Słownik pojęć
Lean Manufacturing
Lean Manufacturing
Słownik pojęć Lean to nic innego, jak kluczowe pojęcia, które pozwolą Ci lepiej orientować się w świecie Lean.
Wypełnij formularz i pobierz całe kompendium Leanowca
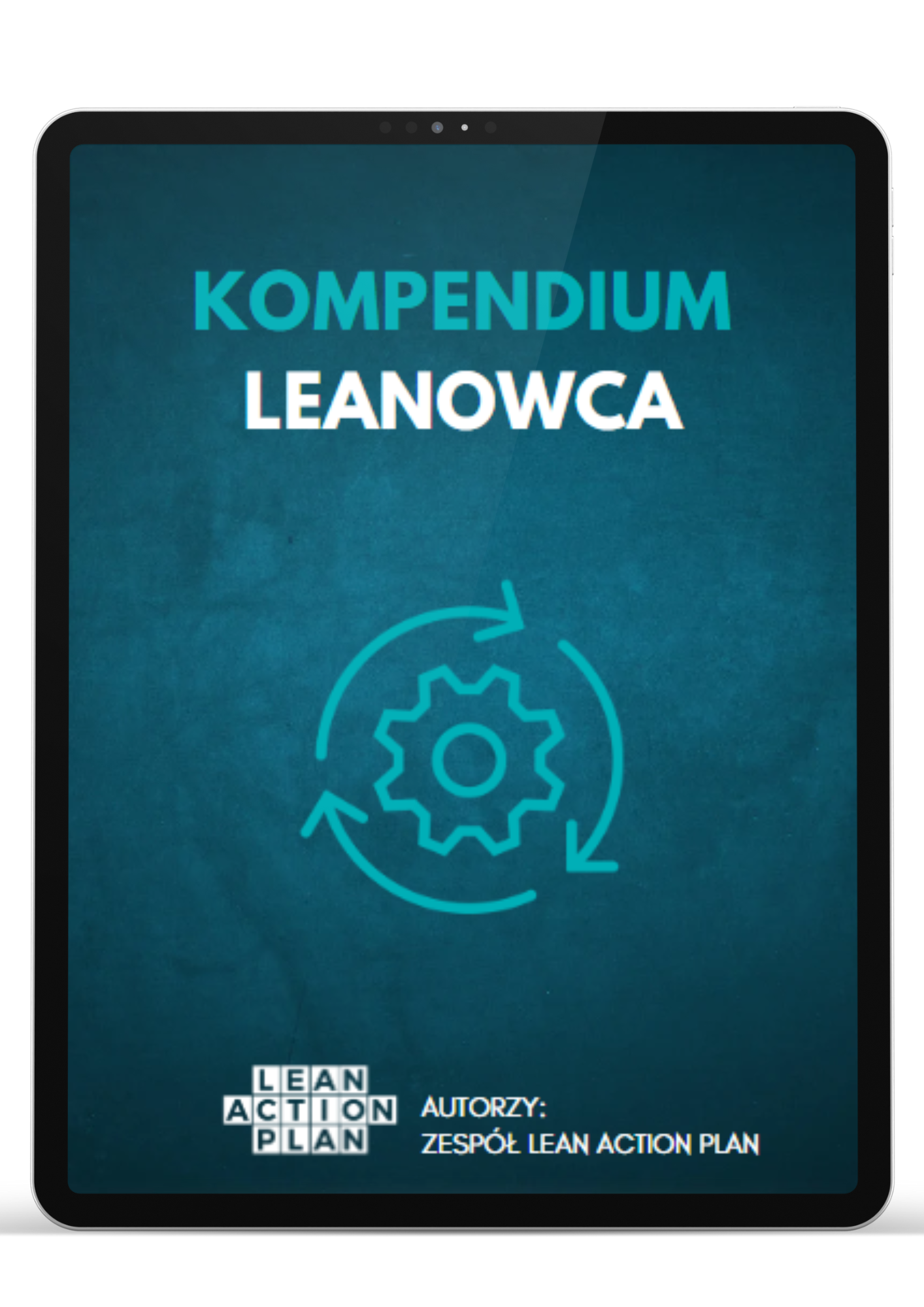
Lean Action Plan – firma konsultingowa w zakresie Lean i optymalizacji procesów produkcyjnych
Lean Manufacturing – „szczupła produkcja”, metodologia zarządzania produkcją oparta na dostarczaniu klientowi oczekiwanej przez niego wartości, eliminując wszelkiego rodzaju straty. Metodologia oparta na Systemie Produkcyjnym Toyoty (TPS).
TPS – Toyota Production System – system mający na celu eliminację strat i doskonalenie przepływu w celu skrócenia czasu od zamówienia klienta do dostarczenia produktu (Lead Time).
Lead Time – czas upływający od momentu złożenia zamówienia klienta do momentu dostarczenia gotowego produktu w odpowiedniej jakości.
Lean Management – „szczupłe zarządzanie”, rozszerzenie Lean Manufacturing na wszystkie szczeble przedsiębiorstwa i poza nie.
Just in Time – „dokładnie na czas” – dostarczanie do klienta oczekiwanego przez niego produktu, w odpowiednim czasie i ilości, w miejscu i jakości przy jak najniższych kosztach.
Klient – każda osoba oczekująca na efekt naszej pracy. Klient zewnętrzny – klient poza naszym przedsiębiorstwem. Klient wewnętrzny – klient w ramach firmy (np. kolejny proces, przełożony, pracownik)
Jidoka – „wbudowana jakość” – system mający zapewnić całkowitą kontrolę jakości w procesach poprzez eliminację możliwości powstania braku, rozwiązywaniu problemów i zatrzymywanie linii produkcyjnej, gdy powstanie wadliwy produkt.
Wartość – wszystko to czego oczekuje klient i jest gotów za to zapłacić.
Strata – wszystkie działania, procesy czy operacje, które nie dodają wartości do produktu z punktu widzenia klienta. Japończycy sklasyfikowali straty w 3 kategoriach (muda, muri, mura).
Muda –„marnotrawstwo” – 7 strat: nadprodukcja, zapasy, transport, zbędne ruchy, braki, oczekiwanie, nadmierne przetewarzanie.
Muri – nadmierne obciążenie – np. praca maszyny na większych obrotach niż powinna.
Mura – nierówne obciążenie – np. dzisiaj praca w nadgodzinach, a jutro pracy na ¾ czasu.
VSM (Value Stream Mapping) – Mapowanie Strumienia Wartości – narzędzie do analizy obecnego przepływu strumienia wartości.
Standaryzacja – proces wdrażania standardów czyli „najłatwiejszych i najbezpieczniejszych procesów dla pracowników, które są najbardziej efektywne z punktu widzenia kosztów i produktywności oraz pozwalają firmie zapewniać najlepszą jakość dla klienta”.
5 S – Organizacja miejsca pracy – wg 5 kroków: Selekcji, Systematyki, Sprzątania, Standaryzacji i Samodyscypliny. Sprawdź aplikację do audytów 5s.
Zarządzanie Wizualne (Visual Management) – najszybsze i najprostsze przekazywanie informacji za pomocą wizualizacji.
Skill maps (mapa umiejętności) – macierz odwzorowująca poziom umiejętności pracowników.
Andon – sygnalizacja świetlna informująca o statusie np. pracy linii produkcyjnej.
FIFO – First In First Out – zasada – co pierwsze weszło do procesu to opuści go jako pierwsze.
One point lesson (lekcja jednopunktowa) – wizualizacja na A4 wprowadzonej zmiany w procesie.
KPI – Key Performance Indicators – Kluczowe wskaźniki efektywności.
Push (Pchanie) – system produkcyjny oparty na prognozach, dążący domaksymalnego wykorzystania wydajności maszyny w efekcie powstają duże zapasy magazynowe surowca, wyrobów gotowych i w toku (WIP).
WIP (work in proces) – zapas produktów w toku znajdujący się pomiędzy procesami.
Pull (ssanie) – sterowanie produkcją według faktycznego zapotrzebowania klienta. Procesy produkują tylko to co chce klient i w odpowiedniej ilości. Zlecenie produkcyjne trafia do jednego procesu pacemaker (stymulatora).
Supermarket – rodzaj magazynu działający zgodnie z zasadą FIFO, posiadający wyznaczone poziomy min – max, ze ściśle przypisaną lokalizacją.
Milkrun (mleczarz) – osoba, która regularnie dostarcza detale do supermarketów lub w odpowiednie pole według standardowej trasy.
Kanban – wizualny system organizacji dostaw detali do produkcji w momencie wystąpienia faktycznego zapotrzebowania. Zlecenie produkcyjne/transportowe wywołane przez klienta w systemie ssącym.
Layout – ustawienie hali „z lotu ptaka”
Diagram Spaghetti – oznaczenie na Layout’cie fizycznego przepływu materiałów / poruszania się pracownika.
Gniazdo produkcyjne – zbiór kilku procesów w bliskiej odległości zapewniający przepływ i minimalny WIP.
Batch – partia produkcyjna – produkcja masowa, wytwarzanie dużej partii i przekazywanie całej do kolejnego etapu.
One – Piece – Flow (przepływ jednej sztuki) – produkowanie i przekazywanie do kolejnego procesu jednej sztuki produktu.
Cycle Time – Czas Cyklu (C/T) – czas wykonania jednej sztuki (lub serii), czas pomiędzy wyjściem kolejnej sztuki z danego procesu.
Takt Time – Czas Taktu (T/T) – tempo z jakim należy wytworzyć jedną sztukę, aby zrealizować zapotrzebowanie klienta.
Balansowanie linii – równomierne rozłożenie pracy na linii produkcyjnej.
Wąskie gardło (Bottleneck) – proces w strumieniu wartości, który blokuje wszystkie pozostałe, często najdłuższy proces.
Heijunka – poziomowanie produkcji – minimalizowanie partii produkcyjnej przy ciągłym zapewnieniu dostępności produktów dla klienta.
SMED – Single Minute Exchange of Die – Koncepcja skracania przezbrojenia do czasu poniżej 10 minut. Dowiedz się więcej dzięki szkoleniu SMED.
Genchi genbutsu – „sięganie do źródła” – koncepcja rozwiązywania problemów na Gemba,
Idź i zobacz – koncepcja rozwiązywania problemów na Gemba.
Gemba – miejsce akcji – miejsce tworzenia wartości np. hala produkcyjna.
Raport A3 – narzędzie do opisywania i rozwiązywania problemów.
Zasada Pareto 20/80 – zasada przedstawiająca proporcję np. ok. 20% produktów zapewnia ok. 80% dochodów.
PDCA (Plan – Do – Check – Act) – koło/cykl Deminga – zasada wprowadzania zmian.
Diagram Ishkawy (rybiej ości) – diagram do identyfikacji przyczyn problemu.
5 Why – 5 x Dlaczego – narzędzie do szukania przyczyny źródłowej problemu zadając pytania Dlaczego?
Poka Yoke – zabezpieczenie przed popełnieniem błędu.
TPM (Total Productive Maintenance) – Totalne Utrzymanie Ruchu – metodologia utrzymania ruchu maszyn i urządzeń.
OEE (Overall Equipment Effectivness) – Całkowita Efektywność Urządzeń – wskaźnik pokazujący stopień wykorzystania maszyn.
Kaizen – Kai (zmiana) Zen (dobra) – koncepcja ciągłego doskonalenia
Słownik pojęć Lean to za mało?
MOŻLIWOŚĆ SKORZYSTANIA
Z BEZPŁATNEGO KURSU –
BONUS INTRO TO LEAN
Z BEZPŁATNEGO KURSU –
BONUS INTRO TO LEAN
Szkolenie Online
Darmowy kurs – wprowadzenie do Lean
Co to jest Lean?
Dom Toyoty i zasady Lean
Wartość i straty