Optymalizacja procesów w firmie produkcyjnej – Skuteczne strategie
Optymalizacja procesów produkcyjnych jest kluczowym elementem w zapewnieniu efektywności, rentowności i konkurencyjności przedsiębiorstw produkcyjnych. Polega ona na ciągłym analizowaniu i udoskonalaniu wszystkich etapów produkcji, od surowego materiału po gotowy produkt. Poprzez integrację nowoczesnych technologii, stosowanie skutecznych metod zarządzania, takich jak Kanban czy Lean Manufacturing, oraz precyzyjne modelowanie procesów, firmy mogą znacznie zwiększyć swoją wydajność, zmniejszyć koszty operacyjne i poprawić jakość produktów. W tym kontekście optymalizacja staje się nie tylko narzędziem do zarządzania bieżącą produkcją, ale również strategią długoterminowego rozwoju i innowacji.
Spis treści:
- Zrozumienie optymalizacji procesów produkcji
- Zarządzanie procesami produkcyjnymi
- Narzędzia Lean management w optymalizacji procesów produkcyjnych
- Wprowadzenie optymalizacji procesów na stanowisku pracy
- Technologia w optymalizacji procesów produkcyjnych
- Podsumowanie
- Pobierz przykład narzędzia do analizy rentowności firmy zupełnie za darmo!
Zrozumienie optymalizacji procesów produkcji
Optymalizacja procesów produkcyjnych to kluczowy element w zarządzaniu efektywnością operacyjną przedsiębiorstwa produkcyjnego. Ten proces polega na analizie, planowaniu i usprawnieniu każdego etapu produkcji w celu zwiększenia wydajności, obniżenia kosztów i poprawy jakości produktów. W jakiej sytuacji przyda się optymalizacja procesów produkcyjnych? Krótko mówiąc, w niemal każdej, kiedy zależy Ci na zwiększeniu efektywności. Przykładowo, dzięki optymalizacji produkcji fabryka samochodów, która wprowadza zautomatyzowane linie montażowe, jest w stanie produkować więcej pojazdów w krótszym czasie i z mniejszym ryzykiem błędów, co prowadzi do zwiększenia efektywności i obniżenia kosztów jednostkowych.
Definicja i znaczenie optymalizacji procesów produkcji
Jak usprawnić proces produkcyjny? Optymalizacja procesów produkcyjnych odnosi się do ciągłego dążenia do doskonalenia metod produkcji w celu osiągnięcia wyższej efektywności, niższych kosztów i lepszej jakości produktów. Jest to proces, który wymaga regularnej analizy i przeglądu istniejących praktyk, a także wprowadzania innowacji i zmian, które mogą przynieść korzyści. Znaczenie tego procesu jest ogromne, ponieważ bezpośrednio wpływa on na konkurencyjność firmy na rynku. Na przykład, producent odzieży, który optymalizuje procesy cięcia i szycia, wykorzystując zaawansowane technologie, może znacznie zmniejszyć ilość odpadów materiałowych i skrócić czas potrzebny na wyprodukowanie partii ubrań.
Kluczowe elementy optymalizacji procesów produkcji
Kluczowe elementy optymalizacji procesów produkcyjnych obejmują:
Automatyzacja i technologia: Wprowadzenie nowoczesnych technologii i automatyzacji może znacznie zwiększyć wydajność i jakość produkcji. Na przykład, użycie robotów w fabrykach może przyspieszyć procesy produkcyjne i zminimalizować ryzyko błędów ludzkich.
Lean Manufacturing i Kaizen: Stosowanie zasad szczupłej produkcji i ciągłej poprawy pozwala na eliminację marnotrawstwa i optymalizację procesów. To podejście koncentruje się na wartości dodanej dla klienta i eliminuje wszystkie działania nieprzyczyniające się do tej wartości.
Analiza i monitorowanie procesów: Regularne przeglądy i analizy procesów produkcyjnych pozwalają na identyfikację obszarów do usprawnień. Używanie narzędzi takich jak systemy ERP (Enterprise Resource Planning) umożliwia zbieranie danych i analizę wydajności w czasie rzeczywistym.
Szkolenia i rozwój pracowników: Inwestycje w szkolenia pracowników są kluczowe, aby mogli oni efektywnie wykorzystywać nowe technologie i metody pracy. Pracownicy dobrze zaznajomieni z procesami i zaangażowani w ciągłą poprawę są nieocenionym zasobem w optymalizacji produkcji.
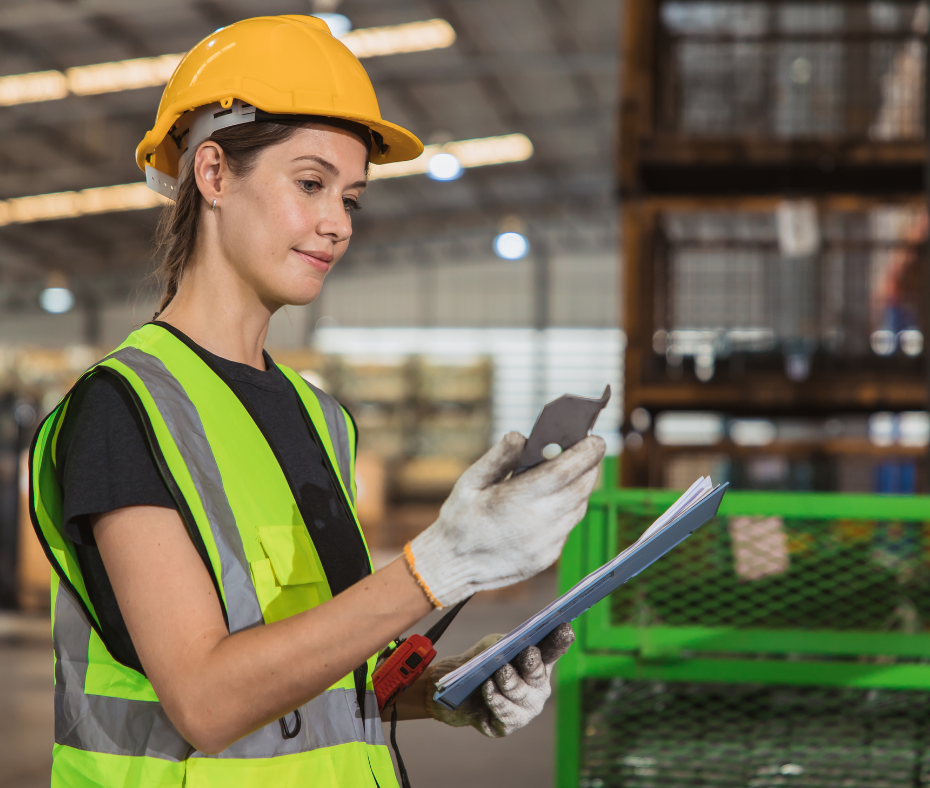
Optymalizacja procesów produkcji jest nieustannym zadaniem, wymagającym innowacyjności, elastyczności i zaangażowania na wszystkich poziomach organizacji. Firmy, które skutecznie optymalizują swoje procesy produkcyjne, są w stanie nie tylko obniżyć koszty i zwiększyć wydajność, ale także poprawić jakość swoich produktów i zwiększyć satysfakcję klientów.i
Zarządzanie procesami produkcyjnymi
Jak zarządzać, by zadbać o optymalne zasoby i procesy produkcyjne? Zarządzanie procesami produkcji to kompleksowe podejście do nadzorowania wszystkich aspektów związanych z produkcją w przedsiębiorstwie. Obejmuje to planowanie, koordynowanie, wykonanie i monitorowanie różnych działań, które łącznie prowadzą do wytworzenia finalnych produktów. Skuteczne zarządzanie procesami w produkcji i nie tylko zapewnia płynność operacji, ale także pomaga w identyfikacji obszarów do usprawnień, zwiększając efektywność i redukując koszty. Przekłada się to na korzyści w zakresie płynności finansowej. Na przykład, w przemyśle motoryzacyjnym, zarządzanie produkcyjnymi procesami obejmuje koordynację łańcucha dostaw, zapewnienie jakości komponentów, optymalizację linii montażowych oraz monitorowanie wydajności i czasu produkcji.
Rola zarządzania procesami produkcji w optymalizacji
Rola zarządzania procesami w produkcji w optymalizacji produkcji jest kluczowa. Przez ciągłe analizowanie i usprawnianie procesów produkcyjnych, firmy mogą zwiększać swoją wydajność, minimalizować marnotrawstwo i obniżać koszty produkcji. Dobre sterowanie produkcją pozwala na lepsze wykorzystanie zasobów – zarówno ludzkich, jak i materialnych – oraz na szybsze reagowanie na zmiany na rynku i w popycie konsumentów. Na przykład, stosowanie zasad Lean Manufacturing i ciągła poprawa (kaizen) w fabryce elektroniki może prowadzić do znacznego skrócenia czasów przestoju maszyn i zwiększenia jakości końcowych produktów.
Jak efektywne zarządzanie procesami wpływa na produkcję?
Efektywne zarządzanie procesami w produkcji ma bezpośredni wpływ na jakość, wydajność i rentowność produkcji. Poprzez ciągłe monitorowanie i optymalizację procesów, firmy mogą:
Zwiększyć wydajność: Poprzez zastosowanie zaawansowanych technologii i metod, takich jak automatyzacja, można zwiększyć prędkość produkcji przy jednoczesnym zachowaniu wysokiej jakości.
Zmniejszyć koszty: Identifikacja i eliminacja marnotrawstwa w procesach produkcji może znacząco zmniejszyć koszty operacyjne. Na przykład, poprawa zarządzania zapasami może zredukować koszty związane z przechowywaniem i przestarzałością materiałów.
Poprawić jakość produktów: Stosowanie skutecznych systemów kontroli jakości na każdym etapie produkcji pomaga w wykrywaniu i zapobieganiu błędom, co prowadzi do zwiększenia satysfakcji klientów.
Zwiększyć elastyczność: Dzięki efektywnemu zarządzaniu, firmy mogą szybciej dostosowywać się do zmieniających się wymagań rynku i wprowadzać nowe produkty szybciej i efektywniej.
W rezultacie, efektywne zarządzanie produkcyjnymi procesami jest nie tylko o zapewnianiu płynnej operacji na poziomie fabryki, ale także o strategicznym wpływie na ogólną wydajność i sukces firmy.
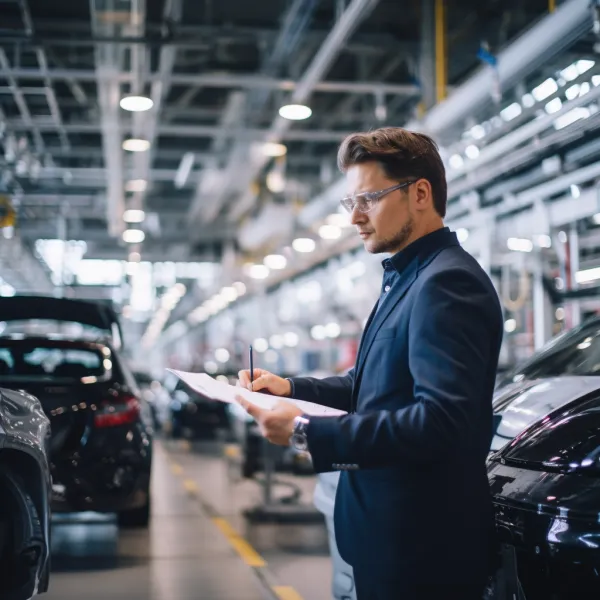
Narzędzia Lean management w optymalizacji procesów produkcyjnych
Optymalizacja procesów produkcyjnych wykorzystuje różnorodne metody i narzędzia, które pomagają zwiększyć efektywność, zmniejszyć koszty i poprawić jakość. Przykłady takich metod obejmują:
Mapowanie procesów: Technika ta polega na graficznym przedstawieniu kroków procesu produkcyjnego, co pozwala na łatwe identyfikowanie obszarów wymagających usprawnień.
Analiza przyczyn i skutków (Ishikawa): Służy do identyfikacji głównych przyczyn problemów w procesie produkcyjnym, co jest kluczowe dla ich skutecznego rozwiązania.
Benchmarking: Porównanie procesów i wyników firmy z najlepszymi praktykami w branży może pomóc w identyfikacji obszarów do poprawy.
Just in Time (JIT) jako strategia optymalizacji
Metoda Just in Time (JIT) to strategia sterowania produkcją, która polega na minimalizacji zapasów surowców i półproduktów, a także na produkcji towarów dokładnie wtedy, kiedy są potrzebne. Na przykład, w fabryce samochodów stosującej JIT, komponenty są dostarczane i montowane niemal bezpośrednio przed wysyłką gotowych pojazdów. Dzięki temu redukuje się koszty magazynowania i obniża ryzyko nadprodukcji.
Automatyzacja procesów: Jak technologia wpływa na optymalizację?
Automatyzacja procesów produkcji za pomocą zaawansowanych technologii, takich jak robotyka i oprogramowanie sterujące, przyczynia się do znacznego zwiększenia wydajności i precyzji. Przykładowo, automatyzacja linii pakujących w przemyśle spożywczym może przyspieszyć proces pakowania i zminimalizować ryzyko błędów ludzkich, co prowadzi do zwiększenia wydajności i poprawy jakości produktów.
Metoda 5S i jej rola w optymalizacji procesów
Metoda 5S, wywodząca się z filozofii lean manufacturing, skupia się na utrzymaniu porządku i efektywności w miejscu pracy. Pięć zasad (Seiri, Seiton, Seiso, Seiketsu, Shitsuke – sortowanie, uporządkowanie, czystość, standaryzacja, utrzymanie dyscypliny) pomaga w organizacji przestrzeni pracy, co przekłada się na lepszą efektywność i bezpieczeństwo. Wdrożenie 5S na hali produkcyjnej może znacząco wpłynąć na redukcję czasu poszukiwania narzędzi i materiałów, co skutkuje zwiększoną produktywnością.
Modelowanie procesów produkcyjnych i optymalizacja planowania
Modelowanie procesów, za pomocą narzędzi takich jak diagramy przepływu czy BPMN (Business Process Model and Notation), umożliwia firmom wizualizację i analizę swoich procesów produkcyjnych. Dzięki temu, można lepiej zrozumieć, jak poszczególne etapy procesu wpływają na całość i gdzie istnieją możliwości usprawnień.
Modelowanie procesów to technika, która polega na tworzeniu szczegółowych, często komputerowych modeli procesów produkcyjnych, co pozwala na wizualizację, analizę i usprawnienie każdego etapu produkcji. Dzięki modelowaniu procesów, menedżerowie mogą lepiej zrozumieć, jak poszczególne operacje wpływają na całość produkcji, identyfikować wąskie gardła oraz przewidywać skutki zmian w procesach. Na przykład, w fabryce samochodów modelowanie procesów może ujawnić, że przestawienie kolejności operacji na linii montażowej znacząco skróci czas produkcji bez dodatkowych kosztów. Efektywne wykorzystanie modelowania procesów prowadzi do bardziej precyzyjnego planowania, lepszego wykorzystania zasobów, zmniejszenia marnotrawstwa i w konsekwencji do zwiększenia ogólnej wydajności produkcji. Jest to narzędzie nieocenione dla przedsiębiorstw dążących do ciągłego doskonalenia swoich procesów produkcyjnych w szybko zmieniającym się otoczeniu biznesowym.
Narzędzie Lean: Jak może pomóc w optymalizacji procesów?
Lean manufacturing to podejście skoncentrowane na eliminowaniu marnotrawstwa i ciągłym doskonaleniu procesów. Narzędzia lean, takie jak kaizen (ciągła poprawa), metoda kanban (system wizualizacji pracy) czy value stream mapping (mapowanie strumienia wartości), pomagają w identyfikacji i usuwaniu nieefektywnych procesów, co prowadzi do zwiększenia wydajności i redukcji kosztów. Przykładowo, zastosowanie metody kanban w fabryce może pomóc w lepszym zarządzaniu zapasami i redukcji czasów przestoju.
Wprowadzenie optymalizacji procesów na stanowisku pracy
Wprowadzenie optymalizacji procesów na poszczególnych stanowiskach pracy to kluczowy krok w kierunku zwiększenia ogólnej wydajności przedsiębiorstwa. Proces ten zaczyna się od dokładnej analizy bieżących działań i identyfikacji obszarów, gdzie można wprowadzić usprawnienia. Na przykład, pracownik linii montażowej w fabryce samochodów może mieć za zadanie przegląd procedur montażowych, aby zidentyfikować kroki, które można zautomatyzować lub usprawnić. Wprowadzenie optymalizacji na poziomie stanowiska pracy nie tylko zwiększa efektywność, ale również może przyczynić się do poprawy morale pracowników, ponieważ ułatwia im pracę i umożliwia skupienie się na bardziej wymagających zadaniach.
Jak optymalizacja procesów wpływa na efektywność miejsca pracy?
Optymalizacja procesów na poziomie miejsca pracy ma bezpośredni wpływ na efektywność operacyjną. Usprawnienia mogą obejmować zwiększenie ergonomii stanowiska pracy, co zmniejsza zmęczenie i ryzyko błędów, oraz wprowadzenie narzędzi, które przyspieszają i upraszczają zadania. Na przykład, wdrożenie ergonomicznych narzędzi montażowych w fabryce elektroniki może przyspieszyć proces montażu i zredukować ryzyko uszkodzeń produktu. Ponadto, lepsze zarządzanie przepływem pracy i eliminacja niepotrzebnych zadań może znacznie zwiększyć produktywność i skrócić czas realizacji zleceń.
Wdrożenie systemu optymalizacji: Krok po kroku
Wdrożenie systemu optymalizacji procesów na stanowisku pracy wymaga zaplanowanego i metodycznego podejścia:
- Analiza istniejących procesów: Pierwszym krokiem jest szczegółowa analiza obecnych metod pracy w celu identyfikacji obszarów możliwych do usprawnienia.
- Projektowanie rozwiązań: Na podstawie analizy, projektuje się konkretne zmiany lub wprowadza nowe narzędzia i technologie (np. program do zarządzania produkcją), które mają na celu usprawnienie pracy.
- Testowanie i ocena: Przed pełnym wdrożeniem, nowe procesy i narzędzia są testowane w kontrolowanych warunkach, aby ocenić ich skuteczność i wpływ na wydajność.
- Szkolenie pracowników: Kluczowe jest przeszkolenie pracowników w zakresie nowych metod i narzędzi pracy.
- Wdrożenie i monitorowanie: Po wprowadzeniu zmian, ważne jest ciągłe monitorowanie ich wpływu na wydajność i wprowadzanie dalszych modyfikacji w razie potrzeby.
Każdy z tych kroków jest istotny, aby zapewnić, że proces optymalizacji przynosi realne korzyści dla przedsiębiorstwa, a także przyczynia się do poprawy warunków pracy dla zespołu.
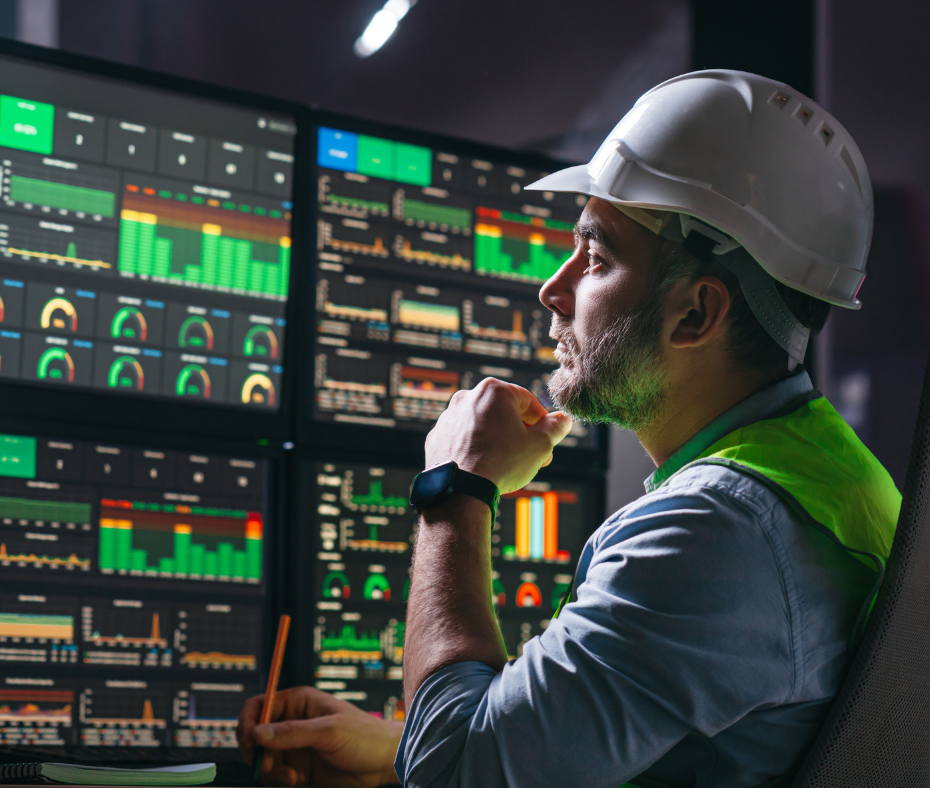
Technologia w optymalizacji procesów produkcyjnych
Zastosowanie nowoczesnych technologii w optymalizacji procesów produkcyjnych to klucz do zwiększenia efektywności i redukcji kosztów operacyjnych. Innowacyjne rozwiązania technologiczne, takie jak zaawansowany program do zarządzania produkcją, robotyka, systemy automatyzacji oraz analiza danych, odgrywają centralną rolę w modernizacji i usprawnianiu procesów produkcyjnych. Na przykład, w przemyśle motoryzacyjnym, zastosowanie robotów w procesach spawania nie tylko przyspiesza produkcję, ale również zapewnia większą spójność i jakość. Z kolei zintegrowane systemy zarządzania produkcją umożliwiają lepsze planowanie, kontrolę zapasów i zarządzanie jakością, co przekłada się na większą przejrzystość i kontrolę nad procesami produkcyjnymi.
Wdrożenie systemów informatycznych dla produkcji
Program do zarządzania produkcją jest nieocenionym narzędziem w optymalizacji procesów produkcyjnych. Systemy takie jak ERP (Enterprise Resource Planning) umożliwiają integrację różnych działów firmy, od zakupów i zarządzania zapasami po sprzedaż i obsługę klienta, co zapewnia spójne i efektywne przepływy pracy. Dzięki temu, decyzje biznesowe mogą być podejmowane na podstawie aktualnych i kompleksowych danych. Na przykład, system ERP w firmie produkującej elektronikę może automatycznie monitorować poziomy zapasów i generować zamówienia zakupu, kiedy poziom zapasów spada poniżej ustalonego progu, co zapobiega przestojom w produkcji z powodu braku materiałów.
Jak technologia wspomaga komunikację pracowników w procesie optymalizacji?
Technologia odgrywa również istotną rolę w ułatwianiu komunikacji między pracownikami, co jest kluczowe w procesie optymalizacji. Narzędzia takie jak wewnętrzne platformy komunikacyjne, systemy zarządzania projektami i współdzielone bazy danych umożliwiają szybką wymianę informacji i współpracę między różnymi działami i poziomami organizacji. Na przykład, w dużym zakładzie produkcyjnym, pracownicy mogą używać aplikacji mobilnej do szybkiego zgłaszania problemów technicznych lub potrzeby wsparcia, co umożliwia natychmiastowe reagowanie i minimalizuje przestoje. Współdzielone platformy do zarządzania projektami pozwalają zespołom na śledzenie postępów w realizacji zadań i efektywnie zarządzać zasobami, co przyczynia się do płynniejszego przebiegu projektów optymalizacyjnych.
Sprawdź odcinek naszego podcastu ,,Produkcja bez chaosu“, w którym odpowiadamy na pytanie: “Jak to jest, że mimo rozwoju firmy maleją zyski?” Pracując na konkretnych przykładach, przechodzimy przez kolejne kroki analizy rentowności firmy.
Rozmawiamy o tym, jak wykonać analizę rentowności swojej firmy:
✔️ Zbieramy wszystkie potrzebne dane
✔️ Przechodzimy przez kolejne kroki analizy
✔️ Pracujemy na konkretnych przykładach.
Podsumowanie
Podsumowując, optymalizacja procesów produkcyjnych jest niezwykle ważnym elementem w dążeniu przedsiębiorstw produkcyjnych do zwiększenia efektywności, redukcji kosztów i poprawy jakości produktów. Należy pamiętać, że obniżenie kosztów przenosi się na wyższą marżę bez zmiany ceny sprzedaży. Wykorzystanie różnorodnych metod i narzędzi, takich jak Just in Time (JIT), automatyzacja, metoda 5S, modelowanie procesów oraz inne narzędzia lean, stanowi fundament dla skutecznej optymalizacji.
Technologia odgrywa zasadniczą rolę w tym procesie, oferując nowe możliwości poprawy przepływu pracy i komunikacji. Oprogramowanie do zarządzania produkcją, takie jak systemy ERP, przyczynia się do lepszego planowania, kontroli i integracji różnych aspektów procesu produkcyjnego. Zastosowanie nowoczesnych technologii w produkcji, takich jak robotyka i automatyzacja, przyspiesza produkcję, jednocześnie zapewniając wyższą jakość i spójność produktów.
Kluczowe jest również efektywne zarządzanie procesami produkcyjnymi na poziomie miejsca pracy, co obejmuje zarówno wprowadzenie optymalizacji procesów, jak i wspieranie komunikacji między pracownikami. Skuteczna komunikacja i koordynacja są niezbędne do wdrożenia i utrzymania efektywnych zmian w procesach produkcyjnych.
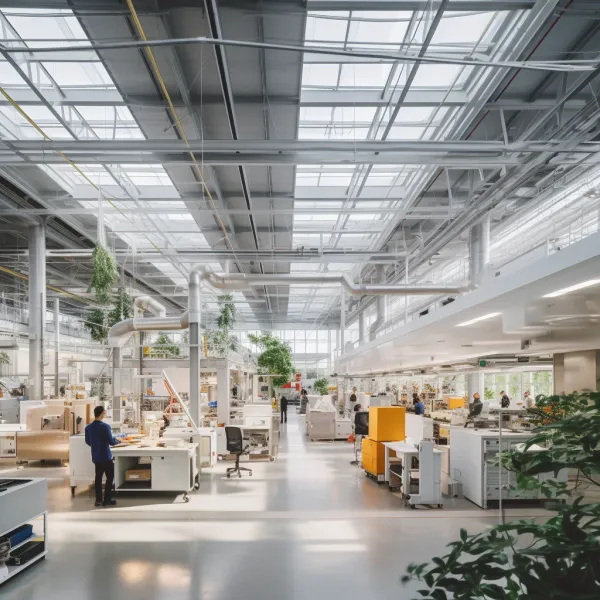
Ostatecznie, cały proces optymalizacji wymaga zaangażowania na wszystkich szczeblach organizacji, od pracowników linii produkcyjnej po kadrę zarządzającą, oraz ciągłego dążenia do doskonalenia i innowacji. Firmy, które skutecznie wdrażają te strategie, są lepiej przygotowane do sprostania wyzwaniom rynkowym, zwiększając swoją konkurencyjność i zapewniając długoterminowy sukces.
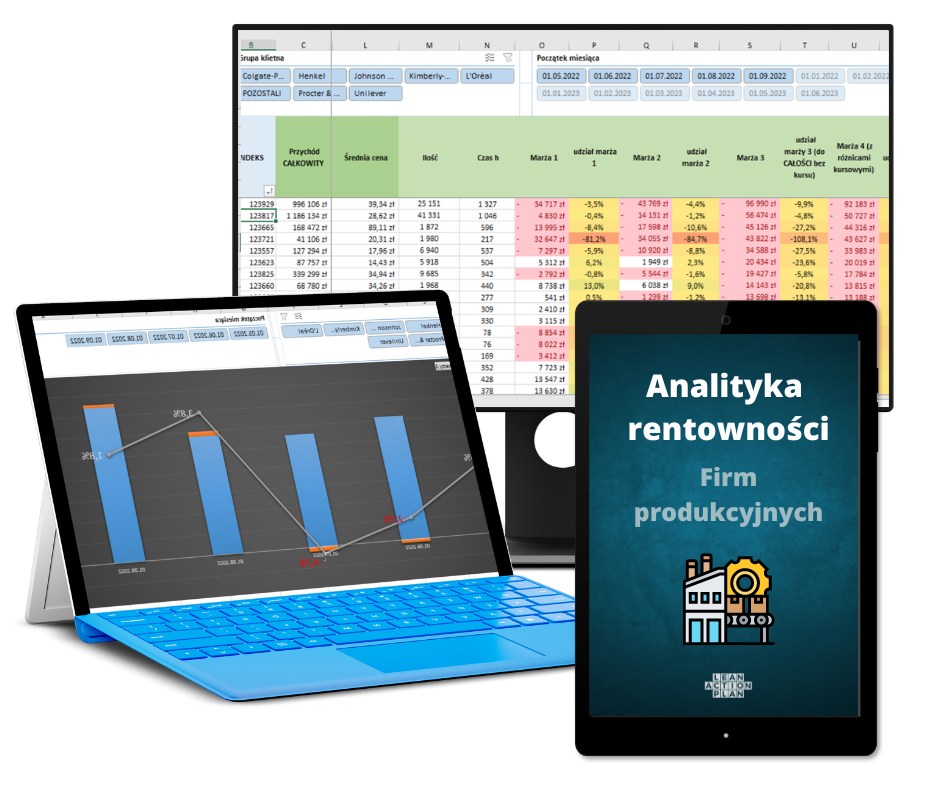