Layout – ustawienie maszyn na hali produkcyjnej
Layout to widok z lotu ptaka na cały obszar lub fragment pomieszczenia z umiejscowieniem wszystkich elementów. W kontekście zarządzania produkcją obszarem ukazanym na layoucie jest hala produkcyjna, a najistotniejszymi elementami z punktu widzenia Lean są maszyny i stanowiska robocze. W tym artykule rozważamy, po co tworzyć layout i go aktualizować, a także jak wygląda ten proces.
Spis treści:
Czym jest Layout w firmie produkcyjnej?
Poszukując najprostszych odpowiedzi mianem layout’u określa się graficzny plan ustawienia maszyn na hali produkcyjnej. Taki układ przestrzenny ukazany z lotu ptaka powinien wskazywać nie tylko rysunki lub symbole urządzeń, ale także kluczowe informacje dotyczące: dróg transportowych, pomocniczego osprzętu jak np.: suwnice, przyłączy mediów, pól odkładczych, kwestii BHP – czyli wyjść ewakuacyjnych i miejsc zbiórek, a także przepływu materiałów.
Firmy planując zakup dodatkowych maszyn, często poświęcają niewystarczającą ilość czasu na rozplanowanie ich rozmieszczenia, dodatkowo nie kierując się przy tym zasadami Lean. Nie traktują dużych odległości pomiędzy stanowiskami jako problemu oraz nie zwracają uwagi na ciągłość przepływu materiału. W konsekwencji na hali produkcyjnej powstają marnotrawstwa w postaci nadmiernego transportu, zapasów międzyoperacyjnych czy zbędnych ruchów poprzez redukcje dostępnej przestrzeni, zarówno w skali makro jak i mikro.
Layout w skali makro i mikro
Layout w skali makro – to odzwierciedlenie ułożenia wszystkich elementów na całej hali produkcyjnej. Analizując layout w skali makro, skupiamy się na zagwarantowaniu ciągłego przepływu, tworząc liniowe i gniazdowe formy organizacji stanowisk roboczych, redukując odległości pomiędzy stanowiskami kooperującymi, tym samym zmniejszając czas operacji transportowych.
Layout w skali mikro – to layout poszczególnych stanowisk roboczych lub obszarów, wraz ze wszystkimi elementami niezbędnymi do wykonywania pracy. Mówimy tu o całym otoczeniu maszyny i przestrzeni roboczej operatora wraz ze sposobem poruszania się po nim. W związku z tym oprócz zapewnienia swobodnego przepływu czynników produkcji na stanowisku, należy zadbać również o ergonomiczne warunki pracy. Optymalizację w skali mikro możemy osiągnąć stosując narzędzia 5S.
Chcesz sprawnie przeprowadzać audyty 5s w swojej firmie? Sprawdź naszą aplikację do audytów 5s.
Po co tworzyć layout?
Poniższe punkty to oczywiście tylko część danych, które jak się okazuje są niezwykle istotne dla realizacji strategii przedsiębiorstwa. Dlaczego? Posiadanie rzetelnie przygotowanej i przede wszystkim aktualnej „mapy”, a także chęć jej doskonalenia, pozwala na:
- elastyczne reagowanie przy wprowadzaniu zmian w procesach oraz możliwość przewidzenia ich konsekwencji,
- identyfikację nieprzemyślanych, źle zorganizowanych transportów oraz ruchów między stanowiskami,
- pracę nad zachowaniem ciągłości przepływu, eliminacją wąskich gardeł oraz sprawną dystrybucją informacji,
- poprawę komunikacji,
- poszukiwanie kierunków rozwoju przedsiębiorstwa poprzez bardziej efektywną adaptację przestrzeni i możliwość inwestowania w powiększenie parku maszynowego,
- dostosowanie przestrzeni składowania oraz magazynów do faktycznych potrzeb produkcyjnych,
- organizowania procesów ze świadomym podziałem na kluczowe grupy produktowe.
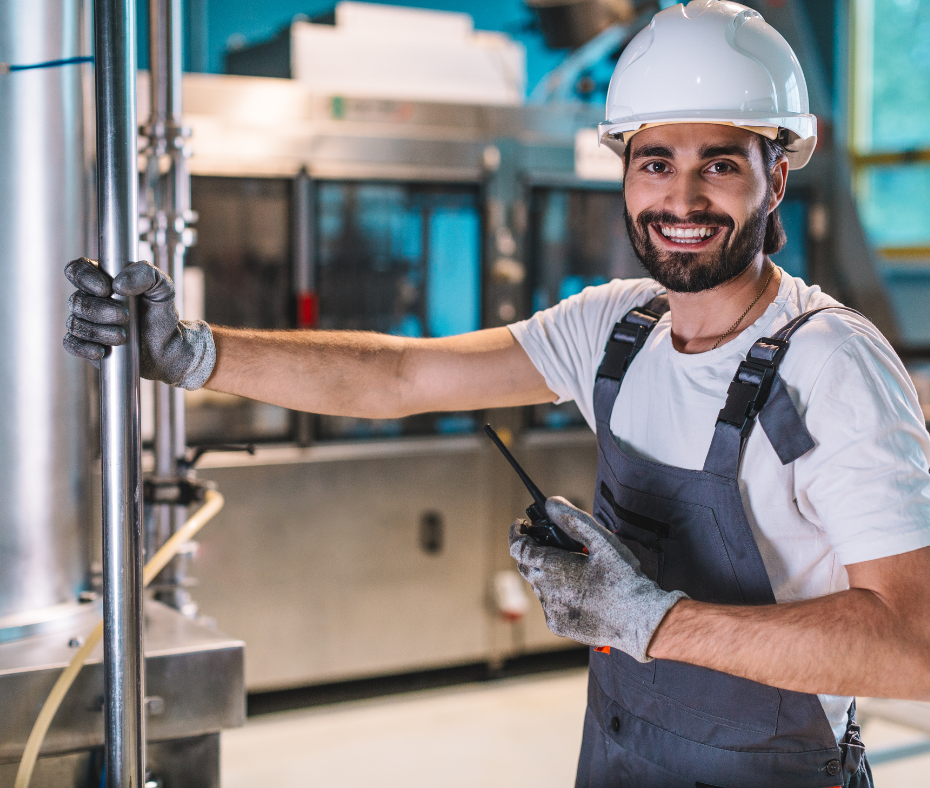
Bez tej wiedzy organizacji grozi stagnacja. Layout eliminuje ryzyko przypadkowego rozmieszczania maszyn, a w dalszej konsekwencji strat czasu, energii oraz zasobów, których niedostrzeżenie w skali lat może przyczynić się do utraty przewagi konkurencyjnej.
Tworzenie layout’u pomaga znaleźć odpowiedzi na wiele pytań. Weźmy na tapet jeden prosty przykład. Firma X zajmuje się przetwarzaniem płyt plexi, pierwsze gniazdo to rozkrój, następnie wykańczanie krawędzi, dalej otworowanie i kolejne działy. Zakupiono nową krawędziarkę, która została umieszczona w dobudówce. Trasa między działem rozkroju, a nową maszyną wynosi 100 metrów, a dalsza droga pod wiertarkę wynosi 80 metrów. Każda taka trasa zajmuje logistykowi wewnętrznemu około 10 minut, uwzględniając załadunek oraz rozładunek pojedynczych sztuk plexi. Aby zredukować ilość tras przy stanowiskach zostały utworzone strefy odkładcze, dające możliwość kumulowania dostaw międzyoperacyjnych. W takim przypadku logistyk wykonuje do 15 tras na zmianę przewożąc załadowane stojaki, co zajmuje mu około 2,5 godziny dziennie. Koszt roboczogodziny w zakładzie wynosi 40 zł brutto brutto, upraszczając pominiemy tutaj kwestię eksploatacji wózka widłowego oraz zużycia paliwa. Umieszczenie nowej krawędziarki w miejscu starej, wiązałoby się z koniecznością demontażu niewykorzystywanego urządzenia, za co zewnętrzna firma zażyczyła sobie 15 000 zł netto. W efekcie trasa między rozkrojem, a krawędziarką skróciłaby się do 15 metrów, a między działem otworowania do 10 metrów, uwzględniając, że między stanowiskami znajdowałyby się pola odkładcze. Co się bardziej opłaca?
- Jednorazowy koszt demontażu 15 000 zł
- Koszt utraconych możliwości produkcyjnych w dniach demontażu
- Skrócenie trasy z 180 metrów do 25 metrów
- Uwolnienie części przestrzeni spod pól odkładczych
kontra
- Dzienna praca Logistyka : 2,5h x 2 zmiany x 40 zł (roboczogodzina) = 200 zł
- W ciągu miesiąca (20 dni roboczych) = 4 000 zł
- W ciągu roku (240 dni roboczych) = 48 000 zł
Co ciekawe, ten przykład wcale nie jest przejaskrawiony. Takie sytuacje się zdarzają. A analiza layout’u i jego bieżąca aktualizacja pozwala na podjęcie słusznej, miarodajnej decyzji. W jakich sytuacjach przyda się w takim razie jego modyfikacja?
Sprawdź odcinek podcastu Produkcja bez chaosu, w którym rozmawiamy o tym, jak istotny jest odpowiedni layout!
Zobacz przykłady jak możesz wdrożyć u siebie nowy Layout
Kiedy zmienia się layout?
Kiedy zmienia się layout?
Zanim jeszcze rozstrzygniemy wspólnie okoliczności wprowadzania zmian do layout’u, warto podkreślić, że to nie jest projekt, który się wykonuje i odkłada na półkę. Jest to proces, powtarzalny, regularny, który wspomaga podejmowanie decyzji. Powinien on zostać uruchomiony w przypadku:
- Zakupienia nowej maszyny,
- Budowy nowej hali,
- Przeprowadzki do innego miejsca,
- Wdrożenia nowego produktu,
- Wzrostu produkcji,
- Spadku produkcji oraz wycofaniu części produktów,
- Optymalizacji przepływu.
Podczas realizacji drugiego oraz trzeciego scenariusza – rozpoczęcia projektowania „od zera”, będziesz musiał się do tego odpowiednio przygotować. Dlatego zachęcam Cię do zapoznania się z kilkoma wskazówkami Jak przygotować firmę do przeprowadzki do nowej hali produkcyjnej.
Trzymając się natomiast reorganizacji już istniejącej hali, o tym, że daną przestrzeń należy, bądź można zoptymalizować, będą wskazywać Ci pewne oznaki. Czy jesteś w stanie je zidentyfikować w swoim zakładzie?
- Zastawione drogi transportowe,
- Zbyt szerokie lub zbyt wąskie trasy,
- Zbyt długie trasy transportowe,
- Wysoki poziom zalegających zapasów międzyoperacyjnych,
- „Celowe” składowanie rzadko wykorzystywanych części i komponentów na hali, a nie w magazynie,
- Brak miejsca na ustawienie nowych maszyn oraz urządzeń,
- Niewykorzystana przestrzeń (w tym zbyt duże pola odkładcze),
- Duża liczba urządzeń transportowych, mimo niskiego poziomu ich wykorzystania,
- Za mała lub zbyt duża powierzchnia magazynowa,
- „Rozrzucone” procesy, skomplikowany przepływ, brak płynności
- Przestarzały sprzęt o wysokiej awaryjności,
- Brak lub niedostosowana automatyzacja.
Jeżeli w tej checkliście zaznaczyłeś kilka razy „TAK” to znaczy, że Wasz zakład prosi się o wprowadzenie pewnych modyfikacji.
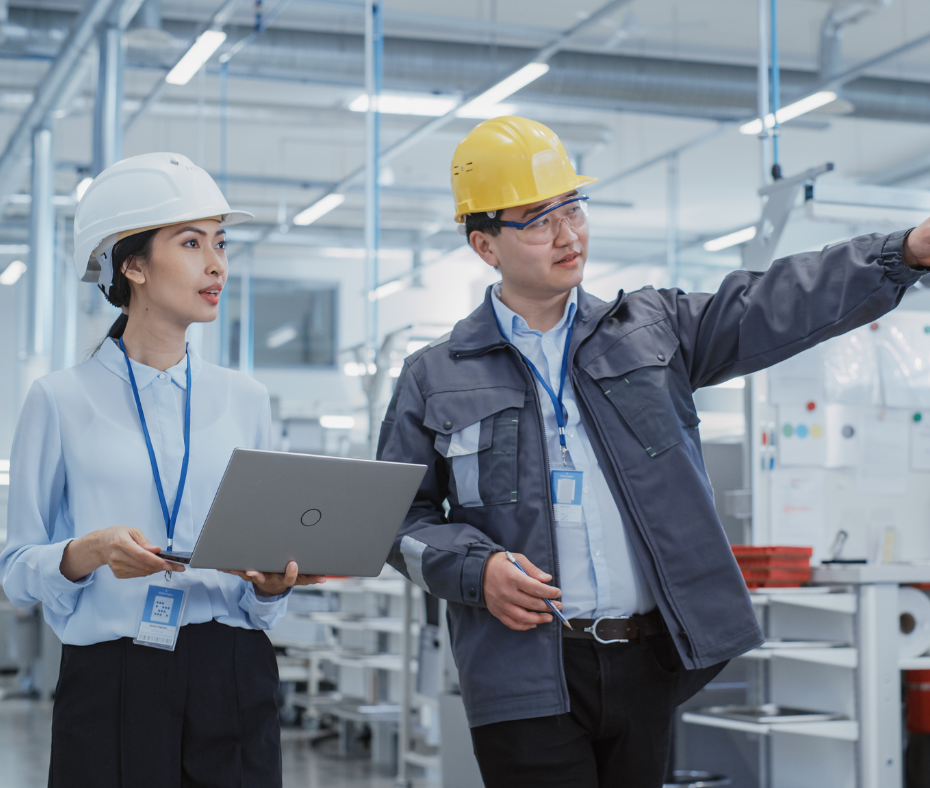
Fazy przygotowania i wdrożenia layout’u
Fazy przygotowania i wdrożenia layout’u
Nie sztuką jest pozmieniać symbole i figury na rysunku. Ale wiadomo też, że taka praca po łebkach nie przyniesie pożądanego efektu. Całe przedsięwzięcie należy odpowiednio zaplanować przechodząc przez etapy analizy danych wejściowych, wstępnej alokacji, szczegółowego opracowania layout’u, aż po wdrażanie zmian.
W pierwszej fazie mamy do czynienia ze studium badawczym uwzględniającym gromadzenie oraz analizę danych oraz interpretację potrzeb. Potrzebna jest tu wiedza na temat:
- Lokalizacji,
- Profilu produkcyjnego,
- Wielkości zatrudnienia,
- Ewidencji maszyn,
- Usystematyzowania sekwencji operacji, ich czasów, a także wydajności,
- Wielkości partii produkcyjnych,
- Norm produkcyjnych,
- Wykorzystywanych surowców oraz materiałów,
- Popytu na poszczególne rodziny produktowe,
- Logistyki wewnętrznej,
- Ograniczeń technicznych na hali produkcyjnej,
- A także relacji z otoczeniem zewnętrznym: system dostaw, system wysyłek, sprzedaż.
Druga faza to praca koncepcyjna. W tym momencie mamy do czynienia z ogólnym layout’em, gdzie należy określić przepływ materiałów, logikę procesów oraz wzajemne powiązania.
Dalej idąc, opracowując szczegółowy layout potrzebne są już precyzyjne dane na temat:
- Maszyn – ich nazewnictwa, ilości, gabarytów oraz potrzebnych wspomagających instalacji,
- Wymogów instalacji mediów – prąd, woda, gaz, wentylacja, sprzężone powietrze itd.,
- Warunków otoczenia produkcyjnego – temperatura, wilgotność,
- Wielkości pól odkładczych – pod dostawy surowców oraz ewentualne zapasy międzyoperacyjne,
- Szerokości dróg transportowych – uwzględniając ruch pieszych, a także pojazdów transportowych,
- Układu pomieszczeń socjalnych oraz komórek pomocniczych jak kontrola jakości, utrzymanie ruchu.

Towarzyszącym procesem dla projektowania layout’u jest analiza możliwości relokacji poszczególnych gniazd produkcyjnych, a także szacowanie budżetu. Bez zabezpieczenia finansów na poczet tej inwestycji nie ma mowy o jakiejkolwiek reorganizacji planu zagospodarowania. Już na początku, na etapie szacowania, a następnie podczas weryfikacji należy uwzględnić ewentualność:
- Skorzystania z firm doradczych w ramach opracowania layout’u oraz wspomagania podczas wdrożenia zmian,
- Skorzystania z usług zewnętrznych w zakresie transportu, demontażu oraz montażu maszyn,
- Wykonania prac remontowych na hali: poprawa, bądź dostosowanie posadzki, zmiana oświetlenia oraz przyłączy mediów, wykonanie dobudówki itd.
- Dostosowania infrastruktury pomocniczej: regały, stoły narzędziowe, stojaki itd. – tutaj w grę w zależności od potrzeby wchodzi zakup lub relokacja dostępnych zasobów,
- Tymczasowego wyłączenia etapów produkcyjnych (obniżenie możliwości produkcyjnych, zagospodarowanie czasu pracowników „o wolnych przebiegach”),
- Zakupu nowych maszyn oraz urządzeń.
Ostatnia faza wdrożenia powinna odbywać się w oparciu o szczegółowy plan uwzględniający terminy, odpowiedzialność konkretnych osób lub zespołów oraz poziom wydatków. W tym kroku konieczne jest dopełnienie wszelkich akceptacji, zgód formalnych oraz niezbędnych procedur do wykonania faktycznej zmiany. Niejednokrotnie będzie się to wiązało również z aranżacją finalnych odbiorów technicznych. Co więcej, jeżeli jest to możliwe, harmonogram rozpoczęcia prac warto skonfrontować z informacjami o sezonowości popytu, a także warunkami atmosferycznymi (pora roku), aby maksymalnie ograniczyć negatywny wpływ na możliwości produkcyjne.
Zmiana Layout’u to skończony projekt, ale wielozadaniowy. Skorzystaj z gotowego planu projektowego.
Wypełnij poniższy formularz i otrzymaj plik Excel.
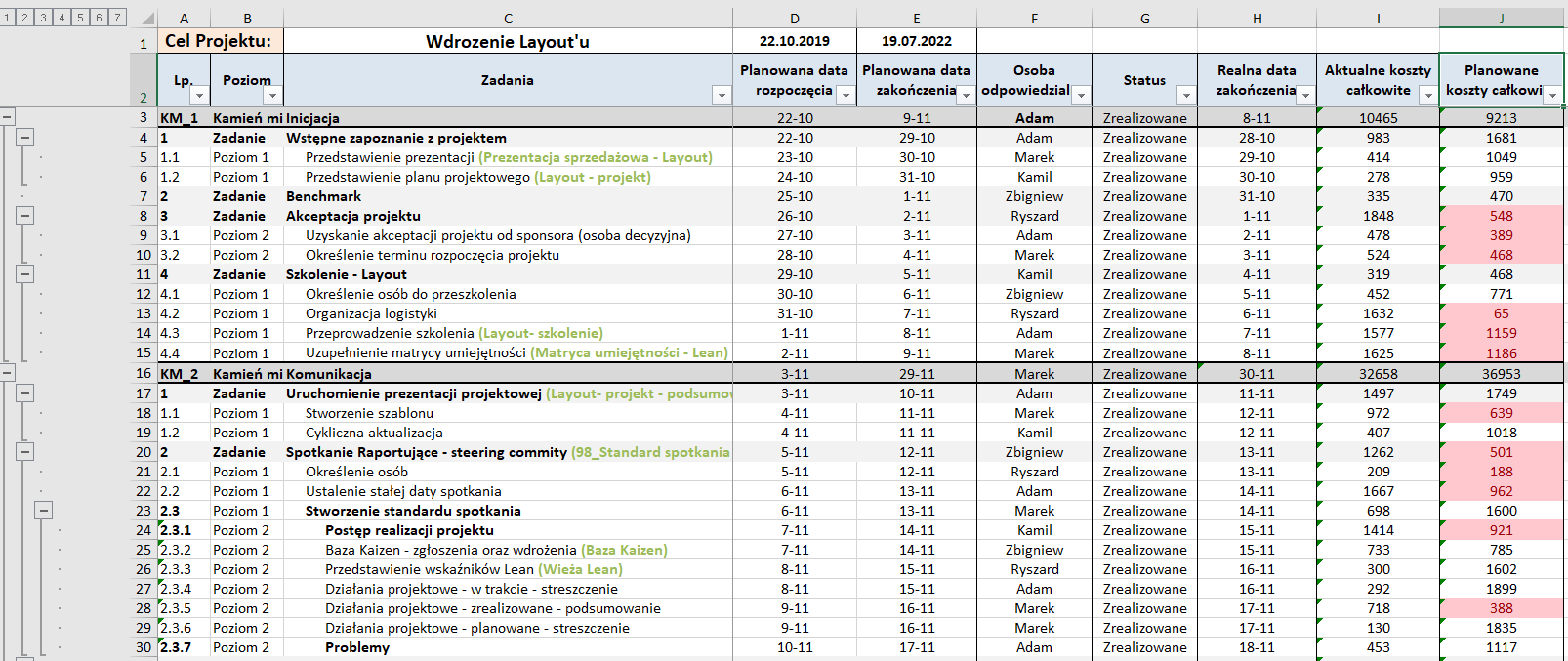
Korzyści ze zmiany ustawienia maszyn:
Skrócenie czasu produkcji
Skrócenie czasu oczekiwania operatora
Zmniejszenie czasu transportu
Zwiększenie dostępnego miejsca
Dowiedz się więcej o Warsztatach Layout, które realizujemy w siedzibie Twojej firmy!
W filmie opowiadam, jak wygląda proces warsztatów, na czym opiera się nasze podejście i co z tego wszystkiego wynika