Jak stać się wszechstronnym inżynierem jakości
POWRÓĆ DO NAGRANIA Z NASZEGO SPOTKANIA LIVE:
DLA KOGO JEST TEN LIVE?
inżynierów jakości (operacyjnych)
specjalistów ds. jakości
kontrolerów jakości
PODCZAS WEBINARU DOWIESZ SIĘ
jak budować kulturę jakości, by zapobiegać błędom, a nie leczyć skutki ich powstania
dlaczego warto promować podejście procesowe
jakie są korzyści z wdrożenia schematu eskalacji problemów
jak angażować zespół oraz komunikować się w taki sposób, by zadania/oczekiwania były zrozumiałe
CO OTRZYMASZ?
podsumowanie Live’a
szablon Excel – tworzenie diagramu Pareto
szablon Excel – tworzenie histogramu
fragment kursu “Wszechstronny inżynier jakości”
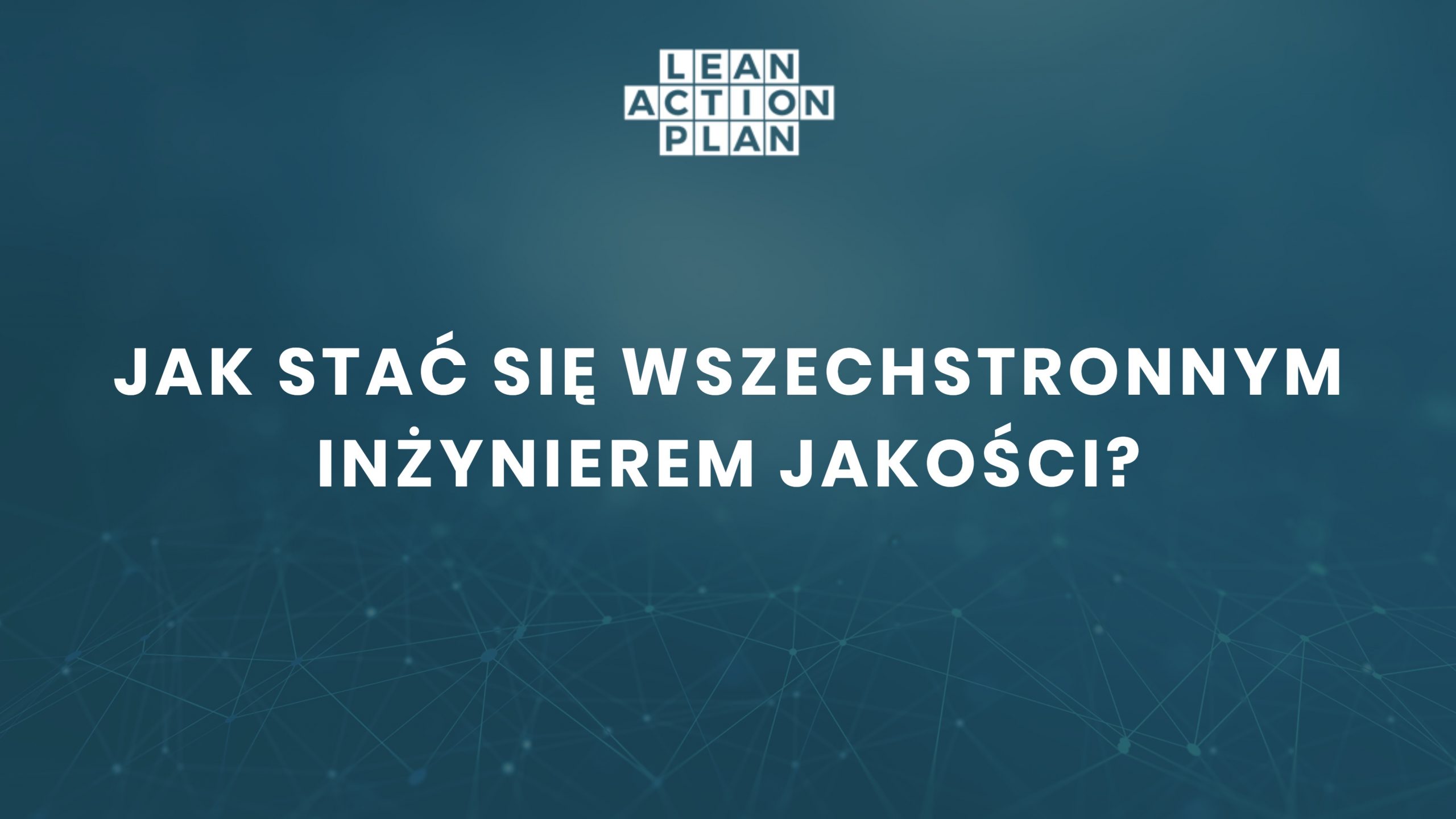
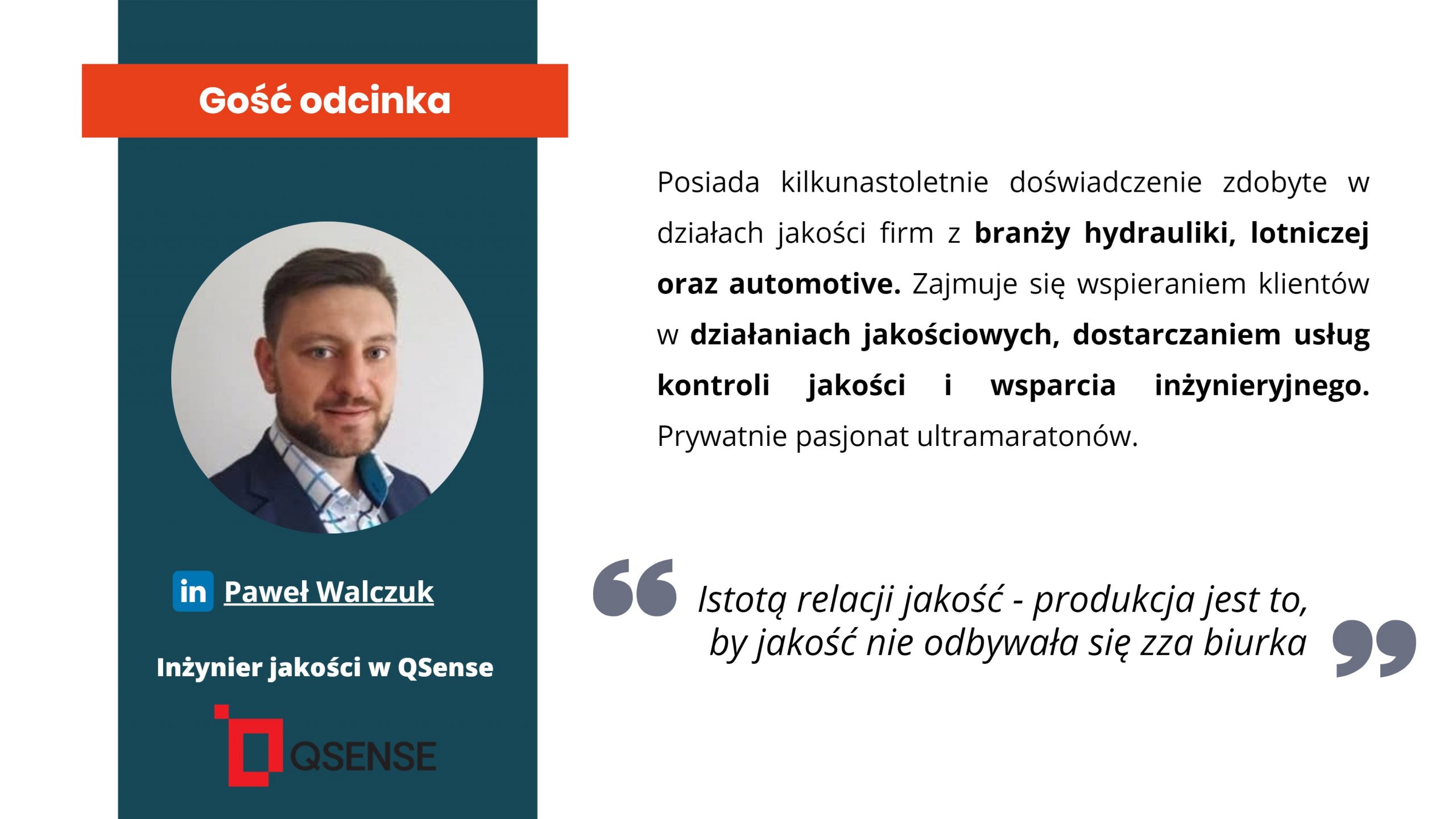
Jak stać się wszechstronnym inżynierem jakości
PAWEŁ WALCZUK
Inżynier jakości w firmie QSense. Posiada kilkunastoletnie doświadczenie zdobyte w działach jakości firm z branży hydrauliki, lotniczej oraz automotive.
Krzysztof Pawłowski: Cześć wszystkim. Tutaj Krzysiek z Lean Action Plan. Dzisiaj spotkaliśmy się w kolejnym Live Action Planie. Tym razem będziemy rozmawiać o jakości, a dokładnie o tym jak zostać wszechstronnym inżynierem jakości.
Dzisiaj będziemy mówili o pracy w jakości, o wszechstronności, o tym jakie obszary współdziałają z jakością i jakie są stanowiska jakościowe. Trochę opowiemy o problemie, który się pojawia między jakością, a produkcją, a czasem między jakością, a klientem. Wspomnimy też o zasadach, metodach, narzędziach i angażowaniu ludzi w doskonalenie jakości.
Dzisiaj moim gościem będzie Paweł “Grizzly” Walczuk. Paweł jest naszym gościem, ponieważ jest też inżynierem jakości w QSense. QSense to nasz partner w zakresie działań jakościowych, szkoleń z tematów jakości w branży automotive, a sam Paweł ma 15 lat doświadczenia w wielu firmach i wielu branżach.
Paweł Walczuk: Tak, QSense jest moim nowym doświadczeniem, ponieważ wcześniej działałem głównie na produkcji, gdzie byłem inżynierem operacyjnym. Tutaj też pracuję przy produkcji, natomiast my wspieramy klienta w jego działaniach jakościowych, dostarczamy usługi kontroli jakości i wsparcia inżynieryjnego, dlatego m.in. działam tutaj w QSense w takiej roli. Wspieramy klientów poprzez ciągłe doskonalenie, wspieranie ich procesów, dostarczanie odpowiednich danych, które im pomagają iść do przodu.
K.P.: Na początku mam jeszcze takie pytanie rozgrzewkowe. Oto pojęcie jakości. Wikipedia mówi, że jest to pojęcie filozoficzne, zdefiniowane przez Platona, jako pewien stopień doskonałości, a jak to się ma do ciebie, co dla ciebie znaczy “jakość”?
P.W.: Dla mnie jakość to nic innego jak spełnienie wymagań klienta. On ma pewne oczekiwania wobec organizacji, z którą współpracuje, a tolerancje i wymagania, które poda to zakres, w którym możemy się poruszać budując tę jakość.
K.P.: Ok, czyli bardzo mocno sprecyzowane oczekiwania, do których możemy się odnieść. Drugą kategorią jest jakość w leanie. Jaki masz stosunek do leanu? Jak współpracujesz z leanowcami, z obszarami doskonalenia procesów?
P.W.: Ja mam takie swoje spostrzeżenie, że leanowiec i inżynier procesu, to są dwaj bardzo dobrzy kumple jakościowca. I to są, przynajmniej na takiej produkcji, przy której ja pracowałem, czyli obróbka metali, dwie osoby, z którymi musisz ciągle współpracować. Jesteś pomostem łączącym bardzo dużo funkcji w organizacji. Dla mnie budowanie jakości bez wsparcia leanu i technologii byłoby bardzo ciężkie, ponieważ wszystkie narzędzia leanowe wspierają dobrą jakość i dostarczają bardzo dużo ciekawych rozwiązań. Lepsze przepływy materiału, lepszą prezentację wizualną, wdrażanie praktyk 5S itp. Te wszystkie elementy pomagają nam budować coraz lepszą jakość i doskonalić swoje procesy, a podejście procesowe jest bardzo ważne w budowaniu dojrzałej organizacji.
K.P.: Przejdziemy teraz do meritum. Przedstawiłem dzisiaj temat wszechstronności inżyniera jakości jako taką prostą drogę, która składa się z 3 punktów. Zaczynamy naszą drogę, karierę w jakimś miejscu związanym z jakością, potem jesteśmy, pracujemy w tej firmie, więc odnajdujemy się w realiach funkcjonowania różnych branż, czasem też zmieniamy firmy w międzyczasie. Na końcu jesteśmy już tymi doświadczonymi inżynierami jakości, tak jak Paweł i możemy patrzeć z innej perspektywy naszych doświadczeń. Chciałbym Was przeprowadzić przez taką podróż, więc zaczynamy. Początek pracy w jakości. Paweł, co dla Ciebie oznacza wszechstronność inżyniera jakości?
P.W.: Tutaj myślę, że warto powiedzieć w jakich funkcjach pracowałem, ponieważ swoją karierę zaczynałem jako kontroler jakości. Wspierałem głównie zadania związane z kontrolą. Najpierw to były dostawy, później trafiłem na produkcję, gdzie byłem odpowiedzialny w późniejszym okresie za programowanie maszyn CMM jako jakąś ścieżkę rozwoju, później zostałem awansowany na inżyniera jakości dostaw i tutaj miałem troszeczkę inne zadania, niż później w działach operacyjnych, ponieważ zajmowałem się bezpośrednio dostawcami i tutaj tak jakby moim klientem byli koledzy z działów montażu, z działów obróbki maszynowej. Ja musiałem im zapewnić jakość tego komponentu, który dostawaliśmy od dostawców. Z drugiej strony ja byłem przedstawicielem firmy, czyli klienta i pracowałem z dostawcą, żeby on poprawiał swoje procesy i przeprowadzał analizy jak najbardziej skutecznie. Tak samo wspierałem go poprzez wymianę doświadczeń, klarowanie wymagań i dopinanie różnych rzeczy. Tam również był wyżej inżynier, który już bezpośrednio zajmował się rozwojem dostawcy. Kolejnym ciekawym doświadczeniem była praca w kolejnej firmie. Byłem już typowo inżynierem operacyjnym i integrowałem dwie funkcje; troszeczkę technologa montażu i dużo tej strony jakościowej. Byłem też odpowiedzialny za przeniesienie całego procesu z zagranicy do Polski, więc trzeba było pracować nad dokumentacją. To także był okres gdzie działaliśmy prewencyjnie. Przy przenosinach tego procesu od razu próbowaliśmy zmapować te procesy przy tworzeniu dokumentacji i zobaczyć co w tych procesach można ulepszyć, czego efektem finalnym było podejście do zrobienie FMEA. Kolejną firmą do której trafiłem była firma lotnicza. Tutaj miałem funkcję operacyjną – wspieranie bezpośrednio procesów produkcyjnych, ale również bezpośredni kontakt z konstruktorami. Jeżeli coś nie wyszło na produkcji, ja byłem odpowiedzialny za cały proces zatwierdzania tych komponentów niezgodnych i przedstawiania działań zaradczych, żeby tego typu problemy nie zdarzały się w przyszłości. Teraz jestem inżynierem w QSense, tutaj dostarczamy usługi i moją rolą jest zapewnienie, że te nasze procesy będą działały jak najlepiej i prewencja będzie poukładana na takim poziomie (szkolenia operatorów, audytowanie), że po prostu będziemy zapobiegać powstawaniu błędów i dostarczać te usługi na najwyższym poziomie. Czyli, rozmawiam bezpośrednio z klientem, przekładam jego oczekiwania na jakiś plan, staram się również robić takie projekty wizualne, jak mogłoby wyglądać raportowanie, czego oni dokładnie oczekują. Jesteśmy dostawcą usługi, ale także dużej ilości danych. Dzięki konkretnym danym, opieraniu się na faktach, nasi klienci mogą również rozwijać swoje procesy i to jest bardzo ważne. Dosyć dużo przechodziłem, więc mam doświadczenie z zakresu produkcji, gdzie przede wszystkim mamy obróbkę maszynową, obróbkę metali i ta multizadaniowość inżyniera polega na znalezieniu się w bardzo szerokim zakresie działów. Cechą wspólną tego wszystkiego jest to, że należy być osobą, która jest bardzo dobrym pomostem w budowaniu kultury jakości i skupia się na działaniach prewencyjnych, a w razie problemu dociera do rzeczywistych przyczyn.
K.P.: Paweł przytoczył już kilka swoich stanowisk. W obszarze jakości jest ich sporo. Paweł, które z tych stanowisk było Twoim ulubionym albo dobrze się na nim czułeś? Może brakuje Ci czegoś wyjątkowego, w którejś z tych ról, którą miałeś, reprezentowałeś?
P.W.: Każda rola była unikatowa. Mogę powiedzieć, że najwięcej wyzwań i ciekawej pracy, gdzie każdy dzień może być czymś nowym, nowym odkryciem, może być bardzo wymagający, to są wszystkie greenfieldy i wdrażanie rzeczy nowych. Wtedy odkrywamy wymagania, patrzymy z czym mamy do czynienia i to są rzeczy takie mocno rozwijające kreatywność. Też to zależy oczywiście od managementu, czy oni wspierają takie działania – zazwyczaj tak. Tutaj mamy wolną rękę we wdrażaniu takich projektów. To jest też dobre, że realizacja każdego projektu, nowej usługi wraz z zespołem to jest bardzo cenne doświadczenie. Po latach, ucząc się na poprzednich błędach wyciągamy wnioski i idziemy do przodu. Także dla mnie wdrażanie rzeczy nowych było mocnym kopem energii, nauką na własnych błędach i bardzo ciekawym doświadczeniem. Dla mnie wiązało się to również ze współpracą z kolegami z zagranicy, także było to spędzanie czasu w multikulturowym towarzystwie i bardzo cenna wymiana doświadczeń. Myślę że taka rola inżyniera jakości projektowego, wdrożeniowego, to właśnie było najciekawsze co mnie na tej drodze spotkało. Ważną rzeczą przy takich greenfieldach jest to, że trzeba się liczyć, że te projekty są bardzo dynamiczne i mogą bardzo nas angażować. O tym się myśli, przeżywa i trzeba brać pod uwagę, że będą nadgodziny. Tak przynajmniej było w tym przypadku. Jak greenfield, to można to sobie raczej w ten sposób poukładać, że jest dużo rzeczy do zrobienia, zazwyczaj pracodawca chce, żeby proces działał i żeby już mógł produkować, także to są bardzo angażujące rzeczy.
K.P.: Wiele stanowisk, wiele obszarów, różne branże, jako inżynierowie możecie w różne miejsca trafić. Oczekiwania mogą być różne. Paweł tu wspomniał o cesze wspólnej, o byciu łącznikiem wszystkich działów. Czy widzisz jeszcze jakieś miejsce wspólne tych wszystkich stanowisk?
P.W.: Myślę, że jest to na każdym z tych stanowisk orientacja na klienta, bo pod terminem “klient” możemy rozumieć bardzo różne rzeczy. Może to być klient końcowy, zewnętrzny, może to być inna fabryka, a może to być inny dział w danej organizacji. Zawsze więc orientacja jest taka, żeby dzięki naszej pracy jakość produktów była zapewniona i produkty niezgodne, żeby nie trafiały do dalszych procesów albo do finalnego klienta. Jeżeli masz problem, to lepiej zatrzymaj się, jeżeli nie potrafisz tego rozwiązać, wezwij kogoś, kto to potrafi, kto może Ci pomóc. To też jest taka rola supportująca jakości, żeby właśnie te procesy i te osoby wspierać. Żeby one były świadome co robić i w jaki sposób reagować. Także to jest cecha wspólna wszystkich funkcji jakościowych.
K.P.: Przejdźmy do drugiej części. Kiedy już znajdziemy się w firmie i w niej działamy i tu mamy te nasze wyzwania. Dodatkowo chciałbym wspomnieć o relacji między jakością, a produkcją. Pytałem wielu z Was na LinkedInie o to jak się ma ten obszar jakości w firmach. Często pojawiało się wyzwanie dotyczące pogodzenia produkcji i jakości. Teraz Paweł do Ciebie pytanie: Jak Ty budujesz tę relację pomiędzy produkcją, a jakością? Jak działasz w tym kierunku żeby wspólnie współpracować na linii produkcyjnej i ponosić wspólną odpowiedzialność?
P.W.: Na Twoim slajdzie pierwsza linijka: “ilość, czy jakość”. Dla mnie jest to bezkompromisowe akurat. Ja widzę to łącznikowo, czyli odpowiednia ilość sztuk, odpowiedniej jakości. To jest nie “czy”, tylko “i”, czyli ilość i jakość, wszystko się musi sklejać. Także wracając nawet do poprzedniego tematu, jakość jest bezkompromisowa. Klient oczekuje, że dostanie daną ilość sztuk i odpowiedniej jakości. To są ze sobą elementy połączone, czyli delivery on time, quality on time. To jest ciągły proces, bo możemy napotkać wiele problemów i tutaj właśnie ważne jest to podejście procesowe. Jeżeli przy wdrażaniu produkcji zmapujemy sobie odpowiednio procesy i będziemy wiedzieć jakie są do nich wejścia, wyjścia, jakie zasoby są do tego potrzebne i przy okazji jeszcze zaangażujemy leanowca, technologa i zrobimy dobre FMEA, to najprawdopodobniej ten romans jakości z produkcją będzie wyglądał dużo lepiej i będzie mniej burzliwy. Także tutaj super sprawą jest dobre wejście. Jeżeli już w fazie projektowania danego procesu przyłożymy się do tych rzeczy prewencyjnych, to będzie łatwiej. Gorzej jest jeżeli jako inżynier zmieniacie pracę i trafiacie w środek nieustabilizowanej produkcji, gdzie ktoś tej prewencji nie zrobił. Było parcie na czas, nie było stawiane na podejście procesowe, ale są dobre chęci. Wtedy trzeba, z mojego doświadczenia, jak najszybciej ugasić te największe pożary. Szacowanie tych pożarów, to po prostu z analizy Pareto; które 20% generuje kolejnych 80% najgorszych problemów i docieranie do przyczyn źródłowych. Najważniejsze dla mnie jest to, że jeżeli już mierzymy się z jakimś problemem, to żeby trafić w jego sedno, przyczynę. Powiedzmy, że przecinasz się, kaleczysz gdzieś regularnie, to nie jest kwestia naklejania plastra, tylko wyeliminowania tego co Cię kaleczy. Powiedzmy to tak obrazowo. Tutaj jeżeli znajdziemy się już w takiej sytuacji, że trzeba najpierw porozwiązywać parę problemów, to warto je zgasić u źródła, znaleźć prawdziwą przyczynę, a po rozwiązaniu tych problemów iść w prewencję, żeby kolejne się nie pojawiły. Tu znowu przydaje się podejście procesowe. Jeżeli zrobimy coś dobrego w jednym procesie i najważniejsze, zweryfikujemy, że to działa, to jeżeli mamy zmapowane procesy i widzimy podobieństwa między nimi, to łatwo te działania przerzucić i zapobiec, żeby na dziale obok coś podobnego się nie wydarzyło. To są takie działania prewencyjne, które na pewno pomagają nam dobrze żyć z produkcją, jeśli pracownicy widzą, że jest zaangażowanie tego szczebla inżynierskiego i liderskiego, to moim zdaniem to jest kluczowe, ponieważ lider jest bardzo blisko produkcji, również na 3 zmianach w fabrykach. To jest niezwykle istotne, żeby rozwijać ten szczebel. To są ludzie, którzy będą nam dostarczać informacje, z którymi będziemy bezpośrednio pracować tam przy linii. I doceniać operatorów. Rozmawiać z nimi, ponieważ oni są przy tej maszynie i zazwyczaj bardzo dobrze wiedzą co tam się stało. Jeżeli mamy sytuację w miarę opanowaną, to nie ma co czekać na to co może się wydarzyć w przyszłości, tylko działać prewencyjnie. Myślę, że to angażuje ludzi, pokazuje dobry kierunek, a przy okazji, finalnie, jeśli macie jeszcze inne rzeczy w życiu poza pracą, jakieś pasje, jesteście dobrymi rodzicami, chcecie spędzać czas z rodziną, to podejście prewencyjne powoduje, że jest mniej pożarów do ugaszenia i zazwyczaj nie trzeba zostawać w tej pracy po godzinach.
K.P.: Jeszcze z takich wskazówek jak godzić jakość, a produkcję, to tutaj mamy taki screen z wczoraj. “Prawdziwy inżynier zawsze w Gemba”. To jest takie super podejście jak faktycznie współpracować z tą produkcją.
P.W.: Generalnie z mojego doświadczenia. Gdzieś tam widziałem, że była informacja o problemie i zespoły spotykają się przy tablicy w biurze i zaczynają rozmawiać o tym problemie, gdzie on jest zupełnie 50 metrów dalej. Dla mnie podstawą zaangażowania produkcji i wzbudzeniem odpowiedzialności jest gemba walk. Jeśli weźmiemy zespół, pójdziemy na miejsce gdzie ta rzecz się wydarzyła, tam gdzie jest to prawdziwe życie produkcyjne, to można zebrać bardzo dużo informacji i przy okazji pokazać pokazać ludziom, że problemy rozwiązuje się tam gdzie one występują, a nie wymyśla się poza ich plecami. To jest moim zdaniem mega istotne w tym wszystkim. Warto też pokazać operatorom, kontrolerom, że produkując coś, kontrolując, biorą odpowiedzialność za pewien proces, za część procesu. Stworzenie takiej atmosfery buduje dobre relacje i zaangażowanie załogi. To zauważałem przez bardzo wiele lat. Teraz tematem do ogarnięcia jest połączenie pewnej fachowości z pracą standaryzowaną. Z mojego doświadczenia, kiedy pracowałem na produkcji, gdzie te narzędzia nowoczesne były wprowadzane, ale była garstka operatorów z bardzo dużym doświadczeniem, to zazwyczaj można było zauważyć, że oni biorą dosyć dużą odpowiedzialność za to swoje działanie i starają się to zrobić jak najlepiej. Tę fachowość trzeba docenić i przelać na pewien standard. To jest bardzo dobra praktyka. Też należy w taki sposób szkolić ludzi i pokazywać im co jest ważne i dlaczego ta ich praca jest ważna, żeby ich angażować. Myślę, że jest to rola idealna właśnie dla inżyniera jakości w jakiejkolwiek produkcji by nie pracował.
K.P.: Taki inżynier jakości staje się też po części liderem. O tej miękkiej stronie zaraz porozmawiamy, a teraz jeszcze ten drugi aspekt, który bywa źródłem różnego typu zgrzytów, czyli jakość, a klient. Jak Ty widzisz budowanie tej relacji z klientem i jak zrobić tak, żeby spełniać te jego oczekiwania i pytanie czy też wszystkie oczekiwania mamy spełniać i jak to pogodzić?
P.W.: Moje spostrzeżenia i podsumowanie. Ja mam takie określenie jak miara dojrzałości. Miara dojrzałości tej relacji z klientem i miara dojrzałości organizacji. Jeżeli, jak to mówimy, klient przyjeżdża na audyt, a my malujemy trawę na zielono, to znaczy, że organizacja nie jest jeszcze na tyle dojrzała, żeby spokojnie do tego podejść. Dojrzała organizacja, która działa prewencyjnie, ma wszystkie procesy poukładane, raczej na audyt klienta nie będzie reagować nerwowo. Będzie to kolejne wyzwanie i okazja do lepszego zrozumienia wymagań klienta, bo można z nim mieć kontakt bezpośrednio i jest to okazja do ciągłego doskonalenia. Myślę, że jest to dojrzałe podejście do relacji z klientem. Patrząc też na połączenie klient – organizacja, czyli dostawca usług, produktów, to ta relacja też powinna być budowana w atmosferze partnerskiej. Dostawca – klient, to są jacyś partnerzy i generalnie atmosfera budowania relacji powinna być oparta na szacunku i partnerstwie. Wydaje mi się, że jakiekolwiek podejście powinno być dojrzałe i również asertywne. Zaraz wyjaśnię czym jest dla mnie asertywność. Generalnie jak mówię “asertywność”, to wszystkim się kojarzy z mówieniem “nie”. Jednak sposób komunikacji asertywnej polega na tym, że wyrażamy nasz stan emocjonalny ze względu na działanie drugiej osoby i kończymy to naszym oczekiwaniem, więc jak najbardziej może to być dialog pozytywny. Jeżeli prowadzi się taką komunikację, otwartą, konkretną, popartą dowodami i danymi, to jest zupełnie inna rozmowa z klientem. Jeżeli on zobaczy jakąś ściemę, to ta relacja nie będzie mogła być dobra i trzeba będzie nad tym pracować. Jeżeli natomiast pojawi się reklamacja, to trzeba ją rozpatrzyć, czasami się zdarza i nie zawsze jest powiedziane, że ponieważ to jest klient, to to będzie nasza wina. Zdarza się też, że klient na swoich liniach popełni jakiś błąd. Przykład: jeżeli wyślemy element z otworami gwintowanymi, a jemu zdarzy się krzywo wkręcić śrubę i zerwać ten gwint, no to może być jego wina. Nie musi być tak, że my mu dostarczyliśmy element z nieprawidłowym gwintem. Teraz, jeżeli są zebrane odpowiednie dowody na to, że my zrobiliśmy dobrze, bo mamy rejestr, kontrolę funkcjonalną tego gwintu i mamy z tego zapisy i dowody, co też jest ważnym elementem systemu jakości, to prowadzimy dialog z klientem i mówimy, że u nas wszystko było ok, mamy dowody, jak możemy mu pomóc, dostarczyć te dane i może poprawi swój proces. Jeżeli ta relacja jest dojrzała, to klient sprawdzi i wtedy mamy win-win. Także to jest droga do wypracowania dialogu i rozwiązania. Czasami może być tak, że rzeczywiście u nas pojawił się błąd. Wtedy trzeba zapewnić tego klienta, że pracujemy nad tym, jego zadowolenie jest dla nas ważne i właśnie robimy doskonalenie tego procesu, żeby zapobiegać powstawaniu takich błędów. Jeszcze lepiej, jeśli po akcjach korekcyjnych sprawdzimy nasze procesy i wprowadzimy działania prewencyjne na druga linię i to juz bardzo dobrze wygląda. Myślę, że to zostanie docenione na pewno.
K.P.: Wydaje mi się, że takim fajnym aspektem jest to, co powiedziałeś na końcu. Ważne jest to co my zrobimy z tymi problemami, jak rozwiązujemy problemy i jak wdrażamy go do organizacji. Uczymy się, nasza wiedza rośnie, przekładamy to na inne produkty, inne miejsca, inne detale. Wtedy widać czy organizacja poważnie podchodzi do tych działań. Klient wtedy też nabiera pewności to jest organizacja, która ma możliwości i warto z nimi działać.
P.W.: Wiesz co, widzę tutaj taki fajny komentarz, że “trudne są do rozpatrzenia reklamacje logistyczne”. Mam bardzo ciekawy przypadek z życia i niekoniecznie trzeba się doszukiwać u siebie i u klienta, ponieważ niektóre przyczyny mogą być dosyć fantastyczne bym powiedział. Dostaliśmy kiedyś reklamacje na zniszczone opakowanie w jednej z firm. Do tej pory to nie występowało, zdarzyło się to pierwszy raz. Pakowanie standardowe w firmie, było tak od lat, klient miał dostarczany produkt w ten sam sposób i nagle coś takiego. Robiliśmy różne testy i według tych wymagań wszystko było spełnione. Okazało się, że przewoźnik, w jednym z centrów logistycznych zmienił prędkość taśmociągu o ileś tam kilometrów na godzinę. Po prostu przyspieszył i się okazało, że siła działająca na ten towar była na tyle duża, że on się uszkodził w centrum logistycznym. Także w stosunku do wymagań ani nie było winy dostawcy, ani nie było winy klienta, że te wymagania przedstawił złe, tylko akurat były dopasowane do tamtych warunków, a warunki zmieniły się niezależnie i nikt o tym nie wiedział. Także czasami warto poszperać i zobaczyć co się mogło zmienić gdzieś u przewoźnika, bo naprawdę można dojść do ciekawych rzeczy. To taka moja z życia historia.
K.P.: Ja też się mogę podzielić historią. Kiedyś w firmie robiliśmy przestawianie układu maszyn i każdy zapominał o takim prostym miejscu jak składowanie pojemników i one spędziły jeden dzień na zewnątrz. Akurat nikt nie zwrócił uwagi, że pogoda na zewnątrz nie była odpowiednia, zapakowaliśmy detal, niby wszystko było w porządku. Jak dojechał na miejsce, akurat na nieszczęście płynął do Brazylii, to cały pojemnik zdążył zardzewieć. Okazało się, że nie był gdzieś tam do końca wyczyszczony, nie był w odpowiednim miejscu składowania. Szukaliśmy tych przyczyn bardzo długo i dopiero dochodząc do tego grupą znaleźliśmy tę przyczynę zupełnie w czymś innym. Takiego czegoś nigdy nie było, pierwszy raz się zdarzyło, ale szukaliśmy.
Paweł, jeszcze takie pytanie wyjaśniające. Jak Wam się udało dotrzeć do tej informacji o zmianie prędkości na ciągu, prędkości tej linii w centrum logistycznym?
P.W.: Zaczęliśmy drążyć temat. Współpracowaliśmy z klientem i on sprawdził swoje wymagania poprzez eksperyment sprawdziliśmy wytrzymałość naszych opakowań, ile są w stanie utrzymać ten produkt w swoim miejscu w danym stanie. Tu nam wyszło, że wszystko było po staremu, więc coś musiało się na tej drodze zmienić. Drążąc troszeczkę tego dostawcę, czy jakaś droga logistyczna, czy środek transportu się zmienił, wyszło w toku dyskusji, że być może to jest kwestia tego, że oni rzeczywiście jeden taki taśmociąg mają długi i tam prędkość jest dosyć duża, a jeszcze paczka z tą zawartością czasami dynamicznie zmienia kierunek. Doszliśmy do tego również przez rozmowę z przewoźnikiem.
K.P.: Mówiłeś o asertywności, tutaj jest taki jeden komentarz. “Co robić w przypadku kiedy klient jest mistrzem asertywności i mówi: nie, nie zgadzam się.”
P.W.: To nie jest asertywność. To nie jest odpowiedź asertywna. Powiedzenie samego nie, to jest odmowa i nic poza tym. Zawsze wypowiedź asertywna wiąże się z pewnym działaniem. Musimy być dyplomatami i próbować się z tym klientem porozumieć. Albo mamy przedstawiciela u klienta albo rzeczywiście próbujemy te nasze dowody przedstawić i “nie, bo nie”, to nie jest dla mnie żadna odpowiedź akurat. Także asertywność nie polega właśnie na powiedzeniu samego “nie”. Asertywność to jest określenie pewnego stanu emocjonalnego ze względu na działanie drugiej strony i oczekiwaniu tego co ma nastąpić. To jest pełna asertywność i może być jak najbardziej pozytywna. Mogę dać Wam przykład asertywnego angażowania załogi. Np. operatorzy wezmą sprawy w swoje ręce i wykażą się kreatywnością np. zgłoszą wniosek racjonalizatorski na poprawę procesu, co może im ułatwić, przyspieszyć pracę. Oprócz całej oceny tego procesu, takim pierwszym elementem, który jakby rozwija proste powiedzenie “good job” jest “czuję się świetnie po tym jak rozmawialiśmy i wdrożyliście takie rozwiązania i oczekuję tego, że taki projekt pójdzie do przodu i będziecie to robić dalej”. To jest właśnie wypowiedź asertywna. To jest mój stan emocjonalny, poprzez działanie drugiej osoby i oczekiwanie tego co ma się zadziać.
K.P.: Zdecydowanie tak. To jest ta sztuka budowania relacji i rozwiązywania tych wspólnych problemów, gdzie tak musimy tego klienta zaangażować w te działania, bo działamy do jednej bramki. Przechodząc dalej do tego doświadczonego inżyniera jakości. Mamy wiele instrumentów zarządzania jakością: zasady, metody, narzędzia. Już lekko powiedzieliśmy o Twoim ulubionym narzędziu i działaniu na linii, na gembie. W takim razie, jakbyś trochę mógł powiedzieć, przybliżyć trochę dla inżynierów, z jakich metod, narzędzi korzystałeś w swoim doświadczeniu albo na stanowiskach albo obecnie z czego korzystasz, co jest dla Ciebie najbardziej przydatne w tym momencie?
P.W.: Generalnie metodę rozwiązywania problemu dobieram do danego problemu. Zazwyczaj jest jakaś sugestia nawet w ogłoszeniach pracy 5 Why, Ishikawa. To są jakieś podstawy, których się używa, natomiast według mnie nie zawsze. Moim zdaniem taki schemat postępowania mój ulubiony, a metoda dotarcia do przyczyny źródłowej i późniejsze jej potwierdzenie, to są już zupełnie dwa różne tematy. Generalnie powiedzmy, że 8D jako taka najbardziej złożona struktura do wypełnienia tych wszystkich kroków. Skrót 8D PDCA. W skrócie, ten cykl PDCA w takich drobniejszych doskonaleniach i zarezerwowanych do takich mniejszych rzeczy na produkcji, tudzież w usługach. Natomiast sama metodologia: po pierwsze trzeba zebrać jak najwięcej danych i do tego służy dla mnie gemba, czyli co się zdarzyło, gdzie, kiedy, kto tam był, kto widział, jaki to ma wpływ na dalszą produkcję, kto jest odbiorcą itd. Zebrać jak najwięcej informacji, bo z tych informacji można wyjść dalej. Jeżeli ten krok zostanie zrobiony niewłaściwie, to później bywa tak, że ta analiza wcale nie trafia w punkt i to bywa problematyczne. Jeżeli jest jakaś duża sprawa, to robimy te kroki 8D. Mniejsza – można 4 stepa zrobić i takie PDCA w 4 krokach. Generalnie bardzo ważna rzecz, zebrać jak najwięcej danych, do tego służy mi gemba, czyli idę na miejsce, sprawdzam co się wydarzyło, jaki detal, jak tam wygląda otoczenie tego wszystkiego, rozmawiam z ludźmi. Druga rzecz, jak już te dane są, to trzeba zabezpieczyć klienta, może nawet lepiej wcześniej to zrobić, ale lepiej zebrać dane moim zdaniem niż od razu działać trochę “na pałę” bym powiedział. Jeżeli chodzi o zabezpieczenie klienta, czyli te akcje natychmiastowe: czy trzeba sortować, czy wprowadzić dodatkową kontrolę, jako działanie zapobiegawcze nie korekcyjne i to robimy. Zapewniamy, że klient już dostanie dobre, a my sobie odfiltrujemy to co jest złe. Kolejny krok, to jest przeprowadzenie analizy. Ja się wcale tu nie upieram przy Ishikawie, która jest tak jakby docelowa, bo w sumie jest metodą która angażuje zespół, ale z mojego doświadczenia nie zawsze musi być opcją pierwszego wyboru. Warto troszeczkę inaczej spojrzeć na problem. Niektórzy odpalają Ishikawę np. nie oglądając serii detali, nie analizując tych danych. Jeżeli macie jakieś metody statystyczne w procesie, warto je przejrzeć, zobaczyć co tam się zadziało, czy ten proces gdzieś do granicy kontrolnej nie podszedł w którymś miejscu. Warto te dane przeanalizować przed analizą, a niekiedy już podczas gemby praktycznie widać co się stało i nie trzeba robić Ishikawy, bo z detalu można wyczytać, co tam mniej więcej się zadziało. Także ważne jest, żeby iść na to miejsce zdarzenia, popatrzeć, porozmawiać z ludźmi i wtedy dobrać metodę. Niekiedy można mieć serię 10 detali, z czego 9 jest dobrych, 1 wychodzi niedobry i już na podstawie analizy tej serii, patrząc na te detale można dojść co było czynnikiem, który wpłynął na to, że część detali jest zrobiona bardzo dobrze, a część jest poza specyfikacją. Jeżeli mamy hipotezę jaki czynnik mógł wpłynąć na to, to można przeanalizować raporty pomiarowe, statystykę przy procesie, domierzyć te detale i wtedy można spróbować postawić hipotezę jaki czynnik wpłynął na tę zmienność. To jest czyste działanie na fizycznych komponentach. Ishikawa to jest, według mnie, bardziej metoda gdzie trzeba przeprowadzić tę burzę mózgów, bo przyczyna, postawienie hipotezy nie jest takie oczywiste. Trzeba zaangażować zespół, bo może ktoś akurat wpadnie na dobry pomysł, jakiś ekspert podpowie co mogło się wydarzyć. Ishikawę zostawiam do takich analiz gdzie czytanie z detalu co mogło się wydarzyć nie jest zupełnie oczywiste. Bardzo istotny krok jest dalej. Mamy hipotezę i najważniejsze dla mnie jest żeby nie uznać tego za absolutną prawdę, tylko tę hipotezę trzeba potwierdzić. Kolejna metoda, krok w działaniu, to jest zaprojektowanie odpowiedniego eksperymentu, tudzież znalezienie przyczyny nie tylko bezpośredniej, ale systemowej i braku detekcji. Czyli np. w 5 Why, ale nie zwykłe, tylko 3L, czyli 3 legged, gdzie mamy przyczynę źródłową, ale szukamy jeszcze przyczyny systemowej, braku detekcji tego błędu. Tu rozwijamy te tematy w taki, a nie inny sposób. Najlepiej zaplanować sobie jakiś eksperyment, który włączy i wyłączy konkretne czynniki i potwierdzi, że ta hipoteza jest prawdziwa. Dopiero wtedy, po potwierdzeniu takiej hipotezy, można przejść do akcji korygujących proces, a tak jak wspomniałem wcześniej, jeśli to zakończy się sukcesem, to popatrzeć na mapę procesów, czy jest coś podobnego i od razu prewencyjnie wprowadzić te działania jeżeli się da. Także może nie mam ulubionej, konkretnej metody, tylko dobieram do danej sprawy metodę, jakieś techniki i tym podobne rzeczy. Ania zapytała: “A co z symulacją wady?” To jest właśnie trochę ten design of experiment, czyli próbuję odtworzyć błąd – to jest jeden design of experiment, czyli włączam jakiś czynnik i go wyłączam albo potwierdzam, że ta moja hipoteza jest prawdziwa, włączając i wyłączając czynnik.
K.P.: Jeżeli dobrze zrozumiałem, to faktycznie te nasze problemy mogą być duże, małe, a czasem faktycznie szkoda tracić czasu, tak leanowo, na szerokie analizy, jak można odczytać na produkcji, bezpośrednio na linii, na detalu zobaczyć i znaleźć tak naprawdę przyczyny bardzo szybko i móc wprowadzić już działania. Przy tych dłuższych, większych tematach, tak, zdecydowanie analiza, praca, zespół, eksperymenty, działania, hipotezy, potwierdzenie. Myślę, że to naprawdę kawał dobrej instrukcji do działań. Dużo teraz mówiliśmy o takich trochę twardszych rzeczach, ale ta strefa miękka. Gdzieś już troszeczkę o niej wspominaliśmy, ale nie tak dużo. Wiem, że dla Ciebie to jest też ważny element pracy inżyniera, mówiłeś troszeczkę tu o angażowaniu. Jak Ty widzisz tę strefę miękką, rozwój tych umiejętności miękkich? Mówiłeś też o feedbacku do pracowników, nawet tym asertywnym, który jest pozytywny generalnie. Też rozwój pracowników pod względem umiejętności, wiedzy, czyli prowadzenie szkoleń, warsztatów, tak żeby wzbudzać ich kreatywność. Jak Ty podchodzisz, jak starasz się angażować ludzi?
P.W.: Z tego co zauważam i potwierdza się to z teorią trenerów zarządzania, działających dosyć intensywnie w Polsce, tutaj mogę przytoczyć Adama Dębowskiego. Jest taka teoria odnośnie przekazywania wiedzy, więc level 1 to jest to, co człowiek wynosi z domu. Te wszystkie zachowania, które widzi u rodziców, uwarunkowania kulturowe, to kształtuje jego trzon osobowości. Później ludzie idą zazwyczaj do szkoły, tam się mówi, że 2+2=4, to jest jakaś tam prawda absolutna, czyli to co jest w podręczniku, to co jest naukowe, potwierdzone. Trzecie podejście jest na bazie własnego doświadczenia i bardzo dużo mądrych rzeczy wyszło właśnie z doświadczeń ludzi. Z tego jak oni pewne rzeczy robili, przeżywali, jakie lekcje z tego wyciągnęli. To podejście trzeciego stopnia jest też podejściem angażującym ludzi. Zauważam, że jeśli zaczniemy mówić “w tej książce jest taka metoda, tak, tak i tak opisana i tak trzeba robić”, to oni podejdą do tego: “znowu tu się jakiś mądrala napatoczył”. Jeżeli natomiast powiecie: “Słuchajcie, ja w swoim życiu już coś takiego przerobiłem. Na początku miałem problem jak ugryźć taki temat, ale wspólnie z zespołem zrobiliśmy takie i takie działania. Pierwsze nam się nie udało.” Czasami warto przyznać się, że coś nie wyszło, bo to jest normalne. Kto nic nie robi, nie popełnia błędów, a kto coś robi, to może się zdarzyć jakiś wypadek przy pracy. Jeżeli chodzi o to podejście trzeciego stopnia, to jeżeli opowiecie pewną historię, która finalnie zakończyła się sukcesem, mimo że mogła to być trudna droga, to takie działania dostarczają największej wartości dodanej na końcu. Jeżeli opowiecie pewien przypadek z własnego doświadczenia, z własnego życia zawodowego, tudzież prywatnego, wtedy ta historia jest dla ludzi bardziej inspirująca, bardziej namacalna. To się wydarzyło, ten zespół coś zrobił i wtedy łatwiej się przytacza metody, z których się korzystało. To zadziałało, tamto nie zadziałało, to nam wyszło super, a to nie. Ten sposób postępowania naprawdę angażuje ludzi. Po drugie, już o tym Krzysztof rozmawialiśmy, widzę tutaj coś takiego jak bezradność wyuczona w społeczeństwie, ogólnie. Widzę to także na produkcji i jest to troszeczkę efekt tego podejścia 2.0. – “Ja Ci dam instrukcję, powiem jak to robić i jest to jakby jednokierunkowe, a kiedy się pojawi problem, to ludzie mówią: “Tu było napisane jak mam zrobić”. Ci ludzie nie angażują się w te problemy, nie biorą odpowiedzialności za swoją pracę. Jeżeli natomiast zadasz pytanie: “Jak Ty byś to zrobił? Ja widzisz rozwiązanie?” to wtedy ten człowiek zaczyna dość kreatywnie myśleć, bo ktoś w końcu okazuje mu zainteresowanie, nie daje mu gotowego rozwiązania, tylko próbuje go naprowadzić na rozwiązanie, używając swojej wiedzy, doświadczenia. To jest jedna z metod angażowania ludzi do pomocy przy tym ciągłym doskonaleniu, rozwoju produkcji, ponieważ Ci ludzie tam zazwyczaj pracują i oni bardzo dobrze wiedzą co mają, czego im brakuje. Ważne jest, żeby wzbudzić tę ich kreatywność, najlepiej zadając pytanie: “Co byś zmienił? Jak Ty to widzisz? Jak widzisz rozwiązanie?” Wtedy troszeczkę tę bezradność i brak ponoszenia odpowiedzialności za tę pracę wydmuchujemy z ich głowy i angażujemy do działania. To są takie moje obserwacje jeśli chodzi o angażowanie ludzi. Warto też, nie tylko robić warsztaty w gronie inżynierskim, liderskim, tylko wziąć człowieka, który tam pracuje realnie i poprosić go o pomoc: “Słuchaj, jest taka i taka sytuacja, chcemy poprawić ten proces, cel jest taki”. Ludzie muszą być też świadomi celu, bo jeżeli podchodzi zespół i zadaje dziwne pytania, a ten człowiek zupełnie nie wie po co to jest, to raczej będzie totalnie zdezorientowany. Warto powiedzieć jaki jest cel, co chcemy osiągnąć, dlaczego ten człowiek jest nam potrzebny i czego od niego oczekujemy. Wtedy zazwyczaj na ludzi można liczyć, oni się angażują, czują za coś odpowiedzialność. Myślę, że to jest ta dobra droga.
K.P.: Znowu kolejna dawka dobrych wskazówek: komunikacja, praca, zapraszanie do współpracy, to niby proste, a ważne żeby to robić. Tutaj taka krótka dyskusja, że to kosztuje, takie podejście. To jest pewnego rodzaju inwestycja, ale bardzo się zwraca sposób rozwijania pracowników, bo oni nam to wszystko oddają. To nie koniec jeszcze. ten webinar jest też skierowany do inżynierów jakości, osób które pracują w tym zawodzie, zaczną być może kiedyś pracę w tym zawodzie. To takie wskazówki Paweł od Ciebie. Jak być inżynierem jakości? Jakie są plusy i minusy? Czy zawsze warto iść w tę stronę, czy są momenty kiedy sobie trzeba odpuścić po prostu?
P.W.: Takie moje pierwsze spostrzeżenie, ponieważ jak by nie patrzeć, należy mieć z tyłu głowy zespół, a nie samotnego kowboja na Dzikim Zachodzie. Raczej w westerny się nie bawimy i nie kręcimy dzikich filmów, tylko nastawiamy się na zespół, czyli bardziej “Siedmiu wspaniałych”. Tutaj dla mnie bardzo istotną rzeczą jest to, że inżynier jakości, to jest taki rodzaj pracy kryzysowej, szczególnie jeśli jesteście w organizacji nieco nieuporządkowanej, no i niestety czasami można się poczuć jak w westernie. Wydaje mi się, że żeby opanować taką sytuację, trzeba być osobą wewnętrznie poukładaną, znać swoją wartość i mieć szacunek do siebie. To jest w tym bardzo ważne. Nie można do tej pracy iść z mega bagażem własnych problemów, bo dostaniecie zazwyczaj jeszcze większą dawkę. Trzeba to po prostu wziąć na klatę i podejść do tego z dużą dozą spokoju i poukładać to w jakiś dobry plan. Myślę, że to jest taki wewnętrzny czynnik, który trzeba przeanalizować przed wzięciem się za tę pracę, bo zanim będzie ten efekt stabilizacji, prewencji itd. mogą być takie wymiany zdań jak mówiliśmy wcześniej. Między produkcją, która ma swoje zdanie, niekoniecznie oni wiedzą, że są odpowiedzialni za jakość. Czasami tak bywa, że trzeba im to wytłumaczyć i jakby nauczyć, że każdy ponosi odpowiedzialność za to, żeby dostarczyć produkty w dobrej ilości, w odpowiedniej jakości. Także tu trzeba mieć trochę nerwów, trochę tej postawy asertywnej, ale tego da się nauczyć. Warto natomiast mieć dosyć dobrze zbudowane poczucie własnej wartości. Trafiając już w środowisko, które działa, w pierwszym momencie można poczuć, że jest dosyć duże ciśnienie i trzeba sobie z tym poradzić. Plusy są takie: jeżeli lubicie pracę z ludźmi i macie żyłkę do bycia troszkę takim dochodzeniowcem, czyli lubicie drążyć tematy, wykazywać się inicjatywą (Generalnie uważam, że praca inżyniera jakości jest bardziej odtwórcza, że jest jakiś proces i te rzeczy się już robi na czymś co jest. Natomiast jest wiele elementów na które można mieć wpływ i mogę one być kreatywne. Taki przykład: Teraz w QSense klient ma wymagania, chce odpowiedni raport i tutaj mega doceniam to, że jest otwarty dział techniczny, który wspiera nas w automatyzacji pewnych procesów. Kierunkiem obecnych czasów jest to, że tych danych przerabia się na tyle dużo, to zarządzanie wizualne jest na tyle ważne, że trzeba przerobić dosyć dużo danych. Takie rozwiązania automatyzujące tę pracę są bardzo ważne i polegają na jakimś dobrym pomyśle tego inżyniera. Wraz ze wzrostem kompetencji, znalezieniu się w świecie technologii na takiej typowej produkcji można spotkać się z błędami tego typu, że otwór został źle wywiercony, ponieważ detal się ruszył, bo go ktoś nie dokręcił w mocowaniu. Dlatego stosuje się automatykę, która sprawdza czy moment został na tej śrubie osiągnięty, następnie sygnał jest wysyłany do sterownika, który go analizuje czy jest ok, nie ok i dopiero zwalnia proces obróbki, kiedy te wszystkie działania zostaną odpowiednio zakończone. Jest to pewien rodzaj prewencji i kreatywności, bo proces zaplanowany, maszyna dostarczona bez tego typu rozwiązań. Tutaj taka uwaga, wy jako inżynierowie jakości nie musicie się znać na tym wszystkim i znać idei działania tych wszystkich automatycznych komponentów i spięcia ich w jakiś układ. Możecie mieć natomiast ideę prewencyjną: “Ok, zastanówmy się czy można wdrożyć takie rozwiązanie, że ten błąd zostanie w jakiś sposób wykryty?”. Żyjemy w świecie szybkiego dostępu do informacji, odpalamy google i szukamy rozwiązań. Właśnie dlatego ta praca może być kreatywna, w zależności jak traficie i jaki będziecie mieli na to pomysł. Być może ktoś da Wam taką, a nie inną robotę, ale niekiedy warto poszukać swojej drogi rozwoju, poprzez szukanie elementów do poprawy, rozwiązań które przyczynią się do sukcesu organizacji. Tak jak wspominaliśmy wcześniej, produkcja-jakość, wszyscy gramy do jednej bramki. Warto stać się takim kreatorem przyszłości.
K.P.: Zdecydowanie tak. Paweł, trochę zmierzamy do końca, więc jeśli masz ochotę podzielić się o KPI, o wskaźnikach w obszarach jakości i działaniu dla osób, które pracują na stanowisku inżyniera jakości, to śmiało możesz jeszcze mówić.
P.W.: No i tutaj kolejny taki temat, że inżynier jakości to jest łącznik między produkcją i tym co się na niej dzieje, a zarządem, który chce mieć ogląd jednym rzutem oka na ich biznes albo na biznes, którym zarządzają. Bardzo ważną rolą, w wielu organizacjach, inżyniera jakości jest dogadać z nimi takie wskaźniki, które opiszą ten proces i będą w jakiś sposób pokazywały jego postęp; czy idziemy w dobrym kierunku, czy w złym. Między innymi koszty braków są takim czynnikiem, czy jeżeli patrzymy na ilość reklamacji, szacujemy, że rocznie nie chcemy mieć więcej reklamacji niż tyle, czy poziom BPM. To są czynniki, przy których musimy zobaczyć jakich danych potrzebujemy albo jakie dane już mamy. Niekiedy zbieramy dane i łatwiej w pierwszym rzucie jest dopasować KPI do tych danych, które mamy, a nie odkrywać Amerykę na nowo i później z czasem wprowadzić inny parametr i go obserwować i powiedzieć, że od tego dnia robimy to i to, bo jest potrzebny akurat taki obraz. Ogólny ogląd na sytuację jest tutaj bardzo ważny i ta rola inżyniera jakości jest tutaj bardzo istotna, żeby pokazywać zespołowi na podstawie tych wskaźników, czy to co robimy idzie w dobrą stronę, czy musimy poszukać rozwiązań w innym obszarze.
K.P.: Jak mówisz o tym, to mi się przypomina taki jeden temat, gdzie kierownik jakości u naszego klienta wprowadził coś takiego jak brak jakości kosztów. Chciał pokazać po prostu, że praca wykonywana w obszarze jakości, to praca prewencyjna i tak naprawdę zarabia dla firmy. To, że ten dział jakości jest dostarczycielem wartości i to ogranicza niepotrzebne koszty, ryzyko. Chciał pokazać też swoją wartość po prostu w pieniądzach, bo to najlepiej obrazuje ile ta jakość kosztuje albo może kosztować.
P.W.: To się chyba nazywa język korzyści.
K.P.: Zdecydowanie.
P.W.: Często jest tak, że zespół ma fajny pomysł i często to widać w takiej produkcji nowoczesnej, ale kiedy trafiamy w sedno przyczyny jakiś tam problemów albo znajdujemy pole do rozwoju, poprawy i nagle okazuje się, że jesteśmy w stanie to zrobić, zapobiegnie to występowaniu różnych defektów, natomiast kosztuje to 30 000 euro. To jest taki czujnik, trzeba to sprzęgnąć z automatyką, no i taki jest koszt. Warto jest mieć te dane historyczne. Z powodu, że tego nie mieliśmy, wyprodukowaliśmy tyle i tyle braków albo reworki kosztowały nas tyle i tyle i jeżeli te 30 000 euro nawet wydamy, no to zapobiegniemy w długim okresie wyrzucaniu powiedzmy 60 000 euro na poprawę tej złej jakości. Myślę, że język korzyści jest bardzo ważny w pracy inżyniera, ponieważ jako lider zespołów, jeśli wypracujemy jakieś rozwiązanie, to będą musieli przekonać kierownictwo, żeby to wdrożyć i najprawdopodobniej zdobyć środki na realizację takiego celu.
K.P.: Jeszcze jedno takie pytanie. Czy ze strony takiej technicznej, umiejętności coś polecasz co warto wiedzieć albo nauczyć się na tym stanowisku albo rozwijać?
P.W.: Na pewno trzeba popatrzeć na specyfikę firmy, co jest potrzebne. W niektórych firmach inżynier jakości będzie blisko działów engineeringu, który zatwierdza różne detale. Ogólnie w pracy inżyniera jakości ważna jest biegłość, znajomość rysunku, bo jest to bardzo często, przynajmniej przy obróbce dosyć ważna umiejętność. Warto dobrać to pod kątem działalności. Na pewno warto jest mieć warsztat metod analizy problemu i docierania do przyczyn źródłowych i m.in. RADIXa można sobie spróbować zrobić, troszeczkę zgłębić metody statystyczne, bo karty kontrolne w procesie w tych szczególnie krytycznych parametrach bardzo się przydają, żeby je śledzić. Wtedy też możemy zapobiegać, jeżeli widzimy, że proces zbliża się do granicy kontrolnej albo jest przesunięty, to warto wtedy reagować. Jest to więc kwestia specyfiki. Ja mogę Wam powiedzieć, że w fazie wdrażania jakiś rozwiązań, gdzie normalnie trzeba by zlecić usługę wykonania jakiegoś elementu zapobiegającego (element bryłowy, mechaniczny), to niekiedy warto jest mieć umiejętności cadowskie, w sensie generowania modeli 3D, bo w coraz większej ilości firm dostępne są metody druku 3D i bardzo szybko możemy zweryfikować jakieś rozwiązanie, drukując model 3D, podstawiając go w proces i od razu mamy potwierdzenie czy to może działać czy nie, czy to w ogóle jest zupełnie nie trafione. Pracowałem również przy takiej produkcji, gdzie działania były bardzo projektowe, czyli klient zamawiał jeden element, który robiliśmy parę miesięcy łącznie, to były wielkogabarytowe elementy, potężne pompy. Tutaj trzeba było zupełnie inaczej pracować, bo ciężko tu postawić jakąkolwiek statystykę, ciężko o pracę standardową, bo element był customowy, na indywidualne zamówienie klienta. W takiej pracy, z jednostkową produkcją bardzo przydają się umiejętności z zarządzania projektem, czyli oszacowania kamieni milowych, kroków, wykres Gantta, co kiedy się powinno znaleźć w czasie. Tutaj już troszeczkę inna specyfika i więcej umiejętności miękkich, bo jeżeli mamy taki projekt pojedynczy, bardzo drogi zazwyczaj, z indywidualną instalacją, bo klient musi to wpiąć w konkretne miejsce i wszystko ma tam znaczenie, to musimy to bardzo dobrze rozpisać na nuty i uczulić ludzi, którzy będą to wykonywać, na to co jest ważne, co jest istotne. Tak więc są produkcje customowe, jednostkowe, gdzie bardziej przydaje się takie podejście projektowe inżyniera.
K.P.: Paweł my jesteśmy już na finiszu naszego spotkania. Jak Ci się podobało?
P.W.: Super. Mam nadzieję, że dałem Wam jakąś inspirację i pewną wartość, która poprawi Waszą pracę albo spowoduje, że pójdziecie tą drogą.
K.P.: Ja też myślę, że dużo wartościowych wskazówek, dużo inspiracji przede wszystkim dla Was do pracy. Nie ma co się poddawać, trzeba iść, działać, rozwijać się, rozwijać firmę, rozwijać obszary, w których się pracuje, także to na pewno warto wykorzystywać. Ja bardzo dziękuję całemu zespołowi QSense i pozdrawiamy przy okazji.
To co, Paweł? Kończymy, żegnamy się.
P.W.: Tak. dziękuję jeszcze raz i życzę miłego wieczoru. Do zobaczenia.
K.P.: Dziękuję za ten czas i pamiętajcie, pracujcie mądrzej, a nie więcej.
Wywiad z Pawłem Walczuk – inżynierem jakości w firmie QSense
Rozmowa przeprowadzona w ramach comiesięcznych rozmów LIVE Action Plan.
WSZECHSTRONNY INŻYNIER JAKOŚCI
Praktyczne zastosowanie narzędzi jakości
Znajomość etapów procesu APQP i PPAP
Prowadzenie oceny sprawności systemów pomiarowych
Dostrzeganie i eliminacja źródeł marnotrawstwa