Przyczyny błędów w procesach: Klasyfikacja, analiza i metody redukcji
W jednym z poprzednich artykułów poruszyliśmy tematykę błędów w procesach pracy i tego jak je wykrywać, oceniać i unikać. No ale – żeby ustrzec się przed błędami, musimy dokładnie poznać ich przyczyny. I właśnie na tym dziś się skupimy. Wiemy, że w kontekście procesów produkcyjnych i operacyjnych, błędy mogą przybierać różne formy – od drobnych nieścisłości po poważne awarie, które mają daleko idące konsekwencje. Dlatego zrozumienie przyczyn błędów i skuteczne zarządzanie nimi jest niezbędne dla każdej organizacji dążącej do doskonałości operacyjnej. Dlaczego tak się dzieje? Ponieważ błędy, niezależnie od ich rodzaju, mogą znacząco wpływać na jakość produktów, efektywność operacyjną i satysfakcję klientów.
Rozpoznawanie i klasyfikacja błędów w procesach
Rozpoznawanie i klasyfikacja błędów w procesach jest podstawowym elementem zarządzania jakością i efektywnością w każdej organizacji. Aby skutecznie zarządzać błędami, konieczne jest ich systematyczne identyfikowanie, analizowanie i kategoryzowanie tak, by ustalić przycyznę każdego z nich . Błędy można podzielić na różne kategorie, takie jak błędy danych, błędy kompletacji, błędy analizy danych oraz błędy przypadkowe czy błędy grube. Każdy typ błędu ma swoje specyficzne przyczyny i skutki, które wpływają na różne aspekty działalności organizacji. Rozpoznanie tych błędów pozwala na wdrażanie odpowiednich działań korygujących i prewencyjnych, co z kolei przyczynia się do ciągłego doskonalenia procesów i minimalizacji ryzyka.
Błędy danych: przyczyny i skutki
Błędy danych są jednymi z najczęstszych problemów, z którymi borykają się organizacje. Mogą wynikać z różnych przyczyn, takich jak błędy ludzkie podczas wprowadzania danych, awarie systemów informatycznych, nieaktualne informacje lub niespójności w źródłach danych. Skutki błędów danych mogą być poważne i dalekosiężne. Mogą prowadzić do błędnych analiz, które z kolei skutkują podejmowaniem niewłaściwych decyzji biznesowych. Na przykład, błędne dane dotyczące sprzedaży mogą prowadzić do nieprawidłowego prognozowania zapotrzebowania, co skutkuje zarówno nadprodukcją, jak i niedoborem produktów. W skrajnych przypadkach, błędy danych mogą prowadzić do utraty zaufania klientów, reputacji firmy i znacznych strat finansowych. Dlatego tak ważne jest wdrażanie skutecznych procedur kontroli jakości danych, regularne audyty oraz szkolenia dla pracowników.
Błędy kompletacji: wpływ technologii na jakość procesu
Błędy kompletacji odnoszą się do problemów związanych z niewłaściwym zestawieniem komponentów lub produktów zgodnie z zamówieniem klienta. W przemyśle produkcyjnym i logistycznym, takie błędy mogą wynikać z manualnych procesów, nieodpowiedniej komunikacji lub niedoskonałości technologicznych systemów zarządzania magazynem (WMS). Technologia odgrywa kluczową rolę w minimalizowaniu błędów kompletacji. Wprowadzenie zaawansowanych systemów WMS, automatyzacji procesów oraz technologii identyfikacji radiowej (RFID) znacząco poprawia dokładność i szybkość kompletacji zamówień. Na przykład, zautomatyzowane systemy mogą monitorować stany magazynowe w czasie rzeczywistym, redukując ryzyko braków i zapewniając, że każdy element zamówienia jest prawidłowo skompletowany. Skuteczne wykorzystanie technologii w procesach kompletacji nie tylko zwiększa jakość obsługi klienta, ale także redukuje koszty operacyjne związane z błędami i zwrotami.
Błędy w analizie danych: jak przestarzałe dane wpływają na wyniki
Błędy w analizie danych mogą wynikać z wielu przyczyn, ale jednym z najczęstszych problemów jest korzystanie z przestarzałych danych. Analiza oparta na nieaktualnych informacjach może prowadzić do błędnych wniosków i decyzji, które mogą negatywnie wpłynąć na całą organizację. Na przykład, decyzje dotyczące strategii rynkowej oparte na starych danych sprzedażowych mogą nie uwzględniać obecnych trendów i preferencji klientów, co prowadzi do nieskutecznych działań marketingowych i strat finansowych. Aby zminimalizować ryzyko błędów wynikających z przestarzałych danych, organizacje powinny regularnie aktualizować swoje bazy danych, stosować systemy monitorowania danych w czasie rzeczywistym oraz wdrażać procedury walidacji danych. Dodatkowo, szkolenia dla analityków danych na temat najlepszych praktyk w zakresie zarządzania danymi mogą znacznie poprawić jakość analiz i decyzji biznesowych.
Błędy przypadkowe vs błędy grube: rozróżnienie i metody zarządzania
Błędy przypadkowe i błędy grube to dwa główne typy błędów, które mogą wystąpić w procesach pracy i analizy danych. Błędy przypadkowe, znane również jako losowe, są wynikiem nieprzewidywalnych i niezamierzonych zdarzeń, które mogą wpływać na wyniki. Przykłady obejmują drobne wahania w pomiarach lub chwilowe zakłócenia w systemie. Z kolei błędy grube, zwane również systematycznymi, wynikają z fundamentalnych problemów w procesie, takich jak wadliwe urządzenia pomiarowe, błędy proceduralne lub niekompetencja personelu. Rozróżnienie między tymi typami błędów jest kluczowe dla skutecznego zarządzania jakością.
Metody zarządzania błędami przypadkowymi obejmują zastosowanie statystycznych narzędzi analizy, takich jak kontrola jakości i analizy odchylenia standardowego, które pomagają zidentyfikować i zminimalizować wpływ tych błędów. Zarządzanie błędami grubymi wymaga bardziej kompleksowego podejścia, w tym regularnych audytów procesów, kalibracji sprzętu, wdrażania i aktualizacji procedur operacyjnych oraz ciągłego szkolenia pracowników. W obu przypadkach, kluczowe jest wczesne wykrywanie i natychmiastowe podejmowanie działań korygujących, aby minimalizować wpływ błędów na wyniki i efektywność organizacji.
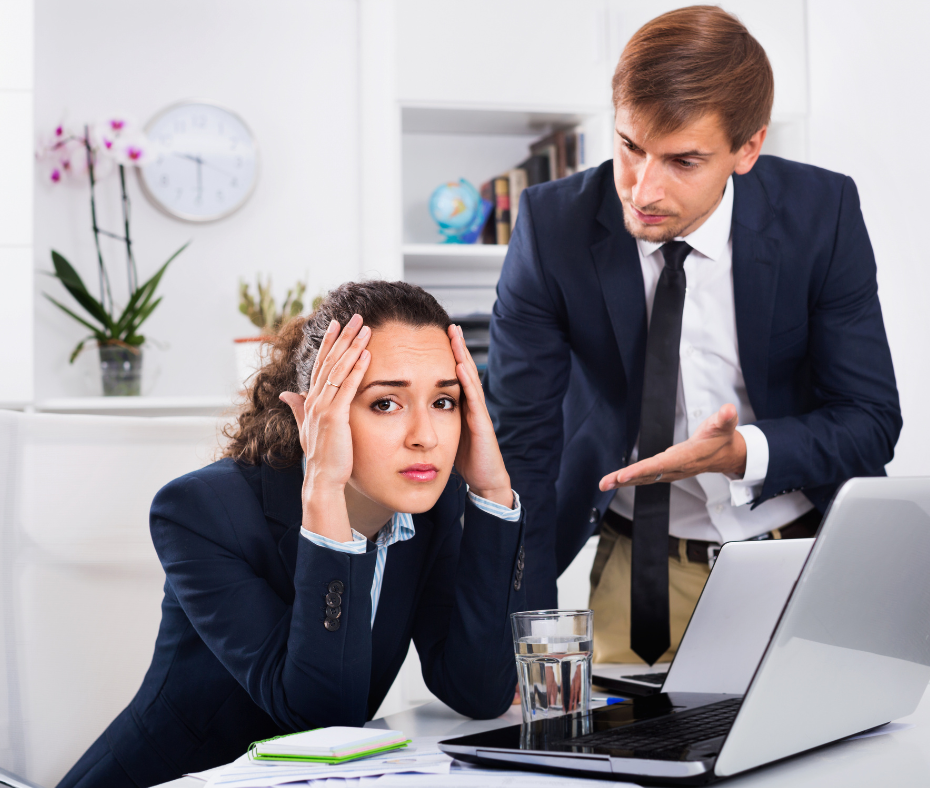
Chcesz dowiedzieć się, z czego wynikają błędy w procesach w Twojej firmie? Sprawdź audyt procesów, który przeprowadzamy – spojrzenie świeżym okiem na procesy pozwala na wyłapanie większej liczby detali.
Analiza przyczyn błędów: metody i narzędzia
Analiza przyczyn błędów jest procesem, który pozwala organizacjom na identyfikację źródeł problemów i wdrażanie skutecznych rozwiązań. Jedną z najpopularniejszych metod jest analiza przyc błędów przyczynowo-skutkowa (root cause analysis, RCA), która polega na systematycznym badaniu sekwencji zdarzeń prowadzących do błędu. Narzędzia takie jak diagram Ishikawy (diagram rybiej ości) pomagają w identyfikacji potencjalnych przyczyn problemów w kategoriach takich jak sprzęt, materiały, ludzie, metody, środowisko i pomiary. Kolejną skuteczną metodą jest technika 5 Whys, która polega na zadawaniu serii pytań “dlaczego”, aby dotrzeć do podstawowej przyczyny problemu. Wykorzystanie narzędzi statystycznych, takich jak analiza Pareto, może również pomóc w priorytetyzacji problemów i skupieniu się na tych, które mają największy wpływ na procesy.
Badanie przyczyn błędów: etapy analizy
Badanie przyczyn błędów składa się z kilku kluczowych etapów, które pozwalają na dokładne zrozumienie i rozwiązanie problemów. Pierwszym krokiem jest identyfikacja problemu, co obejmuje zbieranie danych i dowodów dotyczących błędu. Następnie, należy przeprowadzić wstępną analizę, aby zidentyfikować potencjalne przyczyny. W tym etapie często stosuje się narzędzia takie jak diagram Ishikawy czy analiza 5 Whys. Kolejnym krokiem jest weryfikacja przyczyn poprzez testowanie i zbieranie dodatkowych danych, co pozwala na potwierdzenie lub odrzucenie hipotez. Po zidentyfikowaniu podstawowej przyczyny, należy opracować i wdrożyć działania korygujące, które eliminują problem. Ostatnim etapem jest monitorowanie i ocena skuteczności wdrożonych działań, aby upewnić się, że problem został rozwiązany i nie wystąpi ponownie.
Analiza FMEA i PFMEA: jak wykorzystać w praktyce
Analiza FMEA (Failure Modes and Effects Analysis) oraz PFMEA (Process Failure Modes and Effects Analysis) to metody, które pomagają w identyfikacji i ocenie potencjalnych awarii w produktach i procesach oraz ich skutków. W praktyce, FMEA jest stosowana do oceny ryzyka związanego z produktami, natomiast PFMEA koncentruje się na procesach produkcyjnych. Proces FMEA rozpoczyna się od identyfikacji wszystkich możliwych awarii (modes) oraz ich przyczyn i skutków. Każda awaria jest następnie oceniana pod kątem jej znaczenia (severity), prawdopodobieństwa wystąpienia (occurrence) i możliwości wykrycia (detection). Na podstawie tych ocen oblicza się wskaźnik ryzyka (Risk Priority Number, RPN), który pomaga w priorytetyzacji działań korygujących. W PFMEA proces jest podobny, ale skupia się na specyficznych etapach procesu produkcyjnego. Praktyczne zastosowanie FMEA i PFMEA wymaga regularnych przeglądów i aktualizacji, aby uwzględniać zmiany w produktach i procesach oraz nowe informacje dotyczące ryzyka.
Analiza błędów pomiarowych: ocena i kontrola
Analiza błędów pomiarowych jest ważna dla zapewnienia dokładności i wiarygodności danych pomiarowych. Błędy pomiarowe mogą wynikać z różnych źródeł, takich jak niekalibrowane urządzenia, niewłaściwe metody pomiarowe, wpływ środowiska czy błędy operatora. Ocena błędów pomiarowych obejmuje identyfikację tych źródeł oraz kwantyfikację ich wpływu na wyniki pomiarów. Jednym z narzędzi używanych do tego celu jest analiza niepewności pomiarowej, która pozwala na oszacowanie zakresu, w jakim wyniki mogą się różnić od rzeczywistej wartości. Kontrola błędów pomiarowych wymaga regularnej kalibracji sprzętu, stosowania standardowych procedur operacyjnych (SOP) oraz szkolenia operatorów w zakresie prawidłowych technik pomiarowych. Dodatkowo, stosowanie systemów monitorowania i rejestracji danych w czasie rzeczywistym może pomóc w szybkiej identyfikacji i korekcie błędów.
Analiza kosztów błędu: jak błędy wpływają na finanse firmy
Analiza kosztów błędu jest niezbędna do zrozumienia pełnego wpływu błędów na finanse firmy. Błędy mogą generować bezpośrednie koszty, takie jak koszty naprawy, wymiany wadliwych produktów, zwrotów od klientów oraz dodatkowej pracy związanej z korektą błędów. Mogą również prowadzić do pośrednich kosztów, takich jak utrata zaufania klientów, pogorszenie reputacji firmy, opóźnienia w produkcji oraz zwiększenie wskaźnika rotacji pracowników z powodu frustracji związanej z ciągłymi problemami. W dłuższej perspektywie, błędy mogą wpływać na konkurencyjność firmy na rynku, prowadząc do utraty udziału w rynku i spadku przychodów. Dlatego analiza kosztów błędu powinna obejmować zarówno bezpośrednie, jak i pośrednie koszty, a także uwzględniać długoterminowe skutki finansowe. Wdrażanie skutecznych strategii zapobiegania błędom i działań korygujących może znacząco zredukować te koszty, poprawiając ogólną rentowność i stabilność finansową firmy.
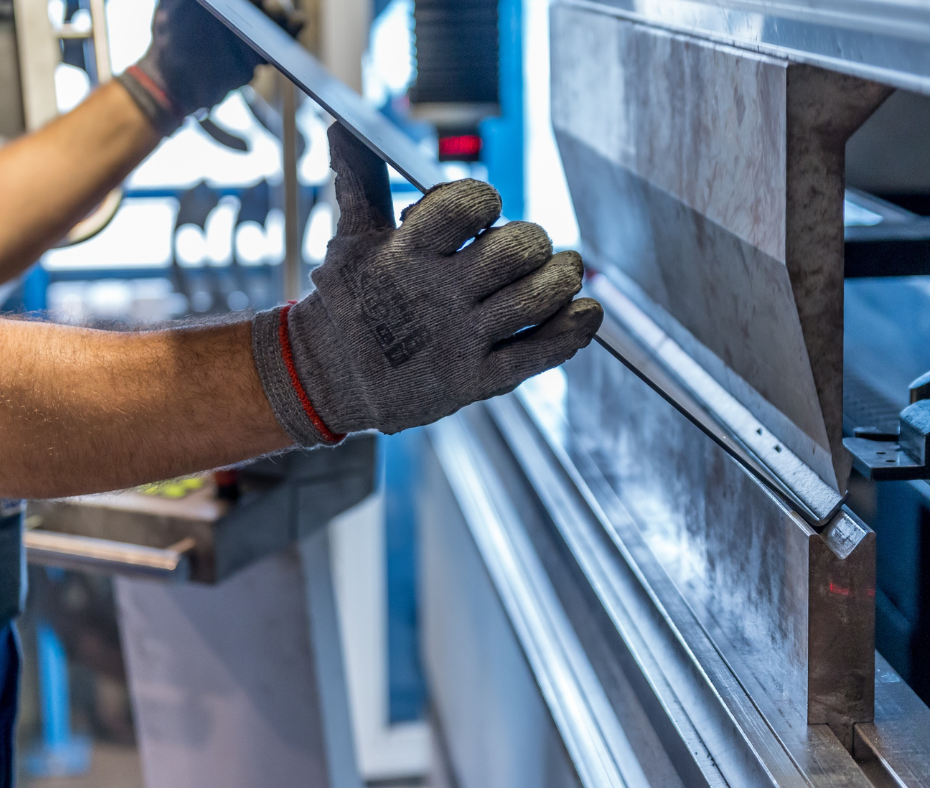
Szkolenie Online
Budowanie zaangażowania i odpowiedzialności pracowników
motywowanie i angażowanie pracowników
wpływanie na percepcję innych osób
wprowadzanie zmiany w myśleniu i zachowaniu swoich pracowników
wykorzystanie użytecznych schematów myślenia
Czynnik ludzki jako przyczyna błędów
Czynnik ludzki jest jedną z najczęstszych przyczyn błędów w procesach pracy. Ludzie są podatni na błędy z różnych powodów, takich jak zmęczenie, stres, brak odpowiedniego szkolenia, niedostateczna komunikacja, a także brak motywacji. Błędy ludzkie mogą mieć poważne konsekwencje dla organizacji, prowadząc do strat finansowych, obniżenia jakości produktów i usług, a nawet do zagrożeń bezpieczeństwa. Zrozumienie, że błędy są nieodłączną częścią ludzkiej natury, pozwala na wprowadzenie skutecznych strategii zarządzania, które minimalizują ich występowanie i wpływ. Przyczyny błędów, które wynikają z pomyłki ludzkiej mogą uwzględniać przeciążenie pracą i obowiązkami. Kluczowe jest, aby organizacje tworzyły środowisko pracy, które wspiera pracowników, zapewniając im odpowiednie narzędzia, zasoby oraz szkolenia, które pomagają w redukcji błędów.
Przyczyny błędu ludzkiego: brak zrozumienia i brak weryfikacji
Brak zrozumienia i brak weryfikacji są dwiema głównymi przyczynami błędów ludzkich w miejscu pracy. Brak zrozumienia może wynikać z niewystarczającego szkolenia, niejasnych instrukcji, czy też skomplikowanych procedur, które pracownicy mają trudności z przyswojeniem. Kiedy pracownicy nie do końca rozumieją, co mają robić i dlaczego, są bardziej narażeni na popełnianie błędów. Z kolei brak weryfikacji odnosi się do braku systemów kontrolnych, które mogłyby wychwycić błędy przed ich eskalacją. Regularne kontrole, audyty oraz procedury podwójnej weryfikacji mogą znacząco zredukować liczbę błędów wynikających z niedopatrzeń. Wprowadzenie takich mechanizmów weryfikacyjnych w procesy operacyjne zapewnia dodatkową warstwę bezpieczeństwa, która pomaga w wykrywaniu i korygowaniu błędów, zanim staną się one poważnym problemem.
Jak ustrzec się błędami: zarządzanie jakością i czynnikiem ludzkim
Aby ustrzec się błędów wynikających z czynnika ludzkiego, organizacje muszą skoncentrować się na zarządzaniu jakością oraz odpowiednim zarządzaniu pracownikami. Zarządzanie jakością obejmuje wdrożenie systemów i procedur, które pomagają w identyfikacji, analizie i korygowaniu błędów. Normy takie jak ISO 9001 dostarczają ram do tworzenia skutecznych systemów zarządzania jakością, które uwzględniają aspekt ludzki. Regularne szkolenia i rozwój kompetencji pracowników są kluczowe, aby zapewnić, że mają oni odpowiednią wiedzę i umiejętności do wykonywania swoich obowiązków bezbłędnie. Promowanie kultury otwartej komunikacji, gdzie pracownicy czują się swobodnie zgłaszać problemy i proponować ulepszenia, również przyczynia się do zmniejszenia liczby błędów.
Dodatkowo, techniki takie jak analiza przyczynowo-skutkowa, sesje feedbacku, oraz programy motywacyjne mogą być skutecznie wykorzystywane do zarządzania czynnikiem ludzkim. Systemy monitorowania i oceny pracy pozwalają na bieżące śledzenie wyników i wczesne wykrywanie potencjalnych problemów. Wprowadzenie procedur zarządzania zmianą, które uwzględniają reakcje pracowników na nowe procesy i technologie, pomaga w minimalizacji oporu i błędów związanych z adaptacją. Efektywne zarządzanie czynnikiem ludzkim poprzez motywowanie, szkolenie i angażowanie pracowników w procesy poprawy jakości, znacząco przyczynia się do redukcji błędów i poprawy ogólnej wydajności organizacji.
Przyczyny błędów i ich znaczenie w działaniach prewencyjnych
Działania prewencyjne i detekcyjne są ważnymi elementami w zarządzaniu jakością i redukcji błędów w procesach produkcyjnych. Działania prewencyjne koncentrują się na zapobieganiu występowaniu błędów poprzez wprowadzenie odpowiednich procedur, standardów i technologii. Natomiast działania detekcyjne mają na celu wczesne wykrywanie błędów, zanim będą miały one negatywny wpływ na produkt końcowy lub proces. Skuteczne połączenie tych dwóch podejść pozwala na minimalizację ryzyka błędów, poprawę jakości produktów i zwiększenie efektywności operacyjnej. Organizacje, które inwestują w zarówno prewencję, jak i detekcję, są w stanie szybciej reagować na problemy, co przekłada się na wyższą satysfakcję klientów i lepsze wyniki finansowe.
Planowane działania prewencyjne: jak wdrożyć Poka Yoke
Poka Yoke, czyli metoda zapobiegania błędom, jest skutecznym narzędziem prewencyjnym stosowanym w zarządzaniu jakością. Poka Yoke koncentruje się na projektowaniu procesów i systemów w taki sposób, aby błędy były niemożliwe do popełnienia lub natychmiast wykrywane. Planowane działania prewencyjne to jendno – jak je wdrożyć? Wdrożenie Poka Yoke w organizacji zaczyna się od identyfikacji obszarów, w których najczęściej dochodzi do błędów.
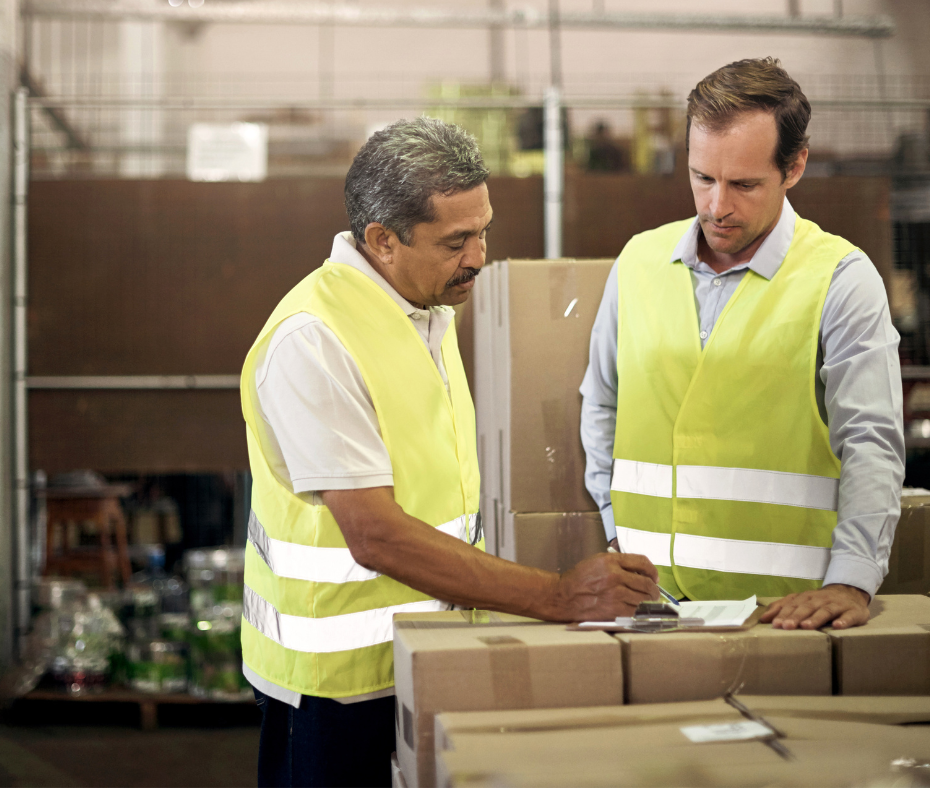
Następnie, należy zaprojektować rozwiązania, które eliminują możliwość ich wystąpienia. Przykłady takich rozwiązań to stosowanie jigs and fixtures, które zapewniają prawidłowe położenie komponentów, lub zastosowanie czujników, które wykrywają nieprawidłowe warunki operacyjne. Kluczowe jest, aby te rozwiązania były proste i niezawodne, aby mogły być łatwo zintegrowane z istniejącymi procesami. Regularne szkolenia dla pracowników na temat znaczenia i stosowania Poka Yoke również są ważnym elementem skutecznego wdrożenia tej metody.
Działania detekcyjne: kontrola wady i zarządzanie jakością
Rozwiązywanie problemów produkcyjnych zaczyna się od.. ich znalezienia i ustalenia przyczyn! Działania detekcyjne są niezbędne do wczesnego wykrywania błędów i wad w procesach produkcyjnych, co pozwala na szybkie podjęcie działań korygujących. Kontrola jakości, jako integralna część działań detekcyjnych, obejmuje różnorodne techniki, takie jak inspekcje wizualne, testy funkcjonalne, badania nieniszczące oraz analiza statystyczna procesów. Systemy zarządzania jakością, takie jak Six Sigma czy Total Quality Management (TQM), integrują działania detekcyjne z całościowym podejściem do ciągłego doskonalenia. Skuteczne zarządzanie jakością wymaga również wdrożenia systemów monitorowania i raportowania, które umożliwiają bieżące śledzenie parametrów produkcji i natychmiastowe wykrywanie odchyleń od normy. Takim programem może być aplikacja ZaPro, która pozwala na zarządzanie procesem produkcji od A do Z – włączając w to raporty i dostęp do nich w czasie realnym. Wprowadzenie systemów wczesnego ostrzegania i regularne audyty procesów pomagają w identyfikacji potencjalnych problemów, zanim przekształcą się one w poważne wady produktów.
Rozwiązywanie problemów produkcyjnych: uwzględnienie błędów pomiarowych
Błędy pomiarowe są często źródłem problemów produkcyjnych, które mogą prowadzić do niezgodności produktów i obniżenia jakości. Rozwiązywanie problemów produkcyjnych z uwzględnieniem błędów pomiarowych wymaga precyzyjnej analizy i oceny systemów pomiarowych używanych w procesach produkcyjnych. Kalibracja i regularne sprawdzanie dokładności narzędzi pomiarowych są niezbędne, aby zapewnić wiarygodność wyników pomiarów. W procesie rozwiązywania problemów produkcyjnych ważne jest również zrozumienie źródeł błędów pomiarowych, takich jak wibracje, zmiany temperatury czy błąd operatora, i wdrożenie środków minimalizujących ich wpływ. Stosowanie metod statystycznych, takich jak analiza systemów pomiarowych (MSA), może pomóc w ocenie i poprawie jakości pomiarów. Regularne szkolenia pracowników na temat właściwych technik pomiarowych i interpretacji wyników również przyczyniają się do redukcji błędów pomiarowych i poprawy jakości produkcji.
Podsumowanie
Przyczyny błędów w procesach są zróżnicowane i obejmują zarówno czynniki ludzkie, jak i technologiczne. Mogą pojawić się również przyczyny niebezpośrednie, które bywają trudniejsze do odnalezienia. Błędy mogą wynikać z niewystarczającego zrozumienia zadań, braku weryfikacji, niewłaściwego szkolenia, zmęczenia pracowników oraz niedoskonałości w systemach i procedurach. Skuteczne zarządzanie jakością integruje działania prewencyjne i detekcyjne, takie jak metoda Poka Yoke i systemy kontroli jakości, co pozwala na minimalizację ryzyka błędów i wczesne wykrywanie problemów.
Błędy pomiarowe wymagają regularnej kalibracji systemów pomiarowych i odpowiedniego szkolenia pracowników. Zrozumienie i analiza przyczyn błędów systematycznych, wraz z regularnym wdrażaniem działań korygujących i zapobiegawczych, są kluczowe dla ciągłego doskonalenia procesów. Takie podejście zwiększa jakość produktów, efektywność operacyjną, zadowolenie klientów oraz stabilność finansową firmy, przyczyniając się do długoterminowego sukcesu organizacji.