Total Productive Maintenance
Totalne Utrzymanie Ruchu
TPM – Total Productive Maintenance – budowa efektywnego utrzymania ruchu na produkcji
Czym jest TPM? Jak policzyć OEE? Zobacz, jakie są podstawowe filary TPM i skorzystaj z instrukcji od czego zacząć. Poznaj korzyści wdrożenia metodologi Totalnego UR.
Czym jest TPM – Totalne Utrzymanie Ruchu
Wolna def. Towarzystwo Przyjaciół Maszyn
TPM – Metodologia prawidłowego utrzymania maszyn
- Budowa solidnego przedsiębiorstwa poprzez maksymalizowanie wykorzystania systemu produkcyjnego
- Tworzenie stabilnego systemu zapobiegania stratom w zakładzie i eliminującego występowanie wypadków, defektów oraz awarii
- Obejmowanie wszystkich departamentów, począwszy od produkcji, działu sprzedaży, po funkcje administracyjne
- Angażowanie wszystkich członków firmy, od kierownictwa do funkcjonalnych pracowników produkcyjnych
- Dzięki wspólnej pracy zespołu zespołów, można wyeliminować wszystkie straty powstałe w wyniki złego funkcjonowania maszyn i urządzeń
Filary TPM – Total Productive Maintenance
Autonomiczne UR
– W strategii TPM kluczowe jest tworzenie samodzielnych zespołów utrzymania ruchu odpowiedzialnych za poprawę efektywności parku maszynowego. Samodzielność oznacza swobodę w podejmowaniu decyzji w zakresie napraw, konserwacji oraz dbałości o dostępność maszyn i urządzeń.
Doskonalenie
– Nastawienie na ciągłe poszukiwanie możliwości redukcji problemów, pojawiających się przy posiadanych maszynach i urządzeniach oraz szukanie dróg poprawy efektywności i jakości pracy.
Planowane konserwacje
– Stworzenie nawyku dbania o maszyny i urządzenia poprzez planowane konserwacje. Zyskujemy dzięki temu możliwość monitorowania stanu maszyny, zużycia narzędzi i zapobieganiu awariom przez detekcję problemu we wczesnej fazie zaawansowania. Ułatwiamy w ten sposób również pracę planistom, dostają oni bowiem dokładną informację na temat daty planowanych konserwacji i szacunkowego czasu ich trwania.
Planowanie nowych maszyn i urządzeń
– Rozsądne planowanie inwestycji w park maszynowy, oparte na faktycznych danych, czyli kupujemy nowe maszyny jeżeli faktycznie są potrzebne.
Zapewnianie jakości
– Analiza przyczyn powstawania braków i dążenie do redukcji ich liczby.
Szkolenia
– Wdrażanie operatorów w procesy konserwacji i napraw maszyn, tak aby mogli samodzielnie przeprowadzać mniej skomplikowane naprawy.
Zarządzanie parkiem maszynowym
– Standaryzacja poprawnych praktyk i utrzymanie ich. Pomiar i analiza kluczowych wskaźników wykorzystania parku maszynowego. W TPM istotne jest, aby maksymalizować efekty przy niewielkich nakładach. Dobrym wstępem do zarządzania parkiem maszynowym jest wykonanie analizy krytyczności maszyn i urządzeń.
BHP i Środowisko
– Dbałość o bezpieczeństwo pracy i wpływ zaplecza technologicznego na środowisko pracy. TPM to nie tylko poprawa dostępności oraz wydajności, ale również nacisk na zmniejszanie emisji oraz poprawę efektywności pracy maszyn.
6 głównych strat w funkcjonowaniu maszyn:
- Awarie
- Bezczynność i drobne przestoje
- Defekty i poprawki
- Straty związane z rozruchem
- Ograniczenie szybkości pracy
- Przezbrojenie i regulacje
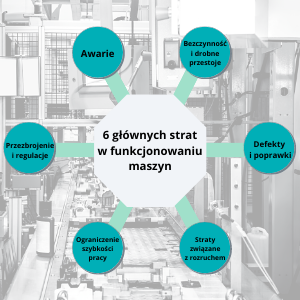
Wskaźnik OEE
Wskaźnik OEE jest jednym z głównych wskaźników w realizacji strategii TPM oraz lean management. Składa się on z trzech elementów takich jak: dostępność, wydajność i jakość. Aby odpowiednio obliczać wskaźnik OEE wykorzystuje się proste sposoby gromadzenia danych. Jeden z najprostszych sposobów to formularz, który w trakcie pracy wypełnia operator maszyny. Ważne jest projektowanie formularza gdyż może to ułatwić zapisywanie istotnych danych w codziennej pracy.
Zebranie niezbędnych danych będzie wymagało zaangażowania operatorów. Nie powinno to jednak stanowić dla nich nadmiernego obciążania, a być częścią ich pracy. Dobrze skonstruowany formularz będzie tu niezwykle pomocny.
Szkolenie Online z CERTYFIKATEM
TPM – Totalne utrzymanie ruchu
Projektowanie wdrożenia TPM w organizacji
Wyliczanie wskaźnika OEE
Zwiększanie wykorzystania zdolności produkcyjnych
Wolisz poszerzać wiedzę w formie warsztatów stacjonarnych? Przygotowaliśmy szkolenie zamknięte TPM, które odbywa się w Twojej firmie i dla Twojego zespołu. Program szkolenia dopasowany jest do potrzeb konkretnie firmy – działamy na wewnętrznych przykładach.
Składowe wskaźnika OEE
Współczynnik wydajności
to różnica między faktyczną ilością wyprodukowanych wyrobów, a planowaną ilością jaką maszyna powinna w danym czasie wyprodukować. Główne straty obniżające wydajność to mikroprzestoje i zmniejszona szybkość pracy.
Współczynnik dostępności
to porównanie dostępnego czasu pracy maszyny z faktycznym czasem jej pracy- wykorzystanie. Dostępny czas operacyjny maszyny może zostać zajęty przez nieplanowane przestoje np.: awarie, usuwanie zacięć materiałowych, długie przezbrojenia, częste uszkodzenia narzędzi itp.
Współczynnik jakości
porównuje całkowitą ilość wyrobów wyprodukowanych do ilości wyrobów spełniających faktyczne wymagania jakościowe klienta. Intuicyjnie główną stratą są występujące braki.
Sposób obliczania OEE:
OEE
=
Dostępność = czas pracy / czas operacyjny netto
X
Wydajność = rzeczywista produkcja / docelowa produkcja
X
Jakość = dobra produkcja / rzeczywista produkcja
Chcesz zwiększyć efektywność swojej firmy jeszcze bardziej? Sprawdź dedykowana ku temu aplikację – OEE Tools.
Przedsiębiorstwo może na podstawie analizy OEE podejmować decyzje na temat organizacji pracy na produkcji, doboru dostawców, konieczności modernizacji maszyn i sytemu kontroli jakości. Wskaźnik OEE jest iloczynem trzech składowych, dzięki czemu staje się on bardzo czuły na wszelkie “niedyspozycje” procesu produkcyjnego. Jeśli bowiem tylko jeden z nich będzie na niskim poziomie, powoduje to natychmiastowe znaczne obniżenie końcowej wartości wskaźnika OEE, który dla firm klasy światowej wynosi 85 proc. Prawidłowo przeprowadzone obliczenia uwzględniają np. takie detale, jak czas przeznaczony na przerwy śniadaniowe, przeglądy, drobne awarie, wymiany, konserwacje, przezbrojenia czy inne przyczyny przestoju.
Od czego rozpocząć wdrażanie TPM?
W przypadku rozpoczynania działań nad rozwojem strategii TPM w firmie należy skupić się w pierwszej kolejności nad obszarami, które są najbardziej krytyczne z punktu widzenia organizacji. Poza ustaleniem celu wdrożenia warto wykonać analizę krytyczności maszyn i urządzeń, która przybliży nas do realizacji planu działania oraz wdrożenia poszczególnych narzędzi w obszarach. Będzie ona swoistą mapą drogową wyznaczającą priorytety ciągłego doskonalenia naszego systemu.
Podstawowe kryteria analizy krytyczności to:
- Obciążenie – jak mocno eksploatowane jest urządzenie? Czy pracuje na 1 lub 2 zmiany, a może nieustannie znajduje się w ruchu powodując duże ryzyko strat w momencie jego uszkodzenia.
- Awaryjność – bazując na danych historycznych jak wiele awarii w roku / kwartale / miesiącu występuje na naszym urządzeniu?
- Zamienność – czy w momencie wystąpienia awarii mamy możliwość wykorzystania innego urządzenia w firmie? Czy możemy zamienić wszystkie jego funkcje? Czy w naszej bezpośredniej okolicy są inne firmy, które wykorzystują podobną technologię, z której moglibyśmy skorzystać w przypadku awarii?
- Stopień automatyzacji – jak bardzo zaawansowane technicznie jest urządzenie? czy operatorzy, technicy UR, mechanicy będą w stanie przywrócić ją do sprawności? Czy konieczne będzie wezwanie serwisu zewnętrznego, który przywróci maszynę do życia?
- Awarie / Obciążenie w czasie – jaki jest stosunek czasu usuwania awarii, do ich wystąpienia? Czy awarie są relatywnie łatwe do naprawienia i czas przywrócenia jest krótki, czy są to poważne przestoje trwające godziny / dni
Dobrze wykonana analiza krytyczności pozwoli nam przenieść ciężar działań na kluczowe obszary i wykorzystać w nich narzędzia, takie jak:
- TPM-1 – Wsparcie operatorów przy realizacji bieżącej obsługi konserwacyjnej
- Budowa bazy części zamiennych wraz z analizą dostawców
- Ustalenie harmonogramu realizacji przeglądów
- Opracowanie planu realizacji RCA – Root Cause Analysis
- Rozwijać matrycę kompetencji na bazie określonych potrzeb
Korzyści wynikające ze stosowania metodologii TPM- Total Productive Maintenance
Skrócenie przestojów planowanych i nieplanowanych- strategia zero awarii
Zwiększenie wykorzystania zdolności produkcyjnych
Wzrost produktywności
Skrócenie czasu cyklu produkcyjnego
Obniżenie kosztów produkcji
Poprawa wizualizacji produkcji w toku
Poprawa jakości produkcji
Zwiększenie stopnia wykorzystania zdolności produkcyjnych
Efektywniejsze zarządzanie zleceniami produkcyjnym
Autor artykułu: Piotr Golonka, Kierownik projektów
Na co dzień pracuje jako Manager Strumienia Wartości integrując wszystkie działy w firmie w celu optymalizacji całego strumienia wartości. Zajmuje się podnoszeniem efektywności procesów, usprawnianiem systemów zarządzania oraz realizacją projektów wdrożeniowych z wykorzystaniem narzędzi takich jak: VSM (Value Stream Mapping), SMED (Single Minute Exchange of Die), 5S, Standaryzacja, Shopfloor Management, KANBAN, TPM (Total Productive Maintenance), Kaizen. Pracował w środowisku dużych korporacji oraz w mniejszych i średnich firmach rodzinnych. Potrafi budować silne zespoły razem z którymi z powodzeniem realizuje ustalony plan.