STANDARYZACJA PRACY
Standaryzacja – jak tworzyć standard pracy, procesów i informacji
Jaka jest definicja standaryzacji? Jakie są zagrożenia braku standardów? Jak tworzyć standard i go wdrażać? Standaryzacja i korzyści z nią związane.
Wszystko o standaryzacji: cele, zastosowanie, tworzenie, wdrażanie
Standaryzacja jest podstawowym narzędziem w metodologii Lean. W prosty sposób można ją zdefiniować jako najbardziej efektywny sposób wykonywania danego procesu, biorąc pod uwagę czas, koszty i jakość. „Standardy stanowią podstawę wszelkich działań doskonalących”. Oznacza to, że bez standardów nie ma żadnego punktu odniesienia do planowanych usprawnień oraz danych pozwalających oszacować faktyczną efektywność procesów w przedsiębiorstwie.
Standaryzacja to jeden z fundamentów szczupłej produkcji (Lean Manufacturing). Praca standardowa to dokumentacja uzgodnionego (zatwierdzonego), najlepszego sposobu wykonywania danej pracy. Definiuje ona pożądaną sekwencję czynności oraz inne parametry, które gwarantują spójne wykonanie zadania. Standardy to najłatwiejsze i najbezpieczniejsze procesy dla pracowników, które są najbardziej efektywne z punktu widzenia kosztów i produktywności oraz pozwalają firmie zapewniać najlepszą jakość dla klienta. Słownik języka polskiego definiuje słowo standaryzacji jako “wprowadzenie jednolitych norm, zwłaszcza w przemyśle”. Zgodnie z tradycyjnym podejściem standaryzacja nie różni się od normalizacji i jest rozumiana jako “przeciętna norma, przeciętny typ, model, wyrób odpowiadający określonym wymogom, wzorzec”. Jak mówi słownik, obecnie rzadko używa się pojęcia normalizacji podczas prac.
Standaryzacja pracy NIE jest usztywnieniem, ani zamrożeniem zmian. Wręcz przeciwnie – standaryzacja pracy to proces dynamiczny i ma sens wyłącznie wtedy, gdy jest w równowadze z ciągłym doskonaleniem. Często niekorzystny wizerunek standaryzacji pracy wynika z niechęci do rozpowszechnionych obecnie systemów ISO. Główne zarzuty to: wzrost biurokracji, usztywnienie procedur pracy, zmuszanie pracownika do wysiłku, ograniczanie swobody pracy przez standardy.
CELE STANDARYZACJI PRACY
Celem standaryzacji pracy są zarówno standaryzacja stanowisk pracy (różne sposoby wykonywania czynności, czas wykonywania czynności), jak i wprowadzenie standaryzacji jakościowej. W ramach standaryzacji stanowisk wyróżniamy takie cele, jak:
- Eliminacja nadmiernych czynności w pracy
- Wzrost wydajności stanowiskowych
- Punkt odniesienia do poziomu dziennej produkcji
- Poprawa jakości obrabianych elementów
- Podstawa do samokontroli w pracy
- Podstawy do szkoleń
Ogólne cele standaryzacji pracy, to:
- Stabilność procesu – powtarzalne czynności, ustalona sekwencja działań
- Szkolenia zatrudnionych – punktem wyjścia są dokumenty pracy standardowej
- Identyfikowanie i rozwiązywanie problemów, podczas weryfikacji zgodności założonego przebiegu procesu ze stanem obecnym
- Kryterium pomiaru pracy – przyjęte standardy pozwalają pracodawcy rzetelnie i obiektywnie oceniać wykonanie pracy
- Uproszczenie procedur – łatwe do naśladowania schematy, oszczędzające czas
- Najbardziej efektywne, bezpieczne oraz korzystne z punktu widzenia kosztów wykonanie pracy, a także uwzględniającego dostępny czas
- Prostota procesu – standaryzacja oparta na wizualizacji (obrazki, rysunki, zdjęcia)
- Zapobieganie błędom i minimalizacji zmienności – gwarantuje, że te same błędy nie będą ponownie popełnione
- Usprawnienie przepływu materiałów oraz porządkowanie stanowiska
- Zatrzymanie wiedzy w organizacji – zgromadzona w postaci dokumentów (Każdy standard musi być zapisany!)
STAN BEZ STANDARYZACJI
- Wydajność każdego dnia znaczeni się różni
- Pierwsza zmiana ma inną wydajność niż druga
- Pracownicy mają różne wydajności
- Każdy pracownik wykonuje operacje w inny sposób
- Szkolenie nowych pracowników trwa długo
- Nowi pracownicy nie osiągają poziomu doświadczonych pracowników
- Brak informacji odnośnie odchyleń od standardu
- Brak punktu odniesienia do usprawnień
- Brak oceny zgodności osiągniętych wskaźników
- Problemy z komunikacją
- Brak jednolitego sposobu szkolenia nowo zatrudnionych
- Niepowtarzalność i przypadkowość
- Nie wiadomo, jakiego efektu się spodziewać
- Nie wiadomo, jak osiągnąć cel, “jak to zrobić?”
ZASTOSOWANIE STANDARYZACJI
Standaryzacja służy do kontroli procesów produkcyjnych poprzez zapisy na odpowiednich kartach (wypełnianie standardowych kart produkcyjnych). Prowadzi to do zwiększenia, wyrównania i monitorowania wydajności wszystkich pracowników, dzięki czemu łatwiej można zarządzać procesem produkcyjnym. Standaryzacja czynności, jest to większy projekt, który polega na udokumentowaniu najlepszych sposobów wykonania czynności. To rozwiązanie w przypadku zmiany pokoleniowej w przedsiębiorstwie, sposoby wykonywania czynności przez doświadczonych pracowników mogą być przekazane kolejnym zatrudnianym osobom. Najczęstszą formą dokumentacji opracowanych standardów są arkusze standaryzacyjne. Mogą one przedstawiać standardy wykonania całych procesów lub poszczególnych operacji i dotyczyć pracy jednego lub nawet kilku operatorów.
ELEMENTY STANDARDOWEGO ARKUSZA STANDARYZACYJNEGO
Podstawową składową arkusza standardowego jest sekwencja operacji lub czynności wraz z czasami wykonania. Opracowanie logicznej sekwencji wykonywania poszczególnych operacji zapewnia powtarzalność procesu redukującą błędy. Czasy wykonywania dają nam za to podstawę oceny wydajności stanowiska, cenne informacje do planowania pracy oraz kryterium porównawcze w postaci np.: wydajności zmianowej, godzinowej itp.
Na standardzie muszą również znaleźć się podstawowe informacje identyfikacyjne jak nazwa procesu, obszar w którym jest on prowadzony, datę opracowania i autora.
Bardzo ważnym elementem są również zdjęcia i schematy obrazujące sposób wykonywania pracy, zwracające uwagę na problemy jakościowe lub wyjaśniające problematyczne czynności.
Ostateczny kształt i forma arkusza standaryzacyjnego zależy od potrzeb. Często pojawiają się na nich również listy niezbędnych narzędzi i komponentów, uwagi do wykonania operacji. Wśród typowych arkuszy standaryzacyjnych możemy znaleźć np.: karty standaryzacyjne operacji, arkusze balansowania operatorów czy standardy zadań rutynowych.
Fragment karty standaryzacyjnej
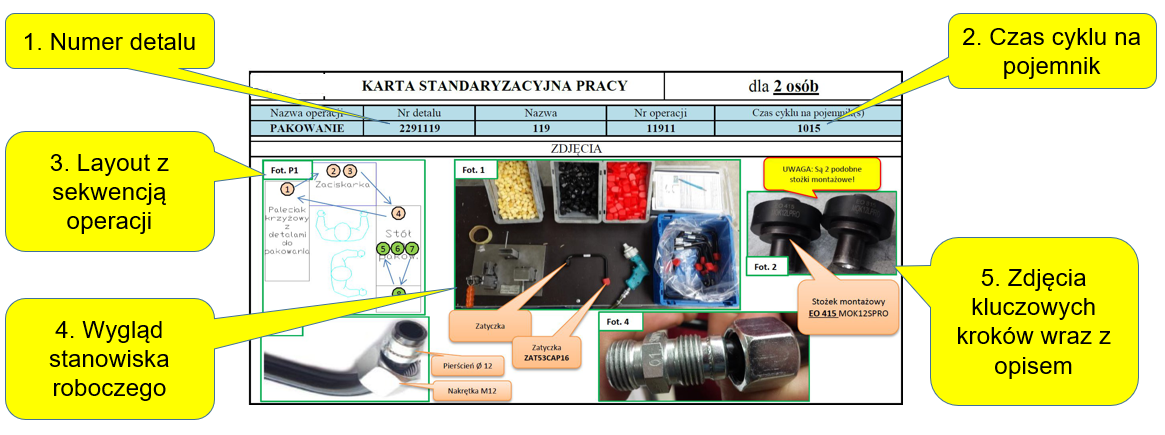
JAK STWORZYĆ STANDARD?
Aby standard był skuteczny musi posiadać pewne cechy. Przede wszystkim ma być jasny i czytelny. Bardzo dobrym przykładem jest sygnalizacja świetlna, gdzie standardowe barwy świateł wykorzystują bezpośrednie oddziaływanie bodźcami wizualnymi, powszechnie kojarzonymi z konkretnym zachowaniem (kolor czerwony – ostrzeżenie/uwaga, kolor zielony – pozwolenie/dobry stan). Są to sygnały jasne i proste w odbiorze i zrozumieniu.
Standardy nie zwalniają pracowników z obowiązku myślenia. Mają one jednak zapewnić, aby pracownicy wykonywali swoją pracę lepiej, szybciej i bezpieczniej poprzez redukcję czynności zbędnych, dlatego tak ważne jest, aby widząc opracowany arkusz standaryzacyjny pracownik od razu zrozumiał zawarty w nim sposób pracy.
Standard musi opierać się na konkretnych, zmierzonych danych. Tworząc go, należy więc kierować się zasadą genchi gembustsu, czyli zobaczyć standaryzowany proces, poczynić obserwację, zmierzyć czasy wykonywania czynności, przeanalizować zebrane dane i udokumentować pracę w postaci arkusza standardowego. Ważne jest również by nie mylić standardu z normą, czyli pamiętać o ciągłym doskonaleniu stworzonych standardów zgodnie z cyklem PDCA.
Etapy tworzenia standardów
Standaryzacja pracy powinna przebiegać płynnie, na podstawie poniższych etapów:
- Identyfikacja kluczowych działań dla danego obszaru
- Priorytetyzacja wyznaczonych działań
- Wybór zespołu współpracowników, którzy opracują ścieżkę postępowania
- Obserwacja bieżących procesów, identyfikacja różnic w sposobie działania i poszukiwanie możliwości optymalizacji
- Doprowadzenie do ogólnego porozumienia odnośnie najlepszych praktyk
- Udokumentowanie ustaleń w prosty i wizualny sposób
- Przeprowadzenie szkolenia na temat nowych standardów pracy
- Monitorowanie efektywności, rozstrzyganie problemów, przestrzeganie standardów i wprowadzanie usprawnień zgodnie z cyklem PDCA
Jak zidentyfikować kluczowe działania w standaryzacji?
Identyfikacja kluczowych procesów i działań może być związana z systemowym podejściem do organizacji. Jest ona rozumiana jako zbiór procesów. Definiując je, należy zwrócić uwagę na kilka charakterystyk, które pozwolą w pełni je opisać m.in.:
- Początek i koniec trwania procesu,
- Wejścia i wyjścia,
- Profil dostawców i klientów danego procesu,
- Właściciel procesu,
- Kluczowość – wpływ na firmę,
- Narzędzia pomiaru i kontroli,
- Używane zasoby,
- Dokumentacja procesu – standardy.
Dobrym narzędziem będzie SIPOC, pomagający zidentyfikować wszystkie elementy procesu. Tworzy się go dla działów i procesów w kliku prostych krokach:
- Określenie działu
- Definiowanie klienta
- Definiowanie dostawców dla danego procesu
- Określanie elementów dostarczanych (opis) oraz ich wskaźników (dostawa, jakość)
- Określanie elementów wyjściowych (opis) oraz ich wskaźników (dostawa, jakość)
- Wyznaczenie oceny ważności danego procesu
Warto kierować się również główną dewizą Lean Manufacturing (w końcu standaryzacja jest jego elementem), a więc pojęciem dodawania wartości. Value Added (Wartość Dodana ) – czynności, które powodują zwiększenie wartości produktu, coś za co klient gotowy jest zapłacić. Pozostała część to marnotrawstwo. Należy w pierwszej kolejności zdać sobie sprawę, które z czynności dodają wartość w naszym procesie, a które są zbędne. Pomaga to na etapie tworzenia standardu, nie pozwala utrwalać ich w pracownikach, lecz pomaga zdać sobie sprawę z koniecznych zmian.
Mając taką świadomość i przyjmując taki sposób patrzenia na cały proces produkcyjny, coraz częściej dostrzegamy możliwości poprawy i rozwoju obecnego stanu.
Analiza procesu jako element standaryzacji
Analiza procesu – jest to proces przygotowania do tworzenia standardu pracy. Polega na dokładnej obserwacji wybranego procesu i wykonywanych przez pracownika operacji. Obserwacja aktualnej sytuacji powinna wiązać się z jak najdokładniejszą dokumentacją rzeczywistości. Pomiarem czasów i spisaniem problemów i uwag.
W rzeczywistości jest to często trudne zadanie, ponieważ pracownicy często zmieniają kolejność zadań, pracują w różnym tempie oraz pojawiają się braki narzędzi lub części.
Dlatego w pierwszej kolejności podczas standaryzacji należy uporządkować proces, poprzez ustalenie kolejności zadań i ich podział na pomocnicze i podstawowe. Dopiero, gdy proces ocenimy jako stabilny, możemy przejść do standaryzacji.
Cele, które powinna spełnić analiza procesu, to:
- Ustalenia rzeczywistego przebiegu i sposobu wykonania prac
- Czas każdej z wykonywanych czynności
- Określenie strat czasu w procesach i potencjału do optymalizacji
- Standaryzacja pracy – czyli najbardziej optymalny sposób przebiegu procesu
- Szczegółowa analiza technicznych kosztów wytworzenia
- Planowanie produkcji i analiza zdolności produkcyjnych
PRZESZKODY WE WDRAŻANIU STANDARDÓW
Niechęć do zmian i siła nawyku są pierwszymi wrogami standaryzacji. Standaryzacja często poprzedzona jest działaniami 5S, a takie połączenie często owocuje całkowitą zmianą dotychczasowego stanowiska pracy – od rozmieszczenia maszyn, stołów roboczych i regałów, po diametralną zmianę sposobu wykonywania operacji. Nieocenioną pomocą jest również wiedza pracowników, do których należy podchodzić z szacunkiem jako do ekspertów w swojej dziedzinie. Zbudowanie odpowiedniej relacji owocuje nie tylko łatwiejszą drogą do wdrożenia zmian, ale i czynnym zaangażowaniem samych pracowników poprzez sugestie, pomysły i weryfikacje proponowanych rozwiązań. Trzeba dać również pracownikom czas na dostosowanie się do nowej rzeczywistości.
KORZYŚCI ZE STANDARYZACJI
Ułatwione szkolenie nowych pracowników
Poprawa stabilności procesów
Zwiększenie powtarzalności
Zwiększenie wydajności procesów
Poprawa jakości
Zobacz też: Normowanie czasu pracy 
Sprawdź aplikację: Karty Pracy – raportowanie na produkcji, która została stworzona po to, by w łatwy sposób kontrolować czas pracy oraz zarządzać zasobami w branży produkcyjnej.
KONTAKT
- Uzupełnij formularz, jeśli masz jakiekolwiek pytania dotyczące rozwoju firmy, przeprowadzenia szkolenia, wspólnych warsztatów lub czy innej formy współpracy. Jeżeli możesz podaj jak najwięcej szczegółów.
- Twoja wiadomość jest dla nas ważna, odpowiemy na nią maksymalnie kolejnego dnia roboczego.
- W zależności od pytania poprosimy Cię o niezobowiązującą rozmowę telefoniczną lub spotkanie online. Taka forma kontaktu pozwoli nam najlepiej zrozumieć potrzeby i oczekiwania.
NAPISZ DO NAS
KONTAKT BEZPOŚREDNI
Obsługa klienta
Anna Etgens
Specjalistka ds. zadowolenia klienta
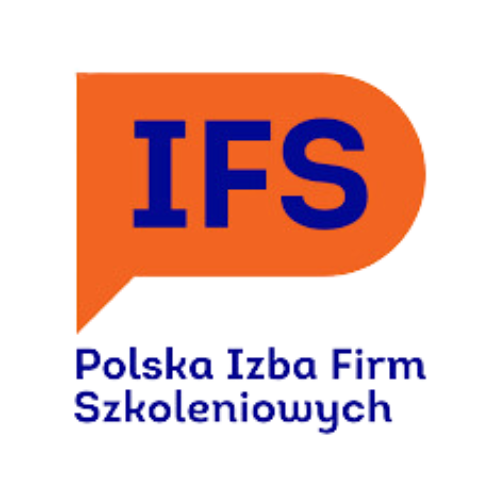
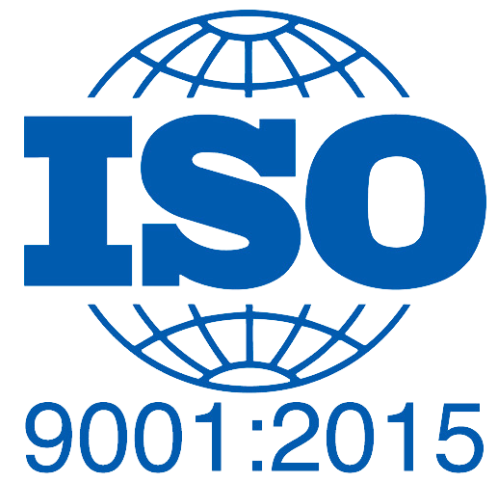