Przykłady wdrożenia 5S – pokaż to swoim pracownikom
Jeśli tutaj trafiłeś, to z pewnością masz przed sobą projekt wdrożenia metody 5S w swojej organizacji, bądź też w jej wybranym obszarze. Masz pewnie odpowiednie zaplecze merytoryczne, przygotowany wstępny plan działania, ale borykasz się z innym problemem.
- Jak przekonać pracowników o słuszności wprowadzenia zmian organizacyjnych?
- Jak zaangażować ich w prowadzenie, a dalej kultywowanie nowego standardu poszczególnych stanowisk pracy?
- W jaki sposób zainspirować ich, do uwolnienia własnych pokładów twórczości, które przełożą się na poprawę efektywności wykorzystania obszaru?
Dlatego też dzisiaj nie będziemy omawiać na czym polega 5S jako sama w sobie metoda organizacji miejsca pracy. Dostaniesz gotową kartę przetargową dla pracowników, czyli kompleksowe omówienie przykładów przed i po wdrożeniu, które stanowią najbardziej trafną formę prezentacji korzystnych zmian dla przedsiębiorstwa. Tak też przejdziemy kolejno przez takie płaszczyzny jak:
- Bez 0S nie zorganizujesz miejsca pracy
- Organizacja miejsca pracy – zacznij od selekcji – 1S
- Drugi etap wdrożenia metody 5S – systematyka
- 3S to nie tylko sprzątanie miejsca pracy
- Czwarty krok – standaryzacja
- Samodyscyplina – utrzymanie jakości stanowiska pracy
- Lean Management i 5S w biurze
Jeśli natomiast chciałbyś trochę uporządkować sobie metodyczny grunt, zapraszam Cię, w formie wstępu do innego artykułu, dedykowanego założeniom tej metody.
A teraz zaczynajmy!
Bez 0S nie zorganizujesz miejsca pracy
„Jak sobie pościelisz, tak się wyśpisz” – to przysłowie stanowi idealną metaforę dla całego etapu przygotowania do wdrożenia metody 5S. Co więcej, można również powiedzieć, że wszystko co tu właśnie znajdziesz, będzie stanowiło podstawę do dalszych działań. Dlaczego?
0S to etap:
- Budowania świadomości czym jest 5S
- Promowania korzyści reorganizacji przestrzeni i eliminacji marnotrawstwa
- Wstępnego rozpoznania obszaru
- Warsztatów i szkoleń dla pracowników
- Powołania zespołu oraz lidera projektu
- Wybrania miejsca pilotażowego
Chcąc zaangażować pracowników i przekonać ich do działania, powinieneś dać im namacalny dowód, że to co będziecie wspólnie robić ma sens. W tym przypadku nie sprawdzi się długa prezentacja przesycona treścią i definicjami. Najlepsze będą przykłady z życia wzięte – czyli zdjęcia! Z ich pomocą będziesz w stanie nie tylko ukazać atuty, ale przede wszystkim w przystępny sposób poprowadzić ich po poszczególnych krokach postępowania, a także zainspirować do zgłaszania własnych pomysłów.
Na warsztatach możesz przekazać pracownikom jak wygląda wstępne rozpoznanie w innych firmach:
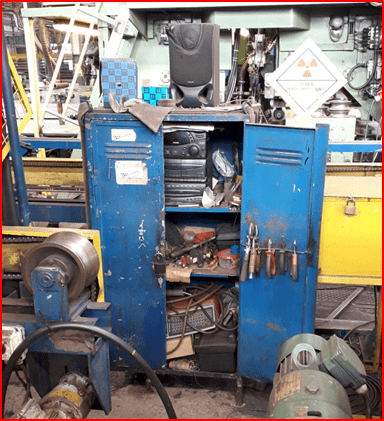
Podczas inicjującego obchodu wykonano zdjęcia newralgicznych obszarów, które charakteryzują się: widocznym nieładem, nieergonomicznym układem zagospodarowania, a także warunkami, które wymagają poszukiwania części i narzędzi. Po fotografii można również się spodziewać, iż na stanowisku znajduje się sporo zbędnych rzeczy, które niepotrzebnie absorbują cenną przestrzeń.
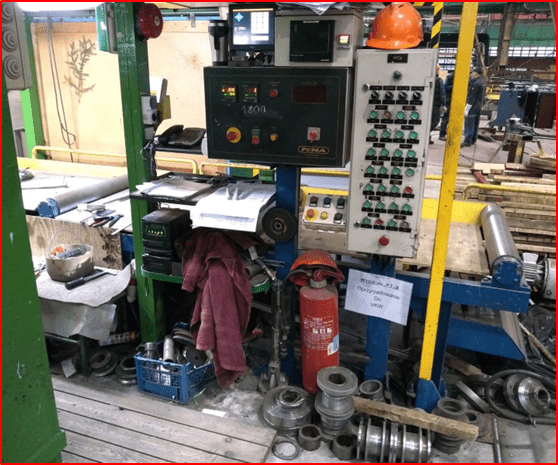
Na kolejnym stanowisku uchwycono dotychczasowy stan, rażąco uwidaczniający ryzyko uszkodzenia narzędzi pracy, a także brak możliwości ich ewidencji. Obsługa takiego miejsca jest nieintuicyjna i niesie za sobą zagrożenie popełnienia błędów poprzez operatorów w trakcie wykonywania procesu.
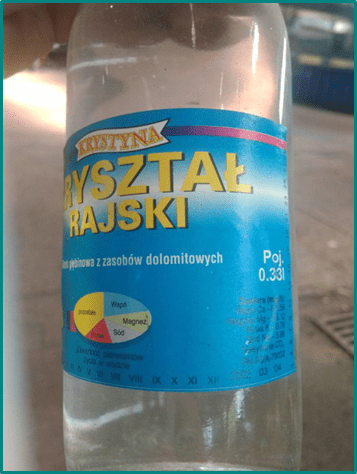
Przykład żartobliwy, jednak niezmiennie odzwierciedlający rzeczywistość pracy w „typowym” zakładzie produkcyjnym. Zwróć uwagę na datę przydatności spożycia – 2002 rok! Tak, takie skarby znajdują się z pewnością na niejednym ze stanowisk. Pokazują skłonność do chomikowania, a także brak nawyku utrzymania ładu w miejscu pracy.
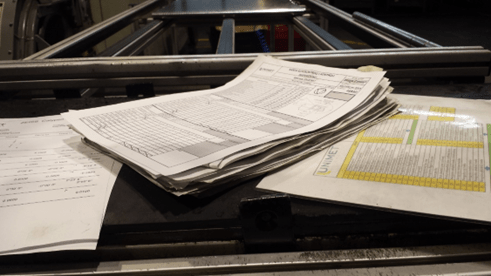
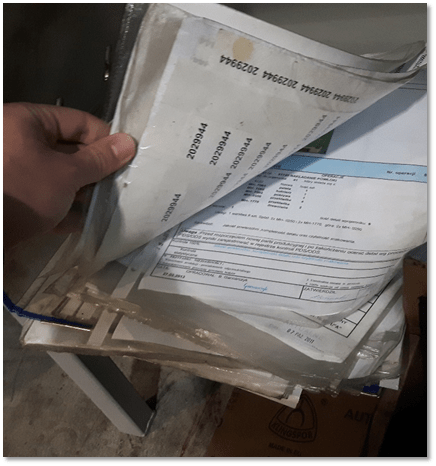
Papiery, wszędzie te papiery! Podczas obchodu wstępnego na hali uchwycono sposób przekazywania zleceń produkcyjnych, specyfikacji technologicznych, a także instrukcji stanowiskowych. Nie ma co się łudzić – takie ułożenie dokumentów może spowodować luki komunikacyjne, niedopatrzenia, opóźnienia w realizacji, a także oczywiście świadczy o tym, że obieg dotychczasowych standardów jest martwy.
Pokazanie tego typu fotografii operatorom jest dla nich pierwszym punktem zaczepienia. Mimo tego, iż ich środowisko pracy może być zupełnie inne, mogą dzięki temu porównać sytuację i powiedzieć „no patrz, u nas jest podobnie” albo „och, czyli jednak u nas nie jest tak źle”. To również świetna okazja do zredukowania poziomu oporu przed zmianą.
Pamiętaj również o tym, że oprócz zaprezentowania przykładów z zewnątrz, w trakcie waszego rekonesansu, także powinniście wykonywać fotografie. Uchwycenie stanu przed, a następnie skonfrontowanie go z sytuacją po wdrożeniu rozwiązań, będzie dowodem słuszności, a także źródłem motywacji do podjęcia kolejnych kroków przez zespół.
Przejdźmy dalej, bowiem inscenizacja stanu 0 to zaledwie przystawka do całej uczty.
Organizacja miejsca pracy – zacznij od selekcji – 1S
Drogą krótkiego wstępu podczas selekcji, głównym zadaniem jest dokonanie identyfikacji przedmiotów pracy poprzez podział na zbędne, niezbędne oraz takie, które mogą się przydać.
Głównie dla trzeciej kategorii pomocne będzie uruchomienie czerwonych etykiet, choć warto przy tym podkreślić, że i dla przedmiotów niepotrzebnych można zastosować taki sam system. Kampania czerwonych kartek pozwala rozwiać wątpliwości odnośnie tego czy:
- dany element można wyrzucić,
- w jaki sposób go zutylizować,
- gdzie go przenieść,
- jaka ilość jest faktycznie wykorzystywana,
- jaka jest częstotliwość jego użytkowania.
Chcąc przedstawić pracownikom istotę prowadzenia selekcji możesz pokazać im poniższe przykłady:
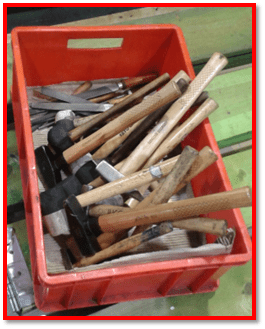
Podczas selekcji w jednym z działów w firmie X znaleziono aż 27 młotków! Jeszcze raz – 27 młotków w 1 dziale!!! A wcześniej pracownicy wyrywali sobie jeden, z rąk do rąk, ponieważ reszta była pochowana w regałach, bądź leżała za maszynami. W efekcie ustalono, że na danym stanowisku pracy wystarczą 4 młotki, a resztę narzędzi przekazano do innych obszarów.
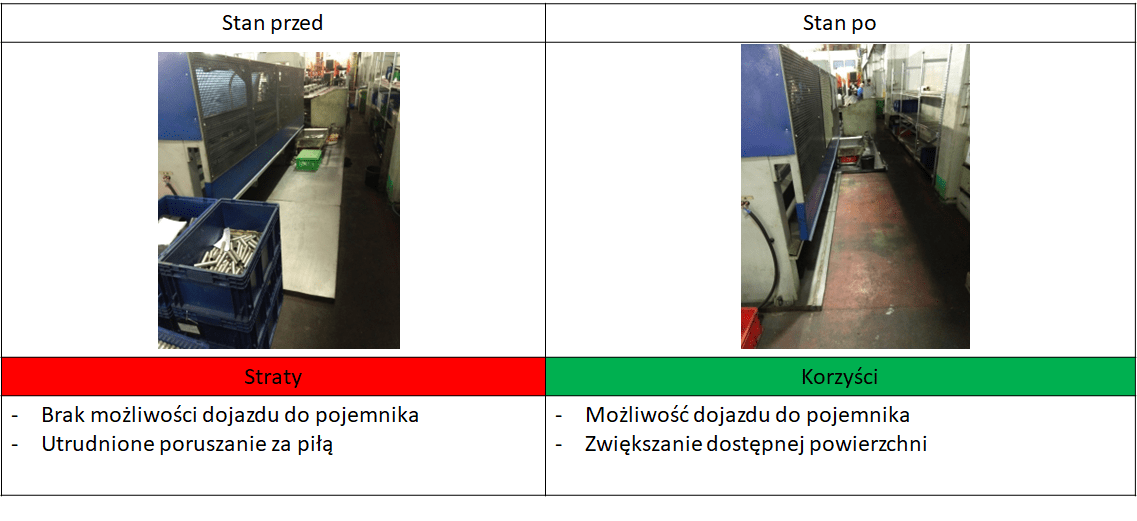
Chcąc przekonać pracowników produkcyjnych o tym, że sortowanie narzędzi pracy działa tylko i wyłącznie na ich korzyść, możesz pokazać im już na samym początku wizualizację stanu przed oraz po.
Powyższe case study przedstawia dwa scenariusze. W pierwszym z nich widać zablokowaną przestrzeń transportową, co wyraźnie utrudnia poruszanie się operatorom przy maszynie, a co więcej wymusza na nich konieczność ręcznego przenoszenia części, ponieważ nie ma możliwości bezpośredniego podjechania pojemnikiem. Tym samym wydłuża to czas trwania operacji, zwiększa ryzyko upuszczenia komponentów (czyli uszkodzenia), narusza zasady ergonomii pracy (chroniczne dźwiganie części), bezpieczeństwa pracy (ryzyko potknięcia się, bądź wywrócenia) i może powodować ludzką frustrację. Drugi scenariusz ukazuje natomiast obraz uporządkowanego miejsca pracy. W wyniku wyeliminowania zbędnych przedmiotów, dojazd został utorowany, rozwiązując wcześniejsze niedogodności.
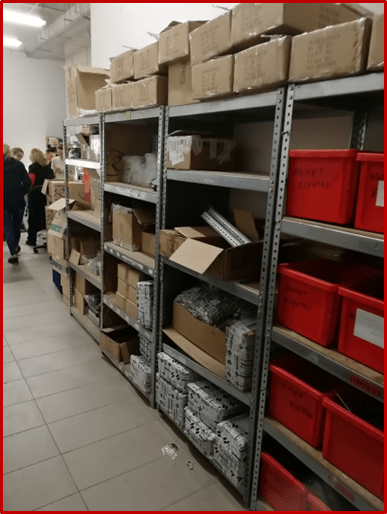
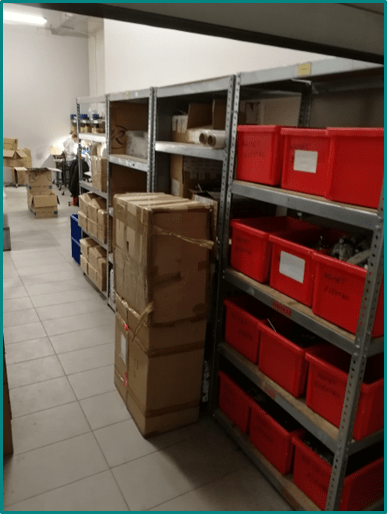
Ponownie w tym przypadku masz przed sobą prezentację stanu przed i po.
Obydwa zdjęcia ukazują układ regałów odkładczych. Pozornie może nie ma tutaj tak dużej różnicy. Warto jednak zwrócić uwagę, iż na fotografii po prawej stronie, w wyniku sortowania udało się wyeliminować wszystkie pojemniki umieszczone nad regałem, co świadczy o tym, że na stanowisku znajdowała się nadmierna ilość zapasów. Za tym zabiegiem idzie jeszcze jedna refleksja, dzięki temu, pracownicy nie muszą już sięgać wysoko po komponenty, ponieważ ich niezbędna ilość znajduje się w bardziej poręcznym miejscu, a bufor bezpieczeństwa składowany jest na magazynie. Układ pozostałych opakowań również jest nieprzypadkowy.
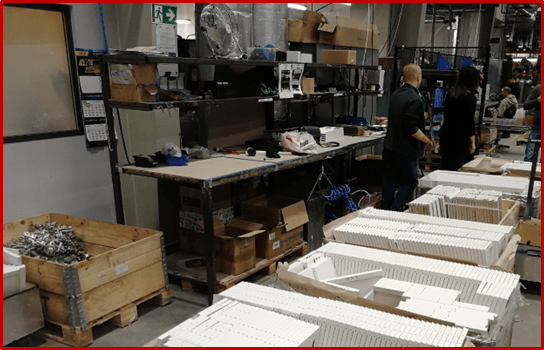
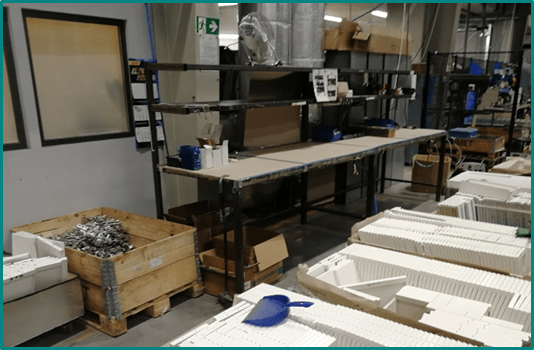
Na stołach roboczych, w wyniku selekcji wyeliminowano zbędne przedmioty i części, dzięki czemu zwiększyła się swoboda ruchów oraz jakość pracy operatora. Potrzebne narzędzia zostały ułożone na blatach, w zasięgu rąk, aby tym samym wyeliminować wszelkie zbędne ruchy.
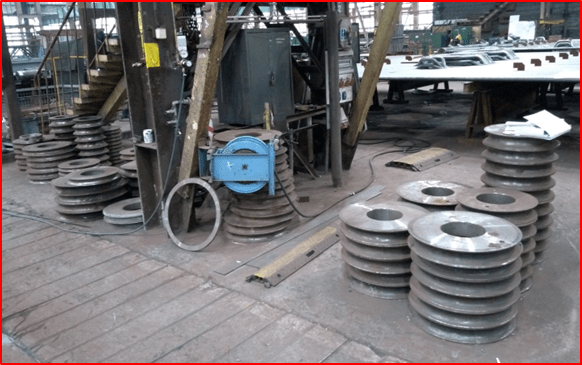
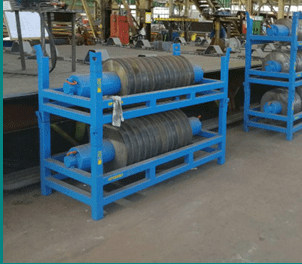
Kto by chciał przekładać wszystkie części, aby wyciągnąć którąś z dołu? Kto by chciał schylać się po każdą z nich, aby podnieść ją z nawierzchni hali produkcyjnej? Nikt by nie chciał! Ale ktoś jednak musiał! Przed selekcją… Wiele nie trzeba tłumaczyć. Dzięki zastosowaniu dedykowanych regałów, nie tylko udało się poprawić ergonomię pracy, ale również odzyskano przestrzeń, wprowadzono możliwość intuicyjnej identyfikacji elementów, ich ewidencji, a także zredukowano ryzyko wystąpienia uszkodzeń i popełniania błędów.
Szkolenie Online
Jak wdrożyć i utrzymać 5S na produkcji oraz zarządzanie wizualne
Jak rozpocząć wdrażanie 5S?
Jakie są działania 5S w poszczególnych krokach?
Pliki i formularze 5S do pobrania
Praktyczne przykłady zastosowania 5S
Preferujesz szkolenia stacjonarne?
Sprawdź szkolenie 5S – organizacja miejsca pracy oraz zarządzanie wizualne.
To praktyczne warsztaty, przeprowadzane w Twojej firmie, które są dostosowane do Waszych potrzeb. Mają na celu organizację miejsca pracy, co znacząco wpływa na zwiększenie efektywności.
Drugi etap wdrożenia metody 5S – systematyka
Po selekcji, przychodzi najwyższy czas na systematykę, czyli określenie optymalnych miejsc ułożenia wszystkich przedmiotów na stanowisku, bądź na hali produkcyjnej.
Opowiadając o tym etapie, powinieneś nastawić zespół na konieczność:
- ustalenia standardowych miejsc pobierania i odkładania części,
- ujednolicenia nazewnictwa i kodowania elementów,
- stworzenia identyfikacji części, etykiet oraz innych oznaczeń,
- wprowadzenia pozostałych elementów zarządzania wizualnego (tablice cieni, linie graniczne, pola odkładcze itd.),
- ustalenia schematu pobierania przedmiotów zgodnego z zasadami ergonomii i bezpieczeństwa pracy ( ciężkie przedmioty – na dolnych regałach lub na podłodze, lżejsze elementy – w wyższych strefach miejsc składowania, przedmioty wykorzystywane najczęściej – możliwie w zasięgu rąk).
Jeżeli w Waszej firmie produkcyjnej, operatorzy nigdy wcześniej nie słyszeli o metodzie 5S, przykłady wdrożenia szczególnie przydadzą się właśnie podczas opisywania istoty systematyki. Ta faza jest idealną okazją do uruchomienia pokładów kreatywności.
Ponownie i tutaj, swoją prezentację możesz oprzeć o kilka wstawek stanu przed i po zmianach.
Na powyższych fotografiach, ukazano dwa scenariusze składowania pasów. W pierwszym układzie brakowało standardowego miejsca odkładczego, co naturalnie powodowało konieczność poszukiwania pasów, czyli tym samym generowało zbędne ruchy oraz straty czasu. W drugim układzie określono dedykowaną przestrzeń, a także zamontowano wieszaki.
Na przykładzie, pozornie, nie widać znaczących zmian. Jednak w wyniku podjętych działań dokumenty otrzymały stałe miejsca przechowywania, a także czytelny i intuicyjny system identyfikacji, z wykorzystaniem etykiet. Trzymanie się tak ustalonego schematu, spowodowało automatycznie większy porządek na stanowisku. Co więcej, ta prosta procedura sprawiła, że obsługa stanowiska stała się możliwa nawet dla osób trzecich, które nie mają na co dzień styczności z danym obszarem.
Systematyka ułożenia przedmiotów pracy naturalnie potwierdza zasadność wcześniejszej selekcji. Na stanowisku znajdują się tylko niezbędne elementy, w sprecyzowanej, potrzebnej ilości, a także w wyznaczonym miejscu. Taka aranżacja przestrzeni nie tylko zwiększa intuicyjność obsługi, pozwala również na płynną weryfikację czy w obszarze nie niektórych brakuje elementów, bądź czy nie należy uzupełnić optymalnych stanów. Wystarczy spojrzeć na zdjęcia. Przyglądając się fotografii po lewej stronie, gdyby nie było tam rękawiczek, byłbyś w stanie stwierdzić, że są one potrzebne? W konfrontacji, patrząc na zdjęcie po prawej stronie, gdyby w pojemniku z etykietą o treści „rękawice”, jednak by ich tam nie było, miałbyś taką samą zagwostkę? Zdecydowanie nie. To jasne, że albo któryś z operatorów właśnie ma je na swoich dłoniach, albo trzeba udać się do działu zaopatrzenia po nową parę.
Kolejny przykład zagospodarowania przestrzeni na dokumentację produkcyjną.
Przykład organizacji miejsca składowania kluczy oraz pozostałych narzędzi. W tym przypadku warto dodać, że składowanie części „luzem” – jak w stanie przed systematyką, uniemożliwia sprawne zweryfikowanie czy wszystkie wykorzystywane na stanowisku przedmioty są sprawne i zdatne do użytkowania. Tym samym powoduje to nie tylko straty czasu na poszukiwanie, ale również zagraża narastającym opóźnieniom w wyniku niekompletnego oprzyrządowania do realizacji procesu produkcyjnego, bądź czynności konserwacyjnych.
Scenariusz po lewej stronie:
– „Ej! Gdzie jest moja suwmiarka?”
– „Leży gdzieś tam…”
Scenariusz po prawej stronie:
– brak pytań –
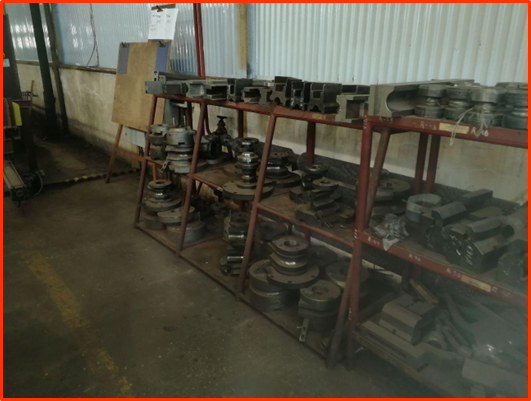
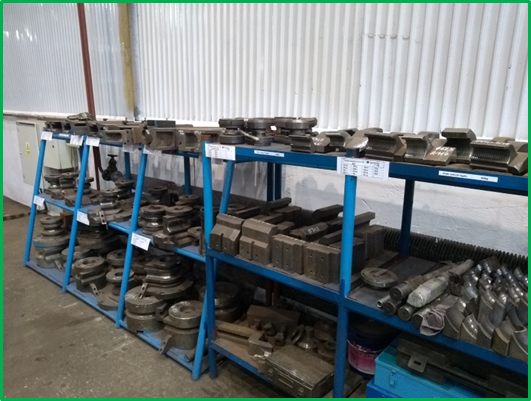
Scenariusz po lewej stronie:
– „Podaj mi proszę sworzeń fi 50 mm i tuleję A001”
– „yyy…ups…, daj mi trochę czasu”
[ 15 minut później ]
– „Sworzeń mam, ale nie wiem o którą tuleję Ci chodzi”
Scenariusz po prawej stronie:
– „Podaj mi proszę sworzeń fi 50 mm i tuleję A001”
– „Już sięgam!”
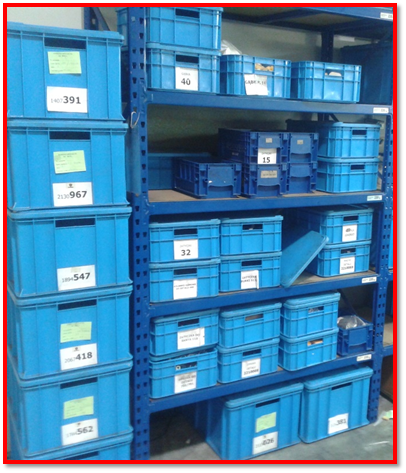
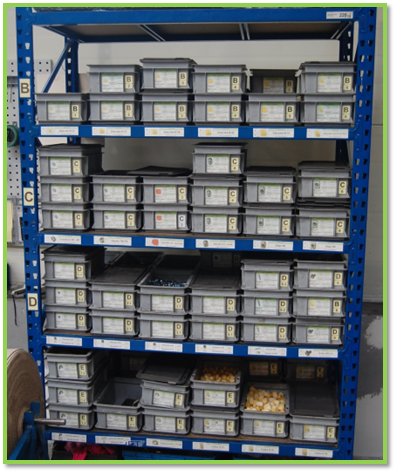
Kolejny przykład. W obszarze dotychczas funkcjonał już pewien system identyfikacji części. W wyniku systematyki, dokonano bardziej szczegółowego rozdziału miejsc składowania, aby wyeliminować konieczność poszukiwania elementów w ramach większych pojemników, w których znajdowały się inne podobne części. Co więcej, system etykiet wzbogacono o fotografie prezentujące wizualizację przedmiotów, a także kody kreskowe umożliwiające dokonanie zamówienia kolejnej partii z magazynu.
Poniżej jeszcze kilka pojedynczych case’ów dla Ciebie:
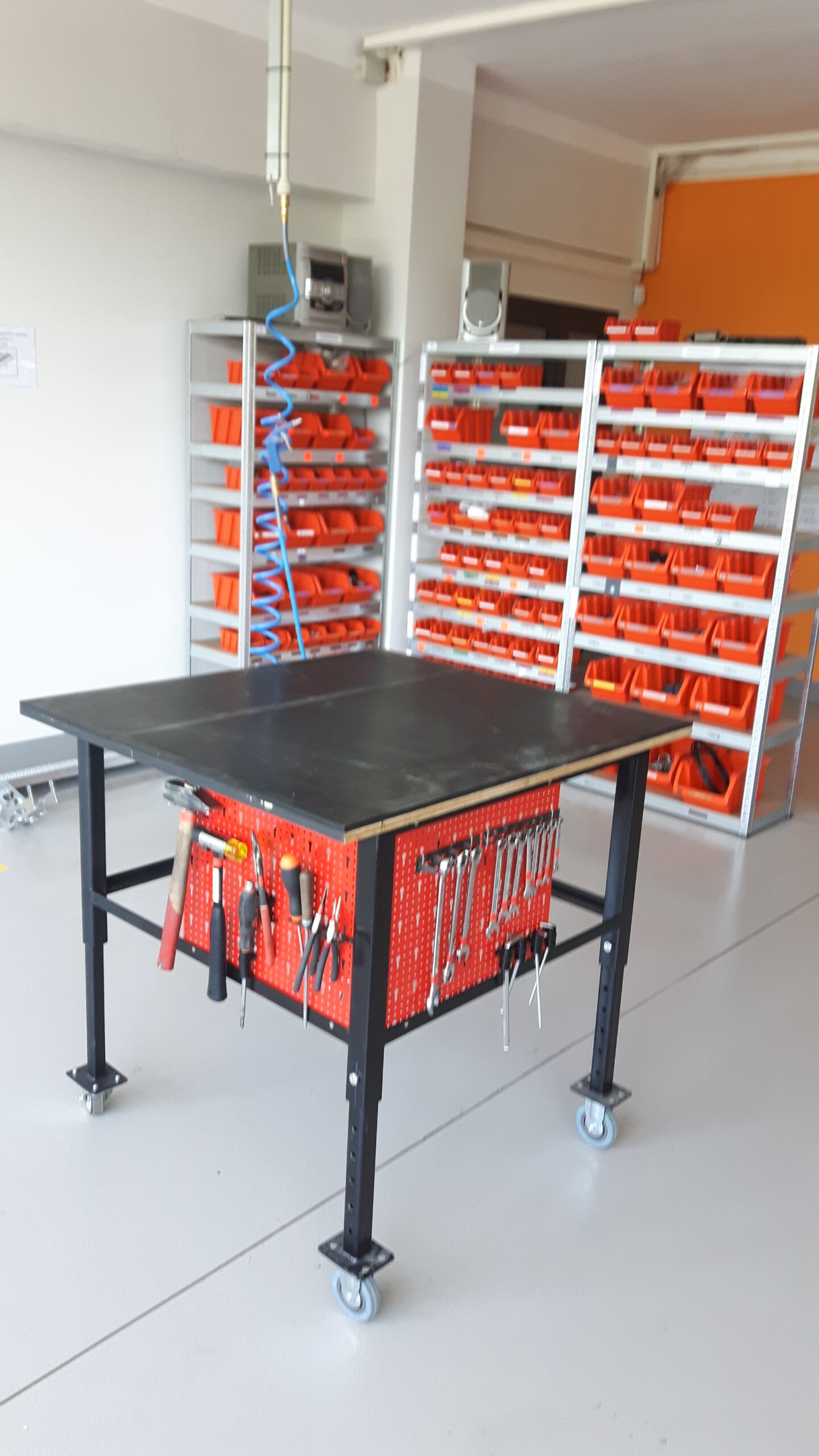
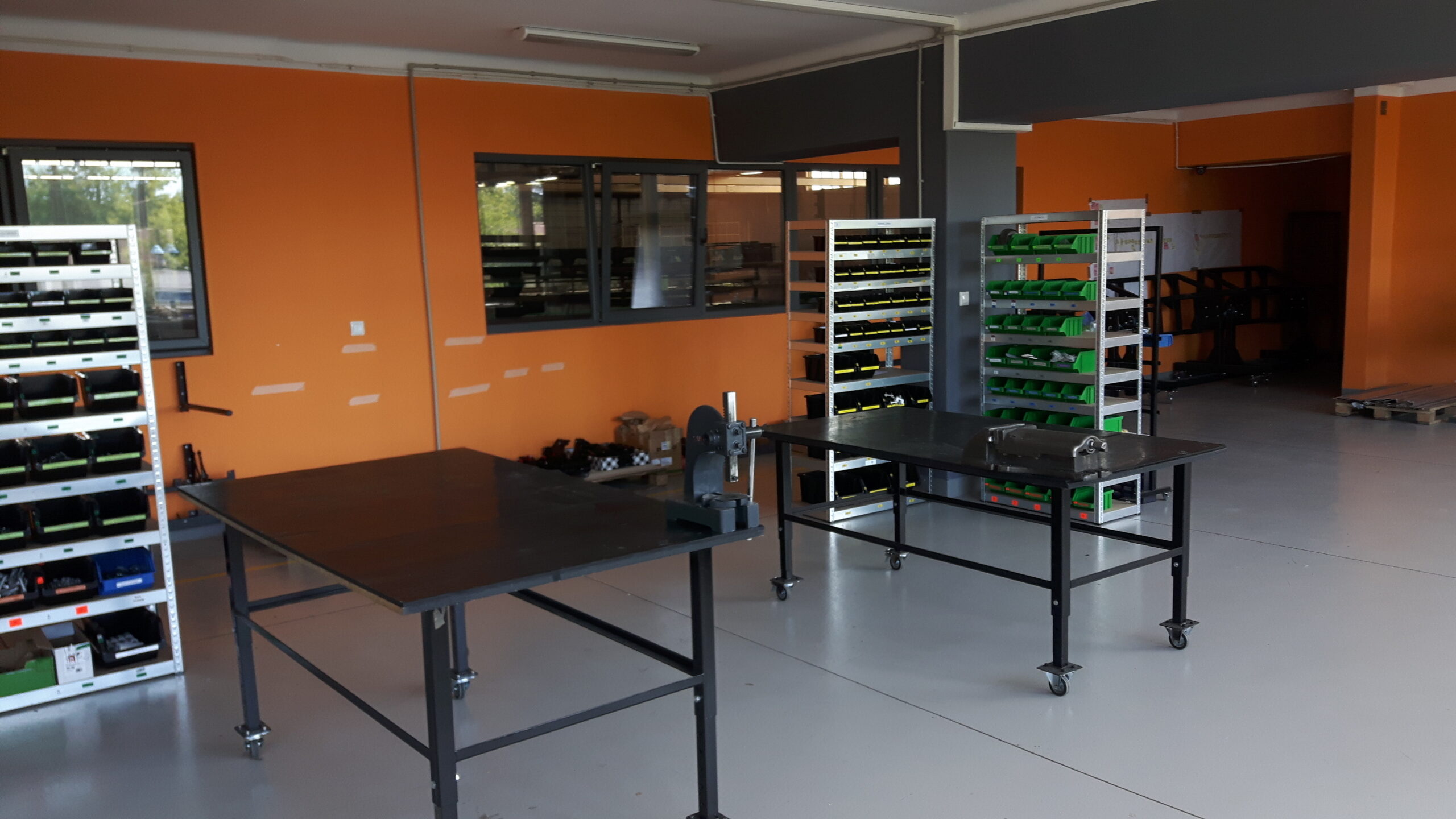
Stan po drugim etapie 5S: stół roboczy z tablicami cieni na podręczne narzędzia, obok regały z pojemnikami wypełnionymi detalami. Na stanowisku nie brakuje oczywiście etykiet.
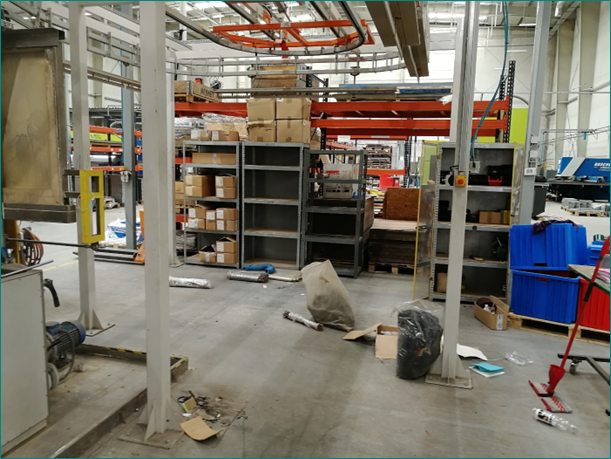
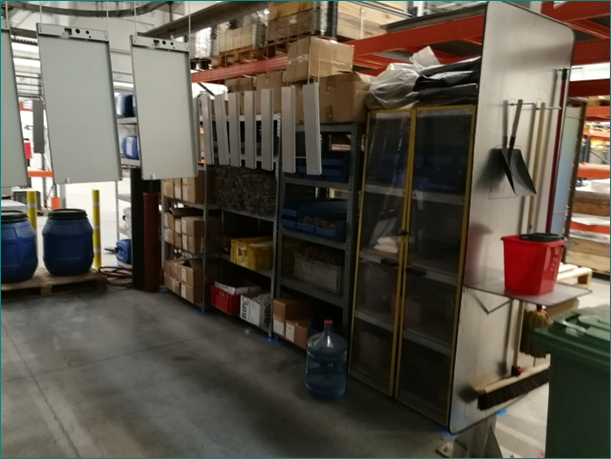
Zdjęcie po lewej: stan przed selekcją, systematyką i sprzątaniem.
Zdjęcie po prawej: stan po zmianach.
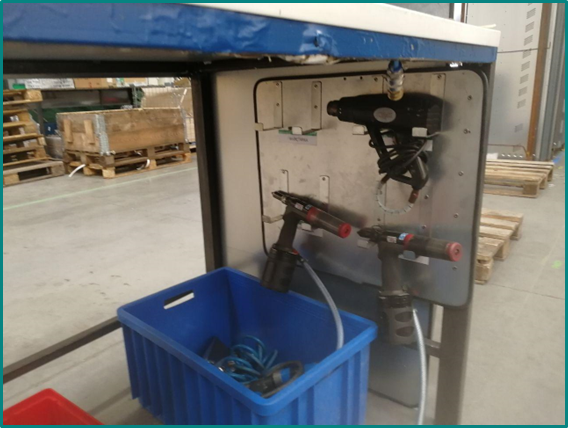
Standardowe miejsce dla narzędzi pracy umieszczone pod blatem roboczym. Przedmioty mają łatwy dostęp do miejsca zasilania.
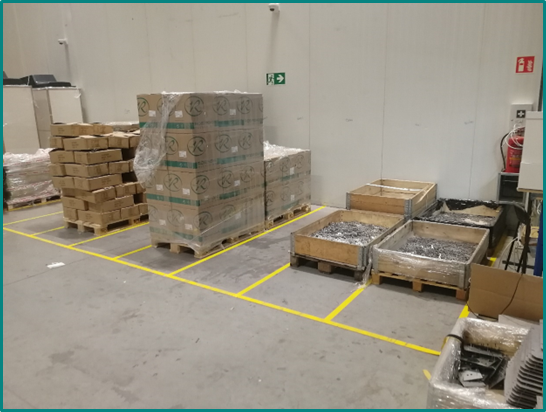
Systematyka w skali makro, czyli w ujęciu hali produkcyjnej – zastosowanie pól odkładczych do wydzielenia przestrzeni składowania wybranych przedmiotów.
Jeżeli jeszcze czujesz mały niedosyt, zapraszam Cię do rozstrzygnięcia kompleksowego Case Study.
3S to nie tylko sprzątanie miejsca pracy
Tak oczywiście, w tej fazie chodzi o utrzymanie czystości na danym stanowisku poprzez rutynowe działania takie jak: wycieranie kurzu, zamiatanie i mycie podłogi, usuwanie odpadów komunalnych, eliminowanie odpadów poprodukcyjnych itd.
Na tym jednak zabawa się nie kończy. I to właśnie Twoim zadaniem jest sprawienie, aby pracownicy produkcyjni popatrzyli na ten krok nieco szerzej, ponieważ to „Sprzątanie” polega również na:
- faktycznym usunięciu ze stanowiska pracy wszystkich zbędnych przedmiotów, które zostały wytypowane w poprzednich etapach,
- stworzeniu jak najbardziej komfortowych warunków pracy,
- zadbaniu o utrzymanie dobrego stanu narzędzi, jak i maszyn.
Dalej idąc, warto również, abyś wspomniał pracownikom o elementach uzupełniających.
Kącik sprzątania, bądź kącik czystości
To bardzo proste rozwiązanie, które sprawia, że działania zmierzające do uporządkowania miejsca pracy stają się bardziej intuicyjne i mogą przerodzić się w pozytywny nawyk.
Kącik sprzątania mieści w sobie wszystkie elementy 5S:
- tylko niezbędne przedmioty, w wystarczającej ilości,
- rozmieszczenie w standardowym miejscu,
- łatwa identyfikacja brakujących elementów (dzięki cieniom oraz etykietom),
- organizacja obszaru pracy sprzyjająca wbudowaniu samodyscypliny.
Poniżej znajdziesz kilka przykładowych zastosowań z różnych firm produkcyjnych, które możesz pokazać swojej ekipie:
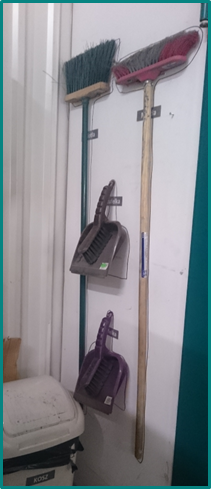
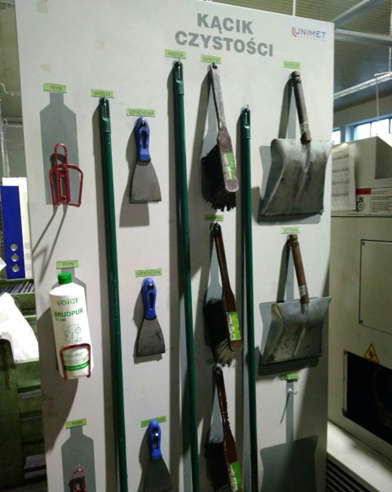
Organizacja kącików czystości może mieć charakter lokalny (jak na zdjęciu po lewej stronie), bądź charakter globalny (jak na zdjęciu po prawej stronie). W pierwszej alternatywie oznacza to, że każdy z działów ma wyznaczoną, określoną przestrzeń, wykorzystuje i pilnuje swoich zasobów do sprzątania stanowiska. W drugiej alternatywie występuje kilka kącików czystości, które znajdują się w kluczowych miejscach na hali produkcyjnej, a z danych zasobów mogą korzystać wyznaczone odgórnie obszary – tym samym unika się ryzyka zgubienia narzędzi, ponieważ istnieje jasne wskazanie o odpowiedzialności konkretnych grup osób.
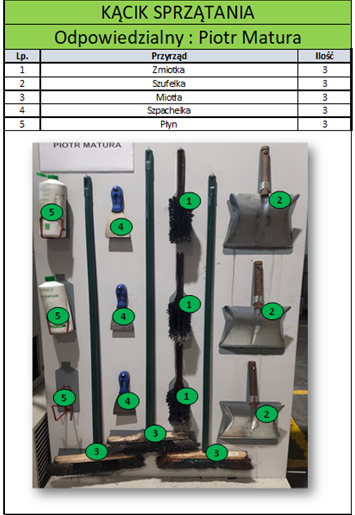
Uzupełnieniem dla działania kącika czystości jest prosty standard, zapowiadający czwarty krok metody 5S. Na powyższej karcie widoczna jest wizualizacja kącika, a następnie określone są ilości narzędzi potrzebne w obszarze oraz osoba odpowiedzialna za utrzymanie wypracowanego stanu.
Instrukcja i harmonogram sprzątania
W ramach akcji sprzątania powinien zostać stworzony również odpowiedni harmonogram ustalający terminy oraz częstotliwość porządków, jak i informujący o osobie odpowiedzialnej za poszczególne działanie. Jego uzupełnieniem może być prosta instrukcja, która wskazuje kluczowe kroki postępowania zmierzające do uporządkowania stanowiska pracy.
Choć pierwsze sprzątanie wykonane w ramach wdrożenia metody 5S pewnie będzie żmudne, czasochłonne i wcale nie takie przyjemne dla pracowników. Wraz z wprowadzeniem rutynowych działań sprzątających, czynności te staną się dla nich prostsze.
Czy można przejść od oporu do nawyku? Może nie zawsze, ale w tym przypadku na pewno!
Jeśli nie wiesz jak zacząć mówić… na początku po prostu spytaj operatorów czy chcieliby wracać codziennie do domu, w którym jest zawsze bajzel, nieumyte garnki, latający kurz i pajęczyny. Oczywiście robota, to nie dom…jednak spędza się w niej średnio rocznie 1200 godzin – warto w takim razie zadbać o komfort i jakość pracy.
W utrzymaniu konsekwencji pomoże:
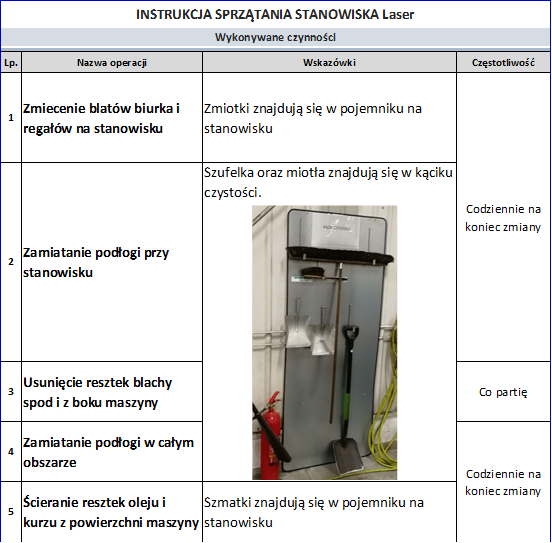
W firmie X finalizując 1 oraz 2 krok metody uporządkowano i przereorganizowano stanowisko. Na podstawie uzyskanego stanu określono kroki, które zapewnią utrzymanie oczekiwanego ładu i zapisano je w postaci instrukcji sprzątania. Poszczególnym działaniom przypisano odpowiednią częstotliwość powtórzeń.
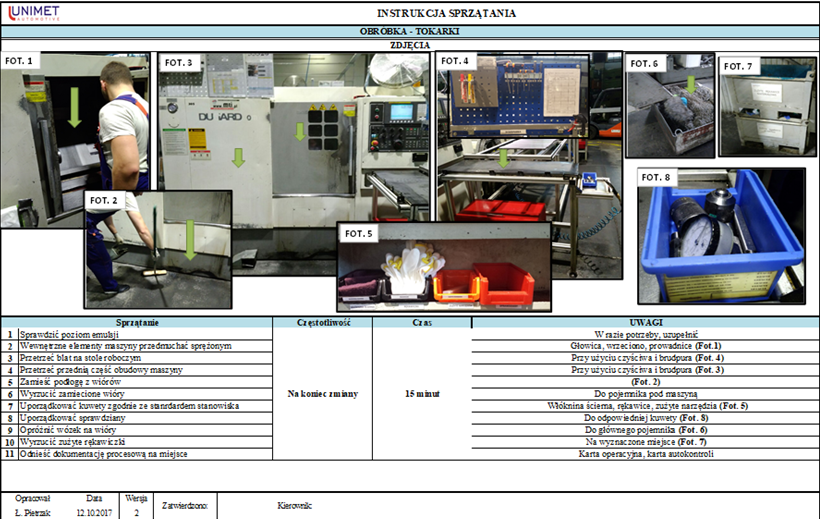
Utrzymanie porządku na stanowisku odnosi się nie tylko używanych blatów, regałów, czy eksploatowanej nawierzchni, ale także dbałości o stan maszyn oraz urządzeń. Proste akcje konserwacyjne stanowią sprzężenie metody 5S oraz TPM – Total Productive Maintenance.
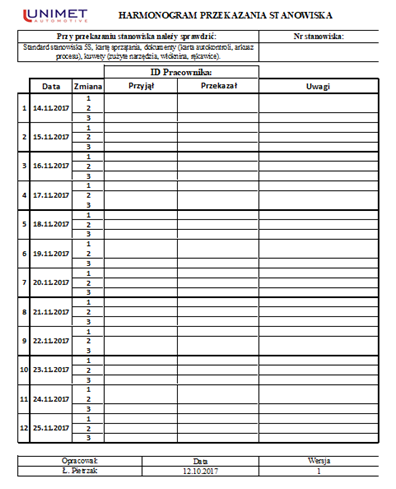

W uzupełnieniu do wcześniej zaprezentowanych instrukcji w firmie X, lider zespołu opracował harmonogram przekazania stanowiska. Osoba przekazująca obszar kolejnym operatorom, swoim podpisem potwierdza, że wykonała kroki porządkowe zgodnie z przyjętymi standardami. Natomiast osoba przyjmująca deklaruje, że jest świadoma w jakim stanie znajduje się obszar podczas rozpoczęcia pracy. W celu usprawnienia wzajemnej komunikacji, na karcie widnieje również kolumna z polem na uwagi.
Na zwieńczenie trzeciego kroku 5S, należy się jeszcze jeden przykład dla Ciebie i Twojego zespołu. Ponownie przedstawiony w układzie – przed i po zmianie.
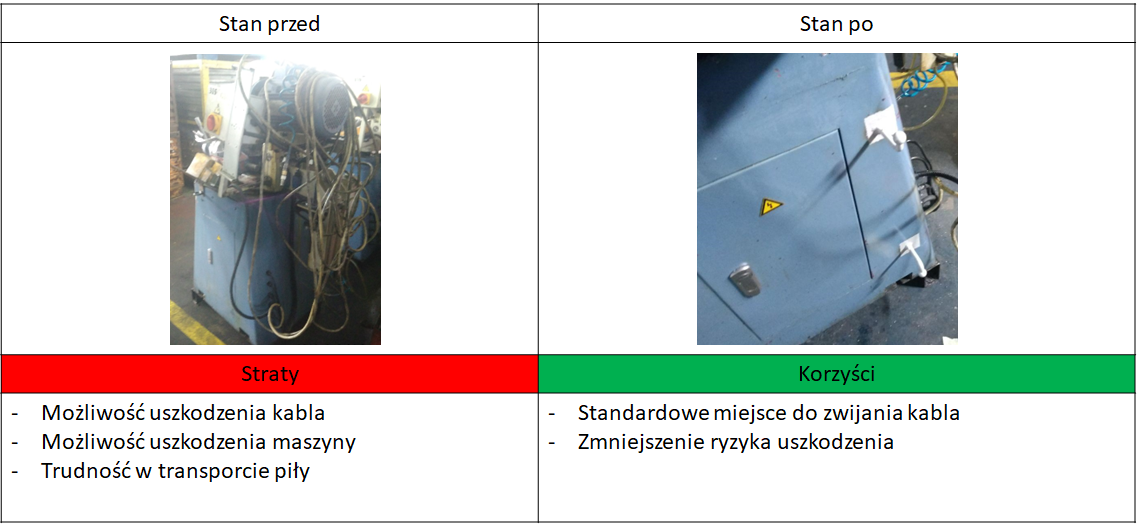
Case study przedstawia zagospodarowanie przestrzeni na i przy maszynie. Przed wprowadzeniem działań usprawniających, na stanowisku istniało wysokie zagrożenie uszkodzenia zarówno samego urządzenia, jak i jego kabla. Co więcej, transport piły był nieporęczny i stanowił wyraźną, zbędną stratę czasu. Po zamontowaniu specjalnych haczyków do zwijania kabla na ścianie maszyny, rozwiały się wszelkie dotychczasowe niedogodności i zagrożenia.
Czwarty krok – standaryzacja
Standaryzacja to fundamentalny element całej metodyki Lean Manufacturing.
W przypadku metody 5S stanowi zwieńczenie wszystkich wcześniejszych starań o uzyskanie bardziej efektywnego stanowiska pracy. Z punktu widzenia pracy z zespołem, nie możesz lekceważyć tego kroku, ponieważ w rzeczywistości jest on nie lada wyzwaniem.
Pracownicy zarówno na etapie warsztatów, jak i faktycznego wdrożenia mogą oponować.
…już przecież trzy główne fazy mają za sobą, a to one najbardziej uwidoczniły zmiany. Po co robić coś więcej?
Znowu, tak i jak i wcześniej, tak i teraz, to do Ciebie należy zadanie, aby przekonać ich o słuszności dalszych działań doskonalących stanowisko pracy.
Wszelkiego typu instrukcje stanowiskowe, instrukcje sprzątania, mapy 5S, wizualizacje stanu pożądanego, One Point Lesson, dodatkowe wizualizacje oraz standardy mają na celu utrzymać efekty wcześniejszych kroków i przyczynić się do:
- zmniejszenia czasu poszukiwania i wykonywania zbędnych ruchów, związanych z sięganiem po narzędzia,
- wzrostu poziomu organizacji stanowiska pracy operatorów,
- zwiększenia komfortu wykonywanej pracy,
- wzbudzenia poczucia estetyki,
- zwiększenia wydajności pracy operatorów,
- uświadomienia istoty ciągłego doskonalenia,
- za czym docelowo idzie również redukcja kosztów produkcji.
Dlatego pokaż im kolejne przykłady!
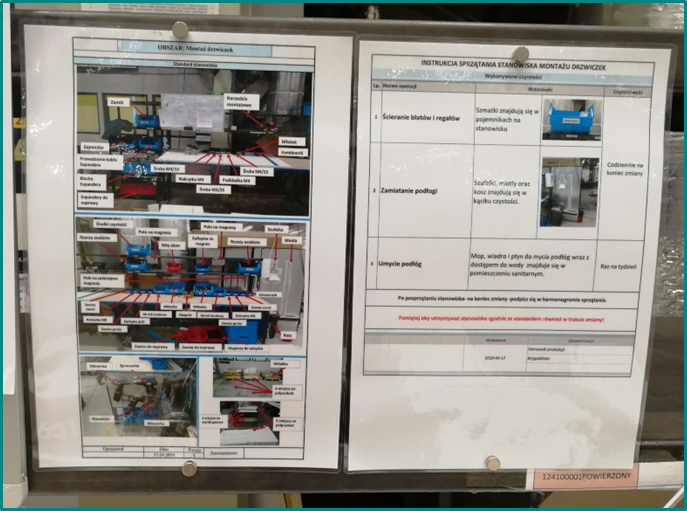
Na podstawie nowego zagospodarowania stanowiska roboczego opracowano standard prezentujący wizualizację oraz opisy rozmieszczenia wszelkich niezbędnych narzędzi oraz części. Stanowi on nieodłączny dokument dla instrukcji pracy (czy też instrukcji pracy standaryzowanej). Dzięki temu obsługa obszaru stała się bardziej intuicyjna, nie tylko dla operatorów, ale także dla brygadzistów, audytorów, nowych pracowników i tych przychodzących na tymczasową zamianę.
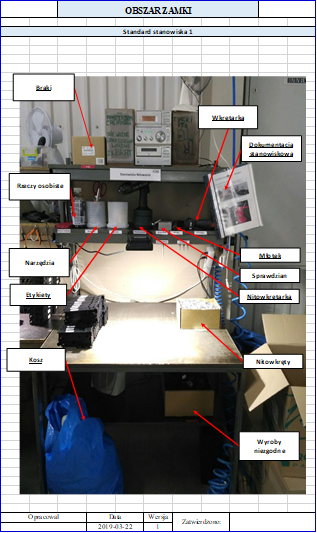
Kolejny przykład prezentujący mapę wzorcowego stanu obszaru roboczego.
Samodyscyplina – utrzymanie jakości stanowiska pracy
No dobrze, wydaje się, że jesteśmy prawie na samym końcu, ale zdecydowanie nie mów tego operatorom! Bowiem jest to jedynie finał pierwszej rundy, a zasada działania 5S sprowadza się do ciągłego poszukiwania kolejnych usprawnień w miejscu pracy. Tak też etap samodyscypliny to budowanie nawyków, podtrzymywanie determinacji w utrzymaniu jakości i ergonomii stanowiska pracy, kreowanie kultury pracy, dalsze szkolenia, dyskusje, a także audyty.
Jeżeli na etapie warsztatów powiesz pracownikom o strasznych audytach, możesz od razu nastawić się na kręcenie nosem. Jeśli natomiast przedstawisz je w świetle okazji do wspólnego monitorowania skuteczności wprowadzonych zmian, a także szansy mierzenia postępów, szala może obrócić się na Twoją korzyść.
Żeby, w takim razie, nie bali się nieznanego i zobaczyli jak to może wyglądać u Was w firmie, pokaż im poniższe rozwiązania:
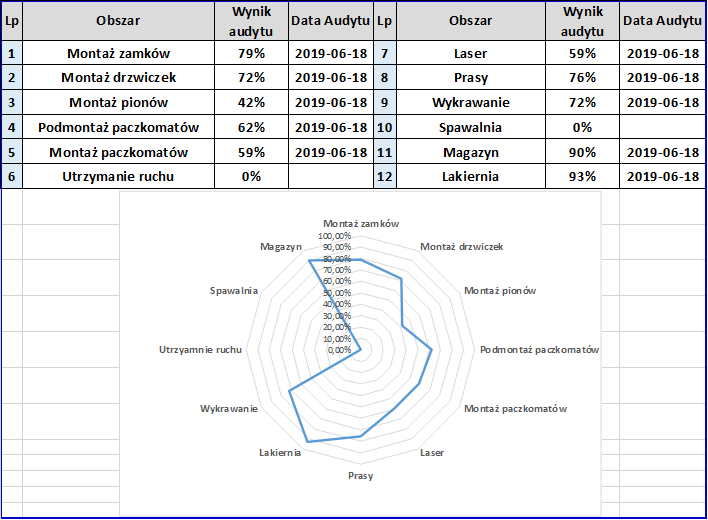
Na podstawie przeprowadzonych audytów w różnych obszarach firmy wykonano ogólny raport podsumowujący. Ukazuje on zestawienie wyników procentowych z poszczególnych działów, a także ich wizualizację z wykorzystaniem w wykresu radarowego. Interpretacja danych powinna opierać się oczywiście o szersze spektrum. Niższy wynik w przykładowym obszarze montażu pionów, wcale nie musi oznaczać, że pracownicy zaniedbują utrzymanie standardów. Może wynikać z tego, że jest to jeden z pierwszych audytów, świeżo po pierwszych momentach wdrożenia 5S. Oznacza to, że przeprowadzona kontrola stanowi wyznacznik do podjęcia działań korygujących, naprawczych, czy doskonalących. Dalej idąc, nie można oczywiście również wykluczać scenariuszy zaniechania, bądź też wzorowego utrzymywania standardów, na miarę 93, czy nawet 100%.
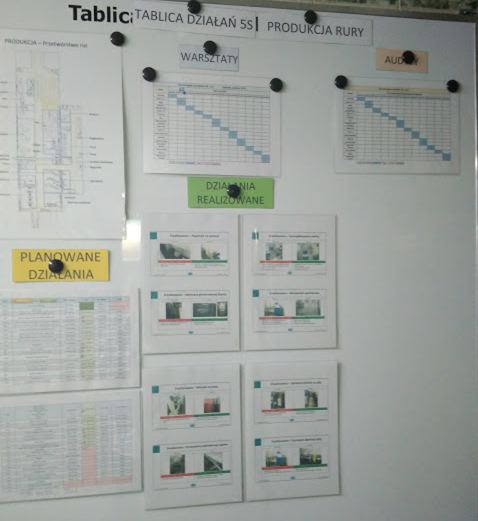
Przeprowadzony audyt jest podstawą do określenia i rozplanowania zadań między pracownikami. Zakres działań może dotyczyć każdego z kroków metody 5S. Warto przy tym zaznaczyć, że zarówno wyniki, harmonogram audytów, a także lista zadań z deadline’ami oraz podziałem odpowiedzialności, powinny być umieszczone w widocznym dla wszystkich pracowników miejscu. Transparentność oraz prostota to klucz do budowania świadomości, utrzymania dyscypliny, a także usprawniania komunikacji.
Jak sam pewnie dobrze wiesz, mimo tego, że o 5S mówi się jako o jednej z najprostszych metod Lean Management i może nawet trochę bagatelizuje się jej moc, wymaga ona odpowiedniego zabezpieczenia zasobów oraz działania w perspektywie długofalowej. Nie może się ona sprowadzać do działania jednostek, a musi wynikać z pracy zespołowej i zaangażowania. Nie ma też swojego końca, a do jej utrzymania, potrzeba chęci i determinacji.
Oczywiście, w ramach przeciwwagi, powinieneś też pamiętać, że jeśli uda Wam się wprowadzić założenia 5S do Waszego zakładu, nie jest to równoznaczne z tym, że już „macie Lean Manufacturing”.
Lean Management i 5S w biurze
W formie zwieńczenia, jeszcze kilka słów o tym, że stosowanie metod i narzędzi Lean Management również jest możliwe w przestrzeni biurowej.
Jak pewnie dobrze wiesz, założenia metodyki nie sprowadzają się jedynie do płaszczyzny produkcyjnej. Na każdą czynność możemy spojrzeć jak na proces, a na każde pomieszczenie jak na stanowisko robocze. Wszędzie możemy poszukiwać i identyfikować marnotrawstwa, wszędzie możemy wprowadzać usprawnienia i podnosić efektywność pracy. Dlatego, w formie poszerzenia perspektywy, szepnij i o tym operatorom. Z pewnością będzie im raźniej, gdy dowiedzą się, że to nie tylko ich może dotyczyć jakaś zmiana.
A jeżeli chcesz poszerzyć kontekst organizacji pracy pracowników biurowych i sprawdzić jak może wygrać proces wdrożenia metody 5S w tym przypadku, zachęcam Cię do odsłuchania wartościowego webinaru „Jak utrzymać i wdrożyć 5S w biurze”.
Sprawdź aplikację Audyt 5S – to rozwiązanie, które usprawnia proces przeprowadzania audytów 5s na produkcji. To rozwiązanie, które pozwala na automatyzację procesu audytu, tworzenie harmonogramów, analizę wyników i koordynowanie działań poaudytowych.
Potrzebujesz formularza audytu 5S na produkcji?
Podaj dane, a wyślę Ci na maila.
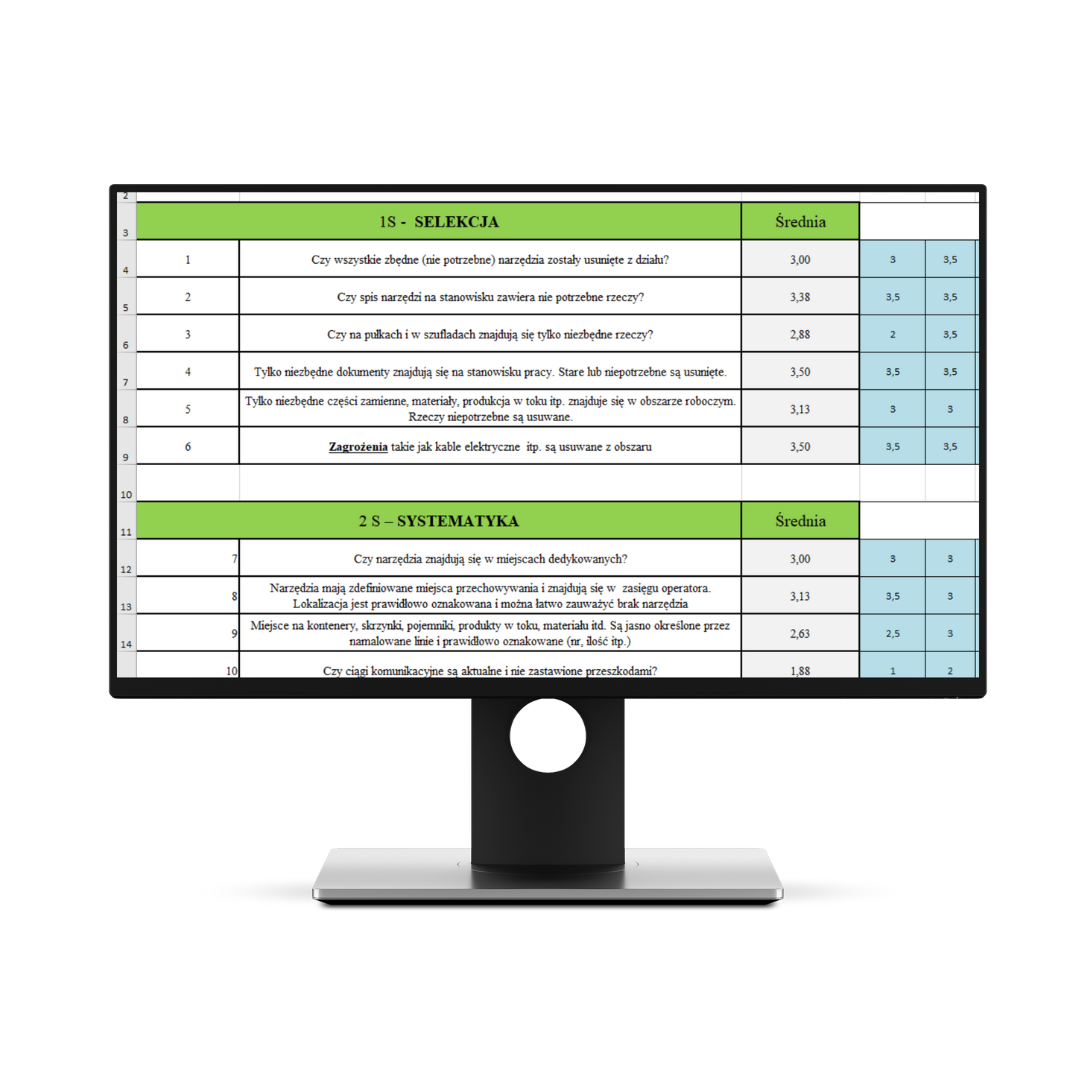