JIDOKA
WBUDOWANA JAKOŚĆ
WBUDOWANA JAKOŚĆ
Jidoka czyli tzw. Wbudowana jakość to drugi z filarów domu Toyoty.
Koncepcja Jidoka
Koncepcja Jidoka opiera się na konsekwentnym budowaniu wartości u źródła. Rozumiemy przez to eliminację wszystkich czynników obniżających jakość produktu już od samego początku strumienia wartości. Strumień wartości to wszystko to co dzieje się z produktem od momentu złożenia zamówienia przez klienta do momentu, w którym otrzyma zamówiony produkt (więcej w zakładce VSM). Jidoka oznacza brak akceptacji dla złej jakości, więc podążając za tą ideą należy zapobiegać by jakiekolwiek braki, defekty czy problemy przedostawały się do następnych etapów procesu produkcyjnego. Żeby osiągnąć wbudowaną jakość należy zmienić podejście do problemów. Trzeba traktować je jak wyzwania i stawiać im czoło.
W usprawnianiu produkcji potrzebne są konieczne narzędzia – jednym z przydatnych jest aplikacja ZaPro. To rozwiązanie stworzone na potrzeby i specyfikę branży produkcyjnej, pozwala więc na kontrolę przekroju procesów produkcyjnych.
Historia wbudowanej jakości
U źródła filozofii Jidoka leży genialny wynalazek protoplasty Totyota Motor Company Sakichiego Toyody. Stworzył on automatyczne krosno z mechanizmem przerywającym pracę w momencie przerwania jednej z nici tkackich. Takie rozwiązanie stanowi sedno Jidoki, ponieważ nie dopuszcza możliwości wypuszczenia wybrakowanego wyrobu. Trzonem całej koncepcji jest zaangażowanie operatorów i uświadomienie im odpowiedzialności za pojawiające się problemy. Obowiązkiem osoby wykonującej pracę na danym etapie jest rozwiązywanie pojawiających się problemów. W firmach mocno świadomych wartości jakie niesie za sobą koncepcja jakości budowanej u źródła, jeżeli pracownik nie potrafi rozwiązać problemu ma obowiązek zatrzymać pracę linii by mógł rozwiązać problem z pomocą innych lub przekazać go osobie będącej w stanie to zrobić. W praktyce niewiele firm decyduje się na zatrzymanie produkcji w celu rozwiązania problemu, ponieważ nie chcą lub nie mogą sobie na to pozwolić, mając na względzie przede wszystkim zobowiązania finansowe i terminowe. Powoduje to dodatkowe naprawy i korekty w późniejszych etapach procesu, opóźnienia i ostatecznie gorszej jakości wyrób, a to z kolei rodzi dodatkowe koszty.
Andon & Poka – Yoke
Narzędziami wspomagającymi utrzymanie wysokiej jakości produktu są andon oraz poka-yoke.
Andon to sygnalizacja świetlna wizualizująca stan maszyny, gniazda produkcyjnego czy też całej linii. Dzięki andonowi, nie jest konieczne zatrzymywanie całej linii gdy na konkretnym etapie pojawi się problem jakościowy. W klasycznej postaci, jeżeli pracownik użyje sygnalizatora andon by zgłosić problem jakościowy, ten zapali się na żółto. Stanowi to zgłoszenie do lidera. Zadaniem lidera jest natychmiastowe rozwiązanie problemu lub decyzja, czy można go rozwiązać w dalszych etapach, czy też należy zatrzymać całą linie. Jeżeli lider nie zareaguje do momentu zakończenia operacji na poprzednim stanowisku linia zatrzyma się automatycznie, a andon zmieni kolor na czerwony.
Poka – yoke to zbiór działań mających uniemożliwić przedostanie się wadliwego wyrobu do następnych etapów produkcji. Rozwiązania w formie poka-yoke zapobiegają przede wszystkim pomyłkom wynikającym z nieuwagi lub błędów operatorów, należy więc zapewnić takie środowisko pracy, w którym popełnienie błędu będzie niemożliwe. Możemy stosować tu wszelkie czujniki wykrywające nieodpowiednie zamontowanie komponentu lub błędną pozycję na linii, nastawy zapełniające właściwą pozycję i zamontowanie komponentu, specjalne kształty montowanych komponentów, aby nie był możliwy montaż w nieodpowiednim miejscu, lub systemowe wymuszanie poprawnej sekwencji wykonania czynności. Więcej na temat poka-yoke.
5x Why & Ishikawa
W celu ustalenia przyczyn źródłowych i poprawnego rozwiązania problemów stosowane są narzędzia analizy jakościowej – „5 x why?” oraz diagramy Ishikawy.
„5 x why?” – 5 razy dlaczego?: Niezwykle prosta metoda polegająca na zadawaniu pracownikowi pytań do momentu ustalenia przyczyny źródłowej problemu. Np.:
Dlaczego maszyna nie działa?
Ponieważ zabrakło oleju.
Dlaczego zabrakło oleju?
Ponieważ wycieka ze zbiornika.
Dlaczego olej wycieka ze zbiornika?
Ponieważ wlot jest nieszczelny.
Dlaczego wlot jest nieszczelny?
Ponieważ pękła uszczelka.
Wniosek: Należy wymienić pękniętą uszczelkę, zamiast ciągle uzupełniać braki oleju i wycierać palmy.
Jak widać na powyższym przykładzie, pytań może być mniej niż pięć lub więcej. Istotą jest dotrzeć do źródła problemu.
Diagram Ishikawy (diagram rybich ości)
Schemat, na którym wypisywane są wszystkie możliwe przyczyny zaistnienia analizowanego problemu.
Problem umieszcza się na głównej osi diagramu natomiast na odnogach umieszcza się kategorie, w których, w których szukamy przyczyn zaistnienia problemu. Więcej o diagramach rybich ości.
Redukcja zapasów
Bardzo ważnym aspektem pracy nie tylko w filozofii Jidoka, ale i całego Lean Manufacturing jest redukcja zapasów. Stanem idealnym jest eliminacja zapasów.
Zapasy wyrobów gotowych stanowią przyzwolenie na istnienie problemów jakościowych . Po co tracić czas na rozwiązywanie problemów skoro zapas może pokryć braki. Takie przekonanie nadal jest powszechne w wielu firmach. Redukcja zapasów obnaża wszelkie problemy w procesach produkcyjnych, nie ma już bowiem możliwości zmiecenia problemu pod przysłowiowy dywan i wykorzystania wyprodukowanych wcześniej zapasów na pokrycie braków. Wprowadzenie systemu ssania (pull) lub przepływu jednej sztuki (OPF – one piece folw), jest jednoznaczne z drastyczną redukcją zapasów wyrobów gotowych i eliminacją zapasów międzyoperacyjnych. To z kolei oznacza, iż produkcja musi działać bez zarzutu.
Chcesz wprowadzić kulturę ciągłego doskonalenia do swojej firmy, lub rozszerzyć świadomość pracowników? Sprawdź szkolenie ,,Lean Day“. To jednodniowe warsztaty Lean Day pozwalają na głębokie zrozumienie sensu działań Lean w organizacji.
Szkolenie Online
Intro to Lean
Na czym polega Lean i jak go wdrażać?
Podstawowe narzędzia Lean
Identyfikacja marnotrawstwa
Korzyści stosowania Lean
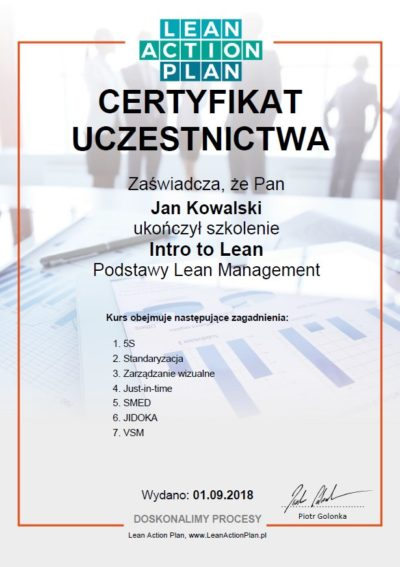