CYKL PDCA
Czym jest cykl PDCA?
Plan (zaplanuj) –Do (zrób) – Check (sprawdź) – Act (Działaj)
To opracowana przez Edwarda Deminga metoda podejścia do wdrażania zaplanowanych działań. Cykl Deminga zakłada eksperymentowanie w myśl powiedzenia „kto nie sieje ten nie zbiera”. Metoda ta składa się z cyklu 4 kroków, podczas których weryfikowana jest postawiona hipoteza.
Etapy cyklu PDCA
Plan – Etap stawiania hipotezy. Należy precyzyjnie określić plan działania (co chcemy zrobić), nakreślić cele i przedstawić spodziewane rezultaty (co spodziewamy się osiągnąć).
Do – test postawionej hipotezy. Należy wdrożyć zaplanowane działania, po czym poddać proces dokładnym obserwacjom, a zebrane dane dokładnie przeanalizować.
Check – porównanie faktycznych wyników uzyskanych przy testowaniu postawionej hipotezy, ze spodziewanymi rezultatami.
Act – jeżeli nie osiągnąłeś zakładanych rezultatów rozpocznij cykl od nowa. Zweryfikuj plan, założone cele i sposób działania. Wprowadź do niego niezbędne poprawki. Przetestuj hipotezę i porównaj wyniki. Jeżeli okaże się, że założenia zostały spełnione na leży zadziałać w kierunku utrzymania opracowanego rozwiązania. Opracować standardy do praktyk będących wynikiem cyklu.
PDCA i filozofia ciągłego doskonalenia
Toyota poznała PDCA podczas cyklu wykładów Dr Deminga w Japoni w latach 1950-1952. Od tego czasu jest to podejście powszechnie stosowane przez pracowników firmy. Do standardowego cyklu dołożyli oni jeszcze piąty element, reprezentujący ich kulturę ciągłego doskonalenia.
Filozofia Kaizen, o której więcej przeczytacie tutaj, przypomina, że należy dążyć do ciągłego doskonalenia a eksperymentowanie w cyklu Deminga stanowi świetną okazję by nauczyć się nowych rzeczy. Ciągłe doskonalenie w środku koła skrywa również słynne japońskie „Idź i zobacz”.
Przykład zastosowania cyklu PDCA
Idealnym przykładem zastosowania koła PDCA jest standaryzacja pracy. Standard z definicji jest tymczasowy, ponieważ ciągle doskonaląc swoją organizację powinniśmy stale weryfikować i optymalizować metody pracy. Z tego względu praca nad standaryzacją powinna przebiegać zgodnie z podejściem Deminga.
Karta standaryzacyjna:
Powyższe zdjęcia przedstawiają efekt standaryzacji, czyli kartę standaryzacji pracy, która przedstawia optymalny sposób wykonywania czynności związanych z danym procesem. Powyższa karta opisuje operację montażu i pakowania wyrobu gotowego i nie powstała by bez zastosowania kroków cyklu PDCA.
- Plan
Aby standard mógł zostać uznany za optymalny sposób wykonania pracy, musi być współtworzony przez osoby zajmujące się danym procesem. Żadne doświadczenie nie będzie cenniejsze od doświadczenia osoby pracującej na standaryzowanym stanowisku, zwłaszcza jeżeli pracuje tam od lat.
W etapie planowania niezbędne jest :
- Określenie zespołu – kto będzie uczestniczył w obserwacjach stanowiska i analizowaniu pracy
- Wyznaczenie czasu i miejsca – Jakie stanowisko/maszynę/detal będziemy obserwować i co najważniejsze, kiedy? Określenie tych rzeczy pozwala odpowiednio zaplanować pracę, tak aby twoja obecność nie kolidowała z planem produkcji.
Jeżeli wszyscy zaangażowani wiedzą co jest do zrobienia można przystąpić do fazy działania.
- Do – Twój zespół spotyka się w Umówionym miejscu o umówionym czasie i możecie rozpocząć proces gromadzenia niezbędnych danych oraz ich analizy.
O tym jak zabrać się za przygotowanie standardu, przeczytasz, więcej w artykule Standaryzacja pracy.
Zwieńczeniem tego etapu jest gotowa karta standaryzacji pracy. Mając takową możesz przejść do kolejnego kroku.
- Check
Zanim karta standaryzacyjna stanie się obowiązującym dokumentem na terenie zakładu musisz zweryfikować treść karty z pracownikami.
Nie możesz od tak narzucić sposobu wykonywania pracy. Twoim obowiązkiem jest pokazać pracownikom przygotowany dokument, odpowiedzieć na ich pytania i wyjaśnić wątpliwości. Jeżeli będą mieli jakieś uwagi to powinieneś z nich skorzystać, jeżeli są słuszne. Jeśli tak nie jest to poświęć chwilę, żeby uzasadnić pracownikom, dlaczego ich pomysły nie są w tym przypadku najlepszym rozwiązaniem.
Jeżeli na tym etapie pojawią się zasadnicze wątpliwości to należy cofnąć się do pierwszego kroku cyklu PDCA. Nie zawsze oznacza to, że musisz powołać nowy zespół i jeszcze raz nagrać cały proces – być może wystarczy tylko kilka aktualizacji w karcie standaryzacyjnej. Gdy jednak wątpliwości co do standardu są duże może warto będzie przeanalizować cały proces jeszcze raz np. z innym operatorem.
Jeśli natomiast wszystko jest w porządku możesz przejść do ostatniego kroku.
- Act
Ostatni krok to wdrożenie standardu w funkcjonowanie firmy. Zanim jednak się to stanie musisz wykonać kilka kroków:
- Wdrażaj i ucz – Należy przeszkolić osoby wykonujące operacje w danym procesie z nowych metod pracy i upewnić się, że wszystko jest jasne i zrozumiałe.
- Sprawdź czy to działa – Jeżeli dobrze podszedłeś do przygotowania standardu i zebrałeś odpowiednie dane z przed wprowadzenia standardu to w bardzo prosty sposób będziesz mógł ocenić czy nowe metody przynoszą poprawę wskaźników takich jak np.: wydajność stanowiska, czy liczba braków. Nie zapomnij też o rozmowach z pracownikami. Weź pod uwagę wszystkie trudności wynikające ze stosowania się do standardu i wszystkie uwagi, które mogły pojawić się w czasie.
Zobacz przykłady kluczowych wskaźników efektywności KPI na produkcji.
Co dalej
Ostatni krok to oczywiście nie koniec cyklu PDCA w przypadku standaryzacji pracy. Jak wspomnieliśmy na wstępie standard jest najlepszym sposobem wykonywania pracy, dopóki nie pojawi się lepszy. Środowisko pracy się zmienia np.: jeden z nowych pracowników może świeżym spojrzeniem zauważyć coś co warto by usprawnić w twoim standardzie lub możesz zainwestować w nowe środki pracy (maszyny, narzędzia), które otworzą nowe możliwości.
Można zatem powiedzieć, że w przypadku większości działań na produkcji cykl PDCA powinien być prowadzony w sposób ciągły.
Zalety cyklu PDCA
Usprawnia realizację
Można (a nawet trzeba) stosować w każdego rodzaju projektach
Zapobiega przestojom w projektach
Poprawia komunikację
Szkolenie Online
Zarządzanie Procesami i Wskaźniki KPI
Jak zacząć wdrażanie zarządzania procesami w swojej organizacji?
Jak definiować procesy w poszczególnych obszarach firmy?
Jak uzupełnić diagram SIPOC?
Jakie wskaźniki dobrać do poszczególnych procesów?
Potrzebujesz pomocy we wdrożeniu wskaźników?
Sprawdź projekt: KPI – kluczowe wskaźniki efektywności na produkcji.
To rozwiązanie szyte na miarę Twojej firmy. Dlaczego? Każdy projekt rozpoczynamy od badania potrzeb i dostosowujemy jego przebieg do konkretnych wyzwań Twojej firmy.
Wypełnij formularz i pobierz plik Excel z Bazą Lessons Learned!
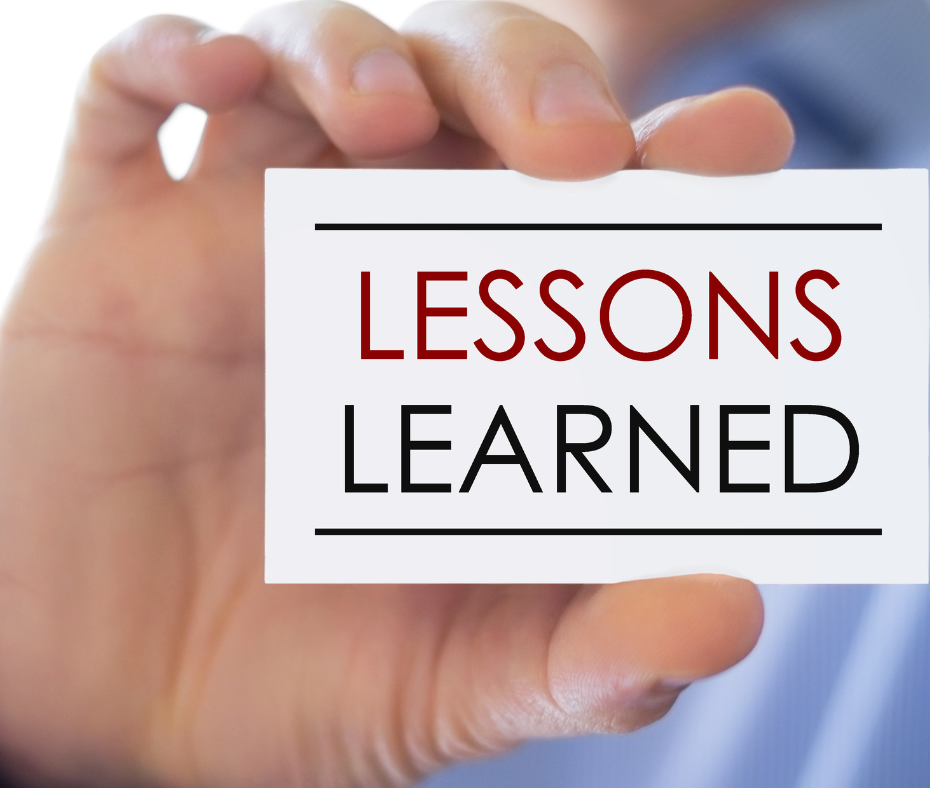
Szukasz rozwiązania, które pozwoli Ci na pełne zarządzanie produkcją? Sprawdź aplikację ZaPro!
To rozwiązanie, dzięki któremu możesz miedzy innymi:
- monitorować zlecenia
- zarządzać zamówieniami
- generować raporty
Autor artykułu: Marcin Wawer, Konsultant, Excel ekspert
Ukończył studia inżynierskie na kierunku Zarządzanie i Inżynieria Produkcji na Akademii Górniczo-Hutniczej w Krakowie. To właśnie na studiach po raz pierwszy usłyszał o koncepcji i narzędziach Lean, które zaciekawiły go tak bardzo, że wytyczyły jego drogę zawodową. Jako konsultant skupia się na obszarach takich jak m.in. standaryzacja pracy, wdrażanie systemu 5S i projekty layout, a także z powodzeniem realizuje szkolenia dotyczące szczupłego zarządzania. Pomaga przedsiębiorstwom w ciągłym doskonaleniu, dbając jednocześnie o własny rozwój poprzez nieustanne zgłębianie wiedzy z dziedzin zarówno technicznych, jak i humanistycznych.