Normy na produkcji – jak je wyznaczać?
Norma, czyli… ,,tyle, ile możesz zrobić w ciągu jednej zmiany”. Tak opisuję normę w podcaście ,,Produkcja bez chaosu”. To najłatwiejsza – i najbardziej podstawowa kwestia w zrozumieniu, czym jest norma. Rodzi się jednak tutaj kolejne pytanie (a nawet kilka): jak ona została obliczona? Czy zostały w niej uwzględnione zakłócenia? W tym artykule postaram się przybliżyć Ci, w jaki sposób możesz wyznaczać normy na produkcji w swojej firmie. Lekturę możesz uzupełnić o przesłuchanie podcastu, w którym poza krótką teorią, omawiam praktyczne aspekty wyznaczania norm na produkcji.
Spis treści:
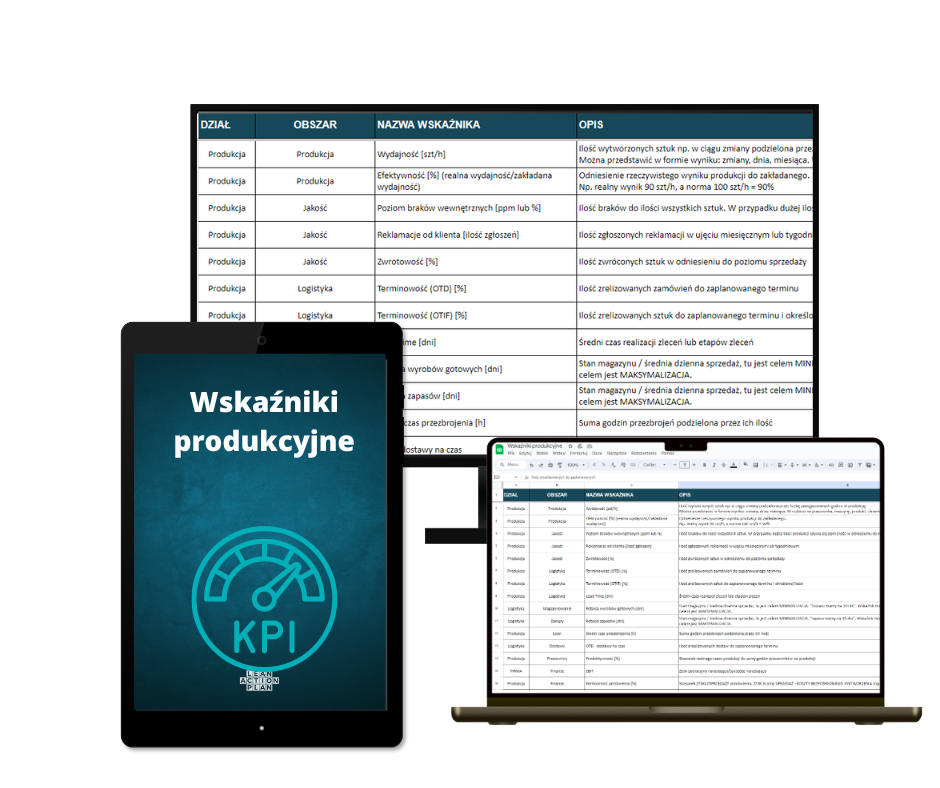
Podstawy wyznaczania normy na produkcji
Być może w Twojej firmie istnieje pojęcie normy, które przejawia się w słowach ,,Normą jest 500 sztuk na dzień”, a może nigdy jej nie obliczałeś. W Lean Action Plan uważamy, że wyznaczanie normy na produkcji to fundament dla zapewnienia efektywności operacyjnej i optymalizacji zasobów w każdym przedsiębiorstwie produkcyjnym. Podstawą tego procesu jest dokładne zdefiniowanie i analiza każdego etapu pracy, co pozwala na ustalenie optymalnego czasu potrzebnego na wykonanie poszczególnych zadań oraz produkcję jednostek produktów. Słowo klucz: optymalnego. Nie jest realne, by przez całą zmianę produktywność pracowników produkcyjnych była na maksymalnym poziomie. Należy więc znaleźć ten złoty środek, który pozwoli uwzględnić optymalny, ale rzeczywisty czas produkcji i przełożyć ten czas na normę.
Normy produkcyjne stanowią nie tylko wyznacznik wydajności pracy. Normatywy produkcji służą jako narzędzie do planowania produkcji, kontrolowania kosztów i motywowania pracowników. Wyznaczanie normy produkcji wymaga interdyscyplinarnego podejścia, łączącego wiedzę techniczną z analizą procesów pracy, psychologii pracy oraz ergonomii, aby zapewnić, że cele produkcyjne są zarówno ambitne, jak i realistyczne. Proces ten opiera się na dokładnym pomiarze czasu (chronometrażu), uwzględnieniu czasu na nieprzewidziane przerwy oraz analizie danych historycznych. Poprawne wyznaczanie norm umożliwia przedsiębiorstwom nie tylko osiąganie zaplanowanych wyników produkcyjnych, ale także ciągłe doskonalenie procesów produkcyjnych w dążeniu do doskonałości operacyjnej.
Czym jest normowanie produkcji i dlaczego jest ważne?
Normowanie produkcji to proces ustalania standardowych czasów potrzebnych na wykonanie określonych operacji lub zadań produkcyjnych, jak również określenie oczekiwanej ilości materiałów potrzebnych do wyprodukowania jednostki produktu. To istotny element w planowaniu produkcji, zarządzaniu zasobami, ustalaniu kosztów oraz w monitorowaniu i poprawie wydajności pracy. Dzięki normowaniu czasu pracy przedsiębiorstwa mogą ustalić realistyczne cele produkcyjne, optymalizować procesy produkcyjne, minimalizować marnotrawstwo zasobów i skutecznie zarządzać czasem pracy.
Normowanie pracy ma znaczenie dla zapewnienia konkurencyjności firmy na rynku. Umożliwia ono nie tylko efektywne wykorzystanie zasobów i maksymalizację wydajności, ale także pomaga w utrzymaniu wysokiej jakości produktów. Poprzez ustalenie standardowych procedur i oczekiwań, normowanie produkcji przyczynia się do zwiększenia spójności i powtarzalności procesów produkcyjnych, co jest niezbędne w osiąganiu i utrzymaniu satysfakcji klientów. Ponadto, normowanie umożliwia lepsze zrozumienie procesów produkcyjnych, co jest fundamentem dla ciągłego doskonalenia i innowacji. W erze szybkich zmian technologicznych i rosnącej konkurencji, umiejętność efektywnego normowania produkcji staje się nieodzowną kompetencją każdego przedsiębiorstwa dążącego do sukcesu.
Różne techniki normowania stosowane w przemyśle
W przemyśle stosuje się różne techniki normowania czasu produkcji, aby dostosować procesy produkcyjne do specyficznych wymagań i warunków. Do najpopularniejszych należą:
- Analiza czasu i ruchu: Metoda ta polega na szczegółowym badaniu poszczególnych zadań i operacji w celu identyfikacji i eliminacji zbędnych ruchów oraz optymalizacji sekwencji operacji.
- Systemy norm czasowych: Ustanawiają standardowy czas, jaki jest potrzebny na wykonanie określonego zadania przez średnio wykwalifikowanego pracownika przy normalnych warunkach pracy.
- Modularne systemy czasu pracy: Polegają na budowaniu norm czasu pracy na podstawie modułów, czyli znormalizowanych jednostek czasu, które mogą być łatwo dostosowywane do różnych zadań produkcyjnych.
- Benchmarking: Porównanie wydajności i technik stosowanych w przedsiębiorstwie z najlepszymi praktykami branżowymi, aby ustalić realistyczne i osiągalne cele produkcyjne.
Rola norm czasu pracy w efektywności produkcji
Normowanie pracy odgrywa rolę w zwiększaniu ogólnej wydajności produkcji w firmach. Jednak kilka innych korzyści pojawia się w wyniku nałożenia realistycznych i osiągalnych standardów. W pierwszej kolejności, oczywiście pomaga to w efektywności procesów produkcyjnych, gdzie każda operacja i ruch musi być zaplanowany, aby zminimalizować marnotrawstwo i optymalnie wykorzystać zasoby. Normy są bazą oceny wydajności lokomotywy, umożliwiającą porównanie rzeczywistych wyników z oczekiwaniami i standardami branżowymi. Jednak korzyści z normowania na poziomie zarządzania są znacznie dalej. W skomplikowanym i opartymi na informacjach środowisku biznesowym planowanie-produkcji i planowanie-zapotrzebowania na surowce odgrywają zasadnicze role w zwiększeniu przewidywalności procesów gospodarczych i szybkim reagowaniu na zmiany w zapotrzebowaniu rynkowym. Normatywy produkcji ułatwiają również komunikację wewnątrz organizacji, dostarczając jasnego przekazu oczekiwanego wyniku pracy. Krótko mówiąc: pracownik wie, ile powinien wyprodukować, a pracodawca wie, czego może oczekiwać. Normowanie jest również związane z ciągłym doskonaleniem. Przeglądy i aktualizacje norm można używać do adaptowania się do nowych warunków rynkowych i technologii, a także nowych metod pracy, co napędza innowację i zwiększa efektywność. Skutecznie wprowadzone i zarządzane normy produkcyjne mogą znacząco wpływać na konkurencyjność firmy, zwiększając jej zdolność do produkcji wysokiej jakości produktów w maksymalnie krótkim czasie i przy minimalnych kosztach.
Metodologie wyznaczania norm
Obecnie ważne są normy wydajności i jakości. To one stanowią fundamenty, na których buduje się sukces przedsiębiorstwa. Te dwie kategorie norm są nierozerwalnie połączone, tworząc system, który pozwala przedsiębiorstwom nie tylko mierzyć i oceniać swoją produktywność, ale także ciągle poprawiać procesy, aby sprostać oczekiwaniom rynku i klientów. Normy wydajności koncentrują się na ilościowym aspekcie produkcji, określając, ile produktów powinno zostać wyprodukowanych w określonym czasie, przy zachowaniu efektywnego wykorzystania zasobów. Z kolei normy jakościowe zapewniają, że każdy z tych produktów spełnia określone standardy jakości przed dostarczeniem do klienta.
Zarządzanie tymi normami wymaga zintegrowanego podejścia, które uwzględnia zarówno potrzebę efektywności operacyjnej, jak i konieczność utrzymania wysokiego poziomu jakości. Wyznaczanie realistycznych i osiągalnych norm wydajności oraz jakości wymaga dokładnej analizy danych produkcyjnych, zrozumienia procesów, a także zaangażowania i współpracy między różnymi działami przedsiębiorstwa. Kluczem do sukcesu jest nie tylko ustalenie tych norm, ale również ich regularna rewizja i dostosowanie do zmieniających się warunków – od wprowadzenia nowych technologii, przez zmiany w popycie rynkowym, po nowe regulacje branżowe.
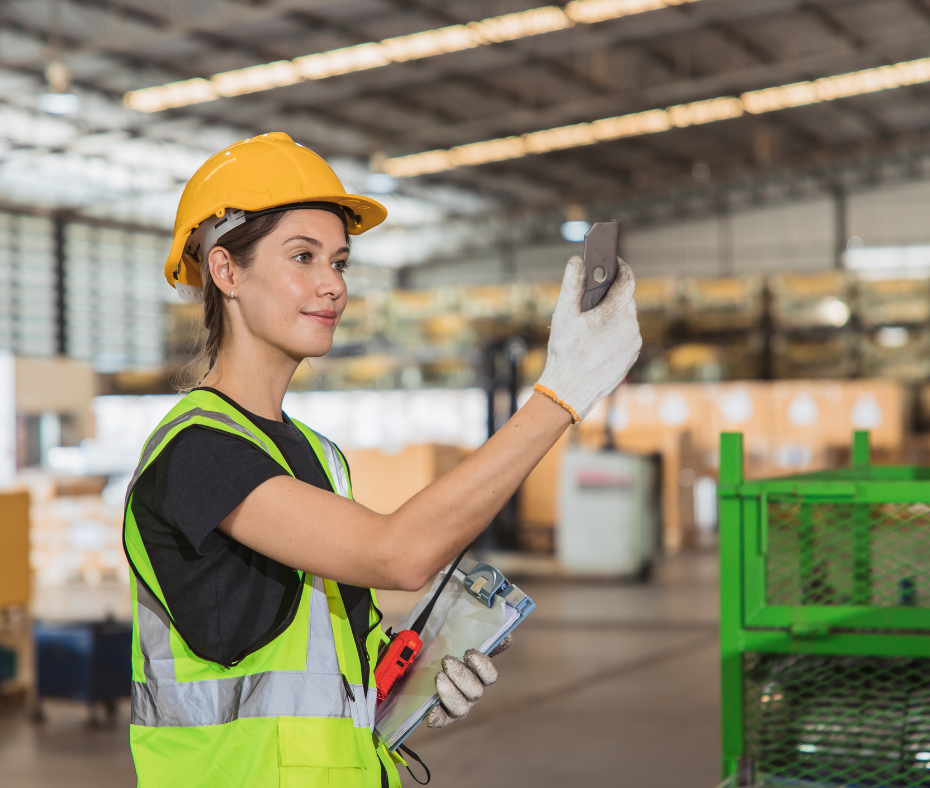
Integracja norm wydajności i jakości w codziennej działalności produkcyjnej umożliwia organizacjom lepsze planowanie, kontrolę i optymalizację swoich operacji. Poprzez stałe monitorowanie i analizę wyników w kontekście tych norm, przedsiębiorstwa mogą szybko identyfikować obszary wymagające poprawy, minimalizować straty i odpady, a także lepiej reagować na potrzeby klientów. W rezultacie, dobrze zdefiniowane i skutecznie zarządzane normy wydajności i jakości są czynnikiem, który może znacząco wpłynąć na zdolność przedsiębiorstwa do utrzymania konkurencyjności i osiągania długoterminowego wzrostu.
Tradycyjne metody normowania
Tradycyjne metody normowania w produkcji skupiają się głównie na ilościowych aspektach wydajności i produkcji, opierając się na historycznych danych i doświadczeniach. Jedną z najbardziej rozpowszechnionych metod jest analiza statystyczna wyników produkcji z przeszłości, która pozwala na ustalenie norm wydajności i ilości produkowanych produktów poprzez obserwację i średnią wydajność w danym okresie. Ta metoda zakłada, że przyszła wydajność będzie podobna do tej, która została zarejestrowana w przeszłości, pod warunkiem, że warunki pracy i procesy produkcyjne pozostaną stabilne.
Inną tradycyjną metodą jest normowanie oparte na czasie pracy, gdzie normy ilościowe ustalane są na podstawie szacowanego czasu niezbędnego do wykonania określonej liczby jednostek produktu. Chociaż ta metoda skupia się na pomiarze czasu pracy, jej ostatecznym celem jest ustalenie ilości produktów, które mogą być wyprodukowane w danym czasie, co pośrednio przekłada się na normy wydajności. Przydatna tutaj może okazać się aplikacja Analiza Nagrań Procesów, której działanie pokazane zostało w podcaście.
To aplikacja do analizy nagrań procesów, która pozwala na proste rozdzielenie procesu na pojedyncze czynności oraz przyśpiesza jego analizę. Dzięki temu rozwiązaniu w łatwy sposób można wyznaczyć normy oraz standardy pracy. Dowiedz się więcej o aplikacji, klikając przycisk poniżej.
Nowoczesne podejścia do normowania
Nowoczesne podejścia do normowania wykraczają poza proste analizy ilościowe, łącząc technologie i zaawansowane analizy danych w celu precyzyjniejszego ustalania norm. Jednym z narzędzi w nowoczesnym normowaniu jest Lean Manufacturing i jego zasada ciągłego doskonalenia (Kaizen), która promuje stałą optymalizację procesów i redukcję marnotrawstwa. W tym podejściu normy wydajności są regularnie przeglądane i dostosowywane w oparciu o ciągłe feedback od pracowników i analizy procesów, co pozwala na bardziej dynamiczne reagowanie na zmieniające się warunki produkcji.
Inne nowoczesne metody, takie jak systemy zarządzania przez cele (Management by Objectives – MBO), kładą nacisk na ustalanie norm wydajności przez zespoły, które bezpośrednio odpowiadają za dane procesy produkcyjne. Metoda ta promuje zaangażowanie pracowników i odpowiedzialność za ustalane cele, co może prowadzić do wyższej motywacji i lepszych wyników.
Dodatkowo, rosnące zastosowanie zaawansowanych technologii informatycznych i analizy dużych zbiorów danych (Big Data) umożliwia przedsiębiorstwom dokładniejsze modelowanie i prognozowanie wydajności produkcji. Wykorzystując algorytmy uczenia maszynowego i sztucznej inteligencji, firmy mogą precyzyjnie analizować ogromne ilości danych produkcyjnych w czasie rzeczywistym, identyfikując wzorce i przewidując optymalne normy wydajności, co otwiera nowe możliwości dla personalizacji i elastyczności w ustalaniu norm produkcji.
Nowoczesne podejścia do normowania wykorzystują zatem kombinację wiedzy eksperckiej, zaangażowania zespołów produkcyjnych oraz zaawansowanych technologii, aby precyzyjniej określić i dostosować normy wydajności, zwiększając tym samym efektywność i konkurencyjność przedsiębiorstw na rynku.
Proces wyznaczania normy czasu pracy
Wyznaczanie normy czasu pracy to kluczowy element w zarządzaniu produkcją, który pozwala na efektywne planowanie, monitorowanie i optymalizację procesów pracy. Norma czasu określa, ile czasu powinno zostać poświęcone na wykonanie określonego zadania lub produkcję jednostki produktu, biorąc pod uwagę optymalne warunki pracy. Jest to narzędzie zarówno dla pracowników, jak i menedżerów, pozwalające na ustalenie realistycznych celów produkcyjnych oraz ocenę wydajności.
Jak obliczyć normę czasu: podstawowe kroki
Jakie są techniki normowania czasu pracy i normy produkcyjnej? Obliczanie normy czasu pracy zaczyna się od zdefiniowania i dokładnego zrozumienia procesu lub zadania, dla którego norma ma być ustalona. Następnie przeprowadza się szczegółową analizę każdego kroku procesu, uwzględniając czas potrzebny na jego wykonanie. Proces ten często wymaga podziału zadania na mniejsze, łatwiejsze do zmierzenia elementy. Kluczowymi krokami w obliczaniu normy czasu są:
- Dokładne zdefiniowanie zadania lub procesu: Określenie zakresu pracy i zrozumienie wszystkich zadań wchodzących w skład procesu.
- Pomiary czasu: Wykonanie pomiarów czasu potrzebnego na wykonanie każdego elementu zadania, najlepiej przy użyciu technik chronometrażu (czyli techniki pomiarów czasu). Pomiary powinny być powtarzane, aby zapewnić ich wiarygodność i średnią wartość – nie chodzi nam o idealny czas produkcji, a o realną wartość.
- Analiza warunków pracy: Ocena, czy warunki pracy, w których przeprowadzono pomiary, są optymalne i czy mogą być uznane za standard.
- Uwzględnienie czasu dodatkowego: Dodanie czasu na nieprzewidziane przerwy, opóźnienia i inne czynniki mogące wpłynąć na czas wykonania zadania.
- Kalkulacja normy czasu: Ustalenie ostatecznej normy czasu na podstawie zebranych danych, uwzględniając wszystkie elementy zadania oraz zapas czasu na nieoczekiwane zdarzenia.
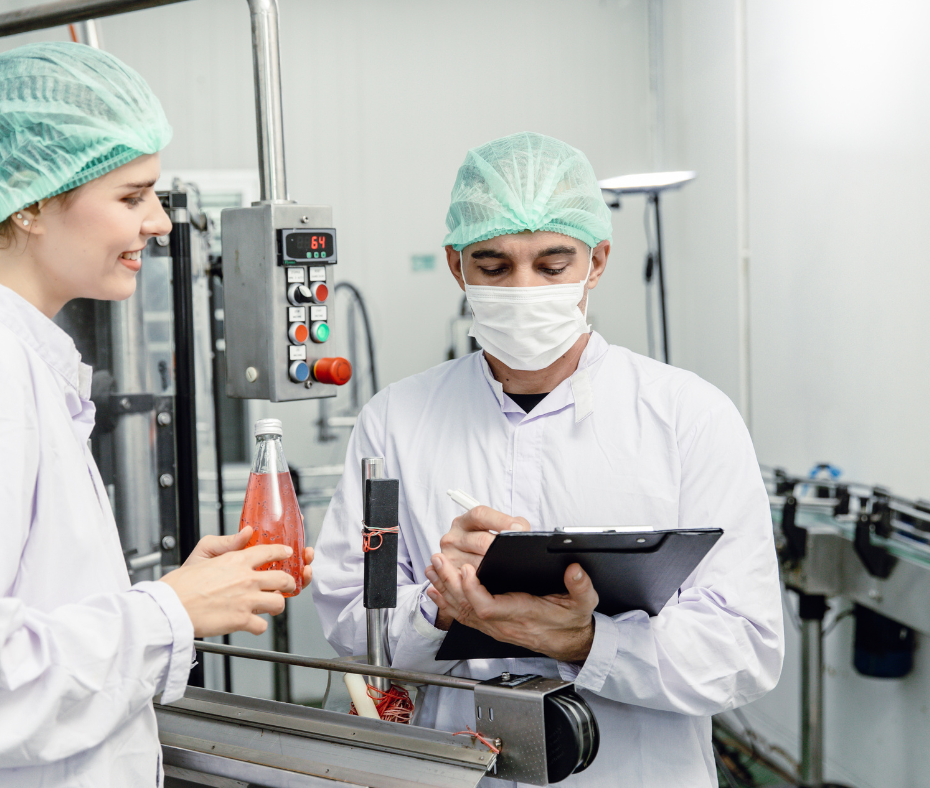
Zastosowanie chronometrażu w wyznaczaniu normy czasu
Chronometraż, czyli dokładne mierzenie czasu wykonania poszczególnych operacji pracy za pomocą stopera lub specjalistycznego oprogramowania, jest podstawową metodą wykorzystywaną przy wyznaczaniu norm czasu pracy. Umożliwia on bardzo precyzyjne ustalenie, ile czasu pracownicy potrzebują na wykonanie danej czynności. Chronometraż jest szczególnie przydatny w identyfikowaniu elementów procesu, które są nadmiernie czasochłonne, co może wskazywać na potrzebę ich usprawnienia lub automatyzacji.
Czas jednostkowy i jego rola w normowaniu
Czas jednostkowy, czyli czas potrzebny na wykonanie jednej jednostki pracy (np. całkowity czas produkcji potrzebny do produkcji jednego produktu), jest ważnym elementem w procesie normowania. Pozwala on na ustalenie, ile produktów lub zadań może być wykonanych w określonym czasie, co jest niezbędne do efektywnego planowania produkcji i oceny wydajności pracy. Analiza czasu jednostkowego pomaga również w identyfikacji obszarów, w których możliwe jest wprowadzenie usprawnień (np. usprawnić zarządzanie czasem), co może przyczynić się do zwiększenia efektywności procesów produkcyjnych.
Zastosowanie tych metod i koncepcji pozwala na tworzenie spójnych i realistycznych norm czasu pracy, które są fundamentem efektywnego zarządzania produkcją i pracy. Regularne przeglądy i dostosowania norm do zmieniających się warunków pracy są kluczowe dla utrzymania konkurencyjności i osiągania celów produkcyjnych.
Chcesz wprowadzić standaryzację pracy do swojej firmy produkcyjnej? Tak się składa, że prowadzimy projekt wdrożenia standaryzacji pracy. To rozwiązanie szyte na miarę – rozpoczynamy współpracę od badania potrzeb i wówczas dopasowujemy konkretne rozwiązania, jakie zostaną wdrożone w ramach projektu. Dowiedz się więcej klikając przycisk poniżej.
Oprogramowanie i narzędzia wspomagające normowanie
Ich zastosowanie przekłada się na znaczące usprawnienia w zakresie analizy danych produkcyjnych, planowania procesów, a także monitorowania i utrzymania wysokiej jakości oraz wydajności produkcji. Nowoczesne systemy informatyczne, takie jak zaawansowane oprogramowanie ERP, MES czy specjalistyczne aplikacje do symulacji procesów, umożliwiają przedsiębiorstwom nie tylko precyzyjne wyznaczanie norm produkcyjnych, ale również ich ciągłą optymalizację. Dzięki automatyzacji zbierania danych i analizie w czasie rzeczywistym, menedżerowie produkcji mogą dokonywać szybkich i trafnych decyzji, dostosowując procesy produkcyjne do bieżących potrzeb i oczekiwań rynku. Ponadto, integracja tych narzędzi z codzienną pracą zapewnia lepszą komunikację między działami, zwiększa przejrzystość procesów i pozwala na efektywne zarządzanie zasobami, co w konsekwencji prowadzi do wzrostu konkurencyjności przedsiębiorstwa. W związku z tym, inwestycja w nowoczesne oprogramowanie wspierające normowanie jest kluczowym krokiem na drodze do osiągnięcia doskonałości operacyjnej i zrównoważonego rozwoju.
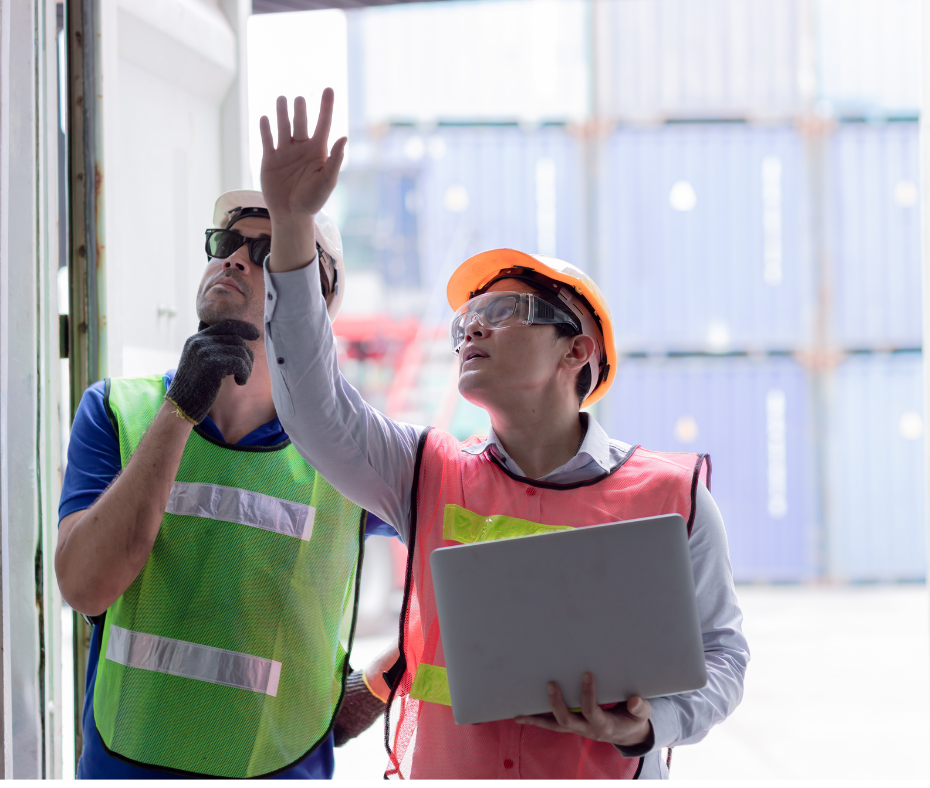
Technologie wspierające proces normowania
Współczesne środowisko produkcyjne wymaga od przedsiębiorstw nie tylko utrzymania wysokiej wydajności i jakości, ale również elastyczności i zdolności do szybkiego dostosowywania się do zmieniających się warunków rynkowych. W tym kontekście, oprogramowanie i nowoczesne technologie stanowią wsparcie w procesie normowania, oferując możliwości, które były nieosiągalne przy tradycyjnych metodach.
Rozwiązania informatyczne, takie jak zaawansowane systemy ERP (Enterprise Resource Planning) czy dedykowane oprogramowanie do zarządzania produkcją (np. aplikacja ZaPro), poza usprawnieniem metod pracy, umożliwiają automatyzację wielu aspektów normowania, od zbierania danych, przez ich analizę, aż po wdrażanie i monitorowanie norm. Te systemy mogą gromadzić i przetwarzać dane w czasie rzeczywistym, dostarczając cennych informacji niezbędnych do precyzyjnego ustalania norm wydajności i jakości.
Ponadto, narzędzia takie jak oprogramowanie do symulacji procesów produkcyjnych pozwalają na modelowanie i testowanie różnych scenariuszy produkcyjnych bez konieczności fizycznego przeprowadzania eksperymentów w rzeczywistym środowisku pracy. Dzięki temu, menedżerowie mogą eksperymentować z różnymi ustawieniami procesów, materiałami czy harmonogramami pracy, aby znaleźć optymalne rozwiązania, które zostaną następnie zastosowane w produkcji.
Przykłady wykorzystania oprogramowania w normowaniu
Jednym z przykładów wykorzystania oprogramowania w normowaniu jest stosowanie systemów zarządzania jakością, które integrują normy jakościowe bezpośrednio z procesami produkcyjnymi. Systemy te, często zgodne z międzynarodowymi standardami jakości, takimi jak ISO 9001, automatycznie monitorują wskaźniki jakości produktów i procesów, alarmując w przypadku odchyleń od ustalonych norm. Pozwala to na szybką reakcję i korektę procesów, zanim problemy jakościowe przełożą się na straty produkcyjne.
Kolejnym przykładem jest wykorzystanie zaawansowanych systemów MES (Manufacturing Execution Systems), które zapewniają szczegółową wizualizację i kontrolę nad każdym etapem produkcji. Oprogramowanie MES może automatycznie zbierać dane dotyczące wydajności maszyn i pracowników, analizując je w kontekście ustalonych norm wydajności. Pozwala to na identyfikację wąskich gardeł produkcyjnych, nieefektywnych procesów oraz na bieżąco dostosowywanie planów produkcyjnych do aktualnych warunków pracy.
Dodatkowo, w ostatnich latach na znaczeniu zyskują rozwiązania oparte na sztucznej inteligencji i uczeniu maszynowym, które mogą przewidywać przyszłe trendy produkcyjne, analizować złożone wzorce danych i sugerować optymalizacje procesów. Takie narzędzia stają się nieocenione przy dynamicznym ustalaniu norm, które muszą uwzględniać nie tylko historyczne dane, ale również przewidywać przyszłe zmiany w produkcji, popycie na produkty czy dostępności surowców.
Wdrożenie nowoczesnego oprogramowania i narzędzi technologicznych w procesie normowania otwiera przed przedsiębiorstwami produkcyjnymi nowe możliwości optymalizacji i automatyzacji, umożliwiając im nie tylko poprawę efektywności i jakości, ale również zwiększenie elastyczności i zdolności do innowacji.
Praktyczne wskazówki i najlepsze praktyki
Jak skutecznie wdrażać i aktualizować normy?
Wdrożenie i aktualizacja norm produkcyjnych to podstawowe elementy zarządzania procesami produkcyjnymi, które wymagają strategicznego podejścia i ciągłej uwagi. Skuteczne wdrażanie norm rozpoczyna się od dokładnego zrozumienia procesów produkcyjnych i identyfikacji wskaźników wydajności, które mają być normowane. Należy zacząć od przeprowadzenia szczegółowej analizy obecnych procesów, aby zidentyfikować obszary, które wymagają usprawnień lub standaryzacji. Ważne jest, aby zaangażować w ten proces pracowników na wszystkich poziomach organizacji, ponieważ ich doświadczenie i spostrzeżenia mogą być nieocenione w identyfikacji problemów i proponowaniu rozwiązań.
Po ustaleniu nowych lub zaktualizowanych norm, kolejnym etapem jest ich skuteczne wdrożenie. Obejmuje to szkolenie personelu, zapewnienie, że wszyscy pracownicy rozumieją nowe standardy i wiedzą, jak ich przestrzegać, oraz wdrożenie systemów monitorowania, które pozwolą na śledzenie postępów i efektywności wdrażania norm. Regularna komunikacja wyników i postępów z pracownikami jest również ważna, ponieważ promuje kulturę ciągłej poprawy i zaangażowania w osiąganie celów produkcyjnych.
Aktualizacja norm jest równie ważna, co ich początkowe wdrożenie. Świat produkcji szybko się zmienia, a normy, które były skuteczne rok temu, mogą już nie być aktualne. Proces ciągłego przeglądu i aktualizacji norm powinien opierać się na regularnej analizie danych produkcyjnych, feedbacku od pracowników oraz na bieżących trendach branżowych i technologicznych.
Przypadki użycia i studia przypadków
Przypadki użycia i studia przypadków stanowią potężne narzędzie w procesie wdrażania i aktualizacji norm produkcyjnych. Prezentują one realne scenariusze, w których przedsiębiorstwa z różnych branż z powodzeniem wprowadziły nowe normy, osiągając znaczące korzyści w zakresie wydajności, jakości i zadowolenia klientów.
Jednym z przykładów może być producent komponentów elektronicznych, który wprowadził system zarządzania przez cele (MBO) w celu zwiększenia wydajności swoich linii montażowych. Poprzez ustalenie konkretnych, mierzalnych celów dla każdego pracownika i zespołu, a następnie monitorowanie postępów w czasie rzeczywistym za pomocą oprogramowania do zarządzania produkcją, firma zdołała znacząco zwiększyć swoją wydajność produkcyjną i zmniejszyć czas przestoju maszyn.
Innym przykładem jest przedsiębiorstwo produkcyjne, które zastosowało metodologię Lean Manufacturing do zrewidowania swoich procesów produkcyjnych i ustalenia nowych norm wydajności. Poprzez identyfikację i eliminację marnotrawstwa w procesach, firma nie tylko poprawiła swoje wskaźniki wydajności, ale również osiągnęła znaczną redukcję kosztów operacyjnych, co przyczyniło się do wzrostu jej konkurencyjności na rynku.
Te przypadki użycia pokazują, jak strategiczne podejście do normowania, wsparte odpowiednimi narzędziami i technologiami, może prowadzić do znaczących usprawnień operacyjnych i wzrostu efektywności produkcyjnej. Kluczem do sukcesu jest jednak nie tylko wprowadzenie nowych norm, ale także ich ciągłe monitorowanie, przegląd i dostosowywanie do zmieniających się warunków i potrzeb przedsiębiorstwa.
Szkolenie Online
Zarządzanie Procesami i Wskaźniki KPI
Jak zacząć wdrażanie zarządzania procesami w swojej organizacji?
Jak definiować procesy w poszczególnych obszarach firmy?
Jak uzupełnić diagram SIPOC?
Jakie wskaźniki dobrać do poszczególnych procesów?
Wyzwania i przyszłość normowania w produkcji
Najczęstsze wyzwania przy wyznaczaniu norm
Wyznaczanie norm w produkcji napotyka na wiele wyzwań, które mogą wpływać na efektywność i skuteczność całego procesu. Jednym z głównych problemów jest szybkość zmian technologicznych i rynkowych, która wymusza na przedsiębiorstwach ciągłe aktualizowanie i dostosowywanie norm, aby odpowiadały one aktualnym warunkom. Dodatkowo, zróżnicowanie produktów i usług, rosnąca personalizacja i krótsze cykle życia produktów sprawiają, że utrzymanie odpowiednich norm staje się coraz bardziej skomplikowane.
Innym wyzwaniem jest zapewnienie, aby normy były realistyczne i osiągalne, jednocześnie motywując pracowników do efektywniejszej pracy. Zbyt wysokie wymagania mogą prowadzić do przemęczenia i spadku jakości, podczas gdy zbyt niskie normy mogą nie wykorzystywać pełnego potencjału produkcyjnego przedsiębiorstwa. Wyzwaniem jest również integracja norm z istniejącymi systemami zarządzania produkcją i jakością, co wymaga dokładnego planowania i współpracy między różnymi działami firmy.
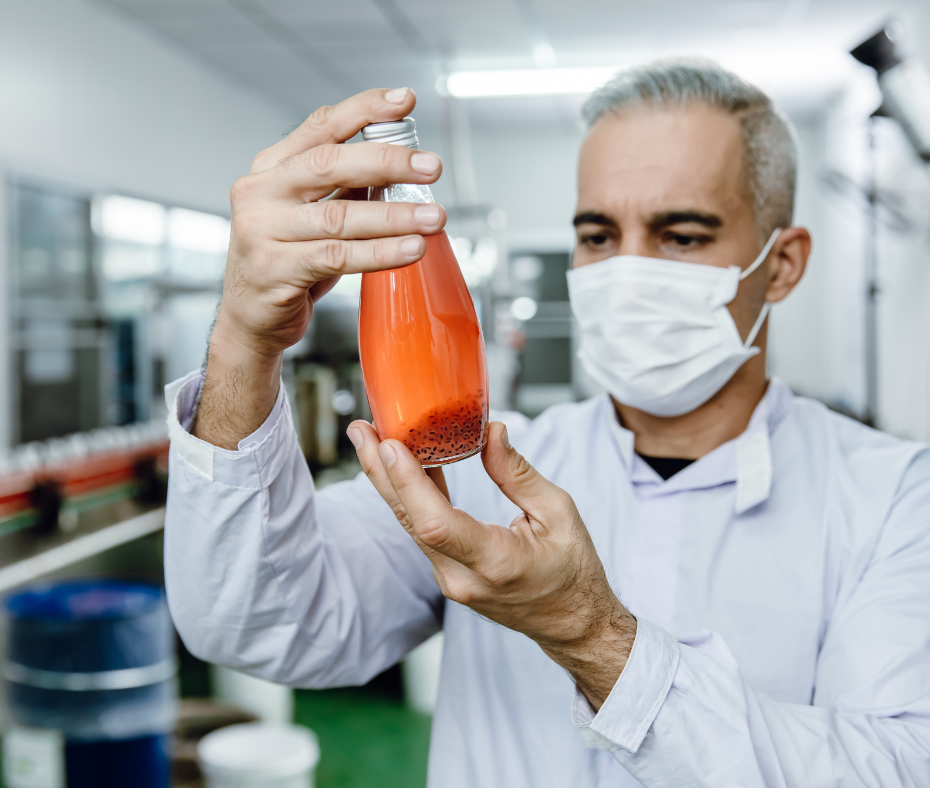
Trendy i przyszłość normowania w erze cyfryzacji
Cyfryzacja i rozwój technologii informacyjnych mają znaczący wpływ na przyszłość normowania w produkcji. Trendy te otwierają nowe możliwości dla precyzyjniejszego i bardziej elastycznego wyznaczania norm, umożliwiając przedsiębiorstwom lepsze dostosowanie się do zmieniających się warunków rynkowych i oczekiwań klientów. Jednym z kierunków jest wykorzystanie zaawansowanych narzędzi analitycznych (np. wspomnianego chronometrażu) i algorytmów uczenia maszynowego do analizy dużych zbiorów danych produkcyjnych, co pozwala na identyfikację wzorców i optymalizację procesów w czasie rzeczywistym.
Innowacje takie jak Internet Rzeczy (IoT) i cyfrowe bliźniaki (digital twins) umożliwiają dokładniejsze monitorowanie i symulację procesów produkcyjnych, co wspiera przedsiębiorstwa w szybkim dostosowywaniu norm do aktualnych potrzeb. Również rozwój technologii wearable i mobilnych aplikacji wspierających pracowników na linii produkcyjnej może przyczynić się do lepszego zrozumienia i efektywniejszego zarządzania procesami pracy.
Przyszłość normowania w produkcji będzie prawdopodobnie kierować się w stronę większej personalizacji i elastyczności, umożliwiając przedsiębiorstwom szybkie reagowanie na indywidualne potrzeby klientów i dynamicznie zmieniające się warunki rynkowe. Dążenie do ciągłej poprawy i adaptacji, wspierane przez nowoczesne technologie, pozwoli na tworzenie bardziej efektywnych i zrównoważonych systemów produkcyjnych, które będą w stanie sprostać wyzwaniom przyszłości.
Podsumowanie
Wyznaczanie normy w produkcji stanowi fundament skutecznego zarządzania procesami produkcyjnymi, umożliwiając przedsiębiorstwom nie tylko osiąganie optymalnej efektywności operacyjnej, ale również zapewnienie wysokiej jakości wyrobów. Proces ten, opierając się na precyzyjnym mierzeniu czasu pracy i zużycia materiałów, pozwala na ustalenie realistycznych celów produkcyjnych, identyfikację możliwości usprawnień i optymalizację zasobów. Normowanie produkcji odgrywa rolę w poprawie konkurencyjności przedsiębiorstwa, umożliwiając efektywne planowanie, kontrolę kosztów, a także ciągłe doskonalenie procesówWyznaczanie norm staje się jeszcze ważniejsze, stanowiąc podstawę do innowacji i adaptacji do zmieniającego się środowiska. Dlatego też, przedsiębiorstwa powinny nieustannie dążyć do udoskonalania swoich metod normowania, wykorzystując nowoczesne narzędzia i technologie, aby utrzymać swoją pozycję na rynku i sprostać oczekiwaniom klientów.
Pobierz bazę wskaźników produkcyjnych
za darmo!
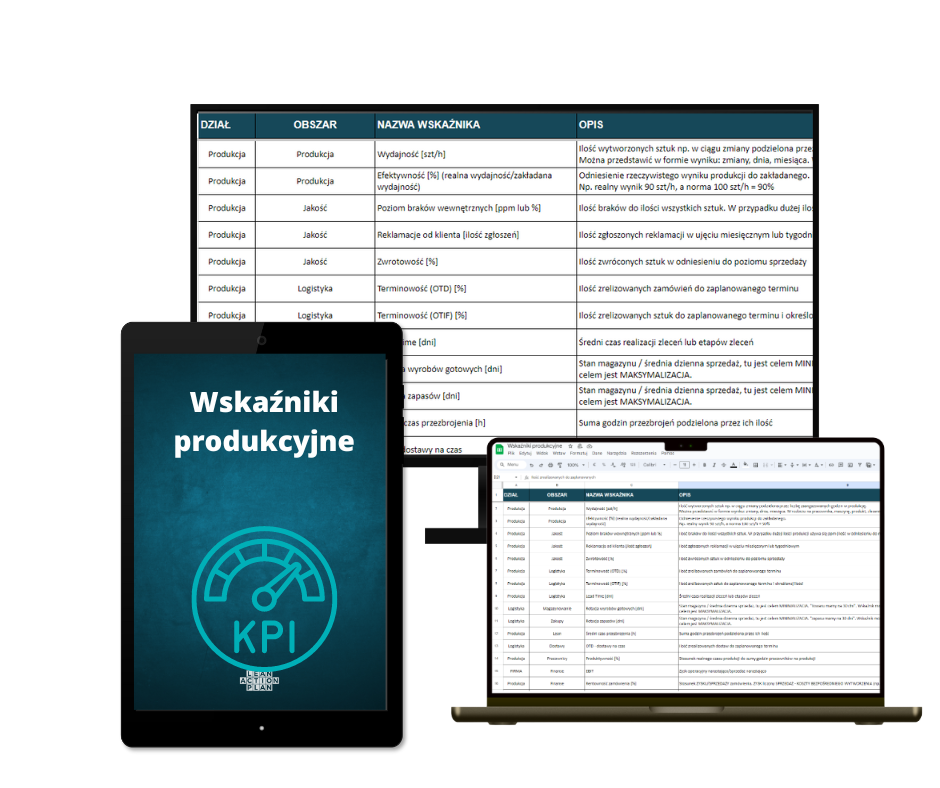