Wskaźnik OEE – jak obliczać i interpretować wyniki?
Jak to jest, że nowa linia miała wytwarzać 1000 sztuk na zmianę, a produkuje tylko 800? Czy wszystko rozbija się o wydajność, czy efektywność? Jeśli w Twojej firmie liczy się wskaźnik OEE, zastanawiałeś się może po co się to robi? Czy jest to machina do wyłapywania strat? A może bat na operatorów i służby utrzymania ruchu? A jeszcze w innej alternatywie źródło wskazania dodatkowych możliwości?
Pytanie o sens stosowania OEE to dopiero początek. W jeszcze większe czeluści rozmyślań prawdopodobnie zaprowadzi Cię kwestia zbierania danych i samych założeń ich gromadzenia. Nie trudno bowiem w tym przypadku doprowadzić do malowania trawy na zielono, podkręcania wyników, bądź ucinania skrzydeł zatrważająco niskimi procentami.
Gdzie w takim razie znaleźć w tym balans i słuszność?
W tym bardziej narzędziowym artykule, postaramy się wspólnie rozstrzygnąć:
Czym jest wskaźnik OEE?
Skrót OEE, w rozwinięciu Overall Equipment Effectiveness to tzw. Całkowita Efektywność Wyposażenia. Jest to zatem wskaźnik ukazujący efektywność wykorzystania maszyn oraz urządzeń w przedsiębiorstwie. Jego główną składową jest miara czasu, a wynik obliczeń w dużym uproszczeniu przedstawia jaką część planów oraz oczekiwań udało się zrealizować przy obecnym poziomie organizacji procesów.
Wskaźnik OEE ujawnia również marnotrawstwa występujące w procesach, dając tym samym szansę na ich wyeliminowanie, drogą prostych, podstawowych działań, niewymuszających kosztownych inwestycji. Każde takie badanie przeprowadzone z głową, bez pobudki do podkręcania wyników, wpisuje się również w ideę metodyki Lean Management.
Sprawdź: Narzędzia Lean
Z czego składa się wskaźnik OEE?
Najbardziej podstawowy wzór wskaźnika OEE jest iloczynem trzech składowych parametrów:
- Dostępności
- Wykorzystania
- Jakości
Chcąc trochę bardziej wnikliwie podejść do jego analizy, warto dodać, że wśród składowych figurują jeszcze dwa dodatkowe elementy, mające znaczenie dla rozpoczęcia obliczeń. Jest to:
- Czas zamówiony
- Czas operacyjny
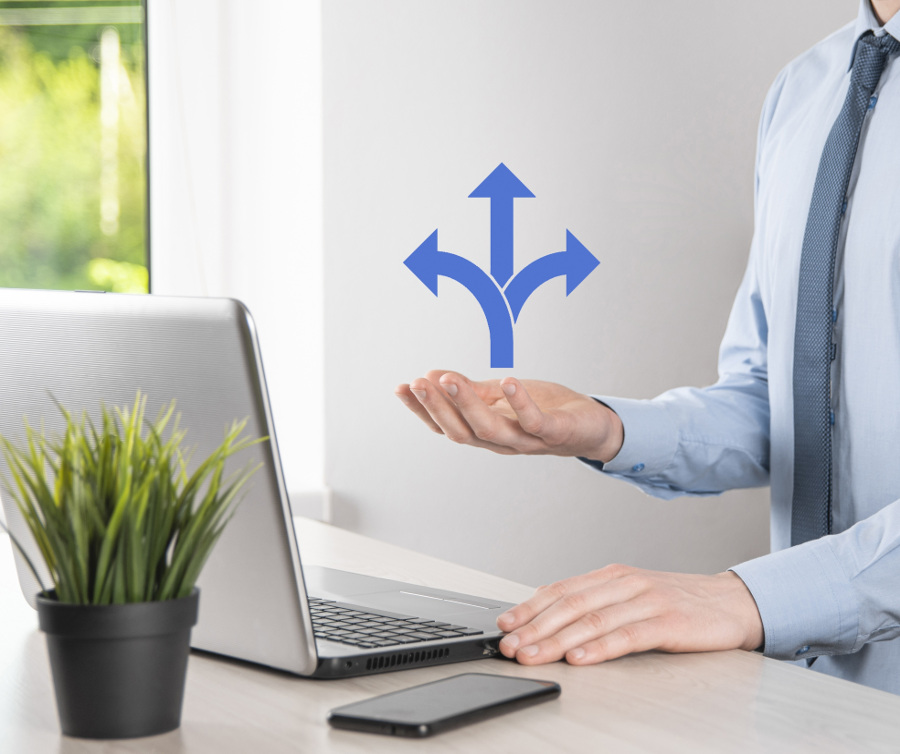
Wskaźnik dostępności
Jeśli chodzi o dostępność maszyn, jest to najprościej mówiąc, czas, w którym mogą one pracować bez zakłóceń. Żeby określić poziom dostępności musimy skonfrontować czas operacyjny, czyli ten, który został zaplanowany do realizacji procesu, z czasem nieprzewidzianych zdarzeń, które ograniczyły te możliwości.
Czym będzie w takim razie czas operacyjny? Słowo „zaplanowany” ma tutaj nieprzypadkowe znaczenie. Jest to czas, pomniejszony o przewidziane i planowane przestoje wynikające z konieczności wykonania remontów, przeglądów, bądź wszelkich innych działań (np.: planowane przezbrajanie).
Dalej idąc, podczas realizacji procesu możemy mieć również do czynienia z szeregiem nieplanowanych oraz wymuszonych zdarzeń takich jak:
- Awarie, a w tym także ustawianie maszyn po ich wystąpieniu,
- Uruchomienia oraz przezbrojenia, które przekraczają normatywne założenia,
- Regulacje, czyszczenie, drobne konserwacje,
- Oczekiwanie na zrównanie cyklu z operatorem, dostarczenie surowców, opakowań do składowania itd.
W tym momencie obliczenia składają się w całość. Wynikiem dostępności jest różnica między czasem operacyjnym (czyli planowanym czasem produkcji), a łącznym czasem nieprzewidzianych zdarzeń.
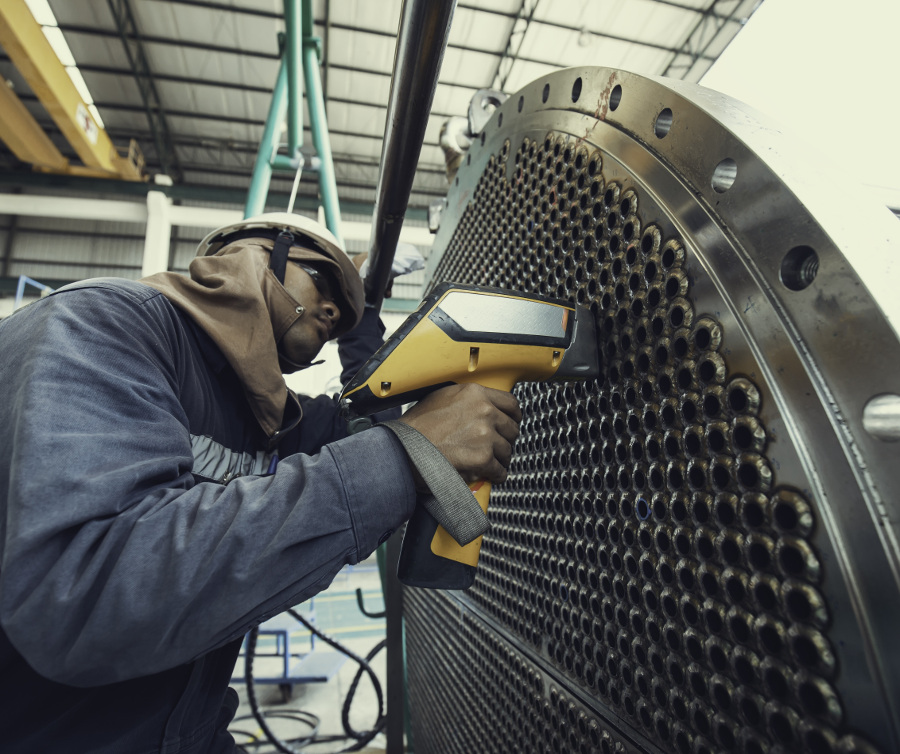
Wskaźnik wykorzystania
Drugim parametrem jest wykorzystanie, które konfrontuje wcześniej obliczony czas dostępny z kolejnym zestawem zakłóceń procesowych.
Jeżeli obliczymy, że nasz dostępny czas wynosi 350 minut, z założenia, maszyna działająca z maksymalną wydajnością powinna pracować właśnie tyle. Z tym, że rzeczywistość dyktuje zupełnie inne warunki. W każdej chwili, w procesie produkcji może dojść do:
- Mikroprzestoju,
- Obniżenia prędkości pracy maszyny, który może wynikać z kwestii technologicznych, spadków napięć, bądź także błędu operatora,
- Konieczności wymiany wewnętrznego narzędzia, czy oprzyrządowania,
- Konieczności uzupełnienia surowca,
- Konieczności usunięcia wadliwego wyrobu z maszyny,
- Straty prędkości spowodowanej: znużeniem pracownika, nadmiernym przeciążeniem, brakami w obsadzie, nieergonomicznymi warunkami pracy itd.
W efekcie takich incydentów, musimy ponownie pomniejszyć możliwości, otrzymując dane o faktycznym czasie regularnej produkcji.
Wskaźnik jakości
To jednak jeszcze nie koniec. Jakby tego wszystkiego było mało, po wykorzystaniu przychodzi kolejny parametr, jakim jest jakość, która sprowadza obliczenia do poziomu regularnej, ale i poprawnej produkcji. Wskaźnik jakości wylicza się poprzez stosunek liczby zgodnych produktów, do liczby wszystkich wyprodukowanych wyrobów. Oczywiście wynika to z faktu, że maszyna pracowała wydając niezgodności, a co za tym idzie, nie tylko wpłynęło to na utratę surowca, ale również czasu.
Żeby wszystko było bardziej zrozumiałe, spróbujmy przeprowadzić analizę start efektywności na przykładzie, z wykorzystaniem konkretnych wzorów i danych.
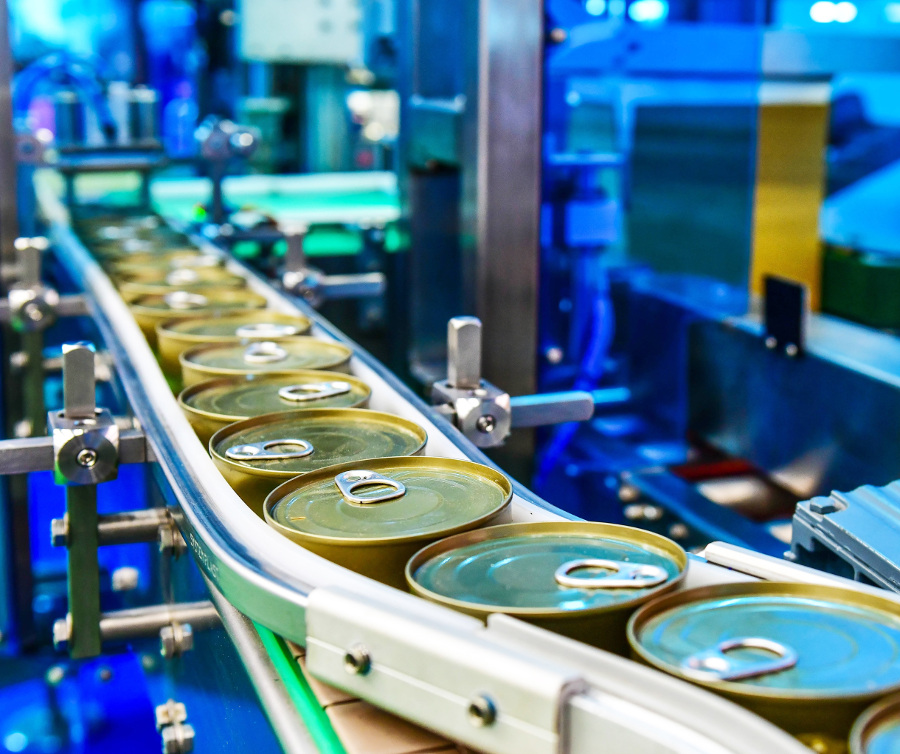
Szkolenie Online z CERTYFIKATEM
TPM – Totalne utrzymanie ruchu
Projektowanie wdrożenia TPM w organizacji
Wyliczanie wskaźnika OEE
Zwiększanie wykorzystania zdolności produkcyjnych
Wolisz naukę offline? Przygotowaliśmy szkolenie zamknięte TPM, które w przystępny sposób przeprowadza pracowników przez elementy metodologii TPM. Odbywa się ono w formie warsztatów zamkniętych w Twojej firmie i jest dedykowane zarówno pracownikom, jak i zarządowi.
Przykładowe obliczenie wskaźnika OEE
Wytwarzamy w zakładzie produkcyjnym towar X.
- Naszym czasem zamówionym, będzie całkowity czas produkcji, a konkretnie ramy czasowe, w których proces miał zostać wykonany.
- Produkcja towaru X ma się odbyć od czwartku (6:00) do poniedziałku (10:00).
- Zakład pracuje na trzy zmiany po 8h, w soboty pracuje tylko jedna zmiana, w niedziele pracownicy mają wolne.
- Czas zamówiony to 24h (czwartek) + 24h (piątek) + 24h (sobota) + 24h (niedziela) + 4h (poniedziałek) = 100h
- Do obliczenia czasu operacyjnego potrzeba nam informacji o planowanych postojach. Zaliczają się do nich: 16h (2 wolne zmiany z soboty) + 24h (wolna niedziela) + 1h (co piątkowy przegląd) + 4h (łączny normatywny czas przezbrojeń) + 2h 40 min (przerwy na posiłki).
- Czas operacyjny wynosi 100h – 47h 40 min = 52h 20 min
- Do obliczenia czasu dostępnego musimy:
- sprawdzić czy przezbrojenia odbyły się zgodnie z założonym czasem – ale niestety nie, ponieważ wydłużyły się łącznie o 2h 10 min,
- zweryfikować czas awarii – 2h 35 min.
- Czas dostępny wynosi zatem 52h 20 min – 4h 45 min = 47h 35 min, a wskaźnik dostępności wynosi (47,583*100%)/52,33 = 90,92%
- Do obliczenia dostępności można również skorzystać ze wzoru:
- Następnie przechodząc do parametru wykorzystania, musimy przeanalizować jakie zakłócenia spowodowały utratę wydajności. W naszym scenariuszu wystąpiły:
- 4 mikroprzestoje technologiczne,
- Kilkadziesiąt mikroprzestojów spowodowanych poprzez czynnik ludzki (uczulenie u jednego z operatorów – kichanie, pracownik musiał przecierać nos i dawkować krople – życie),
- 20 operacji uzupełniania surowca,
- Zdarzenia, które przez swój krótki czas trwania nie sposób było zarejestrować, jednak prawdopodobnie wpłynęły na straty prędkości.
- No ale właśnie, przez to, że tak naprawdę ciężko zarejestrować czas zakłóceń regularnej produkcji, sposób liczenia parametru wykorzystania jest odwrócony. Zamiast sumować czas strat, liczony jest czas jaki potrzebny jest na wykonanie zamówionej ilości produktów. Pomoże w tym wzór:
- Znając czas cyklu (10s) oraz ilość wyrobów (14 520 sztuk – łącznie z defektami), możemy zatem określić, że na wyprodukowanie całej partii potrzeba nam łącznie 40 h 20 min (10s * 14 520 szt / 60 / 60).
- Tym samym oznacza to, że łączny czas zakłóceń wyniósł ponad 7 godzin, a wskaźnik wykorzystania ukształtował się na poziomie (40,33*100%)/47,583 = 84,75%.
- Przejdźmy do trzeciego elementu wskaźnika OEE, aspektu jakości. Realizowana produkcja miała zapewnić 14 000 sztuk wyrobów gotowych dla klienta. Aby skompletować zamówienie wytworzono łącznie 14 520 sztuk. Co w prostym równaniu sprowadza nas do wniosku, że mamy do czynienia aż z 520 sztukami wadliwymi.
- Współczynnik jakości obliczamy w prosty sposób (14 000*100%)/14 520 = 96,41%. Można również skorzystać ze wzoru:
- W tym momencie przychodzi wyczekana pora, na określenie ile wynosi wskaźnik OEE?
Pomnóżmy składowe wskaźniki:
90,92% (dostępność) * 84,75% (wykorzystanie) * 96,41% (jakość) = 74,29%
Wartość OEE = 74,29%
Jak interpretować wyniki? W zakładzie produkcyjnym, w zaplanowanym czasie operacyjnym wynoszącym 52h 20 min, maszyny przepracowały efektywnie przez 74,29% czasu.
Aby znaleźć tu jakiś punkt odniesienia popularnie przywoływaną wartością wskaźnika OEE Overall Equipment Effectiveness (World Class) jest 85% (90% dostępność, 95% wykorzystanie, 99% jakość), która ma świadczyć o bardzo wysokim poziomie efektywności wykorzystania maszyn. W rzeczywistości osiągnięcie takiego wyniku jest nie lada wyzwaniem dla przedsiębiorstw produkcyjnych.
Nad wynikiem można jednak zawsze popracować… choćby wyciągając wnioski z pewnych sytuacji.
Zobacz również: Standaryzacja czasu pracy
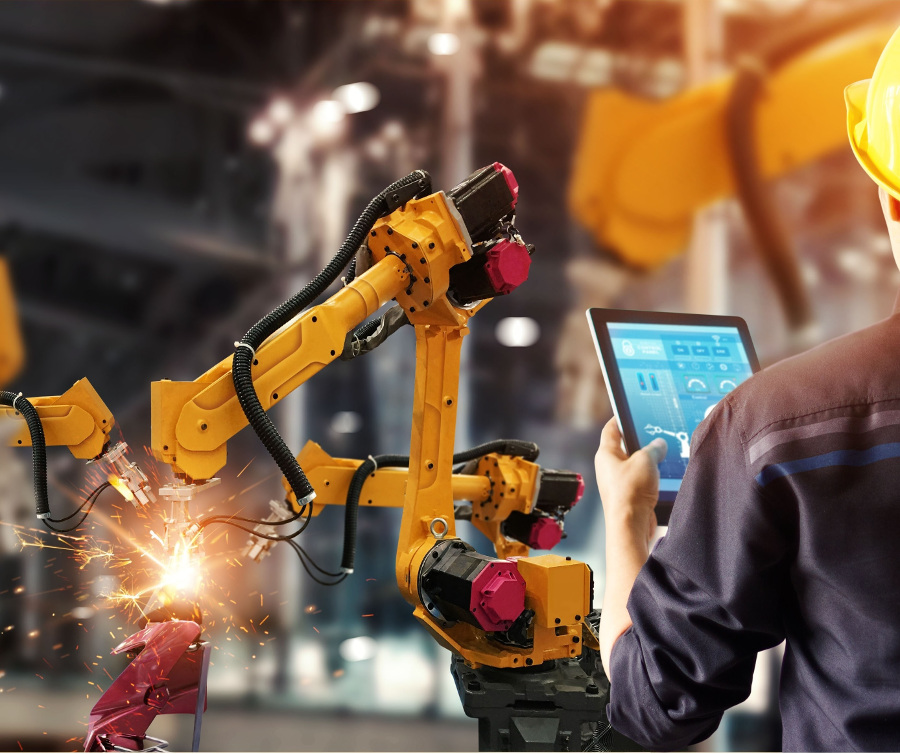
Najczęstsze wpadki przy obliczaniu OEE
To naprawdę niezwykle istotny temat, zarówno w kategorii założeń, obliczeń, interpretacji, jak i samego w sobie sensu opracowywania wskaźnika OEE. Weź pod uwagę jakie błędy popełniają niektóre przedsiębiorstwa i postaraj się wystrzegać ich powielania:
- Planowane przestoje nie powinny być traktowane jako strata – i teraz musisz mnie dobrze zrozumieć. Weźmy pod uwagę scenariusz, w którym w jednej z firm są dwa działy szlifierskie, jeden pracuje na 3 zmiany, drugi na 2. Gdybyśmy policzyli każdy case osobno, wyniki prezentowałyby się bardzo przyzwoicie. Jednak gdybyśmy założyli, że brak trzeciej zmiany na jednym z działów jest stratą, jeden z wyników spadłby drastycznie. Czy to jednak świadczy o nieumiejętnej pracy operatorów, albo kompletnie niezorganizowanej brygadzie UR? Absolutnie! Jest to ewentualnie luka stanowiąca potencjał do wykorzystania (co bardziej w tym przypadku należy skonfrontować z działem sprzedaży oraz planistami).
- Ręczne, analogowe liczenie strat na wykorzystaniu może skutkować otrzymaniem błędnego wyniku – jeżeli zainwestowaliście w rejestratory, bądź detektory, które są podpięte do maszyny, wtedy faktycznie może mieć to sens, jednak w przypadku kiedy nie możecie liczyć na wsparcie zaawansowanego rozwiązania, które uchwyci za Was takie detale, naprawdę wręcz niemożliwym będzie rzetelne odwzorowanie strat. Stąd warto, abyś trzymał się wzoru określonego w przykładzie obliczania wartości OEE (3 punkt artykułu).
Zamiast sumować czas strat, policz czas jaki potrzebny jest na wykonanie zamówionej ilości produktów.
- Różnice w interpretacji strat dla poszczególnych parametrów składowych OEE – nie do końca jest to błędem, ale zdecydowanie może być potraktowane jako wpadka przy analizie danych. Przykładowy, nieprzewidziany przestój, który jest spowodowany opóźnieniem w dostarczeniu oprzyrządowania maszyny, może być przypisany jako ograniczenie dostępności. Jednak jeśli zostanie on w szybki sposób rozwiązany, można by było przypisać go do straty na wykorzystaniu. W zależności od decyzji, uzyskasz inny wynik jednego lub drugiego parametru. Wszystko zależy od świadomości oraz kryteriów interpretacji. Najważniejsze, żebyś umiał wyciągnąć z tego odpowiednie wnioski.
- Sztuki wadliwe przy rozruchu – tutaj ponownie kłania się indywidualne spojrzenie na sprawę. Jeśli klient został zakontraktowany na produkcję konkretnej ilości sztuk wyrobów oraz określony naddatek na straty rozruchowe, z punktu widzenia wyliczania parametru jakości, te nie muszą być brane pod uwagę, ponieważ nie potrzeba czasu na ich powtórne wykonanie.
- Nierzetelny sposób zbierania danych – sprawa wydaje się jasna, jeśli nie będziecie zbierać danych w sposób dokładny, podchodząc do nich zbyt wybiórczo, uzyskane wyniki nie będą odwzorowywać faktycznego wskaźnika wykorzystania maszyn i nie ukażą jaka jest efektywność produkcji. To również oczywiste, że musimy liczyć się z dopuszczeniem pewnego marginesu błędu, ponieważ szansa, że operator zarejestruje każdą potencjalną stratę czasu pracy jest nikła.
Zobacz również: Jak skutecznie zbierać dane z produkcji?
Jak realnie poprawić wartość wskaźnika OEE?
Wskaźnik OEE ma na celu wskazać jak efektywnie pracują maszyny w zakładzie. Skoro już wiemy, co może ograniczać dostępność, wykorzystanie i jakość, możemy rozpracować również plan działań, który zredukuje poziom strat.
Wprowadzenie zmian oraz usprawnień może dotyczyć dokładnie każdej płaszczyzny:
- stworzenia nowych instrukcji,
- określenia schematu komunikacji, kiedy w rytm produkcji wkradną się przestoje niezaplanowane,
- skrócenia czasu przezbrojeń,
- poprawy technologii, która wpłynie na wydajność maszyn, wydajność produkcji,
- modyfikacji systemu detekcji wad,
- przeprowadzenia szkoleń,
- zmienienia harmonogramu przeglądów maszyn.
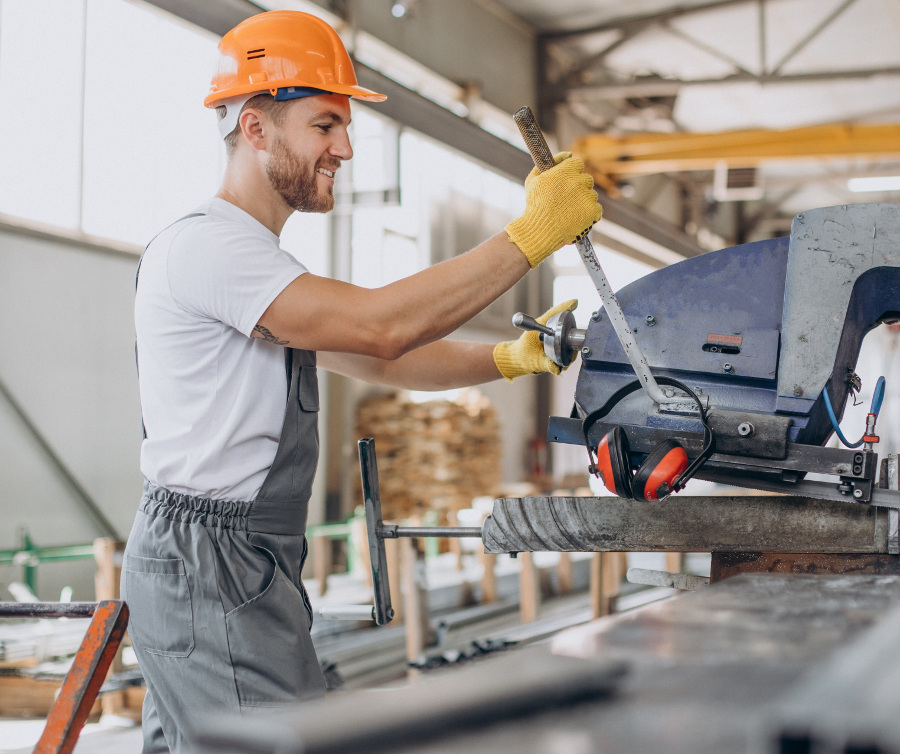
Nie warto zabierać się też za wszystko na raz. W wyłonieniu najbardziej newralgicznych obszarów pomoże Ci bardzo przystępna reguła Pareto, a dokładnie diagram, który ją obrazuje. Z wykorzystaniem tego prostego narzędzia będziesz mógł ustalić, które działania powinny być dla Ciebie największym priorytetem.
Idąc jednak jeszcze dalej, nie patrząc jedynie na oblicze strat, warto wspomnieć, że wskaźnik OEE może również służyć do prezentowania dodatkowego potencjału. Punkt widzenia zależy od punktu siedzenia. Ale tutaj też oczywiście musisz być czujny w interpretacji i podejść do sprawy zdroworozsądkowo. Nie trudno jest coś powiedzieć, znacznie gorzej jest wziąć za coś odpowiedzialność. Jednak mierząc szerzej…
Badanie wskaźnika OEE w takim kontekście może nakłaniać do:
- zwiększania zbytu,
- poszerzania planów sprzedaży,
- poszerzania asortymentu (w celu uzupełnienia luk czasowych bez produkcji),
- otwierania się na nowe rynki,
- zwiększania pozycji konkurencyjnej,
- [ewentualnie uruchamiania kolejnych zmian].
Poszukujmy rozwiązań naszych problemów, mierzmy nowymi alternatywami rozwoju. Taki cel wskaźnika Całkowitego Wykorzystania Wyposażenia wydaje się dużo bardziej stosowny, niż w przypadku popisywania się zawyżonymi liczbami przed audytorem, bądź kiwania palcem na pracowników (co firmy produkcyjne lubią bardzo robić).
Co ważne, używając słowa cel, należy mieć na myśli kierunek w jakim zmierza organizacja, a nie samą w sobie wartość wskaźnika. Ona powinna być jedynie odzwierciedleniem konkretnych działań.
A jaka jest Twoja perspektywa?
Szkolenie Online z CERTYFIKATEM
Wskaźniki OEE, MTTR, MTBF wg normy IATF
- Znajomość podstaw standardu IATF 16949:2016 oraz jego wymogów w kontekście TPM.
- Wyznaczanie celów dla utrzymania ruchu.
- Zapoznanie z pojęciem efektywności wyposażenia.
- Umiejętność wskazania miejsca powstawania poszczególnych składników OEE.
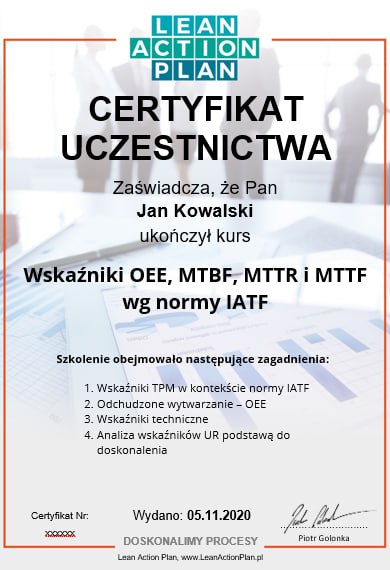
Chcesz monitorować wydajność maszyny lub linii produkcyjnej, zbierać i wykorzystywać dane, by poprawić efektywność? Sprawdź dedykowaną ku temu aplikację wspierającą efektywność – OEE Tools.
Na koniec, bardziej w formie ciekawostki, wskaźnik OEE występuje również w nieco innym wydaniu – TEEP (Total Effective Equipment Performance). Ten wariant poszerza dotychczasowy wzór o czas operacyjny. Co prowadzi nas do scenariusza, w którym dla zapewnienia efektywności parku maszynowego nie ma mowy o żadnych postojach. Myślisz, że można by było wprowadzić takie rozwiązanie 24h/7?