55 pytań i odpowiedzi na rozmowie rekrutacyjnej w temacie Lean
Aż 82% firm produkcyjnych poszukuje na stanowiska średniego szczebla kandydatów ze znajomością zasad Lean. Warto więc dobrze przygotować się do rozmowy rekrutacyjnej, aby nie stresować się pytaniami rekrutera. Grupa stworzona na Facebooku, pozwalająca jej członkom wymieniać doświadczenia związane z Lean Management – Niech LEAN będzie z Wami – wytypowała pytania, które bardzo często pojawiają się na rozmowach kwalifikacyjnych w firmach produkcyjnych, a także usługowych.
Rzetelnie przygotowaliśmy odpowiedzi na większość tych pytań, ale względu na specyfikę rozmowy rekrutacyjnej przygotowane odpowiedzi są raczej zwięzłe i konkretne. Pod każdą z nich znajdziesz jednak odnośnik do artykułów szerzej obejmujących dane zagadnienie.
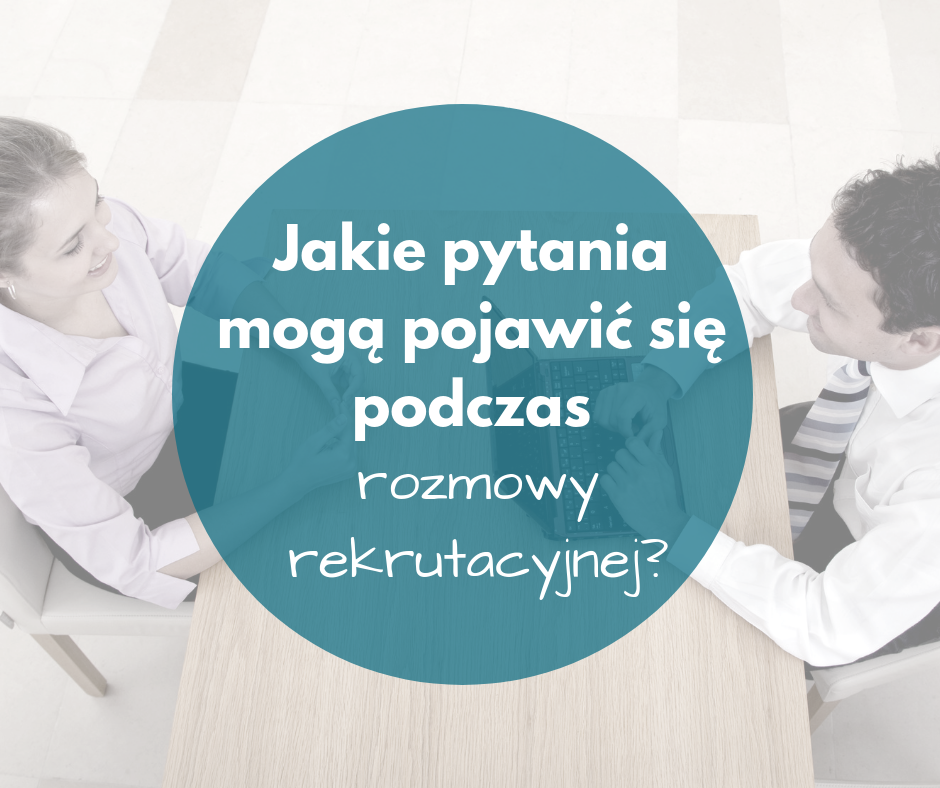
Znajdź odpowiedź na swoje pytanie:
1. Co to jest Lean?
Lean Manufacturing to system zarządzania produkcją stosowany przede wszystkim w przedsiębiorstwach produkcyjnych. Jego główną myślą jest eliminacja strat i marnotrawstw, przy jednoczesnym dostarczaniu produktów i usług o jak najwyższej jakości oczekiwanej przez klientów, zachowując niskie koszty i wykorzystując jak najmniejszą ilość surowców. Opiera się na wielu metodach i narzędziach, za pomocą których optymalizuje się kolejno wszystkie procesy występujące w firmie.
Kompleksowo o Lean możesz dowiedzieć się z artykułu: Lean Manufacturing
2. Czy z Lean’u można uzyskać certyfikat?
Nie, Lean nie jest normą, która podlega certyfikacji. Firma „jest Lean”, kiedy stosuje metody i narzędzia Lean Manufacturing oraz propaguje myśl ciągłego doskonalenia.
Można jednak zdobyć certyfikat z wiedzy o określonych zasadach czy narzędziach, po przejściu szkolenia Lean.
3. Co to jest Kaizen?
Kaizen to filozofia ciągłego doskonalenia. Zakłada ona stopniowe, ciągłe usprawnienia, które zwiększa efektywność działania, a z perspektywy produkcji – umożliwia wytworzenie większej wartości, przy mniejszych stratach.
5. Czym jest system sugestii pracowniczych?
System sugestii pracowniczych to narzędzie, za pomocą którego pracownicy mogą zgłaszać swoje sugestie czy pomysły usprawniające ich pracę. Mogą one dotyczyć nie tylko obsługiwanego przez nich procesu, ale wszystkich otaczających go aspektów. Baza Kaizen, pudełko dobrych pomysłów, aplikacja ProblemBox.
6. Czym jest 5S i na czym polega?
5S to narzędzie służące do organizacji miejsca pracy (np. stanowiska roboczego). Składa się z 5 kroków: selekcji, systematyki, sprzątania, standaryzacji i samodyscypliny.
7. Jakie znasz narzędzia, które można zastosować na stanowisku roboczym do potwierdzenia, czy produkcja jest wykonywana zgodnie z planem?
8. Czym jest standard i jakie ma zastosowanie?
Standard to pewnego rodzaju instrukcja prezentująca aktualnie najlepszą i najbardziej bezpieczną metodę wykonywania określonej czynności. Standardy opracowywane są przede wszystkim dla regularnie powtarzających się zadań. Nie są one ustalane raz na zawsze, lecz podlegają usprawnianiu. Zastosowaniem standardu nie jest wprowadzanie sztywnych procedur, których nikt się nie trzyma, lecz działania, które są bardziej wydajne, bezpieczniejsze, wysokiej jakości oraz angażujące umysłowo ludzi, którzy je wykonują.
9. Podaj przykłady zastosowania zarządzania wizualnego na stanowisku pracy.
Tablice harmonogramowania (np. produkcji lub postępów prac w projekcie),
Tablice informacyjne (np. dotyczące działań Kaizen, Systemu Sugestii),
Matryca kompetencji,
Instrukcje, standardy, One Point Lesson
Ekrany, monitory telewizyjne (zwłaszcza na halach produkcyjnych),
Wykresy, tabele, wskaźniki pokazujące realizację celów, braki, statusy, trendy,
Tablice cieni,
Tablica Andon.
10. Kiedy w procesie tworzona jest wartość dodana?
Procesy, które tworzą wartość dodaną, to takie, które zwiększają wartość wyrobu z perspektywy klienta. To produkty, które wykonane są dobrze za pierwszym razem, dostarczone są na czas oraz klient jest w stanie za nie zapłacić. W procesie wartość dodana występuje podczas czynności zwiększających wartość samego wyrobu. Może to być na przykład tłoczenie, spawanie lub przykręcanie śruby.
11. Która z 7 rodzajów start jest najgorsza? Uzasadnij.
Najgorszą ze strat jest nadprodukcja, ponieważ w związku z nią wywoływane są pozostałe straty. Zbyt duża partia produkcyjna generuje zapasy, które należy również dodatkowo transportować oraz opóźnienia w produkcji innych wyrobów. Nadprodukcja wiąże się także z nadmiernym przetwarzaniem w postaci zużycia energii maszyn, a także samych operatorów na produkcję zwiększonego zlecenia. Dodatkowo zapasy, które oczekują w magazynie mogę stracić swoje właściwości lub ulec zniszczeniu, więc pojawia się marnotrawstwo w postaci defektów lub braków w wyrobach gotowych.
12. Czym jest 8 strata i jak jej uniknąć?
Niewykorzystany potencjał ludzki.
8 strata zwraca uwagę na marnowanie kreatywności pracowników każdego dnia. Powody przychodzą na myśl bardzo intuicyjnie: zbyt duże tempo pracy – nacisk na wyniki oraz gaszenie pożarów, które są wynikiem pozostałych 7 marnotrawstw. Zazwyczaj można jej uniknąć poprzez dzielenie się odpowiedzialnością zarządzających firmą z pracownikami. To właśnie operatorzy są najbliżej procesów i codziennie mając z nimi styczność, znają je najlepiej. Należy więc wdrażać systemy dzielenia się praktyką, doświadczeniem i pomysłami w postaci systemów sugestii oraz kół jakości.
13. Jakie znasz rodzaje czynności ze względu na tworzenie wartości dodanej?
W procesach wyróżniamy trzy kategorie czynności:
Czynności dodające wartości (VA – Value Added), a więc czynności dodające wartość produktowi. Charakteryzują się tym, że w ich wyniku produkt ulega przekształceniu, są wykonane dobrze za pierwszym razem i klient jest w stanie za nie zapłacić.
Czynności nie dodające wartości (NVA – Non-Value Added), które nie wpływają na transformację produktu i klient nie chciałby płacić. Czynności takie dzieli się na dwie kategorie:
Czynność konieczne – Marnotrawstwo I stopnia: Takie straty, które są wymuszone procesem lub technologią i są trudne do całkowitego wyeliminowania. Zalicza się do tego czynności konieczne, które muszą być wykonane, aby proces właściwie funkcjonował (np. logistyka wewnętrzna) lub jest to wymagane z punktu widzenia przepisów BHP, prawa lub zachowania odpowiednich norm.
Czynności zbędne – Marnotrawstwo II stopnia: Czynności całkowicie zbędne, łatwe do wyeliminowania poprzez odpowiednią organizację pracy.
14. Jak przystąpić do wdrażania systemu sugestii pracowniczych?
Pierwszym krokiem będzie weryfikacja poprzednich doświadczeń przedsiębiorstwa w zakresie systemu sugestii. Następnie należy dostosować nowy program do przedsiębiorstwa w oparciu o doświadczenia. Kolejny krok to wyznaczenie założeń i celów systemu, a także regulaminu. Wprowadzenie programu powinno zostać dobrze zaplanowane i szeroko skonsultowane, a także aprobowane przez kierownictwo. Ostatnim etapem wdrożenia będzie pozytywne propagowanie nowego systemu, zachęcenie pracowników do korzystania z programu. Warto również zorganizować szkolenie, które uświadomi pracownikom, jak wartościowe będą ich usprawnienia dla całego przedsiębiorstwa.
15. Czy KAIZEN oznacza to samo co system sugestii pracowniczych ? Uzasadnij.
Kaizen to japońskie słowo oznaczające dobrą zmianę, poprawę. Stanowi ono podstawę filozofii ciągłego doskonalenia. Jego celem jest wyeliminowanie marnotrawstwa w strumieniu wartości. System sugestii pracowniczych może znacząco wpłynąć na poprawę funkcjonowania przedsiębiorstwa, jednak nie jest tym samym co Kaizen. Jako filozofia pracy Kaizen propaguje stałe, stopniowe doskonalenie się we wszystkich obszarach, a więc jest pojęciem szerszym, niż sugestie pracowników, mimo, że podkreśla wagę zaangażowania każdego pracownika – od prezesa po najniższego rangą operatora maszyny.
16. Czym są i jak się prowadzi warsztaty KAIZEN?
Warsztaty Kaizen to cykliczne spotkania zespołów projektowych, które angażują wszystkich pracowników firmy w działania operacyjne nad problemami lub czynności poprawiające efektywność pracy.
Sam przebieg warsztatu zależy od realizowanych działań oraz założonych celów. Można jednak wyróżnić kilka punktów, przez które na ogół przechodzą wszystkie zespoły:
Rozwiązywanie problemów (np. za pomocą narzędzia 5 WHY lub Diagramu Ishikawy);
Identyfikacja i eliminacja źródeł marnotrawstw;
Podział zadań na poszczególnych członków zespołu i wprowadzanie codziennych małych zmian;
Wdrażanie wypracowanych rozwiązań problemów i pomysłów w cyklu PDCA.
17. W trakcie warsztatów kaizen, zespół tworzy wiele pomysłów. Nie wszystkie są związane z tematem warsztatów lub nie prowadzą do osiągnięcia założonego celu. Jak poradził byś sobie z takimi pomysłami, jednocześnie nie demotywując zespołu?
Bardzo dobrą praktyką jest prowadzenie Bazy Kaizen, w której gromadzi się wiele działań do wdrożenia. Część z nich nie będzie miała określonej daty realizacji i trafi do tzw. „zamrażarki”. Możliwe, że nie wszystkie aktualne pomysły dotyczą tematu warsztatów, jednak mogą przydać się później w realizacji kolejnych działań.
18. W jaki sposób możesz wykorzystać tablice zadaniowe, zwane także tablicami kanban lub SCRUM do usprawnienia komunikacji?
Na tablicy kanban znajdują się zadania do realizacji, przedstawione za pomocą różnokolorowych kart. Karty przesuwane są odpowiednio przez kolejne kolumny tablicy, które odpowiadają kolejnym etapom procesu. Tablica kanban może być stosowana do usprawnienia komunikacji, ponieważ posiada jasny podział statusów realizacji poszczególnych działań. W każdej chwili można sprawdzić, na jakim etapie znajduje się dane zadanie. Zazwyczaj występują tablice z podziałem na trzy kolumny: „Zaplanowane”, „W trakcie realizacji” oraz „Zrealizowane”
Tablica SCRUM umożliwia natomiast działanie bardziej projektowe. W pierwszej kolumnie znajduje się temat, który jest jednocześnie nazwą projektu. Kolejne 4 kolumny informują o statusie wyznaczonych w ramach projektu działań „Do zrobienia”, „W trakcie realizacji”, „Do weryfikacji” oraz „Gotowe”.
19. Opisz zastosowanie matrycy kompetencji, zwanej także matrycą umiejętności.
Matryca kompetencji zawiera informację o stopniu zaawansowania umiejętności wykonywania danej czynności przez pracownika. Dzięki takiej wiadomości można szybko zastąpić pracownika podczas jego nieobecności w kluczowych procesach. Matryca kompetencji daje również kierownikowi informację, czy należy zorganizować szkolenie z jakiegoś zakresu lub które pożądane cechy należy wśród pracowników rozwijać.
Najważniejszą kwestią przy projektowaniu matrycy jest stosowanie się do zasady „im mniej, tym lepiej”. Jeśli chcemy uzyskać bardzo szczegółowe informacje, możemy zaciemnić obraz zbyt dużą ilością danych. Wtedy takie narzędzie będzie uciążliwe w użyciu.
20. Omów poszczególne etapy 5S.
1S – SELEKCJA, podział rzeczy w obszarze roboczym na potrzebne, niepotrzebne i możliwe, że potrzebne. W tym etapie organizuje się kampanię czerwonych kartek, która pomaga w określeniu istotności oznaczonych rzeczy oraz wizualizuje skalę zjawiska gromadzenia niepotrzebnych rzeczy.
2S – SYSTEMATYKA¸ wybranie optymalnych miejsc dla wszystkich rzeczy w obszarze roboczym w odpowiedniej ilości i tylko tam, gdzie są potrzebne.
3S – SPRZĄTANIE, gruntowne wyczyszczenie obszaru roboczego oraz przegląd narzędzi, urządzeń i maszyn.
4S – STANDARYZACJA, ustalenie modelowych standardów, instrukcji i procedur w celu utrzymania pierwszych 3S.
5S – SAMODYSCYPLINA, stworzenie nawyku dbania i ciągłego doskonalenia swojego stanowiska pracy.
21. Kiedy używany jest diagram Ishikawy – w jakim procesie?
Diagram Ishikawy służy poszukiwaniu przyczyn źródłowych problemów. Może być stosowany w każdym procesie, jako metoda analizy przyczynowo – skutkowej. Wyróżnia się 5 podstawowych kategorii (Maszyny, Ludzie, Metody, Materiały, Zarządzanie), według których klasyfikuje się przyczyny problemu, jednak można stosować zupełnie dowolne kategorie. Ze względu na tą uniwersalność może być wykorzystywany w różnych procesach.
22. Na czym polega praca z diagramem Ishikawy?
Metoda jest bardzo prosta w użyciu. Rozpoczyna się określeniem problemu – skutku, a następnie identyfikacji wszystkich przyczyn, które mogły go spowodować. Zgodnie z metodologią przyczyny klasyfikuje się w pięciu głównych kategoriach (5M). Nie jest to jednak konieczny warunek, można bowiem stosować dowolne kategorie i dowolną ich liczbę.
Machinery (Maszyny)
Manpower (Ludzie)
Methods (Metody)
Materials (Materiały)
Management (Zarządzanie)
W kolejnym kroku w każdej z kategorii określa się przyczyny, które mogły wpłynąć na wstąpienie zidentyfikowanego problemu. Istotnym jest skupienie się na jednej kategorii i podanie wszystkich możliwych, występujących w jej ramach, przyczyn problemu. Dopiero po wyczerpaniu sugestii można przejść do kolejnej kategorii.
23. Jakie ma zastosowanie metoda 5Why?
Metoda 5 WHY wykorzystywana jest do poszukiwania przyczyn występujących problemów. Polega na zadawaniu pytania „Dlaczego?” po każdej kolejnej odpowiedzi, aż dojdzie się do przyczyny źródłowej.
24. Czy w metodzie 5Why zawsze zadaje się 5 pytań? Ile pytań należy zadać?
Metoda 5 Why oznacza zadanie 5 pytań „Dlaczego?”, jednak nie trzeba sztywno się tego trzymać. Czasami zadając piąte pytanie można otrzymać absurdalną odpowiedź i lepiej poprzestać na czwartym, jeśli właśnie to ukazuje przyczynę problemu. Oczywiście może się zdarzyć, że trzeba zadać więcej pytań, aby dojść do sedna. Ile więc pytań należy zadać? Wszystko zależy od zdrowego rozsądku.
25. Do czego służy Andon i jakie znasz sposoby jego realizacji?
Andon, czyli wizualizacja pracy maszyn i urządzeń, służy poprawie przepływu informacji i stabilności procesów oraz przyśpieszeniu podejmowania decyzji i rozwiązywania problemów za pomocą oddziaływania bodźcami wzrokowymi.
Andonem może być zarówno lampka sygnalizująca aktualny stan maszyny, jak i ekrany ze wskaźnikami, a także przezroczyste obudowy pozwalające obserwować pracę maszyny oraz monitorować poziom materiałów.
26. Na czym polega system TPM?
TPM, czyli Total Productive Maintenance, to metodologia prawidłowego utrzymania maszyn. Polega na tworzeniu stabilnego systemu zapobiegania stratom i eliminowaniu wypadków, defektów oraz awarii. Obejmuje całe przedsiębiorstwo od produkcji po administrację i angażuje wszystkich członków firmy w działania nad budową solidnego przedsiębiorstwa.
Działania w zakresie TPM zawierają się w 8 filarach Domu TPM, którymi są: Autonomiczne Utrzymanie Ruchu, Doskonalenie, Planowane konserwacje maszyn i urządzeń, Planowanie inwestycji w park maszynowy, Zapewnienie jakości, Szkolenia, Zarządzanie parkiem maszynowym oraz BHO i Środowisko.
27. Omów zasadę Pareto i podaj przykłady zastosowania.
Jedynie 20% przyczyn generuje 80% skutków. Oznacza to, że mniejszym wysiłkiem można osiągnąć większe efekty, kiedy kluczowe działania skoncentruje się wokół tych 20%. Należy więc wyznaczyć te czynności, które przynoszą największe efekty i skupić się na ich optymalizacji.
Przykłady:
20% klientów generuje 80% przychodów = skupienie się na profesjonalnej obsłudze kluczowych klientów
20% maszyn generuje 80% awarii = zastosowanie prewencyjnych działań dla najbardziej wadliwych maszyn
20% produktów generuje 80% sprzedaży = poprawa efektywności produkcji kluczowych wyrobów
28. Omów zasadę ABC.
Analiza ABC służy do zarządzania zapasami poprzez ich podział na trzy kategorie:
A – najdroższe towary, wymagające szczególnej uwagi, najczęściej wykorzystywane;
B – średnio wartościowe towary;
C – pozostałe, najmniej wartościowe pozycje.
Podział na te kategorie umożliwia zastosowanie efektywnej gospodarki magazynowej, priorytetyzację dbałości o asortyment i wdrożenie odpowiednich procedur oraz adekwatną analizę cen towarów i produktów na rynku.
29. Czym się różni czas taktu od czasu cyklu i czasu przejścia?
Czas taktu i czas cyklu został przedstawiony na poniższej ilustracji.
Czas przejścia (Lead Time) jest to czas potrzebny na przeprowadzenie wszystkich czynności w procesie od momentu wejścia do procesu do momentu wyjścia z procesu i uwzględnia wszelkie przestoje oraz zakłócenia mające miejsce podczas pracy.
30. Czym jest SMED i jakie korzyści płyną z jego stosowania?
SMED – Single Minute Exchange of Die – to metodologia stosowana to skrócenia czasu przezbrojenia maszyny poniżej 10 min.
Korzyści:
Zwiększenie elastyczności produkcji – realizacja zlecenia klienta bez gromadzenia zapasów,
Przyspieszenie dostaw – produkcja małych partii oznacza krótszy czas produkcji,
Poprawa jakości wyrobów – mniejsza ilość zapasów oraz zwiększona ich rotacja prowadzi do zmniejszenia liczby usterek podczas składowania, SMED eliminuje również błędy związane z ustawieniem maszyn i próbnymi seriami,
Zwiększenie wydajności maszyn – skrócenie czasu przestoju i zwiększenie dostępności maszyn.
31. Jaka jest rola standardu?
Standard to najbardziej efektywny sposób wykonywania danej czynności ze względu na czas, koszt i jakość. Rolą standardu jest ujednolicenie sposobu wykonywania operacji przez każdego pracownika.
Standard stanowią podstawę wszelkich działań doskonalących. Oznacza to, że bez standardów nie ma żadnego punktu odniesienia do planowanych usprawnień oraz danych pozwalających oszacować faktyczną efektywność procesów w przedsiębiorstwie.
32. Omów zasadę PDCA.
Koło PDCA (Cykl Deminga) to opracowana przez Edwarda Deminga metoda podejścia do wdrażania zaplanowanych działań. Składa się ona z cyklu 4 kroków, podczas których weryfikowana jest postawiona hipoteza.
Plan – postawienie hipotezy. Należy precyzyjnie określić plan działania, nakreślić cele i przedstawić spodziewane rezultaty.
Do – test postawionej hipotezy. Należy wdrożyć zaplanowane działania, po czym poddać proces dokładnym obserwacjom oraz dokładnie przeanalizować zebrane dane.
Check – porównanie faktycznych wyników uzyskanych przy testowaniu postawionej hipotezy, ze spodziewanymi rezultatami.
Act – jeżeli nie zostały osiągnięte zakładane rezultaty – rozpoczęcie cyklu od nowa. Następuje weryfikacja planu, założonych celów i sposobu działania, a także wprowadzenie poprawek. Należy ponownie przetestować hipotezę i porównać wyniki. Jeśli okaże się, że założenia zostały spełnione, należy zadziałać w kierunku utrzymania opracowanego rozwiązania, czyli opracować standardy do praktyk będących wynikiem cyklu.
33. Na czym polega balansowanie linii produkcyjnej?
Balansowanie linii opisuje narzędzie Heijunka. Polega na wyrównaniu harmonogramu opisującego, jaki produkt i w jakim czasie należy wyprodukować. Celem Heijunka jest wygładzenie harmonogramów do tego stopnia, by z dnia na dzień niemal nie było w nich różnic. Heijunka umożliwia istnienie ciągłego przepływu, sygnałów ciągnięcia i minimalizację i magazynowania.
Poziomowanie produkcji odbywa się np. poprzez:
połączenie operacji,
przeniesienie operacji na inne stanowisko,
dodatkowe stanowisko do podziału najbardziej obciążonej operacji.
34. Jakie zastosowanie ma system kanban?
System kanban wizualizuje dostawy części, półwyrobów i materiałów do produkcji w momencie wystąpienia faktycznego zapotrzebowania na te elementy. Stosowany jest jako sygnał oznaczający konieczność złożenia zamówienia, w celu uzupełnienia braków.
Kanban jest także systemem komunikacyjnym, który pozwala utrzymać spójność i harmonię wszystkich działań.
36. Czym jest supermarket i jakie ma zastosowanie?
Supermarket to rodzaj magazynu działający zgodnie z zasadą FIFO, posiadający wyznaczone poziomy min – max, ze ściśle przypisaną lokalizacją.
W supermarkecie wyroby przypisane są do ustalonych miejsc (adresy magazynowe), mają jasno określony poziom minimalny i maksymalny utrzymywanego wyrobu. Dodatkowo posiada wizualną informację o obecnym stanie magazynowym.
37. Co to są KPI i jakie mają zastosowanie?
KPI – Key Performance Indicators (Kluczowe wskaźniki efektywności) to finansowe i niefinansowe wskaźniki stosowane jako mierniki w procesach pomiaru stopnia realizacji celów organizacji.
Cała organizacja zna założone cele i podąża w jednym kierunku,
Posługiwanie się przez wszystkich pracowników wspólnym językiem,
Dostrzeganie postępów codziennej, żmudnej pracy,
Podnoszenie wartości podejmowanych decyzji, bazując na rzeczywistych danych,
Dostosowanie codziennych czynności do realizowanych przez organizację celów,
Realny wpływ na kondycję firmy,
Zapewniają obiektywność oceny osiąganych wyników.
38. Czym różnią się KPI lokalne od KPI globalnych ?
Globalne wskaźniki KPI dotyczą działalności całej firmy i ogólnej jej strategii. Poruszają się w zakresie danych obszarowych oraz wyników finansowych firmy. Wizualizację takich wskaźników można przedstawić za pomocą wieży wskaźnikowej.
Lokalne wskaźniki KPI dotyczą bezpośrednio procesów i stanowiska roboczego, a więc małych obszarów. Wizualizacją tych wskaźników może być np. tablica na produkcji.
Szkolenie Online
Zarządzanie Procesami i Wskaźniki KPI
Jak zacząć wdrażanie zarządzania procesami w swojej organizacji?
Jak definiować procesy w poszczególnych obszarach firmy?
Jak uzupełnić diagram SIPOC?
Jakie wskaźniki dobrać do poszczególnych procesów?
39. Jakie znasz narzędzia do rozwiązywania problemów?
Genchi Genbutsu
Wykres Pareto
Arkusze kontrolne
Diagram Ishikawy
Histogram
Diagram korelacji
Cykl PDCA
Raport A3
5 WHY
8D
40. Omów zastosowanie arkusza A3.
Arkusz A3 wykorzystywany jest przede wszystkim do rozwiązywania problemów. Sam proces gromadzenia informacji oraz opracowywania planu działania, a także konieczność akceptacji przez przełożonych jest okazją do rozwoju i rodzi potrzebę współpracy. Służy więc również do komunikacji między autorem a przełożonymi.
41. Opisz etapy rozwiązywania problemów metodą A3.
1.Identyfikacja problemu i krótki opis
Wyjaśnienie, co jest tematem raportu oraz krótki opis kontekstu powstałego problemu.
2.Obecny stan
Wskazanie różnic między stanem aktualnym a stanem oczekiwanym, wizualizacja faktów i danych za pomocą wykresów czy diagramów.
3.Oczekiwany stan, cele
Wyniki, które zostaną osiągnięte po zmianach. Jakie zmiany zostaną wprowadzone. Użyte dane, fakty, liczby potwierdzą istotność działania.
4.Analiza przyczynowo – skutkowa
Co stanowi źródłową przyczynę problemu i jakie czynniki na nią wpływają.
5.Środki zaradcze
Propozycje rozwiązań sytuacji.
6.Wdrożenie planu
Wypunktowanie kolejnych czynności zaradczych, czasu realizacji i odpowiedzialnych oraz wyznaczenie wskaźników skuteczności działań.
7.Ocena wdrożenia, potwierdzenie rezultatów
Przewidywane problemy przy wdrożeniu rozwiązania. Sposób zakończenia i podsumowania działań.
42. Jaka jest rola wskaźnika OEE?
Wskaźnik OEE definiuje, w jakim stopniu wykorzystaliśmy nasze moce produkcyjne. Jest on jednocześnie wypadkową trzech innych wskaźników:
Dostępności – stosunku czasu zaplanowanego na realizację zadania do czasu, który w rzeczywistości możemy na to zadanie poświęcić. Dostępność obniżana jest przez awarie i zależna od przyjętej metody przez przezbrajanie i ustawianie maszyn.
Wykorzystania – jest to stosunek czasu dostępnego do rzeczywistej pracy. Dostępność jest zaniżana przez straty prędkości wykonywania operacji. Inaczej mówiąc – skoro przypisaliśmy pewną pulę czasu maszynie na pracę, to powinna przez ten czas wyprodukować pewną ilość produktów – wskaźnik wykorzystania pokazuje nam, na ile to się udało.
Jakości – stosunek liczby dobrych i wadliwych produktów.
Wskaźnik wyliczamy, mnożąc wymienione trzy składowe. Innymi słowy, OEE = Dostępność ∙ Wykorzystanie ∙ Jakość
43. Na czym polega system audytów Kamishibai?
System audytów Kamishibai ma wspomóc utrzymanie odpowiednich nawyków i ustalonych standardów przez pracowników. Polega na prostych audytach, mających na celu nie tylko kontrolę wykonywanej pracy, czy stosowania narzędzi Lean Management, ale również edukację osoby przeprowadzającej audyt identyfikacji marnotrawstw i nowych usprawnień. Jest to bardzo dobra okazja nie tylko do wypracowania samodyscypliny, ale również lepszego poznania przedsiębiorstwa, występujących w nim procesów oraz samych pracowników i wzajemnego szacunku. Podczas stosowania audytów Kamishibai obserwuje się również poprawę jakości i bezpieczeństwa w firmie.
44. Co to jest VSM i jakie ma zastosowanie?
VSM – Value Stream Mapping (Mapowanie Strumienia Wartości) to dogłębna diagnoza badanego procesu, dostarczająca szerokiego wachlarza informacji począwszy od charakterystyki klienta i jego wymagań poprzez dostawców, aż do kompleksowej analizy procesu produkcyjnego. Mapowanie pozwala nie tylko identyfikować zakłócenia w strumieniu i eliminować je bądź ograniczać, ale również poznać proces pozyskując kluczowe dane na każdym z jego etapów. Stworzona mapa dostarcza zatem spójnego obrazu całego procesu oraz szczegółowych zbliżeń na każdy z etapów.
Głównym celem mapowania strumienia wartości pozostaje identyfikacja i eliminacja marnotrawstw wydłużających tzw. Lead time, czyli czas przejścia produktu przez proces do momentu dostarczenia go do klienta.
Jesteś właścicielem firmy i chcesz doszkolić swoją kadrę w zakresie mapowania wartości? Sprawdź szkolenie VSM, które przygotowaliśmy! To warsztaty, które odbywają się w Twojej firmie w formie warsztatu zamkniętego.
45. Jak możesz wykorzystać czas taktu do optymalizacji liczby pracowników?
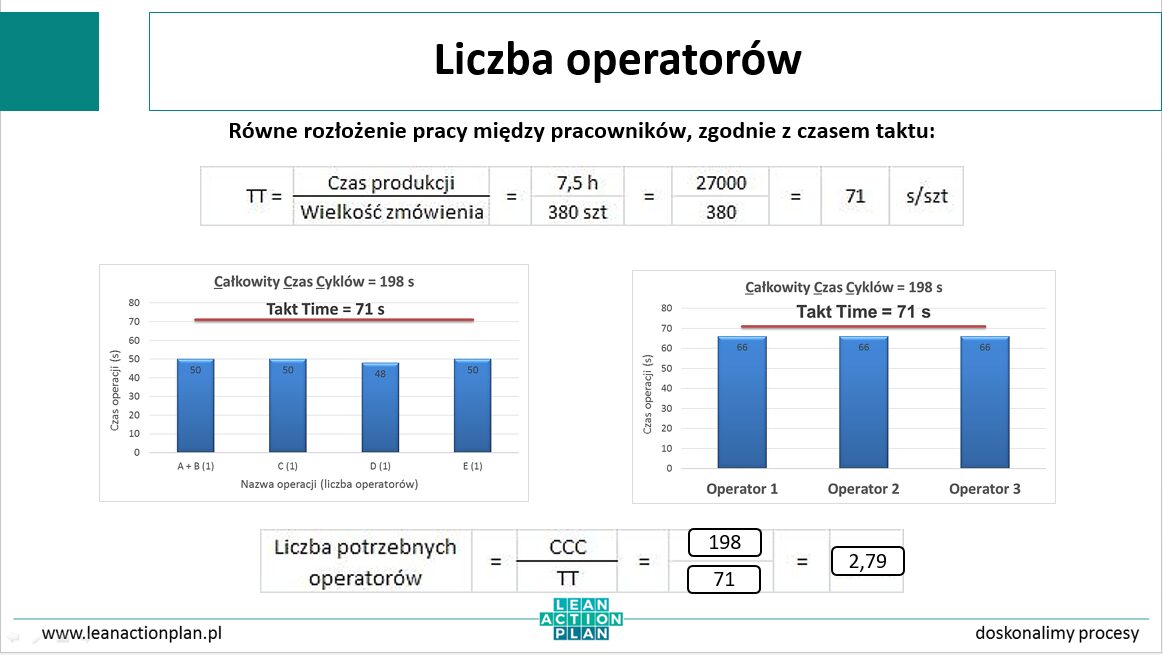
Czas taktu porównywany jest do czasu każdej operacji, aby rozłożenie zadań między pracowników było równomierne. Na tej podstawie można wyznaczyć liczbę pracowników niezbędnych do wykonania danej czynności.
46. Czym jest SIPOC i do czego jest wykorzystywane?
SIPOC to skrót angielskich słów:
S – Supplier (Dostawca)
I – Input (Wejście)
P – Process (Proces)
O – Output (Wyjście)
C – Customer (Klient)
Jest to metoda mapowania procesów, która pozwala na wysoki poziom wglądu w proces i jego analizy. Nie wizualizuje jednak żadnych punktów decyzyjnych. Jest wykorzystywana do identyfikacji obszaru procesu, w którym pojawia się problem. Pozwala również dogłębnie zrozumieć podprocesy i zależności zachodzące między nimi.
47. Czym jest Yamazumi i do czego służy?
Yamazumi (z jap.: wykresy równoważenia obciążeń) to wykres wykorzystywany do wizualizacji podziału pracy. Przedstawia on przydział operacji (najmniejszych niepodzielnych czynności) lub czynności (zbiorów operacji) do poszczególnych stanowisk roboczych. Przydział ten definiowany jest w oparciu o takt klienta oraz przyjęty współczynnik obciążenia operatora. Na jego podstawie można ocenić poziom obciążenia stanowisk roboczych i poprzez odpowiednią analizę dokonać poziomowania produkcji.
48. Co to jest Heijunka i do czego służy?
Heijunka – poziomowanie produkcji – minimalizowanie partii produkcyjnej przy ciągłym zapewnieniu dostępności produktów dla klienta. Istotą Heijunka jest wypracowanie jednakowego rytmu produkcyjnego, poprzez odpowiednie sterowanie zleceniami produkcyjnymi. Wdrażana jest w celu udoskonalenia przepływu procesu produkcyjnego, skrócenia czasu przejścia wyrobu, a także wzrostu wydajności i poprawy jakości oraz zmniejszenia obciążenia procesu produkcyjnego.
50. Omów pojęcie JiT
Just-in-time (JiT, z ang. “dokładnie na czas”) to koncepcja kładąca nacisk na synchronizację całego systemu z zapotrzebowaniem klienta. Oznacza to, że wytwarza się tylko to, co jest niezbędne, wtedy, gdy jest potrzebne oraz w wymaganej ilości – nie mniej, nie więcej. Aby działać zgodnie z tą koncepcją, wykorzystuje się następujące techniki:
Produkcja zgodna z czasem taktu – a więc zgodnie z zapotrzebowaniem klienta;
Standaryzacja pracy – spójne metody prowadzące do redukcji zmienności;
Szybka zmiana profilu produkcji – elastyczność produkcji;
Ciągły przepływ – stała dostawa produktów do klienta;
System pull – uzupełnianie zapasów zgodnie z zapotrzebowaniem klienta;
Zintegrowana logistyka – zarządzanie łańcuchem dostaw jako całościowym systemem.
51. Jaki jest cel prowadzenia warsztatów lean layout?
Po pierwsze, dlaczego zmieniamy Layout:
Zakup maszyn,
Budowa nowej hali,
Wdrożenie nowego produktu,
Wzrost produkcji,
Wycofanie produktu,
Optymalizacja przepływu.
Po drugie, dlaczego forma warsztatowa jest dobra:
Zaangażowanie szerokiego grona osób w projektowanie ustawienia,
Wzrost motywacji osób,
Poprawienie komunikacji międzywydziałowej,
Korzystanie z szerokiej wiedzy i doświadczenia
Spojrzenie z boku innych osób
52. Jakich poziomów organizacji mogą dotyczyć warsztaty lean layout?
Warsztaty Layout dotyczą wszystkich poziomów organizacji, ze względu na 4 cechy:
Plan i układ przestrzenny – pracownicy liniowi
W tym stwierdzeniu pojawiają się słowa klucze: „plan”, „przestrzenny”, „przepływ” oraz „materiał”. Każde z tych haseł ma znaczenie. Mówimy o czynności podlegającej planowaniu, co sugeruje określony wysiłek, ciągłość i celowość działania. Przestrzeń nie jest równa powierzchni, ponieważ wszystkie trzy wymiary mają znaczenie. Przepływ procesu i materiału muszą współpracować ze sobą, gdyż jedno nie istnieje bez drugiego.
Layout to proces, powtarzalny i regularny – średni szczebel
„Proces” wskazuje na sekwencję operacji, działań lub aktywności, a tym samym na podejście strukturalne. Proces nie jest projektem, czyli jednorazowym przedsięwzięciem. Proces jest powtarzalny i odtwarzalny. Tym samym layout to ciągłą podróż, bez mety.
Layout to wizja, a potem podążanie w jej kierunku – kierownictwo
To wrażliwość i regularne sprawdzanie, czy nowe pomysły i idee mieszczą się w ramach strategii umożliwiającej realizację wizji. To proces analizy i syntezy, poszukiwania optymalnych rozwiązań. To również wstęp do inwestycji i decyzji podejmowanych zawczasu – optymalnych kosztowo, jakościowo, kompetencyjnie.
Layout to w końcu strategia – najwyższe kierownictwo
Jeżeli nie jest rewidowana, sprawdzana i odświeżana, to się starzeje i może być zupełnie oderwana od rzeczywistości. Dobry layout zakładu wymaga świadomych decyzji ukierunkowanych na bliższą i dalszą przyszłość. To w końcu odpowiedzialność zarządu.
54. Dlaczego dbanie o wysokie OEE może prowadzić do obniżenia wyników finansowych przedsiębiorstwa?
nadprodukcja, zamrożony kapitał
nadmierna prewencja
uruchamianie kolejnych zmian
wszystko zależy jak się to liczy
przejście z podejścia rozsądkowego na wynikowe
55. Wyjaśnij, co Twoim zdaniem jest ważniejsze – wysokie OEE czy produkcja tego co potrzebuje klient?
W duchu Lean buduje się system oparty o dostarczanie wartości dodanej dla klienta. Produkuje się więc tyle, ile jest zaplanowane, aby zaspokoić potrzeby klienta, a nie żeby osiągnąć wysoki wskaźnik OEE. Nie należy na siłę osiągać wysokiego OEE, który ma po prostu oznaczać nadprodukcję. Należy zapewnić najlepszą jakość przy odpowiednim wykorzystaniu dostępności maszyn.
Odpowiedź brzmi więc „klient jest ważniejszy”, oczywiście z zachowaniem równowagi.
56. Czy umiesz czytać rysunek techniczny? Jakie kluczowe rysunki techniczne znasz?
Rysunek techniczny to podstawowa forma komunikacji inżynierów. Każdy pracujący w firmie produkcyjnej powinien odczytać podstawowe informacje zawarte na rysunkach technicznych w obszarach: Oznaczenia ogólnego layoutu produkcji oraz specyfikacji jakościowej opisującej wymagania klientów.
Więcej o tym w jaki sposób poznać podstawy rysunku technicznego napisaliśmy w artykule Rysunek techniczny najważniejsze informacje.
Podczas Twojej rozmowy pojawiło się jeszcze jakieś inne pytanie? A może właśnie przygotowujesz się do spotkania z przyszłym pracodawcą? Skorzystaj z możliwości komentowania pod artykułem i podziel się swoimi wątpliwościami.
Uzyskaj personalizowaną ścieżkę rozwoju kompetencji!
Widzisz — czasem trzeba zakwestionować status quo, przejąć odpowiedzialność, zaangażować się, ukierunkować na cel.
Indywidualna Analiza Możliwości Rozwojowych to badanie prowadzone przez naszych ekspertów, gdzie nie tylko rekomendujemy dalsze kroki rozwoju, ale także wskazujemy konkretne miejsca do tego.