykonana w określonym czasie, aby cały proces przebiegał płynnie i zgodnie z harmonogramem. Czas taktu wpływa na organizację pracy, ponieważ pozwala zoptymalizować obciążenie stanowisk i unikać przestojów. Jest również niezwykle ważny dla równoważenia linii produkcyjnej – dostosowanie tempa pracy do czasu taktu minimalizuje nadprodukcję i marnotrawstwo zasobów. Dzięki standaryzacji opartej na czasie taktu, firmy produkcyjne mogą osiągnąć wyższą efektywność oraz elastyczność w dostosowywaniu się do zmieniającego się popytu.

Metody i narzędzia wspierające standaryzację
Lean Management to podejście, które koncentruje się na eliminacji marnotrawstwa oraz usprawnieniu procesów w celu maksymalizacji wartości dla klienta. W kontekście standaryzacji, Lean Management stanowi fundament, ponieważ opiera się na ciągłym doskonaleniu i optymalizacji pracy. Dzięki narzędziom takim jak mapowanie procesów, analiza przepływu pracy czy identyfikacja wąskich gardeł, możliwe jest określenie najbardziej efektywnych sposobów realizacji zadań. Lean promuje także zaangażowanie pracowników w tworzenie i wdrażanie standardów, co zwiększa ich odpowiedzialność za jakość i efektywność pracy. Wdrożenie zasad Lean Management pozwala firmom produkcyjnym na osiągnięcie stabilnych, przewidywalnych procesów, które można monitorować i usprawniać na bieżąco.
Metoda 5S – organizacja miejsca pracy
Metoda 5S to jedno z kluczowych narzędzi wspierających standaryzację w firmach produkcyjnych, które skupia się na organizacji i utrzymaniu porządku w miejscu pracy. Pięć kroków 5S to: Seiri (Sortowanie), Seiton (Systematyka), Seiso (Sprzątanie), Seiketsu (Standaryzacja) oraz Shitsuke (Samodyscyplina). Wdrożenie 5S pozwala na eliminację zbędnych elementów, lepsze rozmieszczenie narzędzi i materiałów oraz utrzymanie czystości i porządku. Dzięki temu praca staje się bardziej efektywna, a ryzyko błędów i wypadków zostaje zminimalizowane. Standaryzacja oparta na metodzie 5S wspiera stałe utrzymanie wysokiego poziomu organizacji oraz ułatwia wprowadzanie usprawnień, które przekładają się na wydajność całego zakładu produkcyjnego. Aby utrzymać efekty 5S, wprowadź regularne audyty – pomoże w tym aplikacja do audytów 5s!
Metoda SIPOC – analiza procesów przed standaryzacją
Metoda SIPOC to narzędzie służące do analizy i dokumentowania procesów, które jest szczególnie przydatne przed wdrożeniem standaryzacji. Skrót SIPOC odnosi się do pięciu kluczowych elementów: Supplier (Dostawca), Input (Wejście), Process (Proces), Output (Wyjście) oraz Customer (Klient). Dzięki tej metodzie można dokładnie określić przebieg danego procesu, zidentyfikować kluczowe punkty oraz określić oczekiwania klienta. SIPOC pomaga firmom produkcyjnym zrozumieć, gdzie występują nieefektywności, jakie są źródła problemów i co można poprawić. Dzięki szczegółowej analizie możliwe jest lepsze przygotowanie procesów do standaryzacji, co w efekcie prowadzi do usprawnienia pracy oraz zwiększenia jakości i wydajności produkcji.
Standard Operating Procedure (SOP) – tworzenie i wdrażanie
Standard Operating Procedure (SOP) to szczegółowa instrukcja, która opisuje, jak dokładnie powinny być wykonywane poszczególne zadania na danym stanowisku pracy. SOP pełni kluczową rolę w standaryzacji procesów, ponieważ zapewnia spójność, powtarzalność i wysoką jakość pracy. Tworzenie SOP zaczyna się od analizy procesu, identyfikacji kluczowych kroków oraz opracowania szczegółowych wytycznych. Następnie dokument jest testowany i wdrażany, a pracownicy są szkoleni z jego zastosowania. Dzięki SOP każdy pracownik wie, co ma robić i w jaki sposób, co eliminuje niejasności i błędy. Standaryzacja poprzez SOP pozwala firmom produkcyjnym na łatwiejsze wdrażanie nowych pracowników, kontrolę jakości pracy oraz szybkie reagowanie na zmiany i problemy w procesach.
Proces wdrażania standaryzacji w firmie produkcyjnej
Wdrożenie standaryzacji w firmie produkcyjnej to proces, który wymaga przemyślanego podejścia i zaangażowania wszystkich poziomów organizacji. Pierwszym krokiem jest analiza obecnych procesów oraz zidentyfikowanie obszarów, które wymagają usprawnienia. Następnie należy opracować jasne i czytelne standardy dla każdego etapu pracy. Wdrożenie obejmuje szkolenie pracowników, testowanie nowych standardów oraz monitorowanie ich skuteczności. Kluczowe jest również uzyskanie akceptacji zespołu, ponieważ zaangażowani pracownicy łatwiej przestrzegają nowych wytycznych. Proces wdrażania standaryzacji powinien być traktowany jako ciągły cykl doskonalenia, gdzie standardy są regularnie aktualizowane w miarę rozwoju firmy i zmieniających się potrzeb produkcji.
Etapy wdrażania standaryzacji procesów
Proces standaryzacji składa się z kilku kluczowych etapów, które krok po kroku prowadzą do uporządkowania pracy. Pierwszym etapem jest analiza obecnego stanu procesów, aby zrozumieć, jakie działania są wykonywane i gdzie występują nieefektywności. Następnie określa się standardowe procedury pracy, które są łatwe do wdrożenia i zrozumienia przez pracowników. Kolejny krok to szkolenie zespołu oraz wdrażanie wypracowanych standardów w praktyce. Ważnym elementem jest testowanie nowych procedur oraz zbieranie informacji zwrotnych od pracowników, aby upewnić się, że standardy działają zgodnie z założeniami. Ostatnim etapem jest monitorowanie i aktualizacja standardów, aby stale odpowiadały realiom pracy i potrzebom firmy.
Rola wizualizacji procesów w standaryzacji
Wizualizacja procesów odgrywa kluczową rolę w skutecznej standaryzacji, ponieważ ułatwia zrozumienie złożonych procedur i sprawia, że praca staje się bardziej przejrzysta. Dzięki wykorzystaniu narzędzi takich jak schematy, tablice informacyjne czy diagramy, pracownicy mogą szybko zorientować się, jakie kroki muszą wykonać i w jakiej kolejności. Wizualizacja pozwala również na identyfikację nieefektywności, takich jak marnowanie czasu czy niepotrzebne ruchy w procesie pracy. W firmach produkcyjnych często stosuje się tablice Kanban lub schematy przepływu pracy, które pokazują postępy i usprawnienia. Jasna i czytelna wizualizacja eliminuje nieporozumienia oraz pomaga w utrzymaniu standardów na wysokim poziomie, co przekłada się na lepszą organizację i efektywność.
Audyt procesów – ocena skuteczności i zgodności ze standardami
Audyt procesów to niezbędny krok w ocenie skuteczności wdrożonych standardów. Polega na regularnej analizie, czy procesy są realizowane zgodnie z ustalonymi wytycznymi oraz czy przynoszą oczekiwane rezultaty. Audyt może być wykonywany przez wewnętrznych specjalistów lub zewnętrznych audytorów, którzy obiektywnie oceniają zgodność z procedurami. Podczas audytu sprawdzane są kluczowe wskaźniki wydajności (KPI), jakość pracy oraz zgodność z wyznaczonymi standardami. W przypadku wykrycia odchyleń lub problemów, wprowadza się działania korygujące, które mają na celu poprawę procesów. Regularne audyty zapewniają ciągłe doskonalenie oraz utrzymanie wysokiego poziomu standaryzacji, co przekłada się na lepszą jakość produkcji i wyższą efektywność pracy.
Zastosowanie standaryzacji w różnych obszarach firmy
Standaryzacja w produkcji – zwiększenie wydajności i jakości
W produkcji standaryzacja pozwala na wypracowanie spójnych procesów, które można powtarzać z dużą dokładnością. Dzięki temu pracownicy wykonują swoje zadania według ustalonych procedur, co minimalizuje ryzyko błędów. Standaryzacja ułatwia także szkolenie nowych pracowników, ponieważ jasno określa najlepsze praktyki i oczekiwane standardy. Wynikiem jest wyższa jakość produktów, lepsze zarządzanie czasem pracy oraz ograniczenie marnotrawstwa surowców. Przykładem zastosowania może być praca standaryzowana z wykorzystaniem arkuszy pracy, które szczegółowo opisują każdą czynność na stanowisku produkcyjnym.
Standaryzacja w logistyce – optymalizacja transportu i redukcja kosztów
Logistyka w firmie produkcyjnej wymaga precyzyjnego planowania, aby produkty trafiały do klientów na czas, a surowce były dostarczane w odpowiedniej ilości. Standaryzacja w tym obszarze pomaga ujednolicić procesy związane z transportem, zarządzaniem magazynem czy kompletowaniem zamówień. Na przykład wdrożenie ujednoliconych procedur załadunku i rozładunku skraca czas operacji i zmniejsza ryzyko uszkodzenia towarów. Dzięki standaryzacji firmy mogą też efektywniej wykorzystywać swoje zasoby logistyczne, co bezpośrednio przekłada się na redukcję kosztów transportu i zwiększenie satysfakcji klientów.
Standaryzacja w IT – ujednolicanie rozwiązań technologicznych
W dzisiejszych czasach firmy produkcyjne coraz częściej korzystają z zaawansowanych systemów IT, takich jak ERP czy MES. Standaryzacja w IT polega na ujednoliceniu narzędzi technologicznych i procesów ich obsługi w całej firmie. Dzięki temu pracownicy mają dostęp do tych samych systemów, co ułatwia współpracę między działami i eliminuje problemy związane z kompatybilnością różnych rozwiązań. Przykładowo, ustandaryzowanie procedur korzystania z systemów magazynowych umożliwia szybsze wyszukiwanie informacji i lepsze zarządzanie zapasami. Standaryzacja w IT to także większe bezpieczeństwo danych oraz łatwiejsze wprowadzanie nowych technologii.
Standaryzacja w HR – zarządzanie personelem i szkolenia
Dział HR również może skorzystać ze standaryzacji, zwłaszcza w obszarze rekrutacji, wdrożeń nowych pracowników i prowadzenia szkoleń. Standardowe procedury pomagają ujednolicić procesy rekrutacyjne, co zapewnia równy dostęp kandydatów do tych samych kryteriów oceny. W kontekście szkoleń standaryzacja umożliwia tworzenie powtarzalnych programów edukacyjnych, które przygotowują pracowników do pracy zgodnie z ustalonymi standardami. Dodatkowo, ujednolicenie systemów oceny i awansów w firmie sprawia, że zarządzanie personelem staje się bardziej przejrzyste i sprawiedliwe. To wszystko buduje zaufanie w zespole i wzmacnia kulturę organizacyjną.
Korzyści i wyzwania związane ze standaryzacją
Standaryzacja procesów pracy to strategia, która pozwala firmom na ujednolicenie sposobów wykonywania zadań, co prowadzi do lepszej organizacji pracy i przewidywalności wyników. Dzięki temu przedsiębiorstwa mogą działać efektywniej, redukując straty czasu i zasobów. Kluczowym elementem standaryzacji jest stworzenie jasnych wytycznych, które ułatwiają pracownikom zrozumienie swoich obowiązków oraz eliminują chaos w procesach. Jednak proces ten wiąże się również z wyzwaniami – wymaga zaangażowania, czasu i odpowiedniego podejścia do wprowadzania zmian. Standaryzacja, jeśli jest odpowiednio przeprowadzona, może stać się fundamentem dla dalszego rozwoju i optymalizacji działań w firmie.
Korzyści ze standaryzacji procesów pracy
Standaryzacja procesów pracy przynosi firmom produkcyjnym wiele korzyści. Jednym z największych atutów jest poprawa wydajności – dzięki jasno określonym procedurom pracownicy wiedzą, co i w jaki sposób mają robić, co eliminuje zbędne działania i przyspiesza realizację zadań.
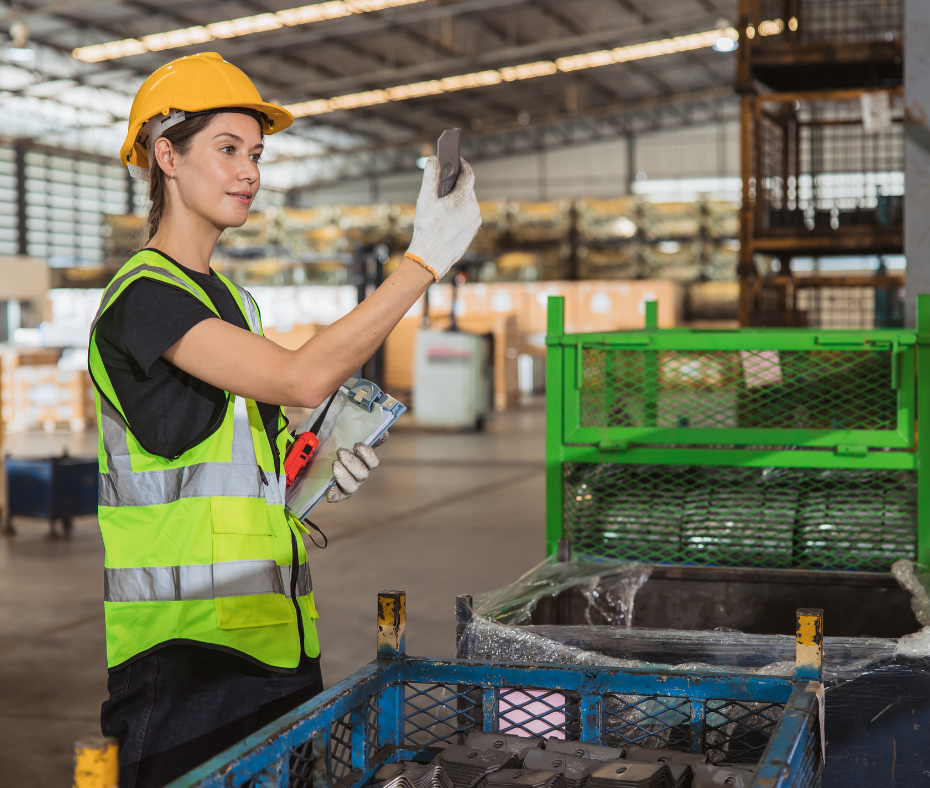
Standaryzacja zwiększa także jakość produktów, ponieważ pozwala na unikanie błędów wynikających z niejasnych lub różniących się praktyk. Dodatkowo, standaryzacja ułatwia szkolenie nowych pracowników, którzy mogą szybko wdrożyć się w obowiązki, korzystając z gotowych instrukcji i standardów. Kolejnym plusem jest lepsza kontrola nad procesami, co umożliwia szybsze reagowanie na ewentualne problemy i wdrażanie działań naprawczych.
Wyzwania i przeszkody w procesie standaryzacji
Mimo licznych zalet, standaryzacja procesów pracy wiąże się także z wyzwaniami. Jednym z głównych problemów jest opór pracowników przed zmianami – wprowadzenie nowych standardów często oznacza konieczność zmiany dotychczasowych nawyków, co może budzić niechęć. Kolejnym wyzwaniem jest różnorodność procesów w firmie – niektóre działania mogą być trudne do ujednolicenia ze względu na ich specyfikę lub indywidualne potrzeby klientów. Dodatkowo, standaryzacja wymaga czasu i zaangażowania – niezbędne jest dokładne przeanalizowanie obecnych procesów, opracowanie standardów i przeszkolenie zespołu. Bez odpowiedniego wsparcia zarządu oraz zaangażowania pracowników, wdrażanie standardów może zakończyć się niepowodzeniem.
Jak unikać problemów podczas wdrażania standardów?
Aby standaryzacja procesów przebiegła pomyślnie, warto wcześniej zaplanować cały proces i zadbać o komunikację w zespole. Kluczowe jest zaangażowanie pracowników – włączenie ich w tworzenie standardów sprawia, że czują się częścią procesu, co zmniejsza opór przed zmianami. Ważne jest także, aby odpowiednio przeszkolony zespół mógł wdrażać nowe zasady z pełnym zrozumieniem. Dobrym rozwiązaniem jest testowanie standardów na mniejszą skalę przed ich wdrożeniem w całej firmie – pozwala to zidentyfikować ewentualne problemy i je skorygować. Regularne monitorowanie efektów oraz zbieranie feedbacku od pracowników umożliwia wprowadzanie ulepszeń, co zwiększa szanse na sukces standaryzacji.
Podsumowanie
Standaryzacja procesów pracy jest kluczowym elementem efektywnego zarządzania w firmach, szczególnie w branży produkcyjnej. Poprzez standaryzację procesów organizacje mogą zwiększyć wydajność, poprawić jakość produktów i usług, a także zmniejszyć straty i koszty operacyjne. Standaryzacja to nie tylko dokumenty i procedury, ale przede wszystkim sposób na ujednolicenie działań i budowanie przewidywalności w codziennej pracy. Chociaż wdrożenie standardów może wiązać się z wyzwaniami, takimi jak opór pracowników czy potrzeba dostosowania procesów, korzyści zdecydowanie przeważają nad trudnościami. Zastosowanie takich metod jak 5S, SOP czy wizualizacja procesów pomaga firmom skutecznie wprowadzać zmiany i utrzymywać wysoki poziom organizacji. Warto pamiętać, że standaryzacja nie jest celem samym w sobie, ale narzędziem wspierającym ciągłe doskonalenie i budowanie przewagi konkurencyjnej.
W usprawnianiu produkcji potrzebne są konieczne narzędzia – jednym z przydatnych jest aplikacja ZaPro. To rozwiązanie stworzone na potrzeby i specyfikę branży produkcyjnej, pozwala więc na kontrolę przekroju procesów produkcyjnych.